
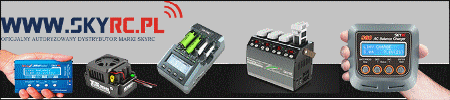
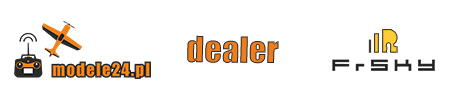
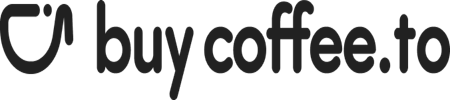
-
Postów
396 -
Rejestracja
-
Ostatnia wizyta
-
Wygrane w rankingu
14
Treść opublikowana przez widar123
- Poprzednia
- 1
- 2
- 3
- 4
- 5
- 6
- 7
- Dalej
-
Strona 2 z 10
-
P51D Mustang czyli narodziny legendy :-)
widar123 odpowiedział(a) na Chuck Yeager temat w Półmakiety
Nie wiem czy dokładnie taka sama, bo występuje pod wieloma nazwami, ale szkielet jest wspólny, a chodzi tu o tokarkę TYTAN 350 i myślę, że się nie pomyliłem ;-) -
P51D Mustang czyli narodziny legendy :-)
widar123 odpowiedział(a) na Chuck Yeager temat w Półmakiety
No powiem, że prawdziwy artysta z Ciebie Łukaszu. Ja takie elementy robię na swojej frezarce ale CNC, a wyrzeźbić takie "cuś" prawie ręcznie to szacun wielki. I jeszcze jedno, jak byś chciał sobie ułatwić życie z tą tokarką (bo też taką użytkuję) to spraw sobie taki imak do noży: https://www.ebay.pl/itm/Mini-Quick-Change-Tool-Post-Holder-Aluminum-Alloy-Holder-Lathe-Tool/162805814178?hash=item25e7fb93a2:g:qZYAAOSwBjdaM-Ht:rk:157:pf:0 Może już spotkałeś takie rozwiązanie, jak dla mnie jest bardzo wygodne (szybka zmiana narzędzia i raz wyregulowana wysokość), zdecydowanie poprawia wygodę i oszczędza czas. -
Adam w TME jak kolega Maciej wskazał można znaleźć złącza które mógłbyś wykorzystać i nie koniecznie tak drogie jak na stronie Hackera. Poniżej masz przykładową parę wtyk i gniazdo na przewód: https://www.tme.eu/pl/details/nppw-10/zlacza-sygnalowe-raster-250mm/ninigi/ https://www.tme.eu/pl/details/nppg-10/zlacza-sygnalowe-raster-250mm/ninigi/ Jest tam tych złączy naprawdę dużo, te które są w linku mają obciążalność na styk 2 A, a należą do grupy sygnałowych. Do każdego rodzaju złączy trzeba jeszcze sobie dobrać piny do zaciskania na przewód żeńskie i męskie.
-
Piper J3C konstrukcja z rurek
widar123 odpowiedział(a) na widar123 temat w Makiety F4C i Giganty F4CX
To prawda, też już myślałem o tym, ale z drugiej strony, to ja nie będę nim kręcił akrobacji, będzie latał jak na moje warunki "latacza" dostojnie i statecznie- 477 odpowiedzi
-
- piper
- kostrukcja spawana
-
(i 1 więcej)
Oznaczone tagami:
-
Piper J3C konstrukcja z rurek
widar123 odpowiedział(a) na widar123 temat w Makiety F4C i Giganty F4CX
Prace nad zbiornikiem dobiegły do końca, jest już zamocowany na swoim miejscu. Zamocowałem też serwo przepustnicy gazu i mniejsze serwo do napędu dźwigni przepustnicy w kabinie. Takie rozwiązanie było prostsze, bo na początku próbowałem sprzęgnąć to mechanicznie za pomocą układu dźwigni, ale za dużo kombinowania przy tym było. Ostatecznie więc dodałem mniejsze serwo, sprzężone w aparaturze co pozwoliło na swobodną regulację każdego z osobna. Tu wspomniane serwo napędu dźwigni przepustnicy w kabinie Osłona maski spasowana z wlewem paliwa i drobny opis żeby nie było wątpliwości do czego to jest I jeszcze krótki filmik jak to wszystko działa- 477 odpowiedzi
-
- 2
-
-
- piper
- kostrukcja spawana
-
(i 1 więcej)
Oznaczone tagami:
-
Piper J3C konstrukcja z rurek
widar123 odpowiedział(a) na widar123 temat w Makiety F4C i Giganty F4CX
Janusz - ten jest idealny, widać że to jest jakiś odlew, więc jest duża szansa na to, że to oryginał. Na nim będę się wzorował. Takie samoróbki druciano-blaszane też właśnie spotykałem i każda była inna.- 477 odpowiedzi
-
- piper
- kostrukcja spawana
-
(i 1 więcej)
Oznaczone tagami:
-
Piper J3C konstrukcja z rurek
widar123 odpowiedział(a) na widar123 temat w Makiety F4C i Giganty F4CX
No i o taki mi właśnie chodziło, gdzieś go już wcześniej widziałem, ale zdjęcie nie było zbyt wyraźne, więc można było się tylko domyślać, a tu jak na dłoni w super ujęciach. Dzięki i pozdrawiam- 477 odpowiedzi
-
- piper
- kostrukcja spawana
-
(i 1 więcej)
Oznaczone tagami:
-
Piper J3C konstrukcja z rurek
widar123 odpowiedział(a) na widar123 temat w Makiety F4C i Giganty F4CX
Otóż to, Piper by mi tego nie wybaczył , tylko po co ten Pan Irku, tutaj wszyscy jesteśmy jedną społecznością, więc mówmy sobie po imieniu, bo jakoś nie bardzo czuję się w takich tytułach- 477 odpowiedzi
-
- piper
- kostrukcja spawana
-
(i 1 więcej)
Oznaczone tagami:
-
Piper J3C konstrukcja z rurek
widar123 odpowiedział(a) na widar123 temat w Makiety F4C i Giganty F4CX
Jeszcze jedną rzecz poszukuję, chodzi o zaczep pod skrzydłem do mocowania górnej połówki drzwiczek kabiny. Znalazłem w necie bardziej szczegółowe zdjęcia, ale każde z nich prezentowało inne rozwiązanie i zgłupiałem, jak to było pierwotnie, bo pewnie te znalezione to radosna twórczość właścicieli Piperów. Jeśli miałby ktoś kilka fotek tego zaczepu, ale z jednego egzemplarza Pipera to bardzo by mi to pomogło w rozwiązaniu tego problemu. Z góry dzięki.- 477 odpowiedzi
-
- piper
- kostrukcja spawana
-
(i 1 więcej)
Oznaczone tagami:
-
Piper J3C konstrukcja z rurek
widar123 odpowiedział(a) na widar123 temat w Makiety F4C i Giganty F4CX
Z tym zbiornikiem to fakt, że trochę popłynąłem ;-) Jednak na rynku nie było gotowych zbiorników, które w miarę pasowały by do planowanego miejsca. Stąd decyzja o własnej konstrukcji, a skoro tak, to forma przypominająca oryginał. W całości może go nie będzie widać, ale od strony wnętrza kabiny trochę będzie widoczny, nawet po pokryciu kadłuba płótnem. Tak się zastanawiam, że skoro mam już formy do tłoczenia, można by się przymierzyć do małej produkcji takich zbiorników, tylko czy znajdą się jacyś chętni?- 477 odpowiedzi
-
- piper
- kostrukcja spawana
-
(i 1 więcej)
Oznaczone tagami:
-
Piper J3C konstrukcja z rurek
widar123 odpowiedział(a) na widar123 temat w Makiety F4C i Giganty F4CX
Do tego tematu podchodziłem jak pies do jeża, wykonywałem różne próby wytłaczania rowków wzmacniających w przedniej i tylnej ściance zbiornika, ale efekty były nie do zaakceptowania. Ostatecznie kolega podjął się wykonania matrycy i stempla do wytłoczenia gotowych ścianek. I tu wielkie dzięki dla kolegi Adama, który wykonał to tak, jak to sobie wymyśliłem na samym początku, ale brak dostępu do odpowiednich maszyn zweryfikował moje zamiary i próbowałem obejść na skróty. Fajnie że to się udało i konstrukcja zbiornika jest tym samym zbliżona do oryginału. I oto same narzędzia - matryca i stempel Przetłoczone ścianki zbiornika, wyszły za pierwszym razem, bez żadnych poprawek. Do przetłoczenia wystarczyło porządne imadło, więc obyło się bez prasy. Pierwsza ścianka już polutowana, ale tym razem normalną cyną. Pierwsze lutowanie niestety nie wyszło, bo próbowałem twardego lutowania srebrem. Jak się okazało miejscowe rozgrzanie tej blaszki do temp. topnika spowodowało pofalowanie, praktycznie nie odwracalne. Na szczęście zacząłem od lutowania prostego paska blachy będącego obwodem zbiornika i tym samym nie zniszczyłem wytłoczonych ścianek. I polutowany cały zbiornik wraz z wlewem paliwa i króćcami zasilania paliwa i odpowietrzeniem. Nie mogłem przepuścić sobie gadżetu w formie charakterystycznego dla Pipera wskaźnika paliwa, który jest w pełni funkcjonalny. Sam wskaźnik wraz z pływakiem wydrukowanym z PETG Całość zamknęła się w wadze 140 g, nie wiem czy to dużo, ale zważywszy że jest to metalowa konstrukcja to chyba nie jest źle ? Pozostało zamontować uchwyty do mocowania zbiornika, jeszcze kilka małych drobiazgów i będzie można myśleć o poszyciu.- 477 odpowiedzi
-
- 4
-
-
- piper
- kostrukcja spawana
-
(i 1 więcej)
Oznaczone tagami:
-
Piper J3C konstrukcja z rurek
widar123 odpowiedział(a) na widar123 temat w Makiety F4C i Giganty F4CX
Wreszcie dobrnąłem do końca z przednią owiewką kabiny. Jeszcze tylu szablonów jakie teraz wykonałem nie wycinałem. Dopasowanie tych krzywizn nie było takie proste jakby się wydawało, ale najważniejsze, że szablon ostateczny jest zapisany w kompie i w każdej chwili można wyciąć w razie W.. Druga rzecz jaka dostarczyła nie małego problemu, to pasek blachy ograniczający dolną część owiewki. Musiałem wydrukować sobie model kawałka kadłuba, żeby na nim modelować i przetłaczać wspomniany pasek. Ostatecznie tak to sobie wygląda: Wspomniany model (szablon do przetłoczenia) Jeszcze trochę nitowania No i doszły już spinki, do których namiar wskazał kolega "solainer" wydaje się że pasują jak ulał - jeszcze raz wielkie dzięki za linka. Muszę jeszcze poszukać tych samych na zapas, bo na stanie mieli tylko jeden komplet 10 szt. dokładnie tyle ile potrzeba na maskę. Można teraz zająć się, odkładanym na później, zbiornikiem i wskaźnikiem paliwa. To chyba ostatni element jaki brakuje mi, żeby zająć się wreszcie poszyciem.- 477 odpowiedzi
-
- piper
- kostrukcja spawana
-
(i 1 więcej)
Oznaczone tagami:
-
Piper J3C konstrukcja z rurek
widar123 odpowiedział(a) na widar123 temat w Makiety F4C i Giganty F4CX
Tak było, bo już zamówiłem. Mam nadzieję, że będą pasowały, szkoda że nie podają wymiarów tej spinki, tylko posługują się skalą modelu, nie wiele to mówi kupującemu, który nie ma styczności z tymi modelami. Dzięki za link, jak przyjdą dam znać.- 477 odpowiedzi
-
- piper
- kostrukcja spawana
-
(i 1 więcej)
Oznaczone tagami:
-
Piper J3C konstrukcja z rurek
widar123 odpowiedział(a) na widar123 temat w Makiety F4C i Giganty F4CX
A mógłbyś podać link do konkretnych spinek, bo byłem na stronie Scorpio i w podanej skali nie występują tam, chyba że są jakoś inaczej oznaczone.- 477 odpowiedzi
-
- piper
- kostrukcja spawana
-
(i 1 więcej)
Oznaczone tagami:
-
Piper J3C konstrukcja z rurek
widar123 odpowiedział(a) na widar123 temat w Makiety F4C i Giganty F4CX
Też się nad tym już zastanawiałem, ale jak do tej pory nic szczególnego nie wzbudziło mojego zainteresowania. Z drugiej strony może to i dobrze, bo już bym myślał o tym nowym i Piper miałby mniej czasu . Pozostał mi silnik po Cessnie 182, którą sprzedałem 2 lata temu, więc silniczek SAITO FG36 czeka w pudełeczku na nowy projekt. Jakby Ci przyszło Stefanie coś ciekawego w podpowiedzi "latadła" do tego silnika, to jestem jak najbardziej zainteresowany. Kiedyś bardzo mi się marzył jakiś model z silnikiem gwiazdowym (nie makietą tego silnika), ale że zwyczajnie takie silniki są poza moim zasięgiem finansowym, to pozostało to w sferze marzeń i nie sądzę żeby się to zmieniło. Tak więc ten nowy projekt musi się dostosować do tego co mam. Żeby nie było, że jestem przesadnym pedantem w porządkach, to sekret tkwi w nowo urządzonym pomieszczeniu, o którym pisałem wcześniej. Poprzednie pomieszczenie zagospodarowałem jako strefę mechaniczną i to tam w większości wykonuję najbardziej pylące i wytwarzające wióry wszelakiej maści prace. To pomieszczenie z ostatnich zdjęć, to głównie przeznaczone do montażu i fazy projektowej, więc zdecydowanie łatwiej utrzymać tam porządek, nie znany z większości pomieszczeń modelarskich Pewnie to ostatni wpis w tym roku, dlatego korzystając z okazji, życzę Wszystkim pomyślnego, owocnego w nowe projekty jak i pełnego przyjemności z oddawania się temu fantastycznemu hobby, Nowego Roku 2019.- 477 odpowiedzi
-
- 1
-
-
- piper
- kostrukcja spawana
-
(i 1 więcej)
Oznaczone tagami:
-
Piper J3C konstrukcja z rurek
widar123 odpowiedział(a) na widar123 temat w Makiety F4C i Giganty F4CX
Zrobiłem mały "upgrade" maski Pipera, parę wycięć oraz atrapę chłodnicy i tak to teraz się prezentuje- 477 odpowiedzi
-
- piper
- kostrukcja spawana
-
(i 1 więcej)
Oznaczone tagami:
-
Piper J3C konstrukcja z rurek
widar123 odpowiedział(a) na widar123 temat w Makiety F4C i Giganty F4CX
Na życzenie kolegi Matijus, a może także i innych, wrzuciłem fotki złożonego modelu na dotychczasowym etapie budowy- 477 odpowiedzi
-
- 5
-
-
- piper
- kostrukcja spawana
-
(i 1 więcej)
Oznaczone tagami:
-
Piper J3C konstrukcja z rurek
widar123 odpowiedział(a) na widar123 temat w Makiety F4C i Giganty F4CX
Jako że charakterystycznym elementem maski silnika Pipera są wloty powietrza, postanowiłem coś wyklepać. Niestety w moim wydaniu zastosowany silnik ma dość duże przesunięcie cylindrów, więc wloty prawy i lewy nie są symetryczne i tak aby mniej więcej równo zaczynały się od czoła maski, jeden od drugiego różnią się długością. To oczywiście wymusiło wykonanie każdego z osobna, bo inne krzywizny itp. Od przodu prezentują się tak samo, ale w rzutach bocznych widać już różnicę. Druga sprawa, to nie było do czego przykręcić osłony od strony mocowania pokrywy zaworów. Nie chciałem nawiercać żeberek cylindra (choć i tak bardzo niewiele miejsca tam nie było), po drugie wkręt pokrywy był w takim miejscu, że ni jak go wykorzystać. Ostatecznie wykorzystałem gniazda od wkrętów mocujących cylinder, gdzie udało mi się osadzić aluminiowe kołki z nagwintowanymi otworami. Dodałem wzmocnienia przynitowane do blach wlotów i przez nie przykręciłem dwoma wkrętami. Blachy wlotów wraz z wzmocnieniami mają wycięcie w kształcie fragmentu cylindra w szczelinie między żeberkami, co pozwoliło na wsunięcie blachy wlotu dość ciasno i wraz z wkrętami mocującymi utworzyło bardzo sztywną konstrukcję. Tak to się teraz ma Przy masce pozostało jeszcze parę otworów od przodu oraz chłodnica, ale to już chyba po Świętach. Pozdrawiam Wszystkich - Darek- 477 odpowiedzi
-
- 3
-
-
- piper
- kostrukcja spawana
-
(i 1 więcej)
Oznaczone tagami:
-
Piper J3C konstrukcja z rurek
widar123 odpowiedział(a) na widar123 temat w Makiety F4C i Giganty F4CX
Dzięki wszystkim za słowa uznania - staram się żeby to jakoś wyglądało . A co do tych spinek to niestety masakra jest, dzwoniłem do kilku sklepów i w żadnym z nich nie potrafili odpowiedzieć z jakiego drutu są wykonane i jakiej długości (każdy tłumaczy że są na magazynie, a oni odbierają telefon w biurze i nie mają jak zmierzyć) operują tylko skalą, która nie wiele mówi. Czekam jeszcze na telefon z 2 firm, które postarają się zmierzyć i podać zbliżone wymiary.- 477 odpowiedzi
-
- piper
- kostrukcja spawana
-
(i 1 więcej)
Oznaczone tagami:
-
Piper J3C konstrukcja z rurek
widar123 odpowiedział(a) na widar123 temat w Makiety F4C i Giganty F4CX
Maska skończona, zostały drobne szczegóły, którymi zajmę się niebawem. Każdy etap prac to kolejne wyzwania, z jakimi do tej pory nie miałem okazji się zmagać, ale po kolei. Na początek musiałem zrobić formę do przedniej części maski. Problem o którym pisałem wcześniej, czyli pozostającymi smugami na formie po zastosowaniu Frkote 770 NC okazał się mało istotny, jako że wyjściowy element i tak będzie malowany, więc nie miało to znaczenia. Oceniając ten środek, muszę powiedzieć, że jest rewelacyjny. Po zastosowaniu 4 warstw nałożonych szmatką, element z formy wyszedł bez zbędnego siłowania, dotyczy to zarówno formy negatywowej jak i właściwej maski. Skusiłem się również na metodę próżniową przy laminowaniu z dodatkowymi materiałami czyli tkaniną do delaminażu, folią perforowaną i matą odsączającą nadmiar żywicy. Efekt po takim laminowaniu zdecydowanie lepszy niż bez pompy próżniowej. Pamiętam jak kiedyś po takim tradycyjnym laminowaniu męczyłem się z uzupełnianiem ubytków spowodowanych uwięzionymi pęcherzykami powietrza, tutaj nic takiego nie było, równa warstwa, w każdym miejscu równo przesączona żywicą, naprawdę polecam jeśli jeszcze ktoś nie próbował. Tutaj tak się to utwardzało I po wyjęciu z worka i rozdzieleniu od kopyta Następnym krokiem było wylaminowanie przedniej części maski w dwóch etapach. Każda z dwóch połówek musiała być laminowana osobno, gdyż potrzeba było dodanie zakładki 6 mm tak aby można umieścić uchwyty mocujące do nachodzących na siebie połówek. Wklejone elementy z blaszki alu do przynitowania górnej o dolnej części maski I pierwsza przymiarka wyciętego szablonu z folii PCV 0,4 mm. Wykonałem takich szablonów ok 4, mimo że wstępnie projektowane były na komputerze, to jednak pewne drobne niedokładności wynikające z wykonanych już wcześniej mocowań maski nieco zweryfikowały miejsca otworów mocujących oraz linii brzegowej łączenia z przednią częścią. I jeszcze mały dodatek, przyrządy do usprawnienia nitowania wzmocnień otworów mocujących I na koniec gotowa maska z blachy alu PA6 0,4 mm, którą wyciąłem na mojej frezarce CNC, po złożeniu w całość wszystko idealnie pasuje ? Co ciekawe mimo, że osłona maski silnika nie jest w żadnym miejscu przykręcana, trzyma się tylko na tych sworzniach (zgodnie z oryginałem), całość jest bardzo sztywna jakby była wykonana z monolitu, nie ma tendencji do kołysania się na boki czy góra-dół. Mam jeszcze zadanie dla poszukiwaczy, ja jak do tej pory nie znalazłem takich spinek jak te poniżej, które pasowały by do mojego modelu. Potrzebuję spinki o całkowitej długości 8-10 mm i wykonane z drutu o śr 1 mm. Jak widać na zdjęciach w chwili obecnej spinki zastępują haczyki z drutu - no nie wygląda to najlepiej ?- 477 odpowiedzi
-
- 3
-
-
- piper
- kostrukcja spawana
-
(i 1 więcej)
Oznaczone tagami:
-
Piper J3C konstrukcja z rurek
widar123 odpowiedział(a) na widar123 temat w Makiety F4C i Giganty F4CX
Dzięki bardzo właśnie takich doświadczeń potrzebowałem, co potwierdziło moje obawy przy polerowaniu. Na wszelki wypadek nałożę jeszcze ze dwie warstwy wosku.- 477 odpowiedzi
-
- piper
- kostrukcja spawana
-
(i 1 więcej)
Oznaczone tagami:
-
Piper J3C konstrukcja z rurek
widar123 odpowiedział(a) na widar123 temat w Makiety F4C i Giganty F4CX
Wszystko się zgadza co do wosku, tylko ten preparat to nie jest wosk, jest to płynna bezbarwna substancja o konsystencji wody. Natryskując pistoletem, bardzo szybko odparowuje rozpuszczalnik i po 10 min jest praktycznie suche i utwardzone. Z woskiem już miałem do czynienia i faktycznie wystarczyło delikatnie wygłaskać powierzchnię żeby była lustrzana, tutaj niestety trzeba użyć większego nacisku, aby otrzymać ten sam efekt, stąd to moje pytanie.- 477 odpowiedzi
-
- piper
- kostrukcja spawana
-
(i 1 więcej)
Oznaczone tagami:
-
Piper J3C konstrukcja z rurek
widar123 odpowiedział(a) na widar123 temat w Makiety F4C i Giganty F4CX
Dzięki za odpowiedź, mam rozumieć, że tym polerowaniem szmatką nie jestem w stanie zetrzeć tej warstwy rozdzielacza?- 477 odpowiedzi
-
- piper
- kostrukcja spawana
-
(i 1 więcej)
Oznaczone tagami:
-
Piper J3C konstrukcja z rurek
widar123 odpowiedział(a) na widar123 temat w Makiety F4C i Giganty F4CX
Koledzy czy ktoś używał takiego specyfiku jako rozdzielacz do form: Pytałem dystrybutora o sposób aplikacji i w zaleceniach otrzymałem odpowiedź, że nakładać natryskowo 4-5 warstw i po każdej aplikacji w odstępach 10 min prze polerować każdą powierzchnię suchą szmatką z mikrofibry. Pan z którym rozmawiałem zapewniał, że takie polerowanie nie uszkadza nałożonej warstwy, ale ja mam wrażenie, że aby usunąć matową powierzchnię po wysuszeniu ścieram to co nałożyłem. Nie wiem czy mi się tak wydaje, czy mam uzasadnione obawy, że forma przyklei mi się do kopyta. Chciałbym mieć pewność że takie polerowanie nie uszkadza powierzchni i mogę śmiało laminować.- 477 odpowiedzi
-
- piper
- kostrukcja spawana
-
(i 1 więcej)
Oznaczone tagami:
-
Piper J3C konstrukcja z rurek
widar123 odpowiedział(a) na widar123 temat w Makiety F4C i Giganty F4CX
Długą ciszę trzeba wreszcie przerwać ? Dość długo trwały przygotowania do stworzenia elementów maski silnika. Nie chciałem tego robić tradycyjnie, bo wydaje mi się że zajęłoby to więcej czasu, więc zdecydowałem się na zaprojektowania sobie modelu maski w CAD. I tu początkowo pojawiły się problemy w związku z koniecznością nauczenia się operowania powierzchniami, myślę że wtajemniczeni wiedzą o co chodzi ? Tym sposobem znowu coś więcej wiem i coś tam umiem. Najważniejsze, że udało się naskrobać i model maski w końcu powstał. Na początek jednak musiałem dokleić uchwyty do tej że maski. Miałem kilka koncepcji, żeby uchwyty były symetryczne no i najważniejsze aby polutowana już konstrukcja zawieszenia silnika się nie rozpadła w trakcie lutowania. Ostatecznie powstały szablony z alu, które skutecznie odprowadzały ciepło od polutowanych elementów i można było miejscowo rozgrzać i dolutować wąsy. Tak to sobie teraz wygląda Kolejnym krokiem było wydrukowanie maski podzielonej na 3 elementy. Ponieważ przód będzie zrobiony z laminatu (klepanie tego z blachy alu było jak dla mnie zbyt mało realne) więc ta część została przygotowana do zrobienia formy, pozostałe elementy to tylko kopyta do uformowania góry i dołu maski z blachy alu. To tyle w skrócie, myślę że teraz już pójdzie do przodu nieco szybciej ?- 477 odpowiedzi
-
- 1
-
-
- piper
- kostrukcja spawana
-
(i 1 więcej)
Oznaczone tagami:
- Poprzednia
- 1
- 2
- 3
- 4
- 5
- 6
- 7
- Dalej
-
Strona 2 z 10