
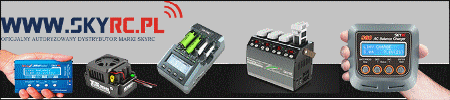
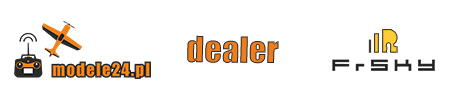
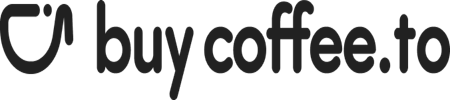
-
Postów
786 -
Rejestracja
-
Ostatnia wizyta
-
Wygrane w rankingu
50
Treść opublikowana przez f2cmariusz
-
Replika Polskiego silniczka SiM 2b - ambitny projekt
f2cmariusz odpowiedział(a) na Paweł Prauss temat w 2-takty
ja na pewno wiem że od wielu lat toczę i frezuję. I z racji że sam kupuję narzędzia. Sam dobieram parametry i zawsze wydaje mi się po bezpiecznej stronie. Ale przy jakim zagłębieniu (przybraniu) z jaką prędkością (mmm/min) i na jakich obrotach powinienem pracować aby było coś tam to tego niestety nie wiem. Bo także wielką niewiadomą są frezy nowe ale kupowane na bankgood.com czu alliexpress.com. Niby do 45 HRC ale wcześniej zanim zacząłem to frez już był tępy. Ten dostawca od którego teraz kupuję frezy spełnia moje oczekiwania jeśli chodzi o trwałość narzędzia przez już ponad 14 godzin pracy. Łysinkę widziałem i pewnie dopiero jutro podejmę decyzję czy ten czy nowy pójdzie do dalszej obróbki wykańczającej. Mając te dylematy na iPhona X sciągnąłem sobie firmy SANDVIK Kalkulator parametrów frezarskich. Cytuję:" niestety nie potrafiłem bez szkolenia prawidłowo posłużyć się tym kalkulatorem parametrów i puściłem jak uważałem za stosowne. I naprawdę nie wiem czy można by było jeszcze szybciej mając na uwadze że frez miał do wykonania konsolki na głębokość 12,95 mm. A sam osobiście frez o długości ostrza 8 mm przerobiłem na ponad 13,5 mm. Tak więc dziękuję za konkretne uwagi. Ponieważ moja firma kupuje dużo frezów w WNT ( https://www.wnt.com/pl/narzedzia/frezowanie.html ) poproszę aby pojawił się przedstawiciel mający trochę pojęcia o kalkulatorze parametrów frezarskich. Szkolenie i będę się bez problemu dzielił wiedzą między teorią a praktyką. i najważniejsze było frezowanie bo powstały wióry które podczas wycierania formy i częściowo stołu frezarki powłaziły mi igiełki w ręce co w tym momencie pisania czuję. Nie jest to nic nowego dla mnie. -
wszystko się zgadza niemniej o zastosowanym rodzaju napędu decyduje wiele czynników w danej kategorii. Przykład to ostatnio stosowane coraz częściej przeciwbieżne napędy w kategoriach takich jak F2B. Model w figurach akrobacyjnych zachowuje wyjątkowo równą prędkość niezależnie czy leci pionowo w górę czy w dół. Odpowiadają za to dwa przeciwsobne śmigła i regulatory oczywiście.
-
Replika Polskiego silniczka SiM 2b - ambitny projekt
f2cmariusz odpowiedział(a) na Paweł Prauss temat w 2-takty
Do północy nie było. Kolejny etap frezowania kokili za mną. Tu mimo że fajnie wyszło to jeszcze wgłąb materiału trzeba wjechać 0,14 mm. I widzę że jak falownik był ustawiony 160 z zakresu do 400 to zdecydowanie ładniejsza powierzchnia wyszła przy posuwie ponad 320 mm/ minutę. -
Selfie tylko tyle że ze statywu i jeszcze ciekawostka z 2016 roku w modelach akrobacyjnych F2B jedna łopata także była próbowana na zawodach we Francji
-
Replika Polskiego silniczka SiM 2b - ambitny projekt
f2cmariusz odpowiedział(a) na Paweł Prauss temat w 2-takty
i zamiast iść do domu wypada poczekać aż skończy przed północą. Całe szczęście mam co robić coraz bardziej śmiałe parametry wpisuję. To obróbka wykańczająca i według obliczeń po zgrubnej obróbce zbiera około 0,34 mm z krokiem 0,04 mm przy posuwie 120 % z 260 mm/min. Oczywiście tylko do fotografii nie ma chłodziwa lejącego się bezpośrednio na frez kula 2 mm. -
Replika Polskiego silniczka SiM 2b - ambitny projekt
f2cmariusz odpowiedział(a) na Paweł Prauss temat w 2-takty
zanim to zanim tamto to jak widać frezarka z obróbką gniazda pod silnik SiM 2b ruszyła dopiero o 6.30. Ale idzie dziarsko z posuwem 233 mm/min i pewnie po południu obróbka zgrubna frezem palcowym 3 mm się skończy przykład konkretny wykonania elektrody do drążenia gdy nie było jeszcze dla mnie dostępnej metody CNC. elektroda na rączkę łopatki ogrodowej. Mimo że symetryczne to dwie elektrody. Zrobiłem takie same. Przykręcając do duralowego rdzenia stosowne kawałki proste szlifowane ze zbieżnościami czy wycięte toczone ze zbieżnościami kawałki miedzi elektrolitycznej na elektrody. po skręceniu na sucho i po pomiarach że jest wymiarowo prawidłowo całość zalutowałem bo konkretne pamiętam prądy podczas drążenia były stosowane. Gorsza elektroda posłużyła jak wykańczająca. Ale przed skręceniem poszczególne elementy były trawione w kwasie azotowym w celu powiększenia podczas drążenia szczeliny iskrowej. Tak aby wykańczająca elektroda małym prądem zrobiła gładką powierzchnię i abym nie napracował się przy polerowaniu. Powstaje LOGO... -
Replika Polskiego silniczka SiM 2b - ambitny projekt
f2cmariusz odpowiedział(a) na Paweł Prauss temat w 2-takty
kokila do SiM 2b'a była po prostu frezowana. Czyli stałbym przy maszynie i kręcił korbą jedną potem drugą i na końcu trzecią. Albo używając skali albo od zderzaka do zderzaka. I oczywiście forma składałaby się z kilku części co by była do wykonania czyli jak wstawka dana jest wyjęta to narzędzie ma miejsce na obróbką. I oczywiście kokila przed samym procesem azotowania będzie wypolerowana. bo po prostu jest łatwiej niż polerować po azotowaniu. Ja już miałem do czynienia z elektrodrążarkami w czasie studiów czyli od 1977 roku. I bez problemu miałem dostęp i sam korzystałem z nich. Bo na OUS-1 potrafiłem zrobić miedzianą elektrodę składającą się właśnie z kilkudziesięciu elementów. Frezarka CNC była ale że sterowanie wymagało wydziurkowania kart perforowanych to i bardzo był ewidencjonowany ten sposób obróbki. Tak że bez problemu z operatorem wymieniałem się pracą. Ja elektroda. On, oni elektrodrążarka. Zachowała mi się taka elektroda to i pokaże jak dawniej powstawały różności. co do frezowania gniazda następnego to zatrzymałem na Z-2.00 i jutro dalej będzie frezował frez prosty 3.02 mm. Przerwałem bo i dzisiaj zabrakło mi wody w zbiorniku i prawie przestało lecieć chłodziwo. Przestało lecieć bo się skończyło w zbiorniku. A się skończyło bo nagle ni stąd ni zowąd tak się ustawiła woda lecąca na frez że zaczęło rozbryzgiwać ciecz. Tam jest około 4 litrów zapasu nad ssaniem pompki do chłodziwa. I to wszystko znalazło się poza frezarką rozbryźnięte. A osłony z pexi były nie założone bo przecież ładnie szło. Więc zatrzymałem co by wyszło przynajmniej jak w gnieździe gaźnika jutro od rana. Czyli od 6.00 -
Replika Polskiego silniczka SiM 2b - ambitny projekt
f2cmariusz odpowiedział(a) na Paweł Prauss temat w 2-takty
jestem zadowolony z osiągniętego frezowania frezem kulowym 2 mm. Aczkolwiek jak dobrze się przyjrzeć frez kulowy nie zabielił do końca po obróbce zgrubnej frezem palcowym 3 mm. Widać to dokładnie na dnie wybrania gdzie w późniejszym etapie powstanie gwint do przykręcenia zbiornika aluminiowego. Ale że sam promień zakończenia dekla zbiornika jest poprawnie zabielony to mogę przejść do następnej obróbki. A to będzie część kokili gdzie będzie odlewał się karter. Znowu przykładowy poglądowy zrzut ekranu z krokiem 0,3 mm gdzie przy posuwie 222 mm/min operacja trwa niecałą godzinę. Zagęszczając ścieżkę do możliwości czyli wytrzymałości freza obróbka wykańczająca to 10 godzin a wcześniej czyli dzisiaj na noc albo jutro z rana obróbka zgrubna frezem 3 mm. -
"replika" modelarskiego silnika benzynowego felgiebel
f2cmariusz odpowiedział(a) na yarun temat w 2-takty
ja tam jestem pewien że to będzie 2,49 cm3 do wyścigu F2C. -
Replika Polskiego silniczka SiM 2b - ambitny projekt
f2cmariusz odpowiedział(a) na Paweł Prauss temat w 2-takty
W trakcie pracy a tu już po obróbce. Ponieważ zostawiłem około 0,05 mm naddatku w osi Z dla freza kula 2 mm to i nie zabieliło obróbki zgrubnej wykonanej wcześniej frezem fi 3 mm. Zostaje jutro zmierzyć i prawidłowo przybrać co by frezem kulą 1,5 mm zabieliło. Niby proste. Ale wymaga cierpliwości. System centralnego smarowania to podstawa. Zresztą jak i chłodziwo podawane w sposób ciągły na sam frez. Na tej fotografii widać że jeszcze w pierwszej rurce po prawej zaczyna dopiero pojawiać się olej. A w innych już jest. Całe szczęście jest dla każdej rurki regulacja. ściekający olej widać na Hiwin'a prowadnicy. Ponieważ powietrzem czyściłem gniazdo to i widać tego skutki -
Replika Polskiego silniczka SiM 2b - ambitny projekt
f2cmariusz odpowiedział(a) na Paweł Prauss temat w 2-takty
teoretyczny wymiar 10,12 to w praktyce zrobił się prawie dokładnie taki jaki trzeba frezem palcowym 3mm. a jutro frezem kulowym K2 będzie szło kilkanaście minut gdybym puścił tą obróbkę z krokiem 0,14 mm tak jak na rysunku. Wpisałem 0,14 tylko dlatego żeby było widać ścieżkę narzędzia. W praktyce będzie zdecydowanie gęściej czyli pewnie co 0,02 mm. A następnie frez kulowy K1. Obrabiam obszarami i wszystko to rysuję w Rhino3D dlatego widać tyko sam gaźnik z niewielkimi zakończeniami typu elipsoida w miejscach przenikania do obszarów. Robię tak dlatego że nie potrafię często w złożonym detalu wyznaczać granic obszaru obróbki. A jak narysuję w Rhino3D to obszar obróbki jest jednoznaczny i nie wymaga siedzenia po nocach. A po nocach będzie szła obróbka jak zrobię porządnie czyli niezawodnie chłodzenie do wrzeciona i do chłodziwa. Orginalne pompki są po prostu zawodne. Chłodziwo jak przestaje lecieć to widać a na wrzecionie mam termometr i też widać bo jest w centralnym miejscu. -
Replika Polskiego silniczka SiM 2b - ambitny projekt
f2cmariusz odpowiedział(a) na Paweł Prauss temat w 2-takty
Typowy mały frez zakupiony w rozsądnej cenie wymaga korekty w celu osiągnięcia dna głębokiego gniazda w kokili do odlania gaźnika silnika SiM 2b. Tego nie widać ale frez palcowy o średnicy mocowania 4 mm kręci się po prostu w uchwycie wiertarki. I w sposób osiowy wydłużyłem możliwość pracy freza w otworze o co najmniej 12 mm głębokości z pierwotnej głębokości 8 mm. I się frezuje -
Replika Polskiego silniczka SiM 2b - ambitny projekt
f2cmariusz odpowiedział(a) na Paweł Prauss temat w 2-takty
trochę musiałem powiększyć co by było widać ścieżkę coraz bardziej wykańczającą powierzchnię przyszłej kokili do odlania gaźnika silnika silnika SiM 2b z aluminium. widać że to tylko 38 minut na oblecenie całej powierzchni z krokiem 0,06 mm frezem 2,5 milimetra. W praktyce pewnie zwolnię. -
Replika Polskiego silniczka SiM 2b - ambitny projekt
f2cmariusz odpowiedział(a) na Paweł Prauss temat w 2-takty
tak już Ktoś wcześniej zauważył: Nie pogonię... Ale ważne że idzie do przodu te zdjęcia dla nie wtajemniczonego to się powtarzają. Ale to już kanały dolotowe po stronie płyty z ewentualnymi wypychaczami skończone. Bo nawet jak w kanale środkowym według pomiarów brakuje 0,27 mm tylko na głębokości to i tak jest to ogromna objętość kanału dolotowego gwarantujące ciśnienie grawitacyjne doprowadzające i zasilanie wypraski w materiał podczas stygnięcia. teoretyczne wymiary a osiągnięte czyli zmierzone na frezowanym detalu. Nieosiągnięte w osi Z z racji za ciężkiej pracy freza. A drugi raz jutro już nie ma sensu przybierać. Raczej gaźnik powstanie w tym czasie. 0,3 mm to dorysowany naddatek i zero w zecie też jest tak ustawione. W MasterCamie gwarantowało mi to ostrą krawędź. A w Fusion360 widzę że jest to już zbędne. a to praca na jutro. -
Replika Polskiego silniczka SiM 2b - ambitny projekt
f2cmariusz odpowiedział(a) na Paweł Prauss temat w 2-takty
Zawody z Lugo z 2016 roku. Cały czas do kupienia silniki konstruktor i wykonawca silnika pokazanego poniżej prosty ściągacz do zdejmowania tarczy oporowej śmigła klucz do śruby kompresyjnej z tarczą podziałową do bardziej precyzyjnej regulacji kompresji przy odkręcaniu kompresji a także po to aby łatwiej z asfaltu podnieść ten że klucz... przyrząd do wyginania rurek mosiężnych. wirujący rozrząd z podebraniami wyważającymi montaż F2B zamiast gumek przykręcany centralną śrubą M3 z ogromnym aluminiowym toczonym elementem. Nakrętka aluminiowa wklejona w skrzydło na stałe. wypuszczenie modelu F2B -
są wyjątki ewidentnie trzymam model prędkościowy F2A w ręku gdzie widać tylko jedną łopatkę. Przeciw waga tej łopatki jest schowana w aluminiowym kołpaku.
-
Nie zapominajmy o liczbie Macha i liczbie Reynoldsa końcówki łopaty śmigła. Doświadczalnie wyznaczono że muszą być te liczby odpowiednie aby to poprawnie działało. Stąd maksymalna średnica przy danych obrotach obowiązuje jak i grubość i głębokość tejże końcówki. Plus ograniczenia w postaci zastosowanych materiałów...
-
i o tym też warto powiedzieć że dobieramy a właściwie myślimy o prawidłowej a może i lepszej współpracy śmigła z danym konkretnym silnikiem. A z tego co wiem nie ma żadnych konkretnych publikacji... na temat jak w tytule postu. Bo w mojej konkurencji F2C jak zaczynałem było śmigło dwu łopatkowe, pojawiła się przez jakiś czas jedna łopata i ponownie aktualnie wrócono do dwu łopatkowych śmigieł. Oba typy śmigieł kopiowałem, wprowadzaliśmy zmiany i na nowo produkowałem. Każdy rodzaj śmigła ma swoje wady i zalety bo nawet w mojej kategorii były próby nad trzema łopatkami ale widać aktualnie rządzą dwie łopatki. A jak ktoś potrzebuje się wgłębić to polecam prace Piotra Strzelczyka. Teraz znalazłem "WYBRANE ZAGADNIENIA AERODYNAMIKI ŚMIGIEŁ"
-
w pewnych sprawach Wiesław Schier był bardzo konkretny. I jak budował model a robił to na pewno sam bo każda sklejona czy dodana listewka była sfotografowana. I zamieszczony rzetelny opis z rysunkami czy zdjęciami w kolejnej książce. Natomiast starsi modelarze pamiętam jak się licytowali na temat paliw. Czyli jak się miał opis poszczególnych składników do paliwa a realne sprawdzenie silnika w locie czy choćby na stojance. Zostawię to bez dalszego komentarza bo nie wiem ile było zrobionych śmigieł aby opublikować tak konkretną tabelkę pewnych zależności. Przepraszam rodziny śmigieł dwu czy czterołapatowych. Ja mam za sobą wykonania konkretnych form aluminiowych do odbijania śmigieł kompozytowych. ( Czytaj węglowych). Teraz projektuję a właściwie rozwijam kolejną wersję dla najlepszych. Oczywiście pod ich sugestię. Ale moje projekty i moje wykonawstwo były od tych kupowanych od najlepszych po 30 Euro troszeczkę niestety gorsze. Zabrakło po prostu rozwijania tematu czyli kolejnych modyfikacji w projekcie i w sumie także w wykonaniu końcowym samego kompozytowego śmigła. Ja natomiast dysponuję książką gdzie na zadany temat jest taka informacja:
-
Replika Polskiego silniczka SiM 2b - ambitny projekt
f2cmariusz odpowiedział(a) na Paweł Prauss temat w 2-takty
duża ilość wody w obiegu chłodzenia wody skutkuje stabilizacją wymiarową całości frezarki. Ja dołożę jeszcze wodne chłodzenie na silniki krokowe to myślę że będzie jeszcze lepiej. po skończonej pracy przed wyjściem wracam do X0,Y0 i dostawiam czujniki. dzięki płynowi chłodzącemu pozwalam sobie na coraz śmielsze parametry. -
Replika Polskiego silniczka SiM 2b - ambitny projekt
f2cmariusz odpowiedział(a) na Paweł Prauss temat w 2-takty
i zrobiła się zima a jak zima to nie dosyć że zimno jest to i "setki" z rana uciekają. ale wystarczy włączyć wtryskarkę i za parę godzin będzie wszystko w normie. od dawien dawna jak mam coś precyzyjnego do skończenia następnego dnia ustawiam czujniki w osi X i Y na dłuższe przerwy czy świąteczne czy weekendowe. co by wiedzieć gdzie jestem A w osi Z nie problem na nowo złapać "zero". -
"replika" modelarskiego silnika benzynowego felgiebel
f2cmariusz odpowiedział(a) na yarun temat w 2-takty
Nie byłoby trudno zaprojektować nową konstrukcję opartą o sprawdzone rozwiązania i swoje jak i innych kolegów wieloletnie nabyte doświadczenie. Jestem pewien że taki projekt powstałby w programie 3D na laptopie w ciągu paru spotkań. Gorzej już by było stworzyć pełną dokumentację wymiarową każdego z osobna detalu jak i płaski czyli 2D rysunek techniczny złożeniowy całego silnika. Plus parę rysunków perspektywicznych tego złożenia ze stosownymi przekrojami. A już zupełnie niewykonalne zrobi się wykonanie takiego silnika w ilościach produkcyjnych gdzie niezbędny jest odpowiedni park maszynowy. A dla mnie odpowiedni to oznacza odpowiednio dokładny gdzie działka elementarna to jeden mikron a i ten mikron da się jeszcze podzielić na części jak między kreskami mikronowymi jest ponad 5 mm miejsca. niestety mam w tym momencie dostęp tylko do jednej takiej obrabiarki i to w przypadku budowy silników modelarskich najmniej potrzebną (Szlifierka na płasko) Można oczywiście zlecić. I tak robię ale tylko w przypadku gdzie wiem że jest z czego za wykonaną usługę zapłacić... Tylko ze względu na brak czasu dalej w szczegółach nie rozwijam tematu. -
Replika Polskiego silniczka SiM 2b - ambitny projekt
f2cmariusz odpowiedział(a) na Paweł Prauss temat w 2-takty
dzięki uprzejmości Kolegi Kamila Jarek dostałem z wizyty u Pana Jana Sewerniaka parę zdjęć zachęcających do umówienia się i wizyty we Wrocławiu w jak najbliższym czasie. informacja na drugiej stronie książki. imponujący kołpak. śmigło średnicy 280 mm. 22 listopad 1950 roku... jeszcze raz dziękuję za umożliwienie pokazanie kolejnego fajnego kawałka historii. A myślę że będzie więcej po wizycie we Wrocławiu. -
Replika Polskiego silniczka SiM 2b - ambitny projekt
f2cmariusz odpowiedział(a) na Paweł Prauss temat w 2-takty
mając ciekawy specyfik BELGOM ALU czy pastę polerską na bazie tlenków chromu czy pyłu diamentowego warto pamiętać o filcu. Kiedyś miałem pod dostatkiem ścinki filcu polerskiego na bazie włókien wełnianych. Teraz jak się skończył wróciłem ponownie do wacików, płatków bawełnianych dostępnych bez problemu na Allegro Wlewając żywicę do kokili jeszcze nie skończonej w dniu wczorajszym odkryłem że mam kolejny karter oryginalnego SiM 2b do naprawy... ścięta konsolka plus powiększony jeden z otworów. zastosowanie OUS-1 w pracy: widać świeżo zakupiony oryginalny imak na OLX.pl sposób na szybkie wycentrowanie i zrobienie pilotażowego otworu osiowo do części toczonej w celu przewleczenia drutu, ustawienia w osi detalu drutu i wycięcia kwadratowego kształtu w osi detalu. -
Replika Polskiego silniczka SiM 2b - ambitny projekt
f2cmariusz odpowiedział(a) na Paweł Prauss temat w 2-takty
zdecydowanie mogę polecić także zieloną pastę (Chromową). Prawie równie wydajna jak pasta diamentowa. a do samego już polerowania czy odświeżania na równi dobra jak pasta diamentowa. W szczególności w przypadku mechanicznego polerowania z wykorzystaniem filcowych tarcz polerskich.