
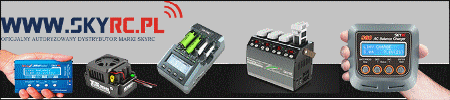
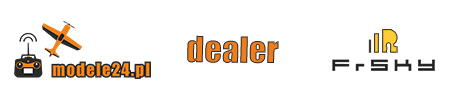
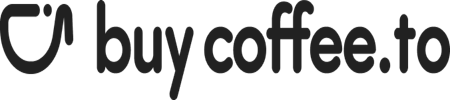
-
Postów
312 -
Rejestracja
-
Ostatnia wizyta
-
Wygrane w rankingu
2
Treść opublikowana przez lukasto
-
Mam ustawienie "fabryczne". Prędkość startowa 100 i akceleracja 15 (jeśli dobrze pamiętam). Nie ruszam tego bo na oko wygląda, że jest ok. Maszyna łagodnie ale szybko osiąga pełną prędkość i hamuje (potrzebuje na to ok 0,5cm)
-
Maszyna nie nadąża się "rozpędzić" do pełnej zadanej prędkości bo ma za krótkie odcinki podczas wiercenia. Cykl mam zaprogramowany na wiercenie co 2mm (2mm zagłębienia -> 0,25mm powrotu -> i powtórka cyklu aż do osiągnięcia zadanej głębokości) a na takim odcinku zdąża "rozpędzić" się tylko do połowy pełnej prędkości. Palenie faktycznie jest spowodowane zbyt dużą prędkością (nie mam co do tego żadnych wątpliwości). Problem w tym, że przy takiej prędkości zagłębiania nie mogę mieć mniejszej prędkości obrotowej bo wiertło nie będzie nadążało "zbierać" materiału. Możesz wyjaśnić mi co to jest "rampa"? Obecnie 0 osi Z mam wysoko bo muszę przewiercić prawie 4cm (musiałem nawet zdjąć chwilowo wyłącznik krańcowy na dole osi, żeby zrobić te wiercenia - widać na filmie jak wisi sobie na kablach ). W normalnej pracy 0 jest na wysokości ok 1,5 cm nad blatem (1,5cm prześwitu pomiędzy blatem a końcówką wrzeciona) - wyliczone tak aby jak najwięcej freza było w uchwycie a "sterczała" tylko część robocza - zwykle ok 1cm dla frezów z uchwytem 3,175mm + mały zapas. "Mały zapas" dodany gdyby się okazało, że będzie potrzeba frezowania w materiale grubszym od 1cm (choć myślę, że będzie to należało do rzadkości )
-
Wiertło jest ostre. Płyta go nie "zjadła". Problemem jest to, że jest to wiertło do stali nierdzewnej a nie do drewna a ja ze względu na obecność wkrętów w bliżej nie określonych miejscach nie mogę założyć wiertła do drewna. Szybkość wiercenia jest ustawiona na 500 mm/min ale i tak "nie wyciąga" takiej prędkości (najszybsza prędkość zaobserwowałem na poziomie 250mm/min - wpływa na to rozpędzanie i hamowanie osi) Wiertło do drewna i do stali działają zupełnie inaczej mimo, ze na pierwszy rzut oka wyglądają bardzo podobnie. Jak same nazwy wskazują służą do czego innego i tak samo jak wiertło do drewna szybko padnie w metalu tak samo wiertło do metalu nie pociągnie długo w drewnie (choć i tak znacznie dużej niż w "odwrotnej" konfiguracji) ale z zupełnie innego powodu. Po szczegóły i dlaczego tak a nie inaczej zapraszam do googla . Tu nie chce mi się pisać, temat wierteł to temat rzeka i można by o tym mówić nie tyle godzinami co całymi dniami. Otwory głębokie bo "na wylot" 2x18mm - 2x bo miał być stół podciśnieniowy ale postanowiłem na razie zrobić "normalny" blat a wysokość osi Z została tak policzona aby 0 było na takiej wysokości aby nie tracić zakresu osi po włożeniu stołu podciśnieniowego. Otwory na wylot bo śrubę będę skręcał nakrętką od drugiej strony. Otworów dużo bo nie chce mi się później kombinować i co chwilę przekładać materiał w którym będę frezował, chcę go zmieścić max dużo na "jedno frezowanie" a trzeba pamiętać, że nie zawsze będę miał "całe deski", często mogą byc "odpady" zatem punkty w których to wszystko będzie mocowane mogą wyjść za każdym razem w innych miejscach. Przy takiej gęstej siatce otworów mam pewność, że zawsze wszystko zamontuję.
-
Twój pomysł był dobry ale znalazłem lepszy . Cykl wiercenia o którym mówisz "83" okazał się dobry ale czas wykonania całości wzrósł z 12 godzin do 56 (przy prędkości obróbki 500mm/min). Podmieniłem cykl 83 na 73 czyli z cofaniem na 2mm (chyba) a nie "pełnym powrotem" i czas spadł mi do ok 2,5 godz (przy prędkości obróbki 500 mm/min). Śmierdzi palonym drewnem jak cholera ale 1/3 otworów mam już gotowe. No i niestety muszę stać z odkurzaczem i na bieżąco odciągać zwierciny i dym przede wszystkim, żeby mi sąsiedzi nie wezwali straży pożarnej . Poniżej filmik: http://youtu.be/n2MZ-RLQ3Ls
-
Co do blaszek może masz rację ale ja przynajmniej na razie nie planuję robić nic w stali czy aluminium. Wiercenie posuwem 60. Narzędzie ma wystarczającą moc tylko wiertło powinno być do drewna a nie do stali, wtedy byłoby lepsze odprowadzanie zwiercin, brak efektu klinowania (wiertło nie ma stałej średnicy) i lepsze skrawanie. Problem w tym, że ze względu na wkręty o których pisałem nie mogę zamontować wiertła do drewna, olejem chłodzącym tez nie mogę lać bo wsiąknie mi w blat i koło się zamyka. Co do uchwytów myślałem o czymś bardzo podobnym ze sklejki 3mm (mam resztki takiej) ale bez "regulacji". Zamiast regulacji robię gęstą "sieć otworów" głównie po to aby móc zamontować na blacie kilka np desek balsowych (nie koniecznie "całych" ale również "dużych odpadów") i frezować wszystko bez przekładania materiału.
-
Próbowałem zmniejszyć obroty ale wiertło nie nadążało wiercić i się "klinowało" (aż mi się wrzeciono zatrzymało). Wiercę w płycie meblowej wiertłem do stali nierdzewnej ale nie mogę założyć wiertła do drewna bo w niektórych miejscach mogę trafić na wkręty i konstrukcje aluminiową. O ile konstrukcję aluminiową mogę przewidzieć gdzie będzie o tyle wkrętów nie bardzo. Zatem tym bardziej wolę mieć otwory montażowe. Sklejkę czy balsę mógłbym połamać przy próbie odklejenia.
-
Jakoś nie ufałbym taśmie. Wolę jak będzie to wszystko przykręcone, przynajmniej będę miał gwarancję, że nic się nie przesunie. Z czystej ciekawości, jak masz zrobione te uchwyty?
-
dzięki, może z tymi w końcu coś się uda zrobić Blat mam już splanowany (udało się na prędkości 500mm/min) Wiercą się teraz otwory przez które będę przykręcał obrabiany materiał do blatu, ale widzę, że zajmie to więcej czasu niż planowanie. Otwory muszę wiercić na wolnym posuwie bo mi się wiertło pali
-
Poleci ktoś jakiś darmowy program CAM? - nic nie mogę znaleźć od kilku dni
-
Próbowałem na 700 ale silnik osi X zgubił mi kroki. Nie wiem czemu podczas szybkiego przejazdu jest ok a podczas frezowania gubi kroki. Przy kilku/kilkunastu próbach maszyna bazowała się powtarzalnie a jak bedzie później to się okaże
-
Zacząłem planować stół i przy okazji zmierzyłem odległość pomiędzy zewnętrznymi krawędziami frezowanego "otworu". W tym przypadku jest to max wymiar po osi X. Mam błąd 0,3mm a ten w większości pewnie wynika z samej metody pomiaru (przymiar elastyczny - błąd przyłożenia do krawędzi, błąd odczytu, itd...). Okazuje się zatem, że poprzedni pomiar zawierał dodatkowe czynniki wpływające na ogólny wynik (teraz już wiem co mi poprzednio "dodało" te 3mm). Oznaczałoby to zatem, że osiągnąłem nawet lepszy wynik w kwestii dokładności niż pierwotnie zakładałem . Stół planuję frezem 3mm (nie mam większego a do jednorazowej "roboty" nie chcę wydawać kilkudziesięciu zł) więc trochę się jeszcze wystoję przy frezarce (wg obliczeń ok 6 godzin frezowania ) Prędkość frezowania mam stabilną (bez gubienia kroków) przy 350mm/min, szybki przejazd jest ustawiony na 700mm/min i jak na razie jeszcze nie zgubił mi kroków. Działa już funkcja Homing i zastanawiam się czy dałoby się ją jakoś zaadoptować do wykrywania długości freza (niestety na płycie sterownika nie mam wejścia na taki czujnik ) Poniżej krótki filmik nakręcony dziś podczas planowania Jakość filmu nie zwala z nóg ale dysponuję tylko "kamerą" w telefonie http://youtu.be/xA1L9SaW5RE
-
Planuję zrobic kesony ale tylko w "skrzydle głównym". Statecznik poziomy pozostawiam zgodnie z oryginałem (bez kesonów).
-
Zapowiada się, że już niedługo zakończą się prace z frezarką CNC zatem najwyższa pora pochwalić się pierwszym modelem wycinanym nową "zabawką" . Będzie to wszystkim dobrze znany Wicherek 25P z kilkoma przeróbkami. Stąd też zmiana nazwy na 25L Od ok miesiąca powoli przypominałem sobie ACADa, czytałem rylacje i zapoznawałem się z planami tego modelu. Jakieś 2 tygodnie temu zabrałem się "na poważnie" do wykreślenia wszystkich elementów tak aby dało się później projekt wysłać na frezarkę Na taim etapie model jest obecnie : kolor czerwony - sklejka 3mm (chodzi m po głowie balsosklejka, ale nie wiem czy będzie wystarczająco mocna) kolor niebieski - balsa 3mm kolor żółty - listewki sosnowe 5x3mm (w 2 miejscach jest 10x3mm) kolor grafitowy - rurka węglowa 8mm i 6mm (w niektórych miejscach drut 1mm) Własne modyfikacje to głównie "detale" ułatwiające montaż i pasowanie wszystkich elementów. Na "tartak" już niedługo zacznę przyjmować zamówienia
-
tak, śruba jest trapezowa fi 10mm
-
Pomiar był robiony przymiarem elastycznym, co prawda przymiar jest bez papierów potwierdzających normowanie, ale ma podaną informację wg jakich norm jest zrobiona. Śruba napędowa jest poliamidowa (kupiłem na Allegro). Ilość kroków faktycznie nie jest równa 200 (jest z jakimiś ułamkami które wyszły podczas kalibracji na odcinku 3cm). Przy ostatnim próbnym frezowaniu uszkodziłem sobie wrzeciono, i poharatałem cały blat roboczy zatem teraz najpierw splanuję blat roboczy bo już wiem, że idealnie poziomy z płaszczyzną pracy freza to on nie jest .
-
Udało się w końcu "odpalić" wyłaczniki krańcowe, brakowało jednego ustawienia w programie . Wszystkie połaczenia silników z elekrtoniką zostały wymienione na ekranowane a przy okazji zrobiony porządek w kablach. Zrobiłem kolejna próbę kalibracji, tym razem za pomocą czujnika zegarowego z zakresem do 3cm. Zauwazyłem, ze przy powrocie mam błąd rzędu 0,02-0,04 (raz "na plus", raz "na minus"). Po skalibrowaniu wszystkich osi na odcinku 3cm (powiedzmy, ze udało się skalibrowac z dokładnością do +- 0,02mm - a przynajmniej tak mi sie wydaje ), zrobiłem próbę na całej długości osi X (590mm) - maszyna faktycznie przejechała 593mm. Macie pomysł jak temu zaradzić? Na odcinku 3cm mam maszyne bardzo dokładną, ale na całej długości jest już błąd 3mm.
-
Zrobiłem próbę podłączenia wyłączników krańcowych i france nie chcą działać. Grzesiek, ty masz ten sam sterownik, wiesz może jak to podłączyć ewentualnie czy trzeba coś dodatkowo ustawić w programie? Próbowałem już chyba wszelkich kombinacji i ciągle nie chcą reagować
-
Właśnie obudowa silnika sama się nie pojawi dlatego się pytałem - teraz wiem, że muszę ją również podłączyć, dzięki Nie wiem jaki cudem ale oś silnika nie ma "połączenia elektrycznego" z obudową zatem przez oś masa "nie przejdzie". Natomiast silniki mam przykręcone do ramy przez amortyzatory gumowe więc przy okazji samoistnie zrobiła się izolacja. Trzeba będzie zatem połączyć wszystko grubymi kablami i powinno być OK .
-
Frezarka bedzie stała w piwnicy w starym bloku więc co do uziemienia to mam powazne wątpliwości jakiej jest jakosci . Byc może kiedyś frezarka pojedzie do teściowej gdzie uziemienie napewno jest (problem w tym, ze wtedy nie będe miał jej "pod ręką") Całośc oczywiście łączę w "jeden obwód" masy ale pytanie czy obudowa silnika tez ma byc z tym obwodem połaczona czy nie.
-
Troche wolno idą prace, ale powoli do przodu Mam przebudowane wszystkie połaczenia w obudowie z elektroniką. wstawiona blacha pomiedzy zasilacz a płytkę sterownika, kable od gnizd przyłaczeniowych silników do sterowniką są ekranowane i podłaczone do masy sterownika. Trzeba jeszcze trochę przerobić kable pomiędzy sterownikiem a silnikami (doprowadzenie masy). Zastanawiam się tylko czy ekran podłaczać do ramy frezarki czy obudowy silnika, czy może jedno i drugie (obecnie wg miernika nie mam połaczenia pomiedzy ramą a obudowa silnika). Podłaczony jest równiez przycisk awaryjnego zatrzymania i reset. W międzyczasie dojechały wyłaczniki krańcowe więc też niedługo je zamontuję.
-
Fajny opis i gratuluję postepów w budowie. Jakis czas temu zacząłem budowę frezarki CNC, zeby ulatwić sobie budowanie modeli a przedewszystkim ziekszyć dokładność wycinanych elementów. Od kilku miesięcy z zapałem przeglądam posty z relacji Wicherków. Juz niedługo (jak tylko skończe pracę z frezarką) mam zamiar zbudowac sobie Wicherka (w rozmiarze 25). Pierwotnie miał to być "oryginał" (juz nawet wiekszość mam zwktoryzowane) ale po przeczytaniu kilku/kilkunatu postów doszedłem do wniosku, że chyba zbuduję wersje 25P z kilkoma usprawnieniami (połączę kilka "papentów" z różnych relacji i dodam kilka własnych ). Będę równiez budował Win-Jinga (najwyższa pora ułatwić sobie budowę skrzydeł ). Juz niedługo załozę swojego własnego posta z relacją a wszystkich zainteresowanych "tartakiem" Wicherka zapraszam do kontaktu ze mną
-
Narazie chce wstawić blachę pomiędzy zasilacz a płyte sterownika i jeszcze troche przerobic mocowanie kabli do silników i wtyków (od strony sterownika) tak aby ekran podłaczyć do ramy frezarki (aluminium) i z drugiej strony połaczyc go z masą sterownika. Moze sie okazać, że dokłasdne frezowanie odcinków 10cm i spore błędy przy odcinkach rzedu 50cm wynikaja z jakiś prądów bładzących lub indukujacych się w jakis "dziwnych" miejscach.
-
No to czeka mnie trochę więcej przeróbek elektroniki
-
Zmieniłem kable na ekranowane - zastanawiam się czy ekran podłączać do masy sterownika... Za dzień lub dwa powinienem mieć czujnik zegarowy ze statywem. Spróbuję jeszcze wstawić jakąś blachę pomiędzy zasilacz a płytkę sterownika, żeby robiła za ekran (może jutro zdążę pojechać ją kupić).
-
Narazie nie chcę kupoać Kressa ze względów ekonomicznych. "Redukcja" w postaci rurki gumowej powoduje, że przy dużym obciążeniu (np. kolizja) "puszcza" czyli zabezpiecza mi wrzeciono. Co prawda muszę wtedy odkręcić silnik i włożyć "redukcję" ponownie, ale wolę tak, niż wysyłać wrzeciono do naprawy. Może kiedyś zamontuję Kressa, ale na pewno nie teraz.