
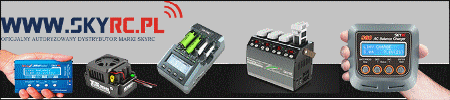
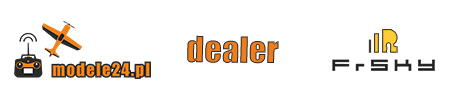
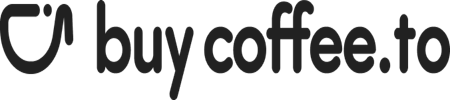
-
Postów
786 -
Rejestracja
-
Ostatnia wizyta
-
Wygrane w rankingu
50
Treść opublikowana przez f2cmariusz
-
to już teraz całkowicie na poważnie. Zamiana silnika żarowego na samozapłon to w latach mojej młodości typowa procedura. Po co? Bo przepracowany samozapłon który traci kompresje jest w przypadku silnika żarowego pełnowartościowym silnikiem. Ja w Pałacu Młodzieży wielokrotnie przerabiałem sobie jak i kolegom używane silniki samozapłonowe na żarowe . I na odwrót. Nowy silnik żarowy MVVS czy Super Tigre przerabiałem do wyścigu. Miałem zadanie bardzo ułatwione bo były wzory silników zatem odpadały problemy doboru stopnia sprężania bo po prostu mierzyłem orginały. A odpowiedni stopień sprężania to podstawa pracy nowego silnika. Po prostu warto znać GMP górny zwrotny martwy punkt tłoka i stosownie wykonać przeciwtłok czy głowicę ze świecą żarową.
-
Replika Polskiego silniczka SiM 2b - ambitny projekt
f2cmariusz odpowiedział(a) na Paweł Prauss temat w 2-takty
kokila do odlania karteru repliki silnika SiM 2b złożona na kołkach kartowanych obsadzonych w tulejach toczonych z materiału serii Q-te ( Dla mnie od roku całkowita nowość. Ważne że idę kupuję ile mi potrzeba. Płacę i mam gotowy materiał o twardości 32-34 HRc) pozostało jeszcze wykonać podebrania aby czerwoną kokilę można było pokazanymi łyżkami rozebrać co by można było później wybić detal odlany z kokili. To już jutro. same tulejki to po prostu stanie przy tokarce SV18 i toczenie. Po mniej więcej 40 minut na jeden detal na gotowo wykonany z dokładnością do dwóch setek. Reszta przytarta papierem ściernym na obrotach do takiego wymiaru co by były widoczne wyraźne ślady powstałe podczas wybijania: na ostatniej tulejce widać że za ciasno było bo przy wyciskaniu złapało tulejkę i powstał delikatny zadzior. Co zostało i w otworze jak i na tulejce usunięte. otwarta kokila z osadzonymi kołkami pozycjonującymi. Robiłem sam tylko dlatego że kupne i tak bym musiał przerabiać czyli skracać bo za długa byłaby część prowadząca. Te tulejki to na pewno oddam do azotowania co by podnieść twardość powierzchni a to na pewno zapobiegnie możliwości zatarcia gdyby na przykład próbować składać kokilę gdy jedna strona jest gorąca a druga chłodna. a tu już wciśnięte twarde kołki w tulejki wcześniej już pasowane do otworów. Oczywiście po wciśnięciu kołków ponownie muszę pasować tulejki co by się nie zatarły podczas wciskania do otworów w kokili. na koniec. Mam praski ale i imadło maszynowe a to zapewnia przyłożenia sił równolegle do kierunku wciskania. -
Replika Polskiego silniczka SiM 2b - ambitny projekt
f2cmariusz odpowiedział(a) na Paweł Prauss temat w 2-takty
a tu dalej nie mam możliwości publikacji kolejnych fotografii z postępu prac. A weekend minął i przerobionej pracy na konwencjonalnych maszynach przybyło. -
szkoda że nie wiedziałem bo może i po Mistrzostwo Świata byśmy sięgnęli...
-
Replika Polskiego silniczka SiM 2b - ambitny projekt
f2cmariusz odpowiedział(a) na Paweł Prauss temat w 2-takty
zapomniałem wstawić fotografię z samego procesu cięcia. Tu widać ostatni moment przed odpadnięciem odpadu wypychacza fi6 mm. Używam do tego małej mocy szlifierki z racji że nie da się docisnąć za dużo bo silniczek zwalnia. Ma to tą zaletę że nie przegrzewa (odpuszcza) ucinanego hartowanego wypychacza. a dzisiaj zacząłem a pewnie w weekend skończę kołki łączące obydwie połówki kokili. Przy czym toczę osiem tulejek. W cztery wciskam fi 18h6 odcięte kiedyś kołki. Można oczywiście kupić gotowe w paru fabrykach produkujących normalki do form ale... Kołki przy otwieraniu ręcznym muszą być z natury bardzo krótkie w części cylindrycznej (1/4 - 1/2 średnicy) a w części stożkowej czyli naprowadzającej pewnie zrobię długość stożka równa średnicy. Dlatego te kupne twarde musiałbym i tak przerabiać. Stąd stoję i w kupionym wałku Q-te toczę... -
Replika Polskiego silniczka SiM 2b - ambitny projekt
f2cmariusz odpowiedział(a) na Paweł Prauss temat w 2-takty
w tym tempie to jeszcze jak widzę jeszcze to potrwa. Ważne że codziennie po parę godzin idzie do przodu. te powstające gwinty będą w odlewni wykorzystane do wybijania wypraski aluminiowej właśnie młotkiem ? w terminie późniejszym będzie to na pewno pokazane. same wypychacze co by się nie myliło mimo tych samych wymiarów nominalnych muszą być indywidualnie suwliwie dopasowane do każdego otworu z osobna. Stąd też numeracja. a same wypychacze wszystkie skrócone na razie do wysokości płaszczyzny podziału. na prostym przyrządzie. Który się sprawdza od lat gdzie hartowany drut czy wypychacz bez problemu ucinam na ustawiony wcześniej wymiar. co jakiś czas litrowy pojemnik znowu jest pełny pełen fajnych odpadów... Nie wywalam tylko rozdaje.? -
Replika Polskiego silniczka SiM 2b - ambitny projekt
f2cmariusz odpowiedział(a) na Paweł Prauss temat w 2-takty
kolejne parę godzin zaowocowało złożeniem w całość. Udało się bez problemu. Ciasno chodzi i jeden i drugi zespół wypychaczy. Tylko dlatego że przez całą długość płyty kokilowej o grubości 36 mm są otwory niewyluzowane. Jutro mam nadzieję na dalsze prace. Czyli wyluzowanie dodanie brakujących jeszcze bolców do pchania wypychaczy ( Młotkiem ?). Oraz stosownego poskracania wypychaczy... -
Replika Polskiego silniczka SiM 2b - ambitny projekt
f2cmariusz odpowiedział(a) na Paweł Prauss temat w 2-takty
wolny weekend a właściwie popołudnie w piątek zaowocowało paroma godzinami pracy przy kokili. Wszystkie wypychacze suwliwie przesuwają się w samej kokili a że otwory w płytkach wypychaczy zrobione to pewnie pod koniec tego weekendu prace nad kokilą będą ukończone. -
Replika Polskiego silniczka SiM 2b - ambitny projekt
f2cmariusz odpowiedział(a) na Paweł Prauss temat w 2-takty
Gwoli przypomnienia dla niecierpliwych Kolegów. Projektantem i organizatorem produkcji silników SiM był pan Michał Oldachowski. A produkcja była prywatnym przedsięwzięciem w państwowych przedsiębiorstwach w ramach gospodarki socjalistycznej... 20200713 hd.mp4 -
Replika Polskiego silniczka SiM 2b - ambitny projekt
f2cmariusz odpowiedział(a) na Paweł Prauss temat w 2-takty
Praca idzie do przodu tylko dlatego że same otwory pod wypychacze na Chińskiej frezarce powstają. Nie wiercą się a frezują na głębokość przynajmniej dwóch średnic co by bez problemu konwencjonalnie dowiercić stosownym wiertłem pod odpowiedni rozwiertak. W tym tempie to dopiero w przyszłym tygodniu kokila będzie gotowa do pierwszego wlania stopu aluminium... Niestety lipiec czyli okres urlopowy... na tej fotografii widać obsadzone wypychacze w płytkach wypychaczy ze stosownym luzem. Od jutra druga strona mam nadzieję że szybciej mi pójdzie.? -
Replika Polskiego silniczka SiM 2b - ambitny projekt
f2cmariusz odpowiedział(a) na Paweł Prauss temat w 2-takty
i sobie frezarka zakupiona w Chinach poradziła z wykonaniem otworów w przedniej płytce wypychaczy.? A ja miałem czas na inne wyzwania akurat dotyczącymi modelarstwa ale nie będącym tematem tego wątka. Otwory nie przelotowe co by mi nie uszkodziły świeżo regenerowanych podkładek !!! A w tyle widać włożone frezy fi 4 i fi 6 mm co by sprawdzić wielkość luzów otworów w stosunku do wypychaczy zamocowanych w tym miejscu. Jest OK. ta płytka obrabiana teraz to ta górna czerwona. zdjęcie wykonane w trakcie pracy a właściwie kontroli czy wszystko głównie z wodą w porządku. Po prostu jak się źle przestawi to rozbryzg o wirujący ER11 szybko uwalnia zbiornik a ja mam co sprzątać wokół maszyny. To niestety dalej nie dopracowałem do końca. blisko umiejscowione dwa wypychacze fi6 wymusiły taką budowę płytki wypychaczy co w rzeczywistości przy dobrym materiale obrabianym 1.2311 spowodowało jak widać na poprzedniej fotografii cienkiej blaszki między po kolei obrabianymi otworami. Nie problem usunąć biaksem... a sama ścieżka narzędzia wygląda tak napisana w programie Fusion360 który każdemu polecam od dłuższego czasu. No niestety tylko umiem wersję CAM bo dalej rysuję w Rhino3D z racji że tam umiem... a tutaj nie ma mnie kto nauczyć i przede wszystkim jak na razie nie mam takiej potrzeby. -
Replika Polskiego silniczka SiM 2b - ambitny projekt
f2cmariusz odpowiedział(a) na Paweł Prauss temat w 2-takty
parę godzin i powstały zagłębienia pod otwory o około dwie dychy mniejsze co by na normalnej wiertarce dowiercić a następnie z drugiej strony wykończyć rozwiertakiem otwory pod wypychacze. a w części gaźnikowej tak to wygląda: pozostało zatem na normalnej konwencjonalnej tokarce z pręta QT wykonać słupy i tulejki. Mam wzornik gotowy wymiaru fi24 wchodzącego w otwory suwliwie. Zatem wystarczy o parę setek wykonać większy wymiar i wszystko samo będzie się trzymać. Jak widać sama płyta na kokile to zamówiona w Bytowie stal gatunek 1.2311 ulepszony cieplnie fabrycznie . O wymiarach 196x196x76 mm. To najtańsza wersja obrobionego materiału. Mnie wtedy pozostało rozciąć na pół wymiar 76 mm ale wcześniej wykonałem otwory pod słupy i kołki. -
Replika Polskiego silniczka SiM 2b - ambitny projekt
f2cmariusz odpowiedział(a) na Paweł Prauss temat w 2-takty
miałem wykonać otwory pod wypychacze w kokili jak i w płytkach wypychaczy po staremu czyli punktując i dalej wiercąc stosownymi wiertłami a na końcu użyć rozwiertaków fi odpowiednie z tolerancją H7. ale ponieważ wszystko jest narysowane i wykonane metodami CAM/CAD to i nie nastręczyło kłopotu odpowiednim frezem wjechać w narysowane otwory i wykonać odpowiednie otwory pomniejszone offsetem o 0,07 mm na stronę co by później rozwiertakiem z drugiej strony prze kalibrować rozwiertakiem odpowiedniej wielkości pod wypychacz który już mam. ileś drobnych programików dla dwóch narzędzi jakim jest frez 2mm robiący otwory pod wypychacze fi3 i fi4 oraz frez 4mm pod wypychacze fi 6 mm umieszczone głównie w kanałach dolotowych jak i cofaczach. zbliżenie samej części silnikowej. a tu niebieska ścieżka narzędzia czyli wykonanie otworu fi 4 frezem palcowym 2 mm w przyszłym wstępnym otworze pod gaźnik gdzie po roztoczeniu powstanie gwint M8x1 do wkręcania gaźnika. Ja to pokazuje bo to już dzisiaj zaczęło się samo robić a jutro będzie kontynuowane. Będzie szło co prawda parę godzin ale samo się wykona. Co bardzo cenię mając takie możliwości wykorzystuję je w dużym stopniu. -
Replika Polskiego silniczka SiM 2b - ambitny projekt
f2cmariusz odpowiedział(a) na Paweł Prauss temat w 2-takty
film filmem ale zdjęcia jak usłyszałem także muszą być: tylko cofacze (tu na niebiesko zaznaczone) są prawidłowej długości. Reszta (czerwonych) będzie wymagała skrócenia do wymaganej długości. Wszystkie będą na płasko skrócone tak że w miejscach niektórych będą nadlewki ale są to powierzchnie obrabiane więc nie ma to znaczenia bo i tak zniknie na przykład przy nacinaniu gwintu. wczoraj skręciłem tak zwaną skrzynkę wypychaczy. Przez co sama kokila podczas pracy w odlewni na stole żeliwnym bez problemu będzie się przesuwać podczas składania i otwierania kokili. sama idea zapięcia dwóch połówek kokili jest stara jak świat i ponownie zastosowana ze starszych moich prac: modyfikacji uległa tylko długość zaczepu a sama geometria zapinania i zaciągania (młotkiem jak widać) jest od dawna taka sama. Dlatego teraz zastosowałem od razu stal ulepszoną cieplnie kupioną dosłownie w sklepie obok. ( Jest hurtownia stali Bodex gdzie telefonicznie zamawiam rano a po południu albo następnego dnia rano po drodze odbieram.) gatunek stali w postaci blach grubych czy prętów do kupienia w dużym asortymencie. A jak przy gatunku stali jest dopisane QT to już wiem że sama obróbka będzie wolniejsza. w tym konkretnym przypadku blacha miała grubość 15,13 do 15,2 a ja zeta ustawiłem na 14,9mm. Ta blacha została postawiona na podkładce i zostało parę dych materiału. ale po drugiej stronie dokładnie widać jakie siły powstają podczas skrawania skoro pozostawiony naddatek materiału się odbarwił !!! W drugiej sztuce częściej wymieniałem freza? -
Replika Polskiego silniczka SiM 2b - ambitny projekt
f2cmariusz odpowiedział(a) na Paweł Prauss temat w 2-takty
Dodałem kolejny film z racji że dużo łatwiej i szybciej jestem w stanie przekazać postęp prac w zakresie budowy Repliki silnika SiM 2b. Tak jak widać fizycznie postają skrzynki wypychaczy. I z jednej i z drugiej strony kokili. Co by delikatnie uderzając w bolce połączone z płytkami wypychaczy( jeszcze nie dorysowane) usunąć wlewek z kokili. -
Replika Polskiego silniczka SiM 2b - ambitny projekt
f2cmariusz odpowiedział(a) na Paweł Prauss temat w 2-takty
Wizyta u odlewnika zakończyla rozważania na temat sposobu dokończenia kokili do odlewania karteru Repliki SiM 2b. Wiele nie pokażę jeśli chodzi o rysunki bo po prostu nie są skończone z racji braku czasu. Narysowałem tylko tyle aby móc zamówić materiały na skrzynki wypychaczy plus zaczepy spinające gorącą formę podczas odlewania. Zaczepy się zrobiły na mojej frezarce . Wcinałem widiowym frezem palcowym fi 6 mm w stali 1.2311 ulepszonej cieplnie o dodatkowym oznaczeniu Q te. Czy jakoś tak. Sprawdzę to na fakturze. To od niedawna mogę kupić w pobliskim sklepie ze stalami. Mam na myśli ulepszoną stal do 32-34 HRc. Do tej pory zawoziłem do obróbki cieplnej zakupiony kawałek uciętej na wymiar stali. Materiał na skrzynkę wypychaczy także mam i jutro dalsza obróbka plus wiercenie otworów pod wypychacze. Rysunki będą dokończone i opublikowane. zaczepy do kokili 1.mp4 -
Replika Polskiego silniczka SiM 2b - ambitny projekt
f2cmariusz odpowiedział(a) na Paweł Prauss temat w 2-takty
Drogi Janku ta część silnika jest zarezerwowana na logo projektu. Logo projektu już powstało i było publikowane. Prace nad budową repliki silnika trwają. Aktualnie ze wstępnie gotową kokilą wybieram się do odlewnika w celu ustalenia dalszych szczegółów co do mocowania czy sposobu podgrzania samej kokili. Mam nadzeję załatwić to dzisiaj. 2020 June.mp4 -
Replika Polskiego silniczka SiM 2b - ambitny projekt
f2cmariusz odpowiedział(a) na Paweł Prauss temat w 2-takty
trochę to nudne podglądać jak się frezuje bo w rzeczywistości chłodziwo całkowicie zakrywa przestrzeń obrabianą. Dodam tylko że tak podawane chłodziwo zapewnia długotrwałą pracę widiowego freza skrawającego stal 123.11 obrobioną cieplnie do twardości 32 HRc. MJHQ3143.MOV -
Replika Polskiego silniczka SiM 2b - ambitny projekt
f2cmariusz odpowiedział(a) na Paweł Prauss temat w 2-takty
jedna strona kokili została skończona. Pozostało ją tylko uzbroić w trzy wstawki. Rysunek na dole. Wstawki koloru czerwonego. ostatnim elementem frezowanym w tej części kokili było odpowietrzenie części gaźnika. Tam powstanie iglakiem obniżenie paro setkowe. Na tej szerokości pozostawionego materiału 0,15 mm. Stosownie jak zachowa się lany materiał będę być może korygował także wymiar 0,30 mm do otworu który jest podłączony już do atmosfery. tak wygląda rysunek do operacji wykonania zagłębienia do odpowietrzenia formy. a to rzeczywisty wygląd fragmentu kokili do odlania karteru i gaźnika silnika SiM 2b -
Replika Polskiego silniczka SiM 2b - ambitny projekt
f2cmariusz odpowiedział(a) na Paweł Prauss temat w 2-takty
jestem miło zaskoczony ilością odsłon tematu w którym tak naprawdę nic się dzieje od wielu miesięcy. To zobowiązuje. Do... dokończenia budowy repliki. Pierwszy weekend w całości poświęcony dalszej pracy. W pierwszej kolejności, tak jak Paweł mi tłumaczy, dokończenie kokili co by uzyskać odlewy karterów. przybyły otwory na wstawkę pod konsolki ( na rysunku 3D kolor czerwony) oraz na wstawkę ulżeniową w komorze korbowej podczas odlewu. te wstawki pod konsolki zapewnią w tej części odlewu prostopadłość spodu konsolek do osi cylindra czy jak kto woli równoległość spodu konsolek do osi wału korbowego. Dlaczego taka zmiana? Poprawiam grubość konsolek bo w orginale jest 3.06 mm albo 3.22 i prostopadłość konsolek ( była lekka zbieżność) i u mnie i w orginale. po tej stronie na samym karterze będzie umieszczony napis: REPLIKA SiM 2b następny temat: co do pokryć chemicznych. Dawno temu pokrywałem w zakładzie na terenie Wólki Mlądzkiej na kolor złoty. Dotykając tym złotym wyrobem z niebieskim czy czerwonym złoty zostaje nieruszony a niebieski czy czerwony zdrapuje. Zatem dalej szukam podwykonawcy elektrolitycznej obróbki powierzchniowej aluminium. samo logo projektu przy współpracy zaprzyjaźnionego studia graficznego powstało. To wykonał promień lasera w ciągu paru sekund. na podstawie projektu wykonanego przeze mnie: to zbiór: 1553 curves, 801 surfaces, ? -
Replika Polskiego silniczka SiM 2b - ambitny projekt
f2cmariusz odpowiedział(a) na Paweł Prauss temat w 2-takty
temat loga "ambitnego" projektu jeśli chodzi o wersję czarno-białą coraz bardziej się krystalizuje. Gdzie powielanie na typowych gadżetach reklamowych w jednym kolorze nie będzie stanowiło problemu. ten projekt oczywiście w moim wykonaniu powstał w programie graficznym Rhinoceros zamieszczam jeden screenshot gdzie na trzech perspektywach widać co i jak co by na Set View "Front" było widać płaski efekt końcowy. Co do grafiki kolorowej to tylko kwestia w Rhino 3D przypisania poszczególnym elementom Repliki Silnika SiM 2b: materiału, tekstury, itp, itd i fotorealistyczna wizualizacja będzie gotowa?. co do kokili to będą zrobione jeszcze poprawki głównie chodzi o konsolki które wykonałem jak w oryginale ze zbieżnościami odlewniczymi. Muszę to pogrubić co by po zrobieniu płaszczyzny konsolka zachowała proporcje wymiarowe. Pokaże na zdjęciach i rysunkach 3D zmiany... -
Replika Polskiego silniczka SiM 2b - ambitny projekt
f2cmariusz odpowiedział(a) na Paweł Prauss temat w 2-takty
jak nie powstanie to Tobie Drogi Andrzeju pozostanie przyniesienie kwiatów na mój grób.?. Innej możliwości nie przewiduję. A co do biegania na "barana" to sektory są wyznaczone na promieniu 19,6 metra co po obwodzie daje zdecydowanie więcej niż 100 metrów. Dla mnie wystarczy że razem uruchomimy i wypuścimy model z silnikiem SiM 2b. A później schowamy się za siatką bezpieczeństwa. -
Replika Polskiego silniczka SiM 2b - ambitny projekt
f2cmariusz odpowiedział(a) na Paweł Prauss temat w 2-takty
silnik o oznaczeniu "1" Paweł sobie zarezerwował dla specjalnego swojego mentora. Na pewno pamiętam o Koledze Andrzeju z Wrocławia.? co do dalszej relacji z budowy silnika? Zaprzestałem bo... i tu można by długo tworzyć spiskowe teorie na dowolne tematy jak w poprzednich postach kolegi potworzyli a dali moderatorowi wątku pole do popisu. A przyczyna jest prozaiczna gdzie biznes zwyciężył chwilowo nad hobby. Czyli dostałem konkretne zlecenia na rysowanie i wykonanie nowych, dalszych od poprawienia modeli śmigieł wyścigowych. Testowanych w zeszłym roku a mając ich cyfrowy model zrobiony w zeszłym roku nie problem porobić korekcje w kierunku odpowiednim...?. Proszę o cierpliwość bo będąc przy zdrowiu temat budowy replik silnika SiM 2b będzie dokończony -
Replika Polskiego silniczka SiM 2b - ambitny projekt
f2cmariusz odpowiedział(a) na Paweł Prauss temat w 2-takty
tak przykładowo dla porównania. Napisy kiedyś i dzisiaj. Na karterze czy poszczególnych elementach silnika. Duże pole do popisu. Ważne aby za dużo nie naćkać. Ale z drugiej strony od czego jest lupa albo okulary o zmiennej ogniskowej czyli soczewki okularowe progresywne, z tak zwaną płynną ogniskową. Idealne dla mnie po 60 roku życia gdzie wymagana jest korekcja wzroku do jednego metra jak i na bardzo bliskie odległości. W dobie smart-fonów... czy odczytania co będzie napisane na poszczególnych elementach repliki silnika SiM 2b. Przykłady z Pawła kolekcji: i współczesne możliwości, wykonane wcześniej na wolnej przestrzeni z tyłu tarczy oporowej śmigła: -
Replika Polskiego silniczka SiM 2b - ambitny projekt
f2cmariusz odpowiedział(a) na Paweł Prauss temat w 2-takty
stacje paliw koncernu "British Petroleum" mijam codziennie dwa razy. I dokładnie widzę że skrót literowy występuje zawsze razem z charakterystycznym znakiem graficznym. Podobnie będzie i u nas. Czyli zawsze skrót od nazwisk autorów projektu będzie występował razem z resztą znaku graficznego. Myślę zatem że nie będzie pomyłek. Jestem nawet pewien. ?