
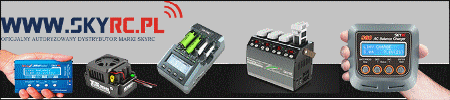
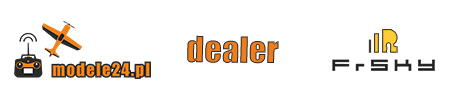
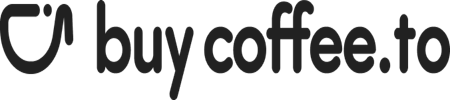
-
Postów
137 -
Rejestracja
-
Ostatnia wizyta
-
Wygrane w rankingu
4
Ostatnia wygrana Karollo w dniu 13 Marca 2018
Użytkownicy przyznają Karollo punkty reputacji!
Reputacja
116 ExcellentO Karollo
- Urodziny 20.06.1990
Informacje o profilu
-
Płeć
Mężczyzna
-
Skąd
Białystok
-
Zainteresowania
Elektronika, mechanika, technika lotnicza
-
Imię
Karol
-
Zdalnie sterowany Jakieś rodzaje prób prawdopodobnie. Na filmie widać wewnątrz jakiś dziwny element, za owiewką. Coś w rodzaju statywu z kamerą.
-
Dzięki za podpowiedź z tymi lotkami w górę Przygotowałem już nawet miksy na moim er9x i lotki są na oddzielnych kanałach. Więc przy następnym oblocie wypróbuję ten sposób. Już tak latałem depronową Spectre Andrew Newtona, tzn z wychylonymi lotkami w górę podchodziłem do lądowania i w ten sposób model bardzo się stabilizował i chyba faktycznie zwalniał, ale to dawno było. Rafik wisi już przygotowany pod sufitem. Ale myślę jeszcze o dodaniu biało czarnych znaków na spodzie skrzydła, np. na natarciu, bo mam problem z oceną położenia z dalszej odległości Coś na wzór pasów inwazyjnych lub szachownicę.
-
Podwozie zmienione, jeszcze osadzić kółka mi zostało i uzupełnić folię. Drut fi 2,5 mocowany na zasadzie rozprężania w kadłub przez szczelinę. Wyszło elastycznie i lekko, z dużym ugięciem podwozia w razie ostrego przyziemienia.
-
Dziękuję, może to i jest sposób, nie pomyślałem o tym.
-
Napęd zmieniłem dzień przed na zakupiony od kolegi na tym forum sunnysky x2216 kv1250, ze śmigłem 9x4.7 SF. Ten jest 20g cięższy i mocniejszy od poprzednika. Wahałem się czy robić skłon i wykłon od razu i nie zrobiłem. Wszystko jest na 0. Kilka przelotów i lądowań to za mało żeby coś powiedzieć, wydawało się że leci po sznurku. Nie ma tendencji do zadzierania na pełnej mocy. Podwozie to mój błąd przy ostatnim lądowaniu, za ostro zszedłem z wysokości i wyprostowanie lotu było równo z trawą. Ale też jest to mój błąd konstrukcyjny, ponieważ podwozie wysunąłem skrajnie do przodu a tam nie było wzmocnienia i ta sklejka miała prawo się tak złożyć. Podwozie oczywiście odbuduję, ale nie wiem czy takie sztywne czy jednak nie druciane.
-
Jest szybki, słucha się sterów, poleciał bez trymowania prościutko. Próbowałem też wolniej polatać i jest to osiągalne ale słaby ze mnie pilot Lotnisko miałem marne, duża trawa szybko hamuje przy lądowaniu, więc wyrwałem podwozie... Ale pierwsze koty za płoty i trochę polatałem.
-
odbudowa Mustang P51 1:5 Phoenix odbudowa skrzydła
Karollo odpowiedział(a) na grabek1985 temat w Półmakiety
Wydawało się że jest beznadziejnie... a tu się wyłania zarys skrzydła Szlifujesz przypalonkę po laserze? Niby nadmuch trochę poprawia przy cięciu sytuację z przypalaniem. Ostatnie pytanie co to za program do projektowania? DS mechanical? -
Rafik poskładany, waga gotowego na oblot wyniosła 765g (z akumulatorem). Było by nawet mniej, gdyby nie to że brakuje na nosie 40g... i po co było ucinać. 😵💫 Wydłużyłem mocowanie silnika, ale zastanawiam się nad lepszym i delikatnie cięższym napędem. Akumulator poszedł większy, na razie 3s Li-ion. Może poskładam pakiety 4s. Regulator nadwymiarowy 40A ale łyknie w razie czego 4s. Kółko ogonowe połączone ze sterem kierunku. Podwozie główne jednak poszło zakupione węglowe. Tu można by zmienić na coś mniej sztywniejszego. Konieczne oddalenie silnika zrobione na podkładkach aluminiowych. Docelowo propsafer zniknie jak lepiej opanuję sztukę lądowania
-
Dziękuję za podpowiedzi, mój też wyszedł szczelny w części ogonowej i tu już nie zrobię przewietrzania, bo musiał bym zerwać trochę folii i dziurawić wręgi. Przez ażurowanie, piasek i inne brudy będą osadzały się na folii. Myślałem o otworach w dolnej lub bocznej części kadłuba, pod skrzydłem. W grę wchodzi wylot podobny do tego na klapce od komory akumulatora.
-
Skończyłem pokrywanie folią Folia transparentna z kavana troszkę się różni od oracover. Wcześniej oklejałem wyłącznie oracoverem ale nie transparentnym i mam wrażenie że kavan słabiej się kurczy, ale przede wszystkim kolor znajduje się w warstwie kleju, co jest minusem. Na plus jest cena i do reszty idzie się przyzwyczaić. Kolorystyka modelu przypomina mi latające zwierzę: W wyniku czego Rafik dostał imię: "Szerszeń" 😀 Do zrobienia zostało podwozie, miało być gotowe, jednak zamówione jest zbyt sztywne. Pracuję też nad wietrzeniem komory akumulatora i regulatora.
-
Miała być maska, jednak po przemyśleniach zmieniłem to. Im dłużej ciągnie się budowa, tym bardziej zmienia się koncepcja Trzeba szybciej kończyć to choć trochę z niego zostanie 😆 Podwozie zamówione, folia już dotarła, więc ostatnie szlify i kryję. Edytowano 19.03 Folia transparentna już częściowo na modelu. Pierwszy raz kryję transparentną, najgorzej idzie z zakładkami.
-
Dziękuję koledze Radosławowi ze sklepu OL-PEN MODEL Modelarski.com za super prezent w postaci kalendarza! Tego się nie spodziewałem miły upominek. Paczka jak zwykle super zabezpieczona
-
Napędy sterów wykonane, jeszcze zabezpieczenia na SW nie ma. Powoli zbliża się czas pokrycia całości, ale przed tym żmudne oszlifowanie kantów i dopieszczenie. Waga na tą chwilę z 4 serwami pokazuje 350g (bez silnika). Jeszcze nie wiem czy kółko ogonowe ma być sterowane. Podwozie raczej gotowe, z węgla lub duralu. Maska drukowana z PETG.
-
Jeszcze wszystko nie zostało złożone razem. Bardziej chodziło mi o wygląd, taki ażurowany kadłub dodaje lekkości konstrukcji. Brakowało właśnie prześwitującego kadłuba, ponieważ te miejsca zostaną przykryte folią transparentną.
-
Chwila nieuwagi... kadłub podziurawiony. Ta operacja ujęła 10% masy kadłuba i to z ogona. Sztywność przed operacją była ogromna, kawał balso-sklejkowego klocka ulepiłem. Po wycięciu otworów jest dalej sztywno. Co prawda lekko zmieniła się odporność na skręcanie, ale jest dobrze