
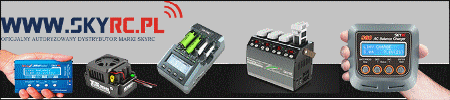
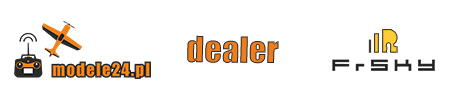
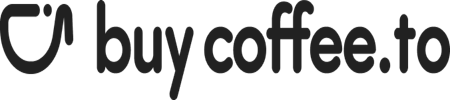
-
Postów
786 -
Rejestracja
-
Ostatnia wizyta
-
Wygrane w rankingu
50
Treść opublikowana przez f2cmariusz
-
Replika Polskiego silniczka SiM 2b - ambitny projekt
f2cmariusz odpowiedział(a) na Paweł Prauss temat w 2-takty
w swojej książce Witold Stańczyk pokazuje rysunek SIM 2b z kołem zamachowym Bardzo starannie wykonana replika: wszystko fotografie dzięki pasjonatowi z miejscowości Duchnów k/Wiązowny k/Warszawy. -
Replika Polskiego silniczka SiM 2b - ambitny projekt
f2cmariusz odpowiedział(a) na Paweł Prauss temat w 2-takty
Dzięki Pasjonatowi z miejscowości Duchnów k/Wiązowny k/Warszawy zeskanowałem wreszcie książkę MODEL DESELS Z 1947 roku wykaz silników z tej książki i niezłe pole dla kolekcjonerów co by pokazali co jest co i jak w rzeczywistości wygląda. Tu jest rozpisane 65 modeli silników. Stan na 1947 rok. -
Replika Polskiego silniczka SiM 2b - ambitny projekt
f2cmariusz odpowiedział(a) na Paweł Prauss temat w 2-takty
-
Replika Polskiego silniczka SiM 2b - ambitny projekt
f2cmariusz odpowiedział(a) na Paweł Prauss temat w 2-takty
zawsze zapraszam na tor modelarski co by się pokręcić wspólnie W tempie co 1,72 sek na obrót. czyli 10 okrążeń przez 17,2 sekundy do 18 sekund. Albo cały wyścig czyli 100 okrążeń przez trzy i pół minuty... Pokręcenie gwarantowane. A to czasami i upadkiem skutkuje jak nieopatrznie balans stracimy. jeszcze chwila i będą gilzy gotowe do frezowania kanałów płuczących. -
Replika Polskiego silniczka SiM 2b - ambitny projekt
f2cmariusz odpowiedział(a) na Paweł Prauss temat w 2-takty
a co tu się obrażać? Kiedyś jak prędkości były "Rytmowe" latało się po czterech. Sam osobiście przed MŚ w Częstochowie na treningu na jednym torze było pięć zespołów choć w powietrzu tylko cztery w tym i ja. Takie czasy rozgrywania zawodów gdy jeszcze nie było przed biegiem oficjalnego treningu organizowanego przez organizatora zawodów na torze gdzie mają odbyć się same zawody. -
Replika Polskiego silniczka SiM 2b - ambitny projekt
f2cmariusz odpowiedział(a) na Paweł Prauss temat w 2-takty
trochę inny tematy: kiedyś model rzeźbiony ręcznie był jak widać przelewany do postaci żywicy odlewniczej a co 10 mm wybrania pozwalały na precyzyjne skanowanie poszczególnych rozciętych przekrojów w celu wprowadzenia skanów do Rhino3D i ustawieniu w przestrzeni rysunkowej tych skanów. A dalej już dokładnie rysowałem modelowy kadłub jako bryła 3D Jak będzie czas a będzie to dokładnie opiszę to co robiłem albo robię. Dokładnie tak samo teraz będę wykonywał formę aluminiową na śmigło. Z tym że akurat mam jedną łopatę całą. Pozyskiwanie jednej łopaty śmigła do niszczącego precyzyjnego skanu mikroskopowego (Dokładnie to widać na 6: 37 ) To mogę sobie pozwolić na maszynie odcinać w ściśle wiadomym miejscu (cięcie frezem palcowym na CNC) a poszczególne przekroje opisać na mikroskopie warsztatowym wprowadzając wyznaczone punkty od razu do Rhino3D. ten syntetyczny olej (czerwony kolor ułatwia rozpoznanie go w paliwie) plus olej rycynowy to składniki mieszanki każdego paliwa do silników samozapłonowych. A nie sam olej rycynowy. Zdecydowanie mniej nagaru się tworzy w komorze spalania niż jak byśmy latali tylko na rycynie. Więcej na 14 stronie. -
Replika Polskiego silniczka SiM 2b - ambitny projekt
f2cmariusz odpowiedział(a) na Paweł Prauss temat w 2-takty
prawie wszyscy moi instruktorzy czy po prostu starsi koledzy modelarze. Z prywatnej biblioteki Waldemara Salacha. -
Replika Polskiego silniczka SiM 2b - ambitny projekt
f2cmariusz odpowiedział(a) na Paweł Prauss temat w 2-takty
zamiast klikania... Kolejne sztuki powstają co by wreszcie przystąpić do wykonania kanałów płuczących. To samo dotyczy wałów korbowych bo przed wykonaniem wałów na gotowo pod azotowanie muszę wypolerować miejsca współpracujących z panewkami. Dopiero azotować. Muszę także uzgodnić z wykonawcą jak pociąć wałki do obróbki mechanicznej i cieplnej i czy wstępnie nie oskórować póki ma twardość hutniczą. Dużo niewiadomych przy zleceniu produkcji wykonania wałów korbowych ale bez problemu do ogarnięcia. -
Replika Polskiego silniczka SiM 2b - ambitny projekt
f2cmariusz odpowiedział(a) na Paweł Prauss temat w 2-takty
Na początek wyjaśnienie: tak a nie inaczej się u mnie wyświetla autor ostatniego postu. Bo do końca nie wiedziałem skąd to określenie padło gdy napisałem kolejną odpowiedz konkretnie dedykowaną. Igły łożyskowe do silnika samozapłonowego po prostu się nie nadają skoro jest inny materiał jakim jest gotowy wypychacz azotowany o dużo lepszych ( Twardość powierzchniowa prawie dwa razy !!! To dużo. Igła ma twardość góra 780 HV po pracy w 150 stopniach Celsjusza a wypychacz 950 HV po azotowaniu w temperaturze 520 stopni Celsjusza. O ciągliwości rdzenia nawet nie wspomnę.(Powtarzam się) przełom igły z łożyska uderzony 200 gramowym młotkiem. Raz. przełom wypychacza odsadzonego uderzony 200 gramowym młotkiem. To się zgięło aż do 80 stopni zanim po kolejnym uderzeniu odpadło. i najważniejsze normalny nowy pilnik po igle z łożyska się nie ślizga tylko zbiera. Widać na końcu zakończeniu sferycznymi igły ubytek materiału. Natomiast po wypychaczu na średnicy 2,6 mm po prostu się ślizga. Gładka powierzchnia sworznia? A co znaczy gładka? Może warto poczytać na temat "TEKSTUROWANIE LASEROWE WARSTWY WIERZCHNIEJ SWORZNIA TŁOKOWEGO SILNIKA SPALINOWEGO W ASPEKCIE TRIBOLOGICZNYM" http://pfmrc.eu/index.php?app=core&module=attach§ion=attach&attach_id=184883 Po co naukowcy się tym zajmują? Bo przecież jak czytam ma się błyszczeć czyli żadnego miejsca na film olejowy?. Brak filmu olejowego oznacza że przy za dużych obciążeniach, zwłaszcza w pobliżu martwego zwrotnego punktu spalania następuje zanik smarowania i dochodzi do styku dociskowo-ciernego co efekty widać na zamieszczonej fotografii przez Kolegę Andrzeja. Dla mnie to po prostu brak nadzoru a właściwie kontroli nad stanem sprzętu. Przekroczyło resurs a Ktoś o to nie zadbał. zabrakło okresowej kontroli ? Bo to trzeba zdjąć tłok z korbowodu? Aby ocenić stan sworznia. Długo by pisać na ten temat. Długo. Tylko po co ciągle o tym samym... Sworzeń zrobiony z wypychacza azotowanego o parametrach które podałem wcześniej. Zabezpieczone przed wypadnięciem zawleczkami dwoma. Taki mam plan odstępstwa jak na razie od oryginału. Myślę że potwierdzi się to w osiąganej eksploatacji silniczka. Przypomnę jeszcze raz. Jestem w posiadaniu dwóch egzemplarzy SIM 2b i tam to tak wygląda: ewidentnie krzywy sworzeń średnicy trzy milimetry i tego tu nie widać ale jedna strona jest ewidentnie na iglaku moletowana co był wcisk w tłoku. Umyję w płuczce to pokarzę molet. drugi tłok wyjąłem z gilzy....i może to jest rozwiązanie Ale igła od łożyska się rozsypie a wypychacz na pewno nie -
Replika Polskiego silniczka SiM 2b - ambitny projekt
f2cmariusz odpowiedział(a) na Paweł Prauss temat w 2-takty
Nie skomentuję bo nie ma o co kopi kruszyć. Moje silniki są dostosowane to takich a nie innych zawodów w ścisły sposób obwarowane regulaminem który muszę przestrzegać. Więc po co temat rozwijać, nakręcając się przy okazji. Merytorycznie poproszę bo dalej nic nie wiem. Dobre te igły z łożysk czy nie dobre? Bo ja jednoznacznie odpowiedziałem że jest lepsze rozwiązanie w postaci wypychaczy z fabryki która je ma w katalogu i na magazynie i jutro będę je miał bo wczoraj zamówiłem. Wykonane w sposób bardzo powtarzalny jeśli chodzi o jakość. Napasałem o konkretnych parametrach tych materiałów. Nie będę powtarzał ale azotowanie odbywa się w 520 stopniach Celsjusza i uzyskujemy twardość 950 HV gdy ŁH15 da się zahartować przy odpuszczaniu w 150 stopniach do twardości 63 HRC znowu sięgam do strony dostawcy stali MULTISTAL gdzie wartość skali 63,3 HRC odpowiada w skali HV 780 jednostek a azotowany wypychać to 950 HV. Zdecydowanie da się to zmierzyć, określić i porównać co nieśniejszym po raz drugi czynię specjalnie dla Kolegi Andrzeja. A nie jak wcześniej napisałem AndrzejC. za co przepraszam jak uraziłem. to samo dotyczy wytrzymałości rdzenia Łh15 to.780 N/mm2. a azotowany wypychać to 1400 N/mm2 Prawie dwa razy bardziej wytrzymały i po wierzchu także bardziej twardy... Z mojego nabytego doświadczenia wiem że każdy element formy wtryskowej po azotowany ma zdecydowanie dłuższy resurs niż bez azotu współpracujące elementy Także w zakresie odlewnictwa ciśnieniowego metalu stały się wypychacze azotowane i oksydowane standardem biorąc pod uwagę żywotność i jakość części. co do tarcia tocznego w główce korbowodu? piętnaście stopni w jedną stronę piętnaście w drugą i tak na zmianę. Nie ma jak się zbudować film olejowy. Więc jak jest za mało to się psuje. Generalnie to praca przejściowa na Politechnice mogła by być z tego. Wspomnę o paru maszynach tokarka i szlifierka TOS na panewkach. Załączam pompę olejową i dopiero mogę uruchomić wrzeciono. Po długim weekendzie jak za szybko uruchomię obroty wrzeciona to słychać bardzo ciężki start bo cały olej spłynie w weekend. Kłania się olej i jego wpływ na zużycie silnika jak i tworzenie czy bardziej zmywanie nagaru co by dalej dobrze ciepło odprowadzać z części silniej się grzejących. Oprócz czystej rycyny jest także olej do wyczynowych dwusuwów z dodatkami. Pisałem już o tym. Także o eterze który dzięki ciepłu parowania skutecznie chłodzi wewnętrznie. w pełni popieram.Nadanie mikroporów na powierzchni to podstawa utrzymania się filmu olejowego. Kiedyś byłem nawet na seminarium dotyczącym tego typu zastosowań lasera.A temat rozwinąłem jak była dyskusja na temat chromowania cylindra. Na razie to tylko w moim zasięgu jest spawanie laserowe. z którego często korzystam. Ale może za słabo się rozglądam? http://pfmrc.eu/index.php/topic/76806-czy-mozna-gdzies-pochromowa%C4%87-tuleje-cylindrow%C4%85/ -
Replika Polskiego silniczka SiM 2b - ambitny projekt
f2cmariusz odpowiedział(a) na Paweł Prauss temat w 2-takty
od wielu wielu lat uważam się za Mechanika Maszyn Mało-skomplikowanych. Daleko mi do Mechanika Precyzyjnego. faktycznie tańszy jest materiał co mnie wcale nie dziwi. Generalnie obydwa materiały na jeden silnik kosztują jak widać grosze. Dalsze przetworzenie czyli wywiercenie otworu nieprzelotowego skrócenie czyli cięcie na wymiar mniejszy od średnicy tłoka o jakieś 1,4 mm na stronę czyli 14 mm minus 2,8 = 11,2 mm. I wszystko by było OK gdyby: powierzchnia bardzo gładka o wysokiej refleksyjności jest potrzebna na elementach toczących się między sobą a igiełka jest takim elementem. Tarcie toczne wtedy występuje . W przypadku panewki główki korbowodu i sworznia ja tam nie widzę ruchu toczenia gdzie występuje tarcie toczne a jak zauważył Pan AndrzejC w czasie pracy korbowód jest obciążony siłami ciśnienia gazów działających na tłok i ta moc nie połamie sworznia zrobionego z igiełki łożyska. I ja tu się w pełni zgadzam. Ale każdy zimny silnik jak się zaleje i go uruchamiamy uderzeniem w śmigło zespół korbowy jest zdecydowanie bardziej obciążony niż podczas normalnej pracy. I mamy problem kruchości wytrzymałości sworznia wykonanego z materiału ŁH15 hartowanego na wskroś a po drugiej stronie stal z rdzeniem o wytrzymałości 1400 N/mm2 i twardym po wierzchu 950 HV gdzie wałek z ŁH 15 ma Re to max 780 N/mm2 czy jak kto woli 780 Megapaskali [MPa}. a twardość jeszcze w skali HRC a to znaczy że iglak od Pawła swobodnie porysuje powierzchnię igły łożyskowej. (Twardość 63 HRC bo myślę że tłok nagrzewa się do ponad 150 stopni) ze strony hurtowni Multistal w której kupuję pozyskałem wiedzę. Tego tutaj nie rozstrzygniemy ale na pewno i taką próbę wykonam na zawodach w Dąbrowie Górniczej. W okolicy mojej pracy na ulicy Sadulskiej w Aninie jest hurtownia łożysk i każdą rzecz mi sprowadzą dostępną na rynku. Wracając do zawleczek. Wydłubałem z używanego zestawu: drut sprężynowy 0,3 mm otwór w sworzniu o średnicy 4 mm to dokładnie 2,4 mm. a tak sobie siedzi wystająca część zawleczki co by można to było łatwo zdemontować a po ponownym włożeniu z pomocą lupy kontrolnie sprawdziłem czy widać że siedzi cała w gnieździe i swobodnie się przesuwa po średnicy w swoim gnieździe. I uwaga. Wiem że sworzeń w tego typie kanałów musi być niedrożny. Otwór w sworzniu będzie nieprzelotowy. -
Replika Polskiego silniczka SiM 2b - ambitny projekt
f2cmariusz odpowiedział(a) na Paweł Prauss temat w 2-takty
Nawiertakiem dotknąłem czoło resztki wypychacza odsadzonego azotowanego. Bez najmniejszego problemu widać zrobiłem początek nakiełka. Zamówiłem 10 wypychaczy fi 4g6 długości 200 mm z serii EM. Materiał 1.2344 to stal narzędziowa do pracy na gorąco 500-550 o C. wytrzymałości rdzenia minimum 1400 N/mm2 i twardości powierzchni na głębokość 0,3 mm minimum 950 HV. (Dobrej klasy pilnik po prostu ślizga się po powierzchni tych wypychaczy) -
Replika Polskiego silniczka SiM 2b - ambitny projekt
f2cmariusz odpowiedział(a) na Paweł Prauss temat w 2-takty
Podane ceny dotyczą wypychaczy 200 mm długości azotowanych. Wypychacz pełny to koszt 3,64 złote za sztukę i z jednego będę miał 12 sztuk sworzni 14 mm długości co daje koszt 30 groszy za sztukę. Wypychacz tulejkowy azotowany to koszt 84,47 zł za sztukę i z jednego wypychacza (35 mm użytku) będę miał dwa sworznie co daje 42,24 zł za sworzeń z otworem 2 mm plus. Zostaje reszta wypychacza z nie zawsze osiowym ulżeniem średnicy ponad 2,5 mm.Wiertło 2,46 sobie swobodnie lata w takim ulżeniu wypychacza tulejkowego. Ponieważ wykonywałem w tego typu wypychaczach otwory to skłaniam się do rozwiązania zasugerowanego na wstępie. -
Replika Polskiego silniczka SiM 2b - ambitny projekt
f2cmariusz odpowiedział(a) na Paweł Prauss temat w 2-takty
wszystko się zgadza, występują jako normalki wypychacze tulejkowe. Ale one są drogie bo szlifowane i w środku na konkretny wymiar tolerowany. Więc tylko z tego powodu mi nie pasują. 35 mm użytku jak dla tej wersji to oznacza dwie sztuki sworznia za kwotę kilkadziesiąt złotych.(~~ 70 zł). Wypychacz zwykły długi to koszt 10 zł. czyli złotówka materiał na sworzeń. Ceny z głowy ale myślę że nie wiele się pomyliłem. Sprawdzę ceny jak biuro w Bytowie po porannej kawie zacznie działalność. -
Replika Polskiego silniczka SiM 2b - ambitny projekt
f2cmariusz odpowiedział(a) na Paweł Prauss temat w 2-takty
kolejny raz przeglądając książkę wypożyczoną z bogatej kolekcji Pasjonata uświadamiam sobie że rozwiązanie zabezpieczenia sworznia tłoka przed rysowaniem czyli popsuciem tłoka już wtedy było stosowane. I wybierając miedzy różnymi rozwiązaniami poruszanymi wcześniej na chwilę obecną nie mam konkretnej decyzji. . Ja preferuje współczesne rozwiązanie jakie jest stosowane w wyczynowych silnikach 2,5 cm3 klasy F2C czyli sworzeń wiercony średnicy 4 mm plus zawleczki z drutu. Gotowy wypychacz wykonany z 0,3 mm warstwą utwardzoną po przez azotowanie powierzchni. Przy jednoczesnym ciągliwym rdzeniu dającym się na wolnych obrotach widiowym wiertłem wiercić. A pociąć gumówką z użyciem płynu chłodzącego to nie problem i doszlifowanie czoła na zadany wymiar. Same zawleczki? Mam działające wzory od lat. Zeskanuję, z wymiaruję stan rozprężony i zamieszczę. I ku temu rozwiązaniu prawdopodobnie będę zmierzał. Bo wciskany(wbijany) sworzeń pełny z igły od łożyska średnicy 3 mm jakoś mnie nie przekonuje. -
Replika Polskiego silniczka SiM 2b - ambitny projekt
f2cmariusz odpowiedział(a) na Paweł Prauss temat w 2-takty
Dzięki uprzejmości Pana z Duchnowa k/Wiązowny k/Warszawy mam w ręku jeden z wielu egzemplarzy z Jego zasobnego modelarskiego zbioru. Książka z 1947 roku. Czyli po 72 latach od daty publikacji zeskanuję całość i upublicznię. Dawno wymyślono i specjalnie nie wiele się pozmieniało. Kwestia tylko wykonania stosownego oprzyrządowania albo kupienia na stronach wcześniej przeze mnie podanych. ja swoje wymiary doskonale znam i oscylują one wokół 14 średnicy. "MORSE TAPERED" - najbardziej klasyczny z klasycznych stożków występujących przy obróbce mechanicznej. Ja użyłem akurat stożka teraz typowego gdzie narzędzie do robienia można bez problemu kupić. (1:50). Jutro w pracy zacznę dzień od sprawdzenia jaki jest stożek na oryginalnym amerykańskim trzpieniu przywiezionym do mnie przez Pawła. ten pierwszy trzpień z nałożonym docierakiem to całkowity oryginał. Reszta dorobiona na wzór oryginału. Wizualnie takie same jedynie w amerykańskim końce trzpienia także są obrobione mechanicznie w dorabianych widać tylko ślady po obróbce cieplnej. -
Replika Polskiego silniczka SiM 2b - ambitny projekt
f2cmariusz odpowiedział(a) na Paweł Prauss temat w 2-takty
właśnie zakończyła się aukcja: 412+20 =432 euro x 4,28 = 1850 zł taką cenę osiąga na ebay.de stolik krzyżowy nadający się także do OUS-1 po bardzo niewielkiej modyfikacji. Pracowałem na takim samym jak na fotografii ponad pięćdziesięcioletnim i w pełni mogę polecić. Przybieram jedną działkę i na pewno pięć setek dokładnie ubywa. A przybranie połowy działki gwarantuje ubytek nieprzytępionym ostrzem dwie i pół setki. Jak na dorosłej tokarce gdzie akurat toczę cylindry i wykonuję to pod hartowanie i szlif z naddatkami 0,15 z dokładnością od 0,01 mm. Samo wychodzi mierząc i po prostu przybierając do póki ostrze noża się nie stępi a na NC10 co drugi osiągnięty wymiar ostrzę narzędzie. -
Replika Polskiego silniczka SiM 2b - ambitny projekt
f2cmariusz odpowiedział(a) na Paweł Prauss temat w 2-takty
W dniu dzisiejszym wylądowałem w miejscowości Duchnów k/Wiązowny k/Warszawy do osoby która dla mnie jest kopalnią wiedzy na temat którym i ja się pasjonuje. Świat modelarski w czasach produkcji SIM 2b. Ogrom silników powstałych przynajmniej jako działające prototypy przyjemnie zaskakuje. Zestawienie: umówiłem się że z bardzo bogatego archiwum będę sukcesywnie pożyczał materiały w celu kopiowania. A zależy mi na jakości dlatego telefonem zrobiona kopia trochę jest za słaba do publikowania. -
Replika Polskiego silniczka SiM 2b - ambitny projekt
f2cmariusz odpowiedział(a) na Paweł Prauss temat w 2-takty
jest czym to się chwalę. Ale zdecydowanie na pierwszy plan wysunę kwestię spotkań typu modelarskiego. Czyli wymiany doświadczeń w gronie zaproszonych gości specjalnie z okazji wizyty Pawła w Warszawie. Tematów poruszyliśmy mnóstwo. Między innymi. Docierak oryginalny. Amerykański. Średnica robocza fi 4 mm z moletką wałek i otworem służy do nabijania rozciętej tulejki na stożkowy wałek. Przyrządu do ściągania nie ma. Rączka jak widać Duraluminium Ja zwykle ta firma preferuje spiralne rozcięcie tulejki. Która w tym wypadku jest pewnie z żeliwa. jeszcze inny typ budowy docieraka znalazłem w necie. -
Replika Polskiego silniczka SiM 2b - ambitny projekt
f2cmariusz odpowiedział(a) na Paweł Prauss temat w 2-takty
-
Replika Polskiego silniczka SiM 2b - ambitny projekt
f2cmariusz odpowiedział(a) na Paweł Prauss temat w 2-takty
Dostarczone przez Pawła w dniu dzisiejszym najlepsze z najlepszych docieraków. Wzór dla mnie do kopiowania do własnej produkcji. tulejki rozprężne które służą do docierania mają spiralną linię rozcięcia. Duraluminiowe oprawy-trzymacze elementów dorabianych u nas wykonam trochę inaczej a to ze względu na bardziej precyzyjny sposób regulacji. to samo i w tych elementach docierających rozcięcie widać jest wykonane po linii spiralnej. -
Replika Polskiego silniczka SiM 2b - ambitny projekt
f2cmariusz odpowiedział(a) na Paweł Prauss temat w 2-takty
Narysowałem co mi jest potrzebne. Bo to podstawa wiedzieć co dokładnie mi jest potrzebne. Jeśli chodzi o narzędzie bo wszelakiego rodzaju wysokości narzędzia w stosunku do detalu to dopiero w trakcie frezowania wyjdzie. kiedyś wycięty kwadratowy trzymak do fi6. Niestety ustawione "zero" na oko i jednego rogu nie ma... aktualnie na stanie w szufladzie wcześniej wykonane frezy widiowe do podcięć. Ja muszę mieć freza widiowego fi12 czterostrzałowego. A mam tylko nowe tak dużo padło słów że ze szmatą i oliwiarką pobiegałem wokół tokarek co by wstydu nie było robiąc fotografie. -
Replika Polskiego silniczka SiM 2b - ambitny projekt
f2cmariusz odpowiedział(a) na Paweł Prauss temat w 2-takty
niestety słowo maniek kojarzy mi się pejoratywnie od tamtych Mistrzostw Polski. A że jestem z natury spolegliwy to będziemy mieli SIM 2b. -
Replika Polskiego silniczka SiM 2b - ambitny projekt
f2cmariusz odpowiedział(a) na Paweł Prauss temat w 2-takty
nigdy nie byłem miłosnikiem starych motorków. Ale widzę wszystko do czasu. Podane linki dla mnie znakomita wiedza jak i dydaktyka. Co do "ambitnego projektu". Bez najmniejszego problemu po wprowadzeniu modelu cylindra narysowanego w Rhino3D w formacie step tym razem. Bo wczeniej by format igs intuicyjnie wygenerowałem ścieżkę narzędzia dla freza-piłki tarczwej na początek takiej jaką kupiłem czyli 25. Zdecydowanie jest to za duża średnica bo nie robi właściwego kształtu. Kszatałt prawdopodobnie powstanie prawidłowy po wpisaniu średnicy narzędzia poniżej 18 mm. Wysokości początku pracy nie są prawidłowe. Nie problem poprawić. Na symulacji tylko jedno okno się wycina. I pierwsze przybieranie jest całe zrobione. W rzeczywistości pierwsze przybieranie będzie nie większe niż 0.05 mm na jedno okrążenia aż do osiągnięcia zadanego konturu. W Rhino precyzyjnie określę minimalną średnicę freza jak i maksymalną średnicę trzpienia do tego freza i pewnie jednoostrzowy wariat powstanie z jakiegoś połamanego freza albo przygotówki jak znajdę w swoich czy kolegów zasobach. -
Replika Polskiego silniczka SiM 2b - ambitny projekt
f2cmariusz odpowiedział(a) na Paweł Prauss temat w 2-takty
poczekaj do końca licytacji