
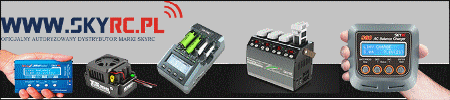
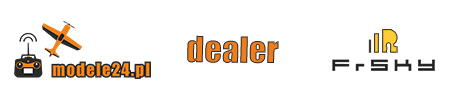
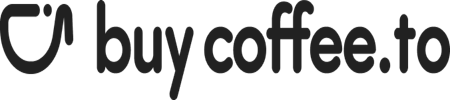
-
Postów
1 036 -
Rejestracja
-
Ostatnia wizyta
-
Wygrane w rankingu
9
Treść opublikowana przez Marek:D
-
Cześć. Ostatnie dni poświęciłem budowie własnej wycinarki do styropianu i chciałbym podzielić się swoim sposobem z innymi, może komuś się przyda. Pierwsza sprawa to transformator. Ja zrobiłem wersję "exclusive". Na początku to co było potrzebne do budowy czyli: - transformator toroidalny 24V 250VA(tak akurat dla mnie pasował, bo plan zakłada drut ok 105cm), - włącznik na dwie żyły - ściemniacz(taki jak do światła natynkowy, 10A) - Voltomierz 30V (ważne żeby był z dopiskiem AC- czyli na prąd zmienny), - Amperomierz 10A AC, - gniazda bananowe, - przewód do zasilania, - dławnica, - puszka na nasze urządzenie. A tutaj już podłączone: Schemat podłącznia wygląda następująco: - dwie żyły od zasilania głównego podłączamy do wyłącznika; - jedna z żył idzie bezpośrednio do transformatora, drugą podłączamy przez ściemniacz do drugiej żyły transformatora; - żyły wtórne - jedna bezpośrednio do banana, druga poprzez amperomierz(szeregowo) leci do drugiego banana; - dodatkowo równolegle wpinamy voltomierz. Układ zasilania mamy gotowy. Następnie ramka do cięcia. Są różne metody napinania drutu, ale ja preferuję najprostsze - układ z napinaniem sprężynami jest dla mnie zbyt skomplikowany. Dlatego ja stosuję sprawdzoną metodę napinania - moja ramka działa na zasadzie łuku refleksyjnego. Napinacz realizowany jest przez sprężynę z szarpaczki(rozrusznika ręcznego) do kosiarki itp. Miałem po prostu taki w warsztacie. Nada się nawet lepiej sprężyna ze zwijaka kabla do odkurzacza - jest szersza. Ja musiałem użyć po trzech sztuk z obu stron, żeby napięcie było solidne. Oczywiście wiercenie takiej sprężyny wymaga zmiany struktury wewnętrznej metalu - należy go nagrzać do czerwoności(wystarczy nad palnikiem gazowym) i powoli ostudzić. Tak przygotowany płaskownik daje się wiercić. Całość mocujemy między dwoma listewkami 10x20. Mocowanie drutu oporowego realizowane jest przez zacisk z kostki elektrycznej. Po rozcięciu plastiku mamy fajne mocowanie, którym łapiemy drut oporowy i przewody wtykane do naszego transformatora. Tak zrobioną ramkę obwinąłem taśmą izolacyjną, umocowałem przewód silikonowy i wywinąłem napinacz w drugą stronę mocując drut. Moja ramka tak się prezentuje: Całość działa, jestem w stanie osiągnąć prąd 24V i 2A co w zupełności wystarcza, układ ściemniacza pozwala na płynną regulację i drut można nagrzewać mniej lub więcej. Dodam tylko, że zastosowałem drut oporowy Nikrothal 80 0.35mm o oporności 11.3 omów na m. Kolejna sprawa to prowadnica. Cięcie elementów trapezowych bądź nawet prostokątnych wymaga równomiernego prowadzenia. Dlatego najlepiej zrobić to mechanicznie. Ja zastosowałem typowe szyny z oprzyrządowaniem ze sklepu elektrycznego, do tego blaszki aluminiowe do mocowania, rolki ze sklepu żeglarskiego do prowadzenia sznurka napinacza oraz kątownik stalowy 20x20mm długości 0,5m. Na taką szynę mocujemy rolki jak na zdjęciu. Nasz kątownik robi za cięgno - jest to dźwignia ze środkiem obrotu przy podstawie. Całośc działa w następujący sposób - za pomocą sznurków łapiemy nasz drut po obu stronach i poprzez rolki mocujemy do kątownika. Mocując w tym samym miejscu - mamy cięcie równoległe. Jeśli różnicujemy odległości mocowania sznurka - jedna strona drutu jedzie szybciej a druga wolniej. Prędkości najprościej obliczyć sobie z twierdzenia talesa - ja jeszcze zrobię podziałkę na swoim kątowniku. Dodatkowo na obu stonach szyny robimy blaszki do mocowania przy naszym stole. Sorki za jakość zdjęć, ale mam nadzieję, że zasadę działania da się zrozumieć(jak zrobię nowe to podmienię):
-
Już się od tego odchodzi, ale zdarzają się inne rozpuszczalniki agresywne dla styropianu. Z tego co pamiętam Epidian 53(staroć) był na styrenie. Większość żywic do laminowania nie ma tego problemu, ale z klejami dwuskładnikowymi bywa różnie. Może ja po prostu miałem takie szczęście, że na taki trafiłem Dokładnie o taki klej chodzi, dobrze doprecyzowałeś Co do aplikacji to prawda, ale ja już nie wyobrażam sobie wklejania w rdzenie styropianowe elementów na inny klej, jest lekki i mocny. Tak jak pisałeś trzeba umieć aplikować. Kiedyś posmarowałem klejem styropian i dziwiłem się czemu skrzydło oklejone balsą jest takie ciężkie i mocne... Poświęcając jeden płat przeciąłem go i okazało się, że klej przeniknął przez cały przekrój styropianu wypełniając wszystkie pory powietrza.
-
Moim zdaniem Andrzejowi chodziło o wcześniejsze sprawdzenie jak żywica reaguje z piankami. W niektórych stosuje się m.in. styren jako rozpuszczalnik, a ten ma destrukcyjne właściwości jeśli chodzi o depron, styropian itp. Także to kwestia rozpuszczalnika. Ja dużo bardziej preferuję klej D4 soudala(puchnący). Przy odpowiednim użytkowaniu spoina jest bardzo mocna bo świetnie klei się do drewna i wnika w pory pianek. Jest też miększa i banalnie się obrabia. Kluczem do sukcesu jest jej racjonalne dozowanie i zwilżenie powierzchni klejonych.
-
Wieśku, dzięki za zwrócenie uwagi. Z tego co pamiętam to chyba masz rację co do firmy styroduru, jutro jak będę na warsztacie to poszukam opakowania może się coś doczytam i zważę jeden listek styroduru. Niestety tylko to mieli w lokalnym markecie budowlanym. Na modelarni mieliśmy też chyba BASF zielony, ale nie wiem jaki typ. Mój żółty był lepszy do zrobienia pylonika, bo przy wciskaniu delikatnie się poddawał jak guma(opis Czarka). Zielony był raczej kruchy i bardziej podobny do pianki pouliretanowej. Ja kupiłem płyty grubości 5cm, ale szperając w necie rzeczywiście zdziwiło mnie, że grubszy styrodur tego samego typu ma większą wytrzymałość w kPa, więc Twoja teoria rzeczywiście ma sens. Ten który mam był bardzo fajny w obróbce i przyjemnie się go szlifowało. Zamawiając Carbovawe przedstawiciel GRM System po dłuższej rozmowie zachęcał mnie do zakupu zamiennika pianki Rohacell w dobrej cenie. Nie do końca wiem jak Rohacell nadałby się do mojej obróbki papierem ściernym i drutem oporowym bo niestety nie miałem go nigdy w rękach. Na razie chyba zostanę przy styrodurze, który mam. Stateczniki zrobiłem z Carbovawe 40g/m^, dźwigar z tkaniny jednokierunkowej 80g/m^(pasek szerokości 6-7mm), do tego aramid 36g/m^ (pasek 10mm). Myślę, że na styrodurze zrzucę max 0,5g na komplecie i nie wiem czy jest sens teraz to robić. To model do nauki DLG, więc na razie zadanie spełni Ale dyskusja idzie w fajnym kierunku, dlatego posłucham więcej takich mądrości
-
Czas mija, a elementów przybywa. Dziś wyjąłem z pieca statecznik pionowy. Za pierwszym razem wyszedł tak jak chciałem, już chyba opanowałem technologię na tyle, że mogę brać się powoli za skrzydła. Komplet stateczników waży 15,2g, te 0,1-0,2 ucieknie jeszcze przy wycinaniu zawiasu i zrobieniu otworków na śruby. Myślę, że jak na taki materiał nie jest źle, szczególnie, że są bardzo mocne. Jak będę miał problemy z wyważeniem to zakupię carbovawe 20g/m i wtedy spokojnie zejdę do 13-14g na komplet. Kolor taki trochę babski, ale mam zasadę, że dół modelu zawsze jest robiony kolorami mocno kontrastującymi(poprzeczne pasy żółtego na czarnym tle modelu), a góra ma mieć taki kolor, żeby łatwo widać było go w trawie i wzory staram się tworzyć wzdłuż skrzydeł. Takie malowania pomagają gdy zaczynamy gubić orientację. Co prawda nie "gubiłem" modelu podczas swojego latania, ale jako początkujący mi to pomagało i jakoś tak zostało. Zabrałem się też za robienie piłki oporowej, skończyłem dziś prawie cały układ zasilania. Zostanie jeszcze sama ramka z drutem oporowym i prowadniczki do drutu. Materiały mam kupione i mam nadzieję w weekend zrobić całość. Jak widać waga już sfatygowana, ale jeszcze działa i przypasowane stery na taśmę klejącą dla poglądu:
-
To zależy od sklejki. Jeśli forniry są z tego samego drewna i jest parzysta ilość to kierunek nie ma znaczenia. Ale jak masz nieparzyste to warto żeberka ułożyć wzdłuż kierunku słoi, ponieważ drewno jest materiałem anizotropowym(nie ma identycznej wytrzymałości w każdym kierunku) i dobrze ułożone włókna mają 10-krotnie większą wytrzymałość niż w drugim kierunku. Kolejna sprawa to żeberka. Widać, że odrysowujesz je ładnie na sklejce, ale żeby były prościutkie należy spiąć je wszystkie w bloczek, zrobić skrajne żeberka jako szablony(ja robiłem z blachy)i szlifować. Chodzi o coś takiego: Wtedy masz pewność, że wszystko jest równiutko i tak jak należy. W przeciwnym razie wszystkie niedoskonałości wyjdą Ci na pokryciu kesonu i folii o czym się na pewno przekonasz(oczywiście będzie to miało wpływ na właściwości lotne). Wiem, że już to skleiłeś, ale warto to zrobić od początku tak jak trzeba. Widzę, że korzystasz z tańszych materiałów, ale warto zainwestować w sklejkę balsowo-lipową. Jest lekka, stosunkowo tania i fajnie nada się do Twojego projektu. Chociaż najlepsza byłaby balsa. Ciężki model na początku kariery potrafi skutecznie zniechęcić modelarza. Chcę, aby wyszło Ci jak najlepiej, dlatego się "czepiam"
-
Patryk dzięki za odpowiedź. Tak właśnie zastanawiałem się jak robi konkurencja i prościej było wyciąć symetryczny, ale już szkoda wykonanej pracy bo mam 4 sztuki niesymetryczne, przycięte, sklejone i obrobione. Jeżeli chodzi o geometrię płatów to raczej trzymam się planów Super GEE II Marka Dreli delikatnie modyfikując wydłużenia(zmniejszyłem wydłużenie stateczników, żeby było troszkę bezpieczniej przy lądowaniu powiększając powierzchnię).
-
Styrodur jest raczej żółtawy, może tak wygląda na zdjęciach. A kupuję normalnie w markecie budowlanym, tylko zwracam uwagę na rodzaj styroduru - są różne gęstości, które zależą od deklarowanych odkształceń - im niższa wartość MPa(z tego co pamiętam to maksymalne obciążenie przy 10% odkształceniu) tym dla nas lepiej bo mniejsza gęstość a pompa i tak CI tego nie zniszczy. To carbowave(czeska tkaniana). Carboline jest ukraińska. Zgodnie z podpowiedziami Czarka zwróciłem się do dystrybutora na PL - GRM System. Mieli najlepszą cenę i towar od ręki. Ps Panowie mam kolejny dylemat... Zabrzmi trochę laicko, ale czy możecie mi wytłumaczyć profil płasko wypukły w stateczniku pionowym z dodatkowym odchyleniem statecznika od osi podłużnej? Mam rozumieć, ze siła nośna wyprodukowana przez statecznik ma być odwrotnie skierowana do siły odśrodkowej podczas wyrzutu? Czy ma to raczej związek z proponowanym kierunkiem krążenia? Jestem praworęczny i jakoś zarówno modelami jak i paralotnia lepiej mi sie kręci w lewo ????
-
Rzeczywiście, zawias z taśmy zdaje egzamin, tylko statecznik spuchł do 8,3g. Dziś wycinałem kolejne rdzenie tym razem do statecznika pionowego. Stwierdziłem, że troszkę zmodyfikuję pierwotne plany i zmniejszyłem wydłużenie statecznika powiększając jego powierzchnię do ok 2 dm^2. Wagowo będzie ciut ciężej, ale będzie mniejszy moment zginający na końcu belki ogonowej podczas lądowania. Na razie szykuje mi się zajęty tydzień, obecnie kompletuję sprzęt do wykonania własnej piły do cięcia styropianu z całym oprzyrządowaniem. Także kolejne postępy dopiero za tydzień. A tu już docięte i sklejone ze sobą na klej piankowy 4 sztuki stateczników: Wyjąłem też niedzielny statecznik poziomy. Wyszedł ładnie, zgrabnie, będzie do najlepszej wersji. Waży po wycięciu rowka 7,8g.
-
Dziś wyjąłem kolejny statecznik. Efekt wizualny super, nie ma wizualnego niedosączenia w rejonie dźwigara. Całość wyszła zgrabnie. Tym razem robiłem statecznik odsączając mylary 8 warstwami ręcznika papierowego w efekcie czego środkowa warstwa była praktycznie sucha - czyli tak ma być. Widocznie mam jeszcze skłonności do dawania zbyt dużej ilości żywicy. Aby łatwiej było dostrzegać na ręcznikach niedosączenia żywicę barwię czarnym pigmentem - dodatkowo aramidowy zawias robi się bardziej czarny i kolor nie przebija przez węgiel. Ku mojej uciesze statecznik waży równiutko 8,0g. Czyli tyle ile mnie satysfakcjonuje Niestety konkretnie dałem ciała podczas wykonywanie rowka na zawiaski. Machnąłem się 0,5cm w wymiarach i zrobiłem rowek na krawędzi aramidu - czego efektem jest to, że połowa wisi na aramidzie a druga połowa jest przecięta na wylot. Byłem na siebie strasznie zły, bo statecznik wyszedł fajnie wagowo a tu taka wtopa... Myślicie, że można to uratować robiąc zawias z taśmy? Najwyżej pójdzie on do "najlepszego odpadu". Zniesmaczony swoim błędem zrobiłem dziś kolejny, czwarty statecznik poziomy. Jutro wyjmę całość i zobaczymy jak wyszło, ale myślę, że jestem w stanie osiągnąć te 8,0g. W przyszłym tygodniu będę też wycinać statecznik pionowy, także mam nadzieję, że jak czas pozwoli uda mi się skończyć usterzenie. Zostaną tylko skrzydła. W międzyczasie planuję też zrobić ramkę do samodzielnego wycinania profili ze styroduru wraz z całym osprzętem prowadzącym drut - ale to chyba opiszę w dziale warsztatu, jako swoisty przewodnik. Fotki tego jak to wygląda:
-
Tych próbników trochę się nazbiera, ale z czasem będzie ich coraz mniej Dziś wyjąłem z pieca statecznik. Wizualnie i konstrukcyjnie wyszedł fajnie, jedyne co to w kolejnym muszę schować dźwigar pod spód, bo na krawędzi widać "niebłyszczącą" powierzchnię carbowave. I najważniejsze. Już w rękach dało się odczuć, że jest lżej, ale całość zweryfikowała waga. Pokazała równo 8,5g. Czy to sukces? Myślę, że na razie zadowalający wynik. Myślę, że na moich użytych materiałach i za bardzo nie oszczędzę, więc trzeba by było myśleć o zrobieniu większego wydłużenia i zmianie materiału. Jak da się z tym wyważyć to będzie ok. Mam nadzieję, że statecznik poziomy będzie lżejszy bo ma być mniejszy i powinienem osiągnąć coś w granicach 7g. Czyli 15,5g komplet. Najwyżej później dokupię sobie carbowave 20g/m^ i z tego zrobię stateczniki. Jestem natomiast bardzo zadowolony ze sztywności. W porównaniu do pierwszej sztuki jest porównywalny na zginanie, ale dużo mocniejszy na skręcanie. Na moje początki będzie w sam raz W sobotę zrobię kolejny i na razie będę czekał na wycięcie kolejnych rdzeni statecznika pionowego. Ale efekt wizualny mi się podoba
-
Bez przesady, manualnie coś tam umiem, ale niestety utyka u mnie teoria. Dziś zrobiłem kolejny statecznik, tym razem na carbowave i malowany. Profile z wklejkami balsowymi praktycznie nie przytyły, w dwóch z nich różnica to 0,1g: Zmartwiony wagą poprzedniego statecznika zacząłem szukać przyczyny... A więc ważyłem wszystko po kolei: - rdzeń styrodurowy - 3.0 - 3.1g - rdzeń z oklejonym natarciem z carbowave oraz zawiaskiem z aramidu - 3.7-3.8g - dźwigar nośny z węgla jednokierunkowego 80g/m^ szerokości 5mm - dwie strony łącznie 0,5g(myślałem o zastosowaniu rowingu, ale niestety mam tylko cięższe) - tkanina carbowave z naddatkami na obie strony - 2.8g. Trochę mnie to zmartwiło bo na starcie mam już 7,0g bez żywicy. Dlatego poprzednik wyszedł ciężko. Szperałem też w wątku Czarka z HERO i tam styrodur na rdzeń waży 2,7g - sądzę, że po prostu mój statecznik ma większą powierzchnię nośną i stąd taki rozrzut. Mój ma ok 2.35dm^ a Czarka 2,2. Na styrodurze wagi nie zbiję i będę miał ok 8-8,5g na stateczniku poziomym. Tego już nie zmniejszę. Można by było zbić wagę carbowave 20g/m^ (odpada teoretycznie 1,4g) i przejściem na Rohacell(kolejne 0,5-1g). Wtedy waga zbliży się do konkurencji, ale nie będę kupował specjalnie materiałów na ogon. Po prostu zrobię najlżejszy jaki się da z tego co jest, myślę, że komplet będzie ważyć ok 16g do lotu. Szału nie ma ale tragedii chyba też nie bo powinienem to jakoś wyważyć. Dziś, żeby było jeszcze optymalniej z masą żywicy przed laminowaniem podgrzałem ją do 40 stopni, żeby była bardziej płynna a odsączanie prowadziłem w worku próżniowym dodatkowo z dociskiem. Jutro wyjmę efekt z pieca.
-
Wczoraj też tak pomyślałem, ale już po wklejeniu... Zostanie zrobić na zwykłe śruby z płaskim łbem tylko schowanym w grubości statecznika. Ewentualnie dowiercenie stożka i przesądzenie CA. Myślę, że opcja nr 1 zostanie, bo mam akurat śruby plastikowe czarne M3 i ładnie by się schowały. Łeb trochę stoczę na mniejszą średnicę, jakby było za szeroko. PS nie jest tak różowo. Waga wczoraj po przeczyszczeniu pokazała statecznik jako 10,5g,co dla mnie jest kataklizmem. Dziś próbuję na carbowave i lepiej odsączę żywicę. Zobaczymy co wyjdzie.
-
Dzięki za podpowiedź, tak spróbuję zrobić w kolejnych sztukach. W rdzeniach umieszczę polakierowane balsowe kołeczki układając włókna równolegle do osi śruby. Takie rozwiązanie powinno się sprawdzić. Później jak będzie za miękko to balsę można zakropić CA i będzie jak skała.
-
A mam jeszcze jedno małe pytanie. Czy robicie jakieś tulejki/gniazda pod śruby w statecznikach? Chodzi o jakieś wypełnienie np żywicą z mikrobalonem w rdzeniu tak, żeby po przykręceniu nie wciskało powłoki z tkaniny do środka rdzenia? Planuję śruby z łbem stożkowym. Nie do końca wiem czy to się robi przed czy po oklejeniu... Tej informacji nigdzie niestety nie znalazłem. Czy pręt do sprężynki ma grubość 0,6-0,8mm?
-
O matko, nawet o tym nie pomyślałem... No nic, statecznik będzie jako próbnik
-
Chłopaki dzięki za miłe słowa. Dla mnie skarbnicą wiedzy były też wątki Czarka i Patryka i wszelkie podpowiedzi chłopaków i Rafała za co jestem też wdzięczny. Mój wątek mam nadzieję, że zbiera te wszystkie rzeczy do kupy, aby przyszły amator wyrobów z laminatu miał gdzie podejrzeć technologię, którą jest w stanie wykonać. Korzystając z okazji mam pytanko. W tej chwili zrobiłem zawias na górnej powierzchni steru wysokości, ale czy są jakieś przeciwwskazania co do tego? Czy raczej robi się zawias od dołu? Czarku a jak Tobie wypada SC pustego kadłuba z ciekawości?
-
Statecznik wyjęty z pieca, wygląda na to, że wszystko wyszło tak jak powinno Delikatnie przyszlifowałem natarcie i wystające tkaniny ładnie odpadły. Fotki jeszcze bez przyciętej krawędzi spływu: I przycięty spływ(jak widać spływ jest równiutki): Przyłożony statecznik do kadłuba: Wszystko wygląda fajnie. Waga pokazała 7,5g, ale trochę temu nie ufam(wcześniej pokazała 5g), bo waga mi ostatnio szwankuje. Kupię nową i zważę jeszcze raz, aczkolwiek te 7,5g jest satysfakcjonujące jak dla mnie. Wersja z carboline będzie lżejsza - sama tkanina pokrycia to zamiast 48g/m^ będzie 40g/m^, odpadają wzmocnienia końcówek i główny dźwigar będzie o połowę cieńszy. Myślę, że jestem w stanie uzyskać wagę poniżej 7g więc powinno być ok. Ten statecznik idzie do mojej wersji "najlepszego odpadu" na której będę uczył się latać DLG.
-
Dzięki za podpowiedzi. Jeżeli chodzi o negatyw to się trochę jeszcze zastanawiam z tego względu, że mała geometria i duże skosy sprawiły że końcowa cięciwa od większej temperatury delikatnie się wygięła i obawiam się że w negatywie mogę mieć podobnie, dlatego zastosuję rozwiązanie z dociskiem z filmiku. Malowanie to pewnie dopiero po prototypach EDIT 27.01.2018 OPISZĘ CAŁY PROCES ŁOPATOLOGICZNIE, BO MOŻE SIĘ TO PRZYDAĆ DLG-owcom WYKONUJĄCYM NAPRAWY Dziś udało się zrobić jeden statecznik. Po sklejeniu wszystkich trzeba było je trochę obrobić do pożądanej geometrii i o tym chcę trochę napisać. Każdy może wykonać to we własnym zakresie także myślę, że moje uwagi mogą być komuś przydatne Stateczniki z braku kleju skleiłem żywicą. Nie jest to najlepsze rozwiązanie, bo osobiście uważam, że klejenie powinno być wykonywane klejem, który podobnie zeszlifowuje się jak materiał podstawowy. Dzięki temu nie mamy "górek" w miejscu klejenia. Do takich operacji najlepszy jest pouliretanowy klej puchnący - główne oznaczenie to D4. Proponuję zakup małych ilości(250ml) ze względu na to, że klej wiąże pod wpływem wilgoci i po dłuższym leżakowaniu w szafie sam wiąże w środku. Mamy wtedy klej do wyrzucenia. Bardzo ważne jest dokładne zakręcanie kleju i jak najkrótsze jego otwarcie. Kolejna wskazówka - pracujemy z klejem tylko w rękawiczkach bo jest okropny jeśli chodzi o czyszczenie. Używamy minimalnych ilości dodatkowo zwilżając fragmenty klejone - najlepiej robić to wodą w popularnych spryskiwaczach po płynie do szyb. Klejenie wykonujemy na folii której nie bierze żaden klej. Ja przykładowo robię to na zużytych workach do Vacu, ale tanim i dobrym odpowiednikiem jest folia z kwiaciarni do owijania kwiatów - sprawuje się super i jest tania. Kolejnym krokiem jest wycięcie ostatecznego kształtu. Ja ztobiłem sobie szablon, odrysowałem kształt i wyciąłem całość nożykiem introligatorskim. Ważne jest, żeby nóż był ostry i tniemy trzymając nóż jak najbliżej pozycji poziomej - unikniemy efektu zaciągania styroduru. Po sklejeniu musimy całość oszlifować, bo na statecznikach zostają nam ślady druta oporowego i im lepiej dopracowany rdzeń tym lepiej wyjdzie efekt końcowy. Przykład widoczności drutu oporowego: Najprostszą metodą jest szlifowanie aż do uzyskania matowej powierzchni - po drucie oporowym mamy powierzchnię świecącą. Szlifowanie trzeba wykonywać bardzo ostrożnie, zalecam papier ścierny 240(ja robiłem 180 ale wymaga to już wprawy, którą nabyłem pracując za młodu dorywczo 5 lat w stolarni i przy lakierowaniu). Papier mocujemy najlepiej na odpadzie styroduru. Nie zalecam zakładania papieru na popularne uchwyty bo nie mamy wtedy żadnego wyczucia i mało widzimy co dzieje się pod spodem. Ponadto ważne jest aby praktycznie nie naciskać klockiem do styroduru, bo narobimy głębokich śladów. Szlifujemy tak, aby cały klocek stykał się ze statecznikiem i opierał się na jak największej powierzchni statecznika. Powoli dojdziemy do wprawy. Oczywiście musimy manualnie zrobić nosek na natarciu. Zalecam zrobienie sobie małego klocka ściętego pod kątem i powolne wyciąganie profilu. Ja robiłem to bez przyrządów - da się. Po całej operacji warto mieć gąbeczkę z papierem ściernym, która idealnie dopasuje się do kształtu noska profilu i przejechać kilka razy po natarciu, efekt jest na prawdę super. Trzeba też uważać i się nie spieszyć - ja przez to drugie jeden schrzaniłem Ważne jest aby szlifować w jednym kierunku, wtedy minimalizujemy ryzyko uszkodzenia cienkiego profilu. Do szlifowania nada się też zamiast klocka styroduru klocek korkowy, który dostaniemy w klepach dla lakierników, podobnie jak papier na gąbce. Oczywiście wcześniej szykujemy mylar do oklejenia stateczników. Ja zastosowałem mylar 0,35mm. Wycinam idealnie kształt szablonu zostawiając 1cm naddatku przy krawędzi spływu. Pozwoli to na wykonanie lepszej krawędzi i sklei ładnie całość. Na mylarach dodatkowo zaznaczyłem sobie gdzie kończy się profil, ale o tym napiszę później. Można oczywiście zrobić całość bez worka próżniowego w negatywach, ale ja mam dostęp do wora więc postanowiłem, że zrobię to tą technologią. Prawdziwy modelarz radzi sobie przyrządami dostępnymi wszędzie i dzięki temu może oszczędzić parę groszy Ja przykładowo worek próżniowy sklejam zwykłą taśmą pakową - jest oczywiście możliwość zrobienia to taśmą przeznaczoną do worków vacu ale po co skoro ta też zdaje egzamin. Podobnie materiał odsączający - w sklepach z laminatami kupimy świetne sączki, ale czy na prawdę trzeba? Ja kupiłem ręcznik papierowy w Biedronce - koszt mniejszy a funkcjonalność ta sama. Co więcej ręcznik ma tą przewagę, że za każdym razem go wymieniam i dłużej żyją moje worki, bo nadmiar żywicy, który wypływa usztywnia ręcznik/sączek i staje się on na tyle twardy, że przy kolejnych laminowaniach potrafi przeciąć worek. Ręcznik dajemy na całości, bo tamtędy przepływa powietrze, które wyciąga pompa. Można też stosować specjalne uchwyty do węża vacu - ja zamiast tego daję krótką rurkę zakończoną sączkiem/ręcznikiem papierowym, żeby nie było ostrych krawędzi. I w taki oto sposób mamy tańsze Vacu Warto przed procesem sprawdzić działanie całego układu - szczególnie czy nie ma żadnych dziurek, którymi może uciekać powietrze itp.Później zwyczajnie nie ma na to czasu i dochodzi nam tylko dodatkowy stres. Ja worek zamykam rurką i gniazdem ze sklepu elektrycznego. Sprawuje się to fajnie, ale traci troszkę szczelność z czasem. Normalnie można to zakleić taśmą, ale ja używam tego rozwiązania, bo nasza pompa vacu ma układ, w którym zadajemy minimalne ciśnienie i po prostu po jego spadku pompa samoczynnie się uruchamia, wypompowuje powietrze i tak w kółko. Następnie czeka nas zrobienie wzmocnienia krawędzi natarcia oraz zrobienie zawiasu z aramidu. Ja zastosowałem folię 3M 904 - cieniutka błona taśmy dwustronnej. Naklejam ją pod kątem 45 stopni na szkło i wycinam całość na szerokość taśmy. Ma to ten atut w porównaniu do kleju w sprayu, że tkanina nam się mniej rozjeżdża. Przyklejone na suchy rdzeń: Przygotowałem też szablon do zrobienia statecznika z płyty wiórowej. Żal było nie kupić, bo odpady w castoramie kosztowały 3zł a do tego celu nadadzą się idealnie: Po przygotowaniach robimy stateczniki. Ja do tego użyłem żywicy LH160 z racji jej mniejszej lepkości w stosunku do L285. LH160 jest tańszą, aczkolwiek równie dobrą żywicą. Jej jedyny minus jest taki, że nie za bardzo lubi pracę poniżej 25 stopni. Dłużej osiąga pełną wytrzymałość i trzeba ją wtedy wygrzać. Ogólnie rzecz biorąc mając 20 stopni w warsztacie robiąc coś na szybko kolejnego dnia mogę spokojnie szlifować elementy wykonane z L285 bez grzania, zaś LH160 muszę wygrzać. Do całości dodałem żółty barwnik. Wałeczkiem przesączyłem tkaninę szklaną ułożoną pod kątem 45x45 o gramaturze 48g/m^, paski wzmocnienia węglowego zrobiłem z tkaniny o gramaturze 80g/m^ bo takie ścinki zostały nam z DYFu 160g/m^. Zawias to aramid 36g/m^ ułożony pod kątem 30/60 stopni. Dodatkowo końcówką wałeczka przesączyłem natarcie oraz zawias na rdzeniu:(sory za jakość fotki) Rdzeń odsączyłem ręcznie ręcznikiem papierowym a mylary przełożyłem 3 warstwami ręcznika papierowego i całość obciążyłem tak jak podpowiedział Rafał. Metoda rzeczywiście wydaje się lepsza od odsączania wałkiem do tapet, bo dzieje się to równomiernie. U mnie środkowa warstwa ręcznika też wyciągnęła trochę żywicy więc kolejnym razem dam więcej warstw, bo może być za bogato z żywicą. Po odsączeniu przykładam rdzeń do jednej połówki i dodatkowo smaruję żywicą sam spływ poza rdzeniem, aby dobrze się to skleiło. Po zabiegu przykładam drugą połówkę i mocuję całość montażowo taśmą. Po takich zabiegach całość wkładam do wora i do pieca. Druga linia na mylarze oznacza koniec profilu za którym smaruję dodatkowo żywicą, aby idealnie skleić dwa myalry. Piec ustawiłem na 40 stopni. Dzięki temu żywica lepiej się rozpłynie i wypełni przestrzenie między włókienkami tkaniny. Ponadto jutro będę miał pełną wytrzymałość laminatu, który będzie gotowy do obróbki. Jeżeli nie macie pieca można go zrobić samemu - bardzo sprytne rozwiązania są w filmikach które przytoczyłem poprzednio. Gość ma skrzynkę ze styroduru gr 5cm, a w środku dwie żarówki 240W. Wkłada całość do środka i może na tym osiągnąć 50 stopni czyli idealną temperaturę. Przyda się to zarówno do robienia stateczników, skrzydeł jak i kadłuba. Jak wyniosę się z warsztatu i zrobię swój własny - to właśnie takie urządzenie sobie zmontuję. Jutro wyciągnę całość i zobaczymy co wyszło
-
Patryku uważasz, że dzieje się to ze względu na barwnik czy grubość szkła? W takim razie spróbuję z 48g/m^ bo taki też mam. Koloru idealnego nie uzyskam bo jest za mało warstw, chodzi jedynie o zabarwienie Z ciekawości zapytam jakich barwników używasz? Ja sugerowałem się filmikiem, ale autor daje dosyć bogato pigment i już go namierzyłem, jest to barwnik z R&G ale cena jak dla mnie kosmos... Rafał mam też mylar 0,35mm, kupiłem właśnie dwa rodzaje. Myślisz, że grubszy będzie lepszy? Do odsączania kupiłem właśnie dzisiaj dodatkowo wałek do dociskania tapety, razem z ręcznikiem papierowym powinno zdać egzamin. W takim wypadku jeśli będę miał możliwość to wsadzę całość do pieca na 40 stopni razem z worem(nie pamiętam czy mamy zrobioną rurkę prowadzącą do pieca). Dzięki za porady.
-
Czarku sprawdziłem i w kadłubie nr 5 wypada idealnie na końcu cięciwy skrzydła. W kadłubie nr 3 jest jest różnica 1,5cm w kierunku krawędzi natarcia skrzydła. Nie wiem czy to źle czy dobrze, ale serwa do napędu lotek planowałem rozmieścić w zależności właśnie od wyważenia. Schowam je w kadłubie albo skrzydłach. Dziś wycięliśmy drugą połowę statecznika. Mam już po 5 sztuk. W weekend będę z nimi walczyć. Jeżeli chodzi o natarcie to chyba wiem o co chodzi, chciałem właśnie zapytać o ile mylarowa folia ma być krótsza na natarciu? Widziałem u nas w modelarni skrzydła niewypały robione technologią na mylarze i efekt był właśnie taki, że mylar zaczynał odłazić od noska jak był za długi. Słabo, ale trochę widać: Dodatkowo przyszła dziś taśma 3M do przyklejenia natarcia noska. Na Rc groups znalazłem o jaką chodzi i zrobiłem dziś próbę. Wyszło fajnie, na klej w sprayu miałem obawy z tego względu, że drobna tkanina 25g/m^ cięta pod kątem 45/45 będzie rozłazić się w palcach, a na taśmie jest lepiej. Oto próbka: Przed pracą obejrzałem wszystkie filmy Norberta Wigbelsa - bardzo przydatne. Użyje mylaru 0,25mm. Pierwsze sztuki na szkle 25g/m^ z żywicą barwioną. Zobaczymy jak będzie wychodzić.
-
Dzięki za dobre słowa Pylonik już oszlifowany i spolerowany, nie wygląda tak źle. Przybyło 0,05g. Dodatkowo zaczęliśmy wycinać stateczniki. Idzie wolno, bo powoli jestem wdrażany w obsługę maszyny, także dziś udało się wyciąć pięć sztuk prawych stron statecznika poziomego Jutro lecą lewe strony i powoli będę brać się za robienie statecznika. W międzyczasie oczywiście powstawać będą kolejne elementy ze styroduru. Na razie zgłębiłem wiedzę teoretyczną na rcgroups oraz YT na temat oklejania mylarem, reszta wyjdzie w praniu.
-
Obecnie mieszkam i pracuję w Białymstoku, ale tutaj niestety nie znam miejscowych, a zimą pewnie na lotnisku nikogo nie ma. Jak tylko pojawi się pogoda to podjadę i popytam miejscowych Bardzo chciałbym wyrobić się do wiosny, bo jak wiadomo wczesna wiosna to najmocniejsza termika i fajnie by było się na nią załapać. Jak tylko zbuduję model i nauczę się go rzucać to chętnie odwiedzę innych pasjonatów tego rodzaju modelarstwa, kilometry to nie przeszkoda Węgiel jednokierunkowy zamawiałem w Havlu, ale 80g na prawdę źle się sprawuje. Kadłub nr 5 miał mieć właśnie węgiel 80, ale przy przesycaniu włókienka bardzo lubią nawijać się na wałeczek co doprowadza mnie do szału. Miałem jeszcze 100g ze starszych zapasów i z tym pracuje się zupełnie inaczej. Kupiłem też 125 i z tym też się dużo lepiej pracuje, ale do mojej konstrukcji jest za ciężki. Jeżeli chodzi o balon to niczym go nie smaruję, sam pięknie odchodzi. Balon z makaronu ma te zalety, że nie potrzebuje rurki w środku i można go łatwo ułożyć na sucho w formie. Ja jak pisałem wcześniej pomagam sobie pompą próżniową, dzięki której odpompowuję powietrze z balona podczas jego układania w formie. Tak przygotowany balonik robię na styk na długość w formie. Za krótki być nie może z tego względu, że balon ma małą odkształcalność. Rurka do połączenia z kompresorem siedzi minimalnie w formie - generalnie im dłuższa siedzi w formie tym ciężej ją ułożyć i tkanina zamiast ułożyć się na zakładkę potrafi wyłazić. Pompowanie balonu robię tak - na początku bardzo wolno żeby się ułożył, tak do 2 barów. Formę od razu skręcam na maksa - tylko co jakiś odcinek naklejam kawałek taśmy pomiędzy połówkami formy, żeby łatwiej mogła wyleźć żywica i powietrze. Jak tylko złapie 2 bary podbijam do 6 i odłączam kompresor(50l) od prądu. Przez kolejne 20-30 minut robię coś tam innego i jeśli fajnie trzyma się ciśnienie to uciekam do domu. Robienie kadłuba nauczyło mnie jednego - warto na formę nałożyć trochę żywicy, zaś tkaniny przesycać wałeczkiem "na styk". Nadmiar i tak zostanie wypchnięty. Podstawą jest też przygotowanie WSZYSTKIEGO co potrzebne do laminowania czyli: pocięte tkaniny, nożyczki, balon, przygotowane ściski do form, deska na sznurek do wiązania połówki, barwniki, dużo pomaga też talerz jednorazowy z którego dużo wygodniej nabierać żywicę wałkiem, młotek do wbicia kołków ustalających, śruby do skręcenia całośći, klucz najlepiej z treszczotką albo wkrętarka, nitka do zakładu(ja stosowałem nylonowe, ale wiem, że fajnie spisuje się też żyłka wędkarska, kevlarowe były fajne bo cienkie, ale ciężko je przecinać mimo, że mam nożyce do aramidu) i inne przyrządy. Jak już zacznie się laminowanie to pomimo sprawnej pracy czas mija nieubłaganie i mi zawsze cały proces zajmuje ok 1h, stosuję najwolniejszy utwardzacz do żywicy. Ogólnie kolejne kadłuby robiłem szybciej i mam wrażenie, że mniej lepka żywica jest lepsza, bo więcej jej ewentualnego nadmiaru wychodzi na zewnątrz. Styrodur pylonika oczywiście nafrezowanym pod żywicę z mikrobalonem - pod przyszłe mocowanie śrub musi być dobrze doszlifowany i odpowiednio większy, żeby nie wyszło tak jak w moim ostatnim kadłubie. Ma wchodzić z lekki oporem. Jeśli chcemy zrobić to lekko to w środku pylonika musi być mało żywicy, jak damy za dużo to jej nadmiar nie ma którędy wyjść. Ja przesycam tkaninę na pylonik, delikatnie układam ją na pyloniku, całość wciskam dosyć konkretnie w formę i drugą stroną pędzla dociskam styrodur. Jak wiadomo styrodur jeden drugiemu nie równy i ważne, żeby wybrać najmniej kruchy. Pod śruby skrzydeł stosowałem sklejkę 4mm lipowo - balsową. Po jej przewierceniu i nagwintowaniu nasączę całosć CA i kilka razy poprawiam gwintownikiem. Takie mocowania stosowałem wielokrotnie i sprawowały się wyśmienicie. Jak się sprawdzi żywica z mikrobalonem w pyloniku to zobaczymy. Podsumowując robienie kadłuba nie jest proste jak się niektórym wydaje. Ja mając zaplecze zrobiłem sam formy i kolejne kadłuby. Do tej pory nie licząc narzędzi wydałem ok 1200-1500zł i mam materiał oczywiście na kilka sztuk kadłubów oraz skrzydeł z dobrych jakościowo materiałów. A sprężarka, pompa próżniowa, nawet głupie nożyczki do aramidu kosztują. Co więcej trzeba mieć doświadczenie w laminatach bo niestety ciężko jest to zrobić z marszu. Mam nadzieję, że najgorsze już za mną. Ale jak widać nawet bez frezarki da się własnoręcznie zrobić kopyto i formę, bo liczą się przede wszystkim chęci
-
Czarku, gdyby nie wątek o Virgosie/wątek Patryka o Spinaczu i Wasze podpowiedzi to tych iteracji byłoby dużo więcej A tak z 5 iteracji mniej zrobiłem bo miałem podstawy teoretyczne, reszta to po prostu trening i praca. Najważniejsze, że cel osiągnięty. Moim największym problemem jest to, że nie miałem nigdy w ręku modelu DLG i nawet ciężko mi się do czegokolwiek odnieść, czy jest dobrze, czy za słabo. Mimo to myślę, że moje kadłuby w zupełności mi wystarczą i będą dobrą bazą do budowy fajnego szybowca. Pozdrawiam, Marek