
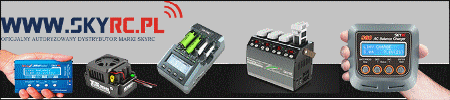
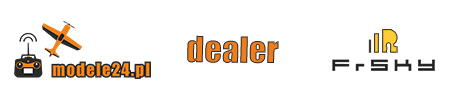
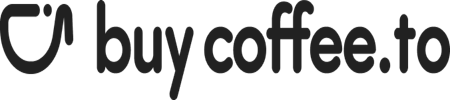
-
Postów
786 -
Rejestracja
-
Ostatnia wizyta
-
Wygrane w rankingu
50
Treść opublikowana przez f2cmariusz
-
od końca odpowiem. Z mojego nabytego doświadczenia wiem że żaden silnik czy samozapłonowy czy żarowy używany nie ma dużej żywotności. Czytaj kompresji. Dlatego że w warunkach polowych jest bardzo dużo kurzu czyli ziarenek mikro kwarcu który zasysając powietrze zasysa także kurz co wydatnie wpływa na żywotność. Oczywiście inne są warunki na torze modelarskim takim jakim był Tor Modelarski w Częstochowie na Włókniarzu a zupełnie inne na wiosennym lotnisku pełnym zielonej trawy. Większość silniczków jakie w mojej obecności się popsuły to rysa na tłoku z powodu że coś wpadło do środka podczas pracy albo defekt którejś pracującej części silnika. Dla mnie nie najmniejszego problemu w przerobieniu silnika popularnego na inną wersję. W szczególności że inni modelarze dawno już to robili i opublikowali rysunki tych że przeróbek. Na ukraińskich czy rosyjskich forach jest to dokładnie pokazane. I jeśli nawet będzie to problem w przerobieniu to po zasięgnięciu wiedzy od kolegów czy z Internetu następny raz pójdzie dużo lepiej a wybiegając jeszcze dalej satysfakcja gwarantowana dla każdego. Przynajmniej tak jest w moim przypadku bo mało rzeczy jest mnie w stanie zaskoczyć jeśli chodzi o zrobienie czegoś na dobrym poziomie. A przez to rozumiem że wykonanej pracy nie muszę się wstydzić.
-
Replika Polskiego silniczka SiM 2b - ambitny projekt
f2cmariusz odpowiedział(a) na Paweł Prauss temat w 2-takty
ustawienie równoległości względem prowadnicy X to podstawa. Zarówno elementu obrabianego jak i elektrody. Elektroda dodatkowo także jest ustawiana równolegle do osi Z. Rysunkowe przestawienie względem bazującego kołka i dwadzieścia minut samego drążenia z przynajmniej na początku kontrolą czy drąży w odpowiednim miejscu. teoretyczne, rysunkowe ustawienie i te praktyczne. tu ewidentnie zalane "naftą" i się drąży. efekt końcowy. Widać że tło elektrody nie całe pracowało. Ale że płynnie powierzchnie nierozwijalne przechodziły między sobą to i zakończyłem po dwudziestu minutach pracy na elektro drążarce. Generalnie jestem zadowolony bo delikatny rysunek liter został oddany na powierzchni nierozwijalnej. Logo "ambitnego" projektu to wiadomo gdzie powstanie. Pozostaje kwestia napisu Made in Poland oraz numeracji fabrycznej.? Niezbędnej w wiadomych względów nie do końca oczywistych dla każdego !!! -
Plac dla modeli latających z wrotkowiskiem. https://www.google.pl/maps/@52.2337814,20.9548219,275m/data=!3m1!1e3?hl=pl
-
Replika Polskiego silniczka SiM 2b - ambitny projekt
f2cmariusz odpowiedział(a) na Paweł Prauss temat w 2-takty
na to pytanie nie ma konkretnej odpowiedzi. Dlaczego? Bo najpierw praca i rodzina albo odwrotnie jak kto woli czyli Rodzina i praca a na końcu hobby w które jak na razie wymaga potężnego wkładu czasowego. A praca to konkretnie szanowanie zleceń od czołowych zawodników ze świata i rozwijanie ich koncepcji. Choćby kolejna wersja śmigła bo jeśli już jest śmigło narysowane i wykonane metodami CAD/CAM i czynnik ludzki jest zredukowany do minimum to po sezonie warto dalej modyfikować. Ale w trakcie tego testowego sezonu z jednej formy powstają różne modyfikację skoku, kształtu a to dzięki temu że powstają prefabrykaty grubsze do modyfikacji po przez przyklejenie w podziale formy stosownych blaszek pogrubiające wyrób do modyfikacji w kontrolowany sposób. co do wypalenia napisu to po prostu rysunek z naniesionymi wymiarami pozwoli mi ustawić odpowiednio elektrodę względem wcześniej wykonanej kokili... -
Replika Polskiego silniczka SiM 2b - ambitny projekt
f2cmariusz odpowiedział(a) na Paweł Prauss temat w 2-takty
powstała elektroda co by wypalić napis "Replica SiM 2b" w formie stalowej do odlania karteru z aluminium. a jak trafić w odpowiednie miejsce elektrodą w gniazdo detalu? Dopóki sobie tego nie narysuję to sam nie wiem. ale jak narysuję wszystko będzie jasne. Ale to dopiero jutro. -
Replika Polskiego silniczka SiM 2b - ambitny projekt
f2cmariusz odpowiedział(a) na Paweł Prauss temat w 2-takty
Po prostu byłem parę razy w tej szkole w celu pozyskania elementów tokarki OUS 1. Koneksje modelarskie pozwoliły mi mieć to co było niezbędne w modelarni. Choć ostatni zakup OUS 1 dla zakładu z którym wtedy współpracowałem odbył się normalnie w sklepie metalowym w Warszawie. Stały w sklepie i wystarczyło zapłacić gotówką a po chwili cała OUS 1 razem ze stolikiem była w bagażniku kombi. powstała elektroda do wydrążenia napisu. Niestety coś poszło nie tak bo z rana użyłem pierwszego złego pliku ze zbyt cienkimi literami. Jutro drugi raz mnie czeka to samo ale już z dobrym plikiem. -
Replika Polskiego silniczka SiM 2b - ambitny projekt
f2cmariusz odpowiedział(a) na Paweł Prauss temat w 2-takty
od niedawna mam zmodernizowane odczyty na starej ale zasłużonej tokarce-frezarce OUS 1 z 1982 roku wyprodukowaną przez Zasadniczą Szkołę Zawodową tow. Salezjańskiego w Oświęcimiu. Cyfrowy odczyt zakupiłem dawno a od niedawna działa w osi X i naprawdę jestem zadowolony. Ułatwia toczenie średnic bo rzeczywiście na ostatnich precyzyjnych toczeniach "zero" wpadki. Oś Z po staremu. Czyli przesuwne mocowanie wymiennego mechanicznego czujnika zegarowego w zależności od potrzeby. OUS 1.mp4 -
śmigło kompozytowe siedzi dociśnięte do piasty zaopatrzonej w ostre nacięcia kołpakiem. Kołpak ma wystającą śrubę M6 ale o skoku 0,75 zamiast typowego skoku jeden dla gwintu M6. Cała siła z jaką dociskamy jest limitowana otworem w kołpaku o średnicy fi 3,2 mm. Zatem przetyczka wykonana z długiego klucza ampulowego o sześciokącie 5 milimetrów. Sześciokąt 5 mm to klucz do kompresji z długim pokrętłem ułatwiającym precyzyjną regulację kompresji a reszta klucza czyli ta rączka jest cieniowana do średnicy 3 milimetry i znakomicie nadaje się do dokręcania śmigła. I dokręcamy ile mamy sił trzymając śmigło przy samej piaście. Dodatkowo każde śmigło wyjęte z formy po ścięciu wypływek jest zakładane na zatoczony wałek na tokarce. Średnica zatoczenia jest ciasno dobrana co umożliwia zatoczenie jednej i drugiej strony śmigła przy piaście. Przy czym po zatoczeniu śmigła wtam gdzie styka się z piastą śmigła dodatkowo zataczam specjalnie zrobionym nożem rowki co daje szansę wbić się aluminiowej piaście w śmigło. Co by zwiększyć szansę na nieobracanie się śmigła jak silnik "kopnie" drugi skuteczny sposób to płaska część tarczy oporowej bez ryflowania za to zaopatrzona w jeden kołek. A śmigło ma otwór w odpowiednim miejscu pod ten kołek. To zdjęcie podczas kontroli technicznej i jest wykręcana dysza w celu kontroli dopuszczalnej średnicy 3 milimetry. A na skrzydłach widać osłonę termiczną zdejmowaną przed samym wyścigiem. Szczególnie ważne w gorące słoneczne dni. A o samych śmigłach i technologii wykonania śmigła ( narysowania 3D w RhinoCeros3D) a właściwie wykonania formy aluminiowej (Fusion360) na pewno także opowiem i udokumentuję to wszystko aktualnymi fotografiami w osobnym wątku.
-
-
Replika Polskiego silniczka SiM 2b - ambitny projekt
f2cmariusz odpowiedział(a) na Paweł Prauss temat w 2-takty
co do samego frezowania kanałów płuczących w cylindrze to wykonuję to na zmodernizowanej a wcześniej wykonanej napędzanej silnikiem krokowym tak zwanej czwartej osi do frezarki trzyosiowej. Co z tego że zrobiłem czwartą oś jak software w międzyczasie stał się dla mnie wersją niedostępną bo pracuję pracuję na oficjalnej edukacyjnej wersji Fusion360 i jak kiedyś potrafiłem uruchomić czwartą oś to teraz nie potrafię. A nie potrafię bo jej w edukacyjnej wersji nie widzę. Może i jest ale ja nie potrafiłem, stąd wersja zastępcza i ręcznie do zderzaka obracam co 90 stopni. Wymaga to stosowania dodatkowo minutnika w telefonie co by wydajność nie spadła. To tylko 400 przekręceń... Oczywiście to adoptowane wrzeciono OUS-1 z 1968 roku bez przeróbki z zakupioną oprawką ER32 na morsie M2 i z tyłu widać ściągacz M10. -
to pewnie będzie dłuższy wywód. Ale że się jeszcze frezuje to nie ma problemu trochę wprowadzić w tajniki kategorii modeli wyścigowych na uwięzi F2C. Modele coraz lżejsze, (dzięki technologii bez drewna przy budowie) to i coraz szybsze. W prędkości ze zwolnieniem prędkości obrotowej poradzono sobie bez problemu zwiększając długość linek tak że 1 kilometr model pokonuje przez 9 okrążeń a nie 10. W Wyścigu F2C dalej jest 15,92 m a prędkość obrotowa bez zmian była na poziomie 16,1 sekundy na 10 okrążeń. Co przy trzech zawodnikach startujących w jednym biegu i wieku pilotów stanowi problem ukończenia biegu. Kończy to się zazwyczaj rozbiciem modelu. A model rozbity to praktycznie złom. Spowolnienie prędkości modeli wyścigowych odbyło się do tej pory po przez zmiany regulaminowe. Gaźnik ma mieć średnicę 3 mm i ma do tego doszedł a-la tłumik który zwiększył troszeczkę powierzchnię czołową modelu. Zmiana średnicy z dowolnej czyli dużej na 3 milimetry spowodowała że modele bez problemu zaczęły latać po 50 okrążeń. Czyli biegi eliminacyjne rozgrywano na jedno międzylądowanie. Zrobiło się to nudne i w przepisach zmieniono że musi być przynajmniej dwa międzylądowania na 100 okrążeń i w finale na 200 okrążeń także musi być odpowiednia liczba lądowań. Tak że dzisiaj 7 cm sześciennych paliwa wystarcza na około 44 okrążenia co daje możliwość taktycznego wyboru międzylądowania między 30 a 40 okrążeniem. Wtedy jak inni lecą i nie przeszkodzą w szybkim lądowaniu piloci wszystkich trzech zespołów jednocześnie na 33 okrążeniu gaszę silniki i jednocześnie lądują. Przeszkadzają sobie wzajemnie i łatwo o nie skończenie biegu. analogicznie po zrobieniu 67 okrążeń wszyscy jednocześnie gaszą silniki i łatwo wtedy o wypadek. widać wielofunkcyjny zawór umieszczony na przodzie zbiornika o pojemności wraz z instalacją doprowadzającą paliwo do silnika 6,9 cm sześciennego, który w połączeniu z tankowaczką ciśnieniową na ramieniu mechanika i zaworem na palcu umożliwia błyskawiczne tankowanie. Wręcz perfekcyjne. Stosowne filmy najlepszych zamieszczę później. Ale tu przykład dobrej pracy mechanika: 20892348_146509639270942_4666710953285386240_n.mp4
-
Replika Polskiego silniczka SiM 2b - ambitny projekt
f2cmariusz odpowiedział(a) na Paweł Prauss temat w 2-takty
po kolejnych próbach już wiem jak będzie wyglądał przód motorka z napisem Replica SiM 2b. Litery nieznacznie pogrubione od poprzednich wzorów i wygląda to tak: Replika SiM 2b.mp4 pora wykonać elektrodę z miedzi elektrolitycznej i wypalić zaakceptowany przeze mnie napis. Będzie minimalnie większy od tego tu pokazanego. Bo każda literka będzie szersza o rozpalenie (0,04 mm na stronę). -
cytuję: " w bardzo małych zbiornikach typu 50ml ". To jak mam nazwać zbiorniki w wyczynowych modelach na uwięzi w kategorii F2C ? Gdzie pojemność z całą instalacją doprowadzającą paliwo do silnika nie może praktycznie przekroczyć 6,9 cm sześciennego? Co do samego paliwa samozapłonowego stosowanego w modelach wyścigowych F2C to od wielu lat nic się nie zmieniło i dokładnie to opisywałem w wątku o budowie Repliki silnika SiM 2b. Generalnie przypomnę że bez rycyny się nie da latać. Drugie tyle oleju stosujemy oleju syntetycznego czy pół syntetycznego przeznaczonego do wyczynowych silników dwusuwowych zawierający detergenty zmniejszające odkładanie się nagaru. Tutaj każdy ma inne nabyte doświadczenie co i jak stosować. Same rurki neoprenowe w modelach wyścigowych wyglądają tak: generalnie jak widać są jak najkrótsze i w niektórych przypadkach gdy króciec z silnika wychodzi na przeciwko króćca ze zbiornika to rurka jest minimalnej długości. Ta długa to idzie do wydechu do "podlewania". Bez tej dozy silnik nie zaskoczy a znowu bez dozy na kółko startowe model bez przerywania poprawnie nie wystartuje. to widać na tej fotografii. Trzy rurki. Pierwsza to dodatkowe paliwo na kółko startowe, druga rurka to normalna paliwowa na 36 kółek lotu a ostatnia długa to podlewanie na tłok. Niezbędne aby poszedł silnik od pierwszego pociągnięcia śmigłem. Wcale nie musi być uderzenie w śmigło !!!
-
a ja na bazie swojego nabytego doświadczenia w kategorii F2C w stosowaniu różnego rodzaju wężyków wiadomego i niewiadomego pochodzenia polecam wężyki neoprenowe. Bez problemu kiedyś znalazłem dostawcę w kraju tak i teraz przykładowy dostawca oryginalnego wężyka produkowanego w Stanach.
-
Replika Polskiego silniczka SiM 2b - ambitny projekt
f2cmariusz odpowiedział(a) na Paweł Prauss temat w 2-takty
okazuję się że dobranie proporcji wielkości liter w opisie na karterze stanowi dla mnie jakiś problem. Bo to co na rysunku wyglądało całkiem poprawnie w rzeczywistości jest dwa razy za cienkie w prze cieniowaniach liter a odpowiednie tam gdzie litery są grubsze. Metodą prób i błędów na pewno wypracuję odpowiednie napisy. co do cylindrów a w nim wykonanie okien płuczących, nie ma problemu. Frez palcowy widiowy 1,5 mm doskonale sobie daje radę i pierwsze tuleje do hartowania niedługo będą gotowe. a sam proces frezowania wygląda tak: Start cutting. SiM 2b..mp4 efekt każdego wyfrezowanego kanału jest pokazany na końcu filmu gdzie obok widać oryginał. -
Replika Polskiego silniczka SiM 2b - ambitny projekt
f2cmariusz odpowiedział(a) na Paweł Prauss temat w 2-takty
trochę słabej jakości powstał w dniu dzisiejszym ten film. To pierwsza próba wykonania na karterze napisu: "REPLIKA SiM 2b. Ma to jak najbardzej sens i w tym kierunku będę zmierzał. Na pewno zdecydowanie lepszy wstawię film ale to innego aparatu do makro potrzeba.. A i sam napis wymaga poprawy proporcji samych liter. video-1611174741.mp4 -
Replika Polskiego silniczka SiM 2b - ambitny projekt
f2cmariusz odpowiedział(a) na Paweł Prauss temat w 2-takty
doskonale zdaję sobie sprawę a pro po oczekiwań modelarzy czy "kibiców". Idzie do przodu. Oczywiście nie tak szybko jak bym chciał... Choćby z powodu zamówień na nowe śmigła czy drobne elementy z 7075 T6/T561 oraz jak dla mnie duże elementy z 7022 stan materiału T651 czyli odprężony przez rozciąganie. Szczegóły w dalszych relacjach... Start cutting. SiM 2b..mp4 -
Replika Polskiego silniczka SiM 2b - ambitny projekt
f2cmariusz odpowiedział(a) na Paweł Prauss temat w 2-takty
w tym wszystkim zapomniałem o rurce w zbiorniku. Rurka z duralu podaje z dna zbiornika paliwo do gaźnika. Mocowana jest na gwincie M3. U mnie będzie podobnie. Orginał w pełnej krasie z zakończeniem M3 a w środku otwór 1,5 mm dalej stosownie większa średnica co by ścianka rurki była około jednego milimetra grubości. Widać brak staranności w wykończeniu powierzchni ze sobą mających być spasowane i zapewnić szczelność. Ja troszeczkę zmodyfikowałem tą prostą rurkę... -
Replika Polskiego silniczka SiM 2b - ambitny projekt
f2cmariusz odpowiedział(a) na Paweł Prauss temat w 2-takty
a dlaczego kanał dolotowy jest zbieżny w mojej kokili? Odpowiedz jest prosta. To wynika z mojego nabytego doświadczenia gdy kiedyś co by był tańszy mój konkretny odlew pracowałem w odlewni wykonując swoje także odlewy jakby przy okazji. a tam formowałem zawsze na kawałku kija układ wlewowy odpowiednio formując właśnie taki kanał stożkowy zwężający się. Reasumując kanały w dobie CAD/CAM i CNC same się wykonały i do tego stożkowe. Dużo więcej by było pracy chcąc wykonać kanały stożkowe na konwencjonalnych obrabiarkach. Po prostu robiłem proste z pod wiertła. I wtedy po docięciu wlewu zostawiając trochę na złapanie w uchwycie mamy pierwszą bazę do obróbki. -
Replika Polskiego silniczka SiM 2b - ambitny projekt
f2cmariusz odpowiedział(a) na Paweł Prauss temat w 2-takty
to się absolutnie zgadza co napisałeś Jacku na temat dalszego sposobu obróbki elementu jakim jest gaźnik z elementem do przykręcania zbiornika. Z tym że co człowiek to i inne podejście do tematu czyli szeroko pojętej obróbki odlewu kokilowego. W moim przypadku obróbka odlewu odbędzie się na frezarce a to zmienia całkowicie podejście do tematu. W pierwszym etapie powstanie gwint do zbiorniczka na frezarce plus M3 na rurkę aluminiową do ciągnięcia paliwa z dna zbiornika. Frezowałem takie już gwinty odpowiednio zrobionym frezem jedno ostrzonym. I mam pełną kontrolę nad przebiegającym procesem i gwint z eleganckim zakończeniem czy wybiegiem sam powstaje.? Dalszy etap to wkręcenie w prostopadłościan stalowy, zaciśnięcie w odpowiednim miejscu i obrobienie czterech otworów po kolei zmieniając co 90 stopni prostopadłościan. Reasumując: Mam tylko konwencjonalne tokarki plus jedna malutka CNC ale na niej nie ma sterowania do robienia gwintów. Jeszcze nie mam bo przeróbka wchodzi w grę na zmianę sterowania zostawiając zasadniczą mechaniczną część maszyny. -
Replika Polskiego silniczka SiM 2b - ambitny projekt
f2cmariusz odpowiedział(a) na Paweł Prauss temat w 2-takty
jeszcze wczoraj bylem pewien że to już koniec wszelakich obróbek skrawających czy elektroiskrowych przy kokili do Repliki Silnika SiM 2b. Ale jak widać na zamieszczanych przeze mnie fotografiach wcześniej i teraz: inaczej wygląda kształt wejścia - ssania w gaźniku u mnie ( na razie na kokili) i w orginale. Ale po krótkim namyśle zostawiam to co zrobił frez kulowy K0,75 bo po prostu jest ładnie. zestawienie orginału i to co kiedyś narysowałem. orginał -
Replika Polskiego silniczka SiM 2b - ambitny projekt
f2cmariusz odpowiedział(a) na Paweł Prauss temat w 2-takty
tempa szalonego w budowie kokili nie ma ale jeśli jak kiedyś codziennie coś zrobię to finał jest pewny. To oczywiście moja prywatna opinia. Pierwszy wlew w gorącą kokile pewnie w przyszłym tygodniu odbędzie się pod warunkiem że odlewnia z którą wcółpracuję nie zrobiła urlopu w sierpniu. tak jak napisałem prace frezerskie nad kokilą do odlania kartera Repliki Silnika SiM 2b zakończyłem tak jak i prace tokarskie w dniu dzisiejszym dokończyłem. rdzennik wykonany. Przykręcany od tyłu kokili śrubą M6 wstawienie tego rdzenia gwarantuje nie powstanie tak dużej objętości która jest zawsze szkodliwa podczas odlewów. Mam nadzieję że wypychacze postawione wokół tego rdzenia zepchną detal z rdzenia czyli kokili... widać że już troszeczkę przetarłem powierzchnie które później będą odpowiedzialne za jakość powierzchni odlewu tu rdzeń ciasno wsunął się na swoje miejsce po dociągnięciu kluczem śruby trzymającej rdzeń. ingerencja biaxem będzie niezbędna w celu skasowania wstawki na drodze dolotu surowca do detalu. To wynik wstawienia wstawek i nie dokończenia wcześniej korekcji kształtu w obrębie wstawek... Poprawię ręcznie. pokazane na przekroju mocowania dzisiaj utoczonej wstawki Bardziej dokładnie ten fragment mojej pracy. Narysowana śruba imbusowa to M6x20 z sześciokątem pod klucz 5 mm. -
Replika Polskiego silniczka SiM 2b - ambitny projekt
f2cmariusz odpowiedział(a) na Paweł Prauss temat w 2-takty
i generalnie wszelkie prace dotyczące obróbki skrawaniem zakończyłem. Pozostało wszystko uruchomić czy jak kto woli rozruszać na sucho. Jak będzie działać na sucho to zobaczymy jak działa na gorąco czyli ponad 300 stopni dostanie ze zwykłej kuchenki elektrycznej. tyle wystarczy rozsunąć dwoma łyżkami aby kołki przestały ciasno pasować. Samo frezowanie drugiej strony wykonałem z rana po odpowiednim narysowaniu- dorysowaniu tego co chcę wykonać. Bo wcześniej to tylko wiedziałem że są potrzebne wybrania co by po wlaniu aluminium móc rozpołowić kokilę. tu to sam rysunek tejże polówki kokili. jest to narysowane jak już większość wie w Rhino3D na jednej z warstw: warstwy widoczne z boku rysunku gdzie opisane są w sposób jak widać. a ścieżki narzędzia generują się same w Fusion360 po zaimportowaniu rysunku z Rhino3D w uniwersalnym formacie STEP w sumie sama ścieżka narzędzia to godzina pracy freza palcowego fi4 mm. tu wychodzi Machining time 1:00:00 rzadko a właściwie pierwszy raz widzę tak równy wynik w postaci dokładnie jedna godzina bo: zwolniłem teraz do 80% posuwu 203 mm/min i maszyna realnie pracowała 1:16:42 Zwolniłem a i tak maszyna stała bo byłem jak zwykle już czym innym zajęty. Ale ważne że zrobione jest kolejny etap i chyba więcej prac na frezarce przy kokili nie przewiduje.? -
Replika Polskiego silniczka SiM 2b - ambitny projekt
f2cmariusz odpowiedział(a) na Paweł Prauss temat w 2-takty
udało się wreszcie znaleść czas na wykonanie podebrań na łyżki którymi po wlaniu stopu aluminium rozpołowi kokile umieszczoną na stole. Trochę w kolejności przy montażu filmu się pogubiłem... Jest nie po kolei ? lapy.mp4 coraz mniej zostało pracy do gotowej kokili czyli pierwszych odlewów. -
Dobrze że tego posta nie przeczytałem przed wykonaniem tych prac ? średnica 2,83 na długości 66,87 mm czyli ponad 23 średnice... Zapewniam robiłem i dłuższe. Niestety nie udokumentowane bezpośrednio fotografią czy filmem na maszynie. Takie szpilki formują otwór w procesie wtryskiwania termoplastycznych tworzyw sztucznych a średnica otworu jest dobierana za każdym razem do aktualnie zakupionych wkrętów co by w procesie montażu można było trwale skręcić obudowę plastikową. Pewnie każdy się z tym spotkał rozkręcając dowolne elektronarzędzie. niewiedziałem.mp4