
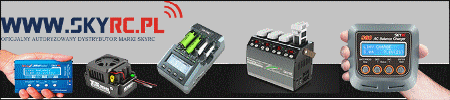
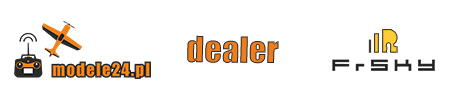
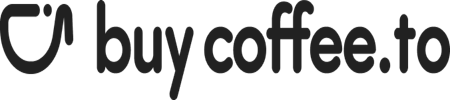
-
Postów
546 -
Rejestracja
-
Ostatnia wizyta
-
Wygrane w rankingu
1
Ostatnia wygrana Kamilos w dniu 26 Grudnia 2024
Użytkownicy przyznają Kamilos punkty reputacji!
Reputacja
55 ExcellentO Kamilos
- Urodziny 19.10.2000
Informacje o profilu
-
Płeć
Mężczyzna
-
Skąd
Warszawa
-
Imię
Kamil
-
Przez dłuższy czas nic się w temacie nie działo więc wrzucam filmik z oblotu prototypu. Zrobiony jest z XPS i oblaminowany włóknem szklanym i węglowym, skrzydła są zrobione metodą vacuum bagging z mylarem 0.3mm. Lot wykonałem na pakietach 12s 3700mAh.
-
Dużo tego pasa startowego potrzebujesz? Jak coś to wpadaj na Reguły. Pinezka: https://www.google.pl/maps/place/Lotnisko+Modelarskie+RC+Reguły/@52.154844,20.8585731,238m/data=!3m1!1e3!4m5!3m4!1s0x4719344826e26ea5:0x4e0447b6b7835a56!8m2!3d52.155012!4d20.8584971?hl=pl&entry=ttu&g_ep=EgoyMDI1MDYwMS4wIKXMDSoASAFQAw%3D%3D
-
Fcc to soft na rynek "ogólny" czyli możliwe jest wykorzystanie większej mocy nadawania, LBT to wersja europejska z ograniczeniem do 25mW jeśli dobrze pamiętam. W pytaniu czy nadajnik podziała z FCC chodzi o to czy możesz tam wgrać soft w tej wersji? Czy o to czy zadziała z odbiornikiem FCC? Jeśli to pierwsze to raczej tak, po prostu w ExpressLRS Configurator zaznacz żeby build był w wersji FCC(oczywiście należy używać wersji odpowiedniej dla regionu w którym latasz ). To tak najprościej rzecz ujmując.
-
Około 130% powierzchni EDF-a. Dla spalinowej turbiny nie będzie problemu z podciśnieniami w kadłubie
-
Powstał pierwszy statecznik z "eksperymentalną" powierzchnią z kutego węgla. Ogólnie to powstał raczej jako demonstrator technologii i chyba nie będę go wkładał do samolotu mimo że w środku ma dźwigar, zawias steru kierunku itd. Wyszedł ciężko . Następny już będę robił taki do latania
-
Ostatnio ciężko znaleźć czas na zrobienie dużej formy na kadłub ale w weekend udało się chwile wygospodarować żeby zrobić formy na statecznik pionowy. Aktualnie jeszcze przed polerką bo czekam na pastę ale już po gładzeniu na mokro. Standardowo kilkanaście warstw tkaniny szklanej i wypełnienie z poraveru.
-
Średnica na końcu to 110mm.
-
Dziś trochę multitasking, podczas gdy przygotowywałem pozytyw drugiej formy kadłuba, wrzuciłem do frezowania pozytyw statecznika pionowego. Wykonany z płyty Obomodulan 700 terra.
-
Trochę mnie tu nie było projekt miał mały przestój ale w sezonie kiedy jest super pogoda do latania to ciężko znaleźć czas na siedzenie w warsztacie. Aktualnie jestem na etapie robienia form na kadłub. Jedna już prawie gotowa. Formy na kadłub będą trzy ze względu na jego geometrie, inaczej nie dało by się wyciągnąć którejś połówki oraz samo laminowanie byłoby trudniejsze ze względu na trudno dostępne miejsca (a takie by były jakbym nie podzielił na więcej niż dwie połówki). Zdjęć z robienia formy mam dwa, jedno po drugiej warstwie żelkotu a drugie po którejś z wewnętrznych warstw tkanin, już nie chciało mi się rękawiczek ściągać żeby dalej foty strzelać. Technologia widziana już na tym forum więc nie będę jej opisywał. Aktualnie jeszcze przed polerką. Pozytywy na kolejne połówki i formę kabinki są w produkcji albo już są gotowe. EDF 110mm już kupiony więc teraz nie ma odwrotu, musi polecieć
-
Trochę to trwało ale połówka kadłuba gotowa. Trzeba jeszcze trochę poszlifować. Ciężko to idzie i dosyć dużo czasu zajmuje, rozważam narysowanie tego jako konstrukcja z drewna. Będzie szybciej i precyzyjniej, co miałem posprawdzać to już udało mi się ogarnąć, pozycjonowanie materiału itd.
-
Czekam z niecierpliwością żeby zobaczyć jak latasz logo , jeśli chodzi o nowy projekt to główna zmiana to jeżdżąca brama. Prace idą powoli, udało mi się wyfrezować już komplet stateczników. Zdecydowałem że je zalaminuje pod mylarem i wrzucę do wora. Myślę że w przyszłym tygodniu wezmę się za skrzydła, tutaj lekko zmodyfikuję plany bo frezowanie ich powierzchni zajmuje za dużo czasu oraz wytwarzanie już sobie przećwiczyłem frezując je oraz stateczniki(strategie obróbki, frezy walcowe i kulowe itd.). Zrobię tak że wyfrezuję wnętrze jak na zdjęciu z pierwszego postu a powierzchnię wytnę drutem, przyśpieszy to nieco prace i na frezarkę już wrzucę kadłub. Zestaw stateczników prezentuje się tak: ten z prawej ma jeszcze nadmiary pianki nie odcięte. Wewnątrz są już kieszenie na rurki węglowe na których będą montowane stateczniki do kadłuba.
-
Trochę mi szkoda czasu na zabawę w mniejsze EDF'y. Ogólnie to też plan jest taki że szpej z tego prototypu czyli składane podwozie, serwa itd. pójdzie do docelowej konstrukcji.
-
Zasilanie planuję 12s i pewnie 5Ah(takie pakiety akurat mam), powinno starczyć na te 3 - 3:30 min lotu. Dziękuję i również życzę wesołych świąt i szczęśliwego nowego roku.
-
Dzień dobry, cześć i czołem dawno nie zakładałem tu tematu. Dosyć długo się zastanawiałem czy jest sens relacjonować moje poczynania oraz czy wgl. zakładać ten temat tak wcześnie(chodzi o etap budowy a nie moment w czasoprzestrzeni ). Bardziej doświadczeni użytkownicy pewnie pamiętają mnie z moich zbyt ambitnych projektów jak na technologie produkcji które w tamtym czasie prezentowałem, a mianowicie ich brak . Ale nie uważam tamtego etapu za zmarnowany czas i środki bo jednak wiedza jaką zdobyłem jest dosyć spora dzięki dosyć brutalnej weryfikacji moich pomysłów przez rzeczywistość. Tyle jeśli chodzi o krótki wstęp. Do rzeczy, ostatnio zainteresowałem się modelami odrzutowymi. Tak wiem że dział nie ten ale i prezentowany model jest na etapie budowy elektrycznego prototypu zanim zacznę robić formy i docelowy kompozytowy model z turbiną spalinową. I tutaj jeśli ktoś by był ciekaw, tak latałem już samolotami z silnikami turboodrzutowymi. I to nawet całkiem sporymi samolotami ale jako że to było w ramach kontraktu, więcej nie mogę napisać. Ale od tamtego czasu wciągnąłem się w ten temat. Pomysł na budowę tytułowego płatowca natomiast ma początek około września tego roku, w dniu w którym Patryk mi powiedział że może mi sprzedać jego maszynę CNC(tak chodzi o ZOśkę). I tak oto w listopadzie przywiozłem frezarkę do garażu i po miesiącu nauki oraz zbierania elementów potrzebnych do uruchomienia(komputer, jakieś wtyczki itd.) rozpocząłem pierwsze próby wytwarzania płatowca. Do nauczenia się jest sporo, aktualnie frezuję głównie w XPS ponieważ uczę się modułu CAM w Fusion 360. Wyfrezowanie pierwszego elementu płatowca zajęło 4 próby 2 się nie udały przez źle przygotowane programy a 3 przez mój błąd bo nie zaznaczyłem punktów do których muszę przyłożyć materiał żeby punkt zero się zgadzał. Pierwszy element nadal nie nadaje się do użytku bo były źle ustawione wymiary przygotówki i profil skrzydła wyszedł tak jakby stał na 1cm podkładce . Przechodząc do samego płatowca, prezentuje się tak: założenia są takie aby zrobić płatowiec w rozmiarach, w których będzie poręczny w transporcie, a które nie są zbyt popularne na rynku, z tego co się orientuje tylko Carf Rebel, Krill AreS mini, Interceptor od TomJets oraz jeśli chodzi o pianki to Avanti i Havoc od e-flite są dostępne jeśli chodzi o seryjną produkcję. Piszę o modelach które nie są odwzorowaniem prawdziwych samolotów. Kilka informacji o projekcie: - rozpiętość skrzydeł ok. 1.2m - długość kadłuba ok. 1.7m - waga gotowego do lotu ok. 4.5-5 kg - możliwość zamontowania wektorowania ciągu - aktualnie materiał to XPS wzmacniany rurkami węglowymi, jeszcze nie wiem czy będę laminował go w worku czy tylko okleję taśmą pakową - docelowo full kompozyt z form - oczywiście na razie napęd elektryczny który obracać będzie wiatrakiem 110mm. Jeśli chodzi o aktualny postęp prac to wygląda tak: Od razu rozwieję możliwe wątpliwości, tak wiem że frezowanie skrzydeł z XPS w ten sposób jest delikatnie mówiąc nie efektywne ale robię to z premedytacją bo wolę zepsuć kilka kawałków XPS niż płytę poliuretanową za kilka tysięcy złotych . Na powyższych zdjęciach widać skrzydło o którym pisałem wyżej, poszarpane krawędzie to efekt wycinania go z płyty styroduru brzeszczotem. Płat od środka będzie wybrany, jest to już przetestowane rozwiązanie w samolocie który latał z dużymi prędkościami(potwierdzonymi danymi z telemetrii, na pokładzie był Pitot) więc nie boję się o sztywność, oczywiście będzie wzmocnione rurkami węglowymi na które miejsca widać. Na zdjęciach wnętrza skrzydła widać że miejscami jest dosyć nieregularna kieszeń, otóż na jednej płycie były łaćznie 4 próby rezania i nie chcąc marnować płyty wcisnąłem jeszcze właśnie 4 próbę ale musiałem zahaczyć o poprzednie wycięcia, stąd te kieszenie. Jeśli chodzi o te stopnie to uznałem że nie ma sensu od środka wykonywać obróbki detalicznej. Aktualnie już wiem że powierzchnie sterowe będą inne, między klapą a lotką nie będzie przerwy oraz lotka będzie sięgała do końca skrzydła. Na ten moment to tyle, w styczniu prace trochę pewnie zwolnią bo jako że ja to ja, już zaplanowałem mały remont ZOśki a pisząc mały remont mam na myśli budowę swojej frezarki po prostu przerzucę graty z ZOśki na swoją ramę, sorry Patryk .
-
Ja używam tego: https://www.castorama.pl/lekka-szpachla-naprawcza-toupret-1-kg-id-1089475.html?exactc=7b548adcd9a73a19fecbfd33750c36b8&keyword=pla_smart_performancemax_wykonczenie_pm&gclid=CjwKCAiA0JKfBhBIEiwAPhZXDwwVZ65Vdrhr7Zi0dfyMGgXnjar1KYgVHYk7SStzIMYbXP38VkegghoCSHsQAvD_BwE jest bardzo lekka i szybko zasycha ale ma dwie główne wady, pierwsza to jest dość kijowa, a druga to nie jest odporna na wodę itd. Ja ją szlifuję na tyle by powierzchnia była dobra(więcej raczej ciężko uzyskać) a potem lakieruje i szlifuje pod wodą. Trzeba uważać żeby przy szlifowaniu nie zniknęła cała warstwa lakieru bo wtedy szpachla zacznie odpływać jeśli szybko jej nie osuszysz ręcznikiem/ścierą(może nie będzie uciekać bardzo szybko ale łatwo żeby pojawiło się wyczuwalne wgłębienie).