
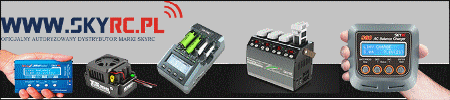
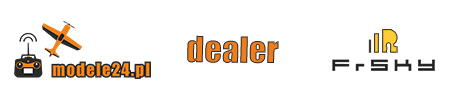
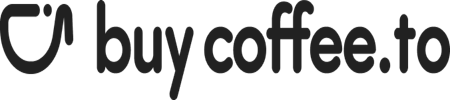
-
Postów
30 -
Rejestracja
-
Ostatnia wizyta
Reputacja
0 NeutralOstatnie wizyty
Blok z ostatnimi odwiedzającymi dany profil jest wyłączony i nie jest wyświetlany użytkownikom.
-
NeoComposito. Usługi inżynierskie dla modelarstwa.
btg opublikował(a) temat w Twój sklep - reklama za free
Oferujemy współpracę w zakresie projektów inżynierskich i wzorniczych. Zakres usług: + kompleksowe opracowywanie rozwiązań koncepcyjnych. +przygotowywanie dokumentacji technicznej +tworzenie rysunków technicznych i modeli 3D +tłumaczenia tekstów technicznych +doradztwo techniczne i konsultacje +przerysowywanie dokumentacji technicznej +specjalizujemy się w konstrukcjach szkutniczych Zapytaj nas o referencje! Zapraszamy do współpracy! tel. 515 185 887 neocomposito.office@gmail.com -
A dokładniej, chropowatość w um nie powinna być większa niż h=100/V, gdzie V jest prędkością obiektu w m/s. Co do gładkości powierzchni: Oracle zastosowało specjalny film ribletowy minimalizujący opór (http://www.businesswire.com/news/home/20100224006699/en/). W planach jest też stosowanie pokrycia skrzydeł nano powierzchniami reagującymi na prąd elektryczny... Ale wkraczamy już tutaj w modelarskie Science- fiction. To, co wydaje się najrozsądniejszym wykończeniem to papier wodny 2500, potem polerowanie. Z powyższego wzoru wynika, że chropowatość dopuszczalna jest odwrotnie proporcjonalna do prędkości. Odnosi się to również do warstwy przyściennej. Niskie liczby Re w jakich kadłuby modeli się poruszają pozwalają na relatywnie długie zachowanie warstwy przyściennej. Ostatnio byłem w Centrum Techniki Okrętowej, do modeli tankowców dodawali druciki na ich bulbach wby sztucznie wywołać turbulencje warstwy przyściennej i dokładniej móc odwzorować opór tarcia. W skali modeli przepływ laminarny jest zachowywany znacznie dłużej niż dla ,,dorosłych jachtów". To zachęca również do stosowania profili laminarnych z dalekim położeniem maksymalnej grubości, nawet 60 czy 70%, a zatem odsunięcia jak najdalej punktu osiągnięcia minimalnego współczynnika ciśnienia Cp. Modele dają nam znacznie więcej możliwości i nie można powiedzieć, że wszystkie efekty są liniowo skalowane. W kilach robionych w formach z CFRP UNI można uzyskać ciekawe efekty: odpowiednio układając włókna można uzyskać taką strukturę, która w przechyle pod wpływem obciążenia kila będzie zarówno zginana jak i skręcana. Spowoduje to pracę kila w dolnej części pod mniejszymi lub większymi kątami natarcia, w zależności od potrzeb. Bardzo ciekawe i wymagające zagadnienie hydro-elastyki! Wkrótce wrzucę zdjęcia z budowy formy żeńskiej. Jednak mamy teraz znacznie więcej roboty nad ,,dorosłymi łódkami". Gdy tylko będzie trochę więcej oddechu to pobawimy się z tym modelem
-
Witam, Cieszę się, że wątek mojej budowy modelu spotkał z tak dużym odzewem Z góry zaznaczam, że to mój drugi model kopyta. Nie uważam siebie w żaden sposób za eksperta w dziedzinie budowy kopyt. Oczywiście, ze istnieje tysiąc metod. Najlepiej przecież wyfrezować z przygotówki aluminiowej w dokładności +/- 0,001 mm... Albo wyfrezować z bloku styropianu z niedomiarem i pokryć specjalną pastą modelarską, aby frezować gotowe kopyto. Tylko to kosztuje grube pieniądze a mój budżet był ograniczony. Nie miałem czasu nabrać doświadczenia w budownictwie modelarskim. Robię według tego, co kiedyś kilku wspaniałych modelarzy mi pokazało, gdy się jeszcze w to bawiłem. Bardziej jestem teoretykiem i doceniam Wasze doświadczenie w zakresie budowy kopyt. Z chęcią porozmawiam natomiast o wpływie szorstkości kadłuba i jego geometrii na opory ruchu i o zastosowaniu algorytmów genetycznych przy optymalizacji parametrycznej kadłuba w zastosowaniach modelarskich. Wyjaśniam wątpliwości jakie się pojawiły: To, co teraz wykonuję to kopyto (forma męska) na podstawie którego zostanie wykonana forma żeńska i z której powstanie kadłub z CFRP UNI. Efekt ugięcia balsy między wręgami zniwelowałem wypełniając przestrzeń od wewnątrz zwykłą poliuretanową pianką montażową z pistoletu. Gdy wrócę do pracowni, porobię odpowiednie zdjęcia. Ostatnie z zamieszczonych zdjęć obrazuje kadłub pomalowany czarną farbą. Następnie kadłub został przeszlifowany papierem 600 i położona została warstwa włókna szklanego 200g. Zapewni to sztywność zewnętrzną kopyta. Balsa po dziś dzień jest jednym z najbardziej docenianych materiałów przekładkowych. Z dołu pianka, z góry laminat- kształt będzie dobry, a tak jak Kolega wcześniej zaznaczył, grunt aby zrobić formę żeńską- ta cała balsa się może nawet potem skruszyć. Po nałożeniu laminatu położyłem cieniutką warstewkę szpachlówki, zeszlifowałem, trysnąłem farbą, zeszlifowałem, zaszpachlowałem znów dołki, pomalowałem, zeszlifowałem. Kształt kadłuba jest już wyprowadzony. Mam teraz tak mało czasu, że nie mam kiedy do tego znów usiąść. Leży kopytko w pracowni i czeka na mój czas. A w planach: zrobienie formy żeńskiej oraz laminowanie z CFRP UNI. Jeśli uda mi się załatwić to w metodzie infuzji, a jak nie to ręcznie epoksydem. Pozdrawiam, Kuba
-
Cześć Postanowiłem udokumentować budowę kadłuba mojego jachtu Innovator II. Kiedy sam zaczynałem zabawę z modelami jachtów RC samemu brakowało mi tego typu opisów budowy, mam nadzieję, że informacje i rady zawarte w mojej relacji przydadzą się komuś z Was. Finalnie ma wyglądać tak: Dzień 1 Materiały jakie przygotowałem to wydrukowane plany, deska 90 cm (kadłub ma 99 cm długości, więc wystaje, gdybym mógł wybrać to wziąłbym deskę ok. 110 cm, ale akurat taką miałem ,,pod ręką"), 4 listewki balsowe 1000x100x3 mm oraz dwie sklejki topolowe 60x40 cm gr. 3 mm. [fot. 1] [fot. 1] Na ścianie pracowni powiesiłem wydrukowane wizualizacje 3D gotowego modelu. Aby podczas kolejnego żmudnego szlifowania przypomnieć sobie, że niby koniec końców ma to wszystko tak wyglądać . Wydrukowałem poszczególne przekroje na kartkach A4. Pamiętać należy aby uwzględnić grubość balsy jakiej będziemy używać i o tę wartość ,,zoffsetować" nasze przekroje. W przeciwnym wypadku uzyskamy nieco więcej wyporności niż było założone w planach. Wyciąłem przekroje pozostawiając spory naddatek ok. 1 cm dookoła faktycznej linii cięcia sklejki Listewki na balsę przyciąłem do szerokości 12 mm W tym czasie zdążył wyschnąć klej i przekroje zostały przyklejone na sklejkę Do przycinania listewek użyłem piły i przykręciłem imadełkami metalowe płaskowniki, aby uzyskać żądaną szerokość listewek (12 mm) BHP to podstawa!!! Gogle przy pracy z piłą oraz filtr przeciwpyłowy. Później podczas szlifowania, szpachlowania, malowania polecam specjalny filtr z dużymi pochłaniaczami 3M tzw. do ,,par organicznych". Ten filtr pozwolił mi przetrwać dzisiejszy dzień Bardzo istotna jest wentylacja pomieszczenia! Okna otwarte, a niekiedy dobrze wywołać przeciąg otwierając jednocześnie drzwi. Maska przeciw parom organicznym 3M: Przyszedł czas na wycinanie przekrojów. Tutaj bardzo istotna jest precyzja, aby piła szła dokładnie po konturze przekroju. Zaoszczędzi to czasu na późnijeszym szlifowaniu i wyrównywaniu. Lepiej od razu zrobić to dobrze Wszystkie wręgi wycięte! Zacząłem od wręgi rufowej. Mój projekt ma rufę typu ,,retrousse", charakterystycznie nachyloną pod kątem do linii wodnej. Aby móc nadać kształt tej końcowej sekcji konieczne jest przyklejenie za wręgą końcową (x=10 cm od rufy) pochylonej atrapy rufy, do której będą przyklejane listewki Na deskę naniosłem markerem linię centralną kadłuba i odznaczyłem miejsce mocowania poszczególnych wręg. Poszywanie zaczynam tredycyjnie od położenia przysłowiowej stępki A następnie krawędzi burty tzw. sheerline. Aby prawidłowo odwzorować krawędź burty można albo zaznaczyć markerem na boku wręgi gdzie się kończy burta dla danego przekroju (jak ja zrobiłem) albo przygotowując plany zaprojektować nacięcie w które będzie wchodzić mała listewka 2x2 mm. W ten sposób mamy zaznaczony obszar poszywania. Nakładam listewki zaczynając od burt dokładam do dolnej listewki. Klej cyjanoakrylowy nakładam na CAŁEJ DŁUGOŚCI LISTEWKI. To bardzo ważne gdyż listewki w ten sposób sklejone nie uginają się między wręgami i można je pewniej wstępnie szlifować. Tak wygląda gotowa poszyta jedna strona kadłuba: Jak widzicie, najpierw kładłem listewki wzdłuż burty ,,od dołu" a potem kładłem listewki wzdłuż stępki. ,,Schody" pojawiają się na poszywaniu tzw. obła, czyli tego zaokrąglenia pomiędzy burtą a dnem. Listewki odwzorowujące obło muszą być zukowsowane pod koniec aby dopasować się do prostych listewek biegnących wzdłuż stępki. Nie jest to bardzo trudne, wystarczy przyłożyć końcówkę listewki ,,na próbę" następnie zaznaczyć nożykiem gdzie powinno być dokonane zukosowanie i przyciąć. Po przyklejeniu listewki wzdłuż burty i stępki dobrze przykleić listewkę biegnącą wzdłuż obła. Do tej listewki będą ukosowane pozostałe listewki- aby ukosować do równej krawędzi tej listewki a nie łapać nagle dwóch listewek ,,w powietrzu". Listewki nakładać z nadmiarem długości- na koniec wszystko się przytnie I przycięte: I tak się zakończył dzień pierwszy i byłem z niego zadowolony, bo widziałem, że to dobre Dzień 2: Dokleiłem dziób, który następnie wypełniłem listewkami pozostałymi po poszywaniu kadłuba: Po wyszlifowaniu: Ubytki zostaną zaszpachlowane, pomalowałem na czarno sekcje dziobowe aby wiedzieć kiedy przestać szlifować Cały kadłub następnie zaszpachlowałem szpachlówką Novol poliestrową wykańczającą. Ważne aby nanosić możliwie mało szpachlówki miękką szpachelką z tworzywa sztucznego Nakładanie najlepiej robić od burty w stronę dna: I wyszlifowałem. Przy szlifowaniu ważne jest aby nadać ostateczny kształt kadłuba. Dlatego zawsze szlifuję przez kostkę, nigdy gołymi rękoma. Powstają wtedy bowiem dołki. Dno szlifuję wzdłużnie, burty również, zaś aby na oble nie powstały a tego powodu żadne wystające górki, obło szlifuję pod kątem 30-40 stopni względem linii centralnej kadłuba czyli od burty do dna, od dna do burty itd.: Pod ręką czuć, że kadłub jest już gładki i że jego linie są płynne. Ale to złudne wrażenie. Przy użyciu prostej metody można sprawdzić gdzie na naszym modelu są ,,dołki". Całą powierzchnię dosłownie skrapiamy farbą w sprayu tak, zeby wyglądała jak na obrazku poniżej. Czemu skrapiamy a nie po prostu malujemy? Szybciej schnie i szkoda farby, a chodzi o to tylko aby tak skropioną powierzchnię delikatnie przeszlifować papierkiem 120-200. W miejscu gdzie papier nie ściera farba pozostanie i te miejsca należy zaszpachlować i wyrównać: Po przetarciu: Przyszła kolej na kolejne szpachlowanie, tym razem już ,,punktowe". Aby wiedzieć gdzie nałożyć szpachlówkę i nie musieć szukać tych miejsc gdy już mamy połączoną masę z utwardzaczem, ja robię tak że siadam spokojnie i obserwuję całą powierzchnię zaznaczając markerem miejsca do zaszpachlowania. Większe obszary bądź drobniejsze ubytki. Na tym etapie cały czas najważniejsze jest wyprowadzenie powierzchni, więc ubytki można sobie darować na obróbkę wykańczającą, potem. To szpachlowanie i szlifowanie powtarzam aż do momentu uzyskania satysfakcjonującej powierzchni. Szpachlówka schnie bardzo szybko, więc proces można szybko przeprowadzić. Szpachlówkę warto mieszać z utwardzaczem na wadze z dokładnością do 1g. Wtedy mamy pewność, że ,,zżeluje" i jednocześnie że zdążymy donieść ją do modelu przed zżelowaniem. Naprawdę warto stosować się do zaleceń producenta w tym względzie! Szpachlówka Novol łączy się w stosunku wagowym 100:2-3 gram. Po tych operacjach pomalowałem kadłub farbą w sprayu i wygląda tak: Komentujcie, subskrybujcie, zadawajcie pytania. Na wszystkie chętnie odpowiem Dalszy ciąg prac nad modelem już w poniedziałek! Kuba
-
Wyroby z kompozytów polimerowych. Politechnika Warszawska.
btg opublikował(a) temat w Twój sklep - reklama za free
Podejmiemy się zrobienia dowolnego wyrobu z kompozytów polimerowych. Nasza oferta kierowana jest głównie do zawodników oraz osób, dla których najważniejsze są osiągi ich modeli. Należymy do w Koła Naukowego Konstruktor ( http://imik.wip.pw.edu.pl/knk/ ) przy Wydziale Inżynierii Produkcji Politechniki Warszawskiej w którym na co dzień mamy styczność z najnowocześniejszymi technologiami stosowanymi w kompozytach polimerowych. Naszym głównym obszarem zainteresowań jest mechanika kompozytów. Włókno szklane, aramidowe, węglowe. Struktury ,,sandwich'owe" na przekładce z Airex-u, Herex-u, Coremat'y, Honeycomb Aramid, balsy oraz innych rdzeni. Oferujemy najwyższą jakość i właściwości mechaniczne wyrobów przy jak najniższej masie. Analizy FEA, laboratoryjne badania wytrzymałościowe, optymalizacja geometrii wyrobu pod kątem wytrzymałościowym. Opracowywanie modeli w środowisku CAD/CAM/CAE, przygotowanie form na CNC i procesu technologicznego. Bazujemy na technologii vacuum bag-u. Z NAMI WYGRASZ! kontakt: Jakub 515 185 887 studio.btg@gmail.com -
Motorówka od podstaw
btg odpowiedział(a) na Chriss temat w Statki , okręty, okręty podwodne , żaglowce
Co do stopniowanego dna: wszystko pięknie, stabilniejsza jazda, mniejsza powierzchnia zmoczona, należy tylko o jednej rzeczy pamiętać: Stopień musi być zaprojektowany w taki sposób, aby zapewniony był stały dopływ powietrza do niego z obydwu stron po bokach. Przy dużej prędkości model może cierpieć na niestabilność, jeżeli nie zostanie ten warunek spełniony. W "dorosłych" motorówkach nieraz doprowadza się powietrze do stopnia poprzez tunel z wlotem na poziomie pokładu. Przestudiuj, jak wygląda połączenie burty z dnem, chodzi mi o te nacięcia w tylnej części: http://www.fountainpowerboats.com/images/racingbanner.jpg tutaj jest to dalej wytłumaczone; konieczność zapewnienia dopływu powietrza: http://www.navaldesign.co.za/articles/Stepped%20Hulls-%20Feb07.pdf