
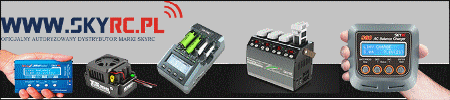
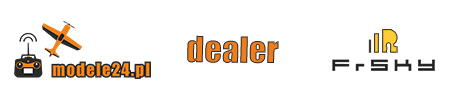
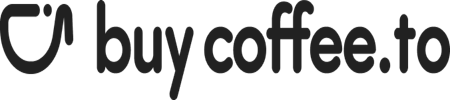
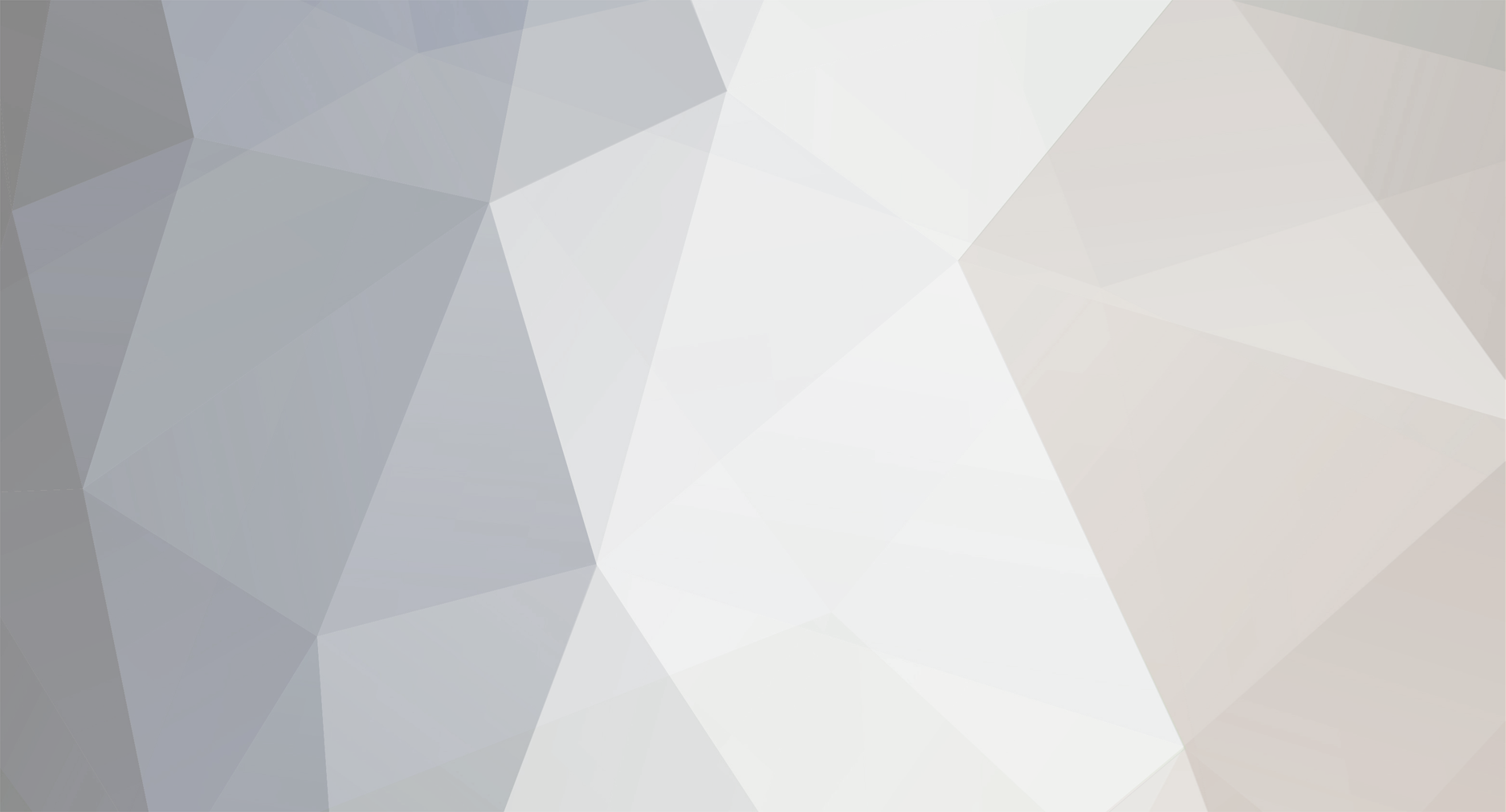
Stearman
Modelarz-
Postów
404 -
Rejestracja
-
Ostatnia wizyta
-
Wygrane w rankingu
6
Treść opublikowana przez Stearman
-
Witam po długiej przerwie ? Czas biegnie nieubłaganie, porażki uczą nas wiele, a mnie trudno zniechęcić. Wiele nauczyłem się na tym projekcie i po cichu wróciłem do początku, do tego co miało być pierwsze czyli model WILGI 35 jako trenerka łatwego w pilotażu i dającego dużo radości ze zwykłego lotu jak i z podstawowych akrobacji ? Dzisiaj, dzień po oblocie, jestem bardzo zadowolony z efektu i mimo trudności jestem bliski tego czym miał być dla mnie ten model. Tak więc prezentuję model własnej konstrukcji PZL - 104 Wilga 35A ? DANE: Rozpiętość: 1300mm Masa własna: 860g Masa do startu: 1030g Napęd: Silnik D28361120kV + 40A ESC + 3S 2200 mAh + śmigło 10x7 Konstrukcja: Zestaw STYRO, części drukowane 3D. Sterowanie: lotki, wysokość, kierunek i klapy. Model projektowałem tak by był lekki - zakładałem masę ok 1300g, dlatego na koniec jestem bardzo miło rozczarowany tak niska masą ostateczną 1030g. Projekt z uwagi na krótki dziób samolotu zakładał maksymalnie w przodzie umieszczone najcięższe elementy wyposażenia, akumulator i serwa, tak by nie dorzucać masy na dziób przy wyważeniu. I tu kolejna niespodzianka, model wyszedł bardzo dobrze jeśli chodzi o wyważenie - musiałem dodać tylko 30g ołowiu.... na samym końcu modelu bo dziób był za ciężki ? Możliwe to było dzięki zdejmowanej przedniej części kabiny, dający możliwość daleko w przodzie umieszczenia pakietu i dobremu dostępowi do reszty komponentów. Mocno ażurowa osłona silnika daje bardzo dobrą wentylację pakietu i regulatora. Przy projekcie dodałem kilka elementów utrudniających konstrukcję do testów: - możliwość regulacji kąta zaklinowania statecznika poziomego +-5 stopnia od bazy - regulacja jedna śrubą. - wyjmowane podwozie, - elementy wykonane metodą termoformowania: maska silnika, końcówki skrzydeł, - oświetlenie - leflektor na lewym skrzydle. Ogólnie nie było łatwo, ale efekt końcowy jest zadowalający... a budowa... całkiem przyjemna.... Ostatecznie wyszedł bardzo ładny model i całkiem nieźle się prezentuje Oblot.....? Niestety wczoraj przy oblocie wiało dość mocno, pilot oblatywacz mało latała w tym roku.... dopiero drugi raz na lotnisku.... ale raz kozie Duży wiatr podniósł poprzeczkę.... Jak widać na filmie z oblotu.... lot był krótki i nerwowy i z kraksą na końcu. Ustawiłem EXPO na 50% maksymalnych wychyleń, start pod wiatr ok, model bardzo słabo reagował na stery, bardzo ociężale, a jak obrócił się z wiatrem to poszedł jak dziki sam... spanikowałem by wracać na pas.... i lądowałem z wiatrem, szybko, nerwowo i na końcu model wyhamował na krzakach... ? pech... OBLOT_M1.mp4 Prawa goleń podwozia została wyłamana, ale nie odpadła. Była na tyle sprężysta, że jeszcze nadawała się do startu... Po rzeczowej, ostrej rozmowie z pilotem, postanowiłem jednak spróbować jeszcze raz.... odblokowałem stery na 100% i dopiero można było polatać. Ponieważ cały czas rył trochę dziobem w dół zmniejszyłem kat natarcia statecznika o 1 stopień i teraz było dobrze. Duży wiatr... lądowałem bez klap, nie było potrzeby. Jak w locie wypuszczałem klapy na 30 stopni to prawie zwisał przy tym wietrze.. a na 45 stopniach wiatr go zdmuchiwał OBLOT_M2_ladowania.mp4 Niestety kolejny film z lotu i "akrobacji" jest za duży.. czy jest możliwość wstawienia większego filmu tu na portalu? Podsumowując: Model lata poprawnie, łatwo wychodzi z korkociągu i ostrych beczek. Nawet przy dużym wietrze wykonuje lot odwrócony i podstawowe akrobacje. Ląduje przewidywalnie i poprawnie - dobrze reaguje na stery nawet przy małej prędkości. Przy klapach 30 pod wiatr trzyma kurs i sterowność prawie w zawisie, dopiero przy 45 przesuwa go w tył i przepada na prawe skrzydło. Widać to na filmie... jutro podzielę i w kawałkach go tu wrzucę. Dość mocna konstrukcja... sporo wytrzymała. Do poprawy: - nowe większe śmigło bo zauważalny niedostatek ciągu - 750g ciągu to za mało jak na duży wiatr i akrobacje. Zastosuje większe śmigło. - naprawienie podwozia bo z tym to da się, ale wstyd latać Jeśli kogoś interesują szczegóły budowy mogę zamieścić jakiś skrót relacji... Jutro wrzucę resztę filmów. Ogólnie jestem zadowolony i to jeszcze nie ostatnie słowo tego modelu
-
Płatowiec PZL-130 ORLIK TC-II
Stearman odpowiedział(a) na Stearman temat w Modele średniej wielkości
Bardziej przemawia do mnie wersja TC-II, bardziej nowoczesny wygląd i ta agresywność linii jakby obietnica całkiem niezłej jazdy podczas lotu... ? Może mi się taki uda zrobić, na tyle łatwy w pilotażu by dał się okiełznać średniozaawansowanemu pilotowi, ale jak przesuniesz dźwignię na pełny gaz.... to wyjdzie z niego niezły wariat A co wyjdzie... zobaczymy. Jakby co otwarty jestem na współpracę ? -
Płatowiec PZL-130 ORLIK TC-II
Stearman odpowiedział(a) na Stearman temat w Modele średniej wielkości
Dzięki Wielkie, kończę właśnie jeden z projektów i Orlik będzie następny Nie wybrałem jeszcze technologii wykonania, ale zarys już jest -
F4U Corsair, Ziroli 1800mm drukowany
Stearman odpowiedział(a) na pengo temat w Modele średniej wielkości
Posłuchaj, jeśli zdobyłeś taki materiał, to go dobrze wykorzystaj nie od razu wycinaj elementów na próbę. Optymalizuj wszystko w projekcie 3D i nie lekceważ zaoszczędzonej masy bo ona wprost przekłada się na właściwości lotne modelu Z takich "pasów" kompozytowych można sklejając na zakładkę uzyskać bardzo wytrzymały laminat o dowolnym kształcie i zbudować z niego lekki i wytrzymały "domek" na silnik lub centralny keson "W". Koledzy o większym doświadczeniu z laminatami podpowiedzą jak to zrobić. Taka "sklejka" laminatowa o grubości 3mm w postaci zamkniętego kesonu czy nawet teownika będzie o wiele mocniejsza niż rurki węglowe.... Rurki jakie dajesz na skrzydła o ściance 0,5mm przy kościach centropłatu będą bardzo słabe, w stosunkowo krótkich kawałkach szybko popękają. Użyj tego laminatu taka rada. Mogę zadać pytanie z czego drukujesz "ten zielony materiał"? Długo masz już drukarkę i projektujesz części? Pytam bo sam jestem fanem projektowania3D Nie widzę na zrzutach.... mocowanie silnika. Ma już wprowadzone kąty skłonu i wykłonu silnika (chyba tak to się nazywa)? Przeniosłeś na model 3D kąty zaklinowania skrzydła, statecznika, profil skrzydła? Wiem, że to upierdliwe sprawy, opracowanie założeń, ale zaoszczędza Ci sporo pracy później, gdy będą wymagane zmiany i korekty... Unikaj skręcania, jeśli masz zamiar coś sklejać, na śrubę zawsze potrzebny jest otwór i naddatek, który przy klejeniu niczemu nie służy i nie przenosi obciążeń. To nie do końca tak, że jak wyjdzie za ciężki model to po prostu weźmiesz mocniejszy silnik.... poleci, ale możesz być rozczarowany jego właściwościami aerodynamicznymi.... mówią, że nawet cegła poleci, ale co to za latanie Co będzie poszyciem modelu, wydruk 3D? Mówią, że piękne rzezy pięknie działają, choć może nie są oczywiste i przeczą przyjętym kanonom. Spójrz na swoją konstrukcję i jeśli Ci się podoba to będzie ok będziesz miał radochę z każdego etapu, od projektowania po oblot. -
F4U Corsair, Ziroli 1800mm drukowany
Stearman odpowiedział(a) na pengo temat w Modele średniej wielkości
Bardzo ciekawy projekt i gratuluję wyboru klasyka Jakiej średnicy rurek używasz jako główne podłużnice? (materiał, średnica i ścianka?) Fajnie, że wykonujesz modele tego co zaprojektowałeś, ale nie czujesz, po wydrukowaniu i skręceniu, że jeszcze sporo do optymalizacji tego co już masz wykonane? Strasznie dużo tych śrubek jakie stosujesz M3, M4? To co na monitorze wygląda całkiem dobrze zaprojektowane, w wykonaniu i skali okazuję się... dalekie od oczekiwania - normalne przy projektowaniu 3D. Musisz sobie zadać pytanie.... jakie uszkodzone elementy chciałbyś wymieniać? Popękane rurki? Po czym.... po krecie, gdzie popękane rurki będą najmniejszym problemem do naprawy, bo uszkodzeniu ulegnie połowa kadłuba? Taki sposób projektowania, łączenia komponentów, śrubki, mocowania, wzmocnienia będą Cię kosztowały sporo "masy", mogą okazać się nie praktyczne, a w końcowym rozrachunku trudne do realizacji, bo by wymienić jedna rurke będziesz musiał rozebrać pół modelu.... Zastanów się nad permanentnymi połączeniami klejonymi, o wiele lżejszymi i mocniejszymi. Kilka uwag, bo widzę, że masz duże zdolności i potencjał w projektowaniu, może Ci pomogą a może nie - tylko moje spostrzeżenia: Połączenie, węzeł jest tak mocny jak najsłabszy jego element... w twoim przypadku rurka... Nieważne jak masywne i mocne zrobisz mocowanie silnika, zacisk ze śrubami itd., jego najsłabszym elementem będzie będzie przekrój poprzeczny rurki gdzie kończy się zacisk, a zaczyna "swobodna" rurka. Ten przekrój (w zasadzie dwa bo są dwie rurki) z uwagi na wibracje silnika, naprężenia z lotu będzie poddawany dużym naprężeniom - szczególnie w takim układzie naprężeniom skrętnym - a tych "nie lubią" rurki węglowe, bo powodują ich rozwarstwienie i zniszczenie. Może postaraj się zwiększyć przekrój poprzeczny podpierania głównych podłużnic. Jakie mocne śruby byś nie dał i jak mocne połączenie osiągniesz "na ziemi" na sucho w powietrzu będzie ono o wiele słabsze. Bliskość silnika, temperatura i wibracje spowodują, że takie połączenie poluzuje się i rurki się wysuną... z czasem. Rurki są gładkie, nie możesz ich ścisnąć za mocno bo popękają... i tak dochodzi do tego, że najlepiej je skleić. Główne podłużnice w postaci 2 rurek tworzą płaską kratownicę, średnio odporną na zginanie, ale słabo odporną na skręcanie - a właśnie momenty skręcające będą przenoszone od silnika. Jeśli ich nie zwiążesz, nie zbudujesz przestrzennej kratownicy z co najmniej jeszcze jedna podłużnicą to cała ta konstrukcja szkieletu będzie wiotka, podatna na skręcenia przenoszone na poszycie. Długie rurki węglowe, nie podparte na długości jak "struny" przenoszą wszelkie wibracje... Bardzo fajnie wychodzą Ci elementy wycinane z kompozytu, aż się prosi by wykonać główny dźwigar "W" jako keson z kompozytu. Mocny i lekki. Kibicuje, jak będę mógł pomóc to dorzucę swoje uwagi. Sam robię Corsarza, ale o wiele mniejszego i inna techniką Dobra robota ? -
Płatowiec PZL-130 ORLIK TC-II
Stearman odpowiedział(a) na Stearman temat w Modele średniej wielkości
Racja, dlatego zdecydowałem się na własną konstrukcję. Kupiłem raz podwozie, niby do 3.5kg modelu, ale spaliła się elektryka po kilku ruchach.... pewnie miałem pecha. Projektując samemu można zaprojektować golem by chwała się z dwolonym kątem, a obudowa idealnie pasowała do użytkowania czy wzmocnień płata. Protestuje to zobaczę jak z wytrzymałością, ale wygląda obiecująco. Pomyślę jeszcze nad jakimś prostym systemem, lekkim do małych modeli. -
Płatowiec PZL-130 ORLIK TC-II
Stearman odpowiedział(a) na Stearman temat w Modele średniej wielkości
Jak na wcześniejszym filmie... Małe serwo waży niewiele, a upraszcza konstrukcję bo nie trzeba spinać bowdenem przedniego koła z serwem steru kierunku. Daje to też możliwość wyprostowania koła przedniego przed schowaniem i wyłączenie go gdy jest schowane - to będzie realizowane sterownikiem podłączonym do odbiornika. Sterownik da to możliwość kontroli skrętem przedniej goleni, wymuszenia wyprostowania koła przedniego przed schowaniem, powolne chowanie i wysuwanie podwozia, wyłączenie serw podwozia gdy podwozie jest schowane i zablokowane. -
Płatowiec PZL-130 ORLIK TC-II
Stearman odpowiedział(a) na Stearman temat w Modele średniej wielkości
Prace nad podwoziem prawie ukończone, prototyp jest i działa. Musiałem przeprojektować kształt osłon przedniego podwozia bo w pierwszej wersji były po prostu w kształcie walca, a w oryginale są bardzo obłe i ładnie komponują się z wnękami podwozia głównego. Dla zobrazowania wydrukowałem kształt jaki będzie miał kadłub w tym miejscu. Udało się wszystkie trzy golenie otwierać jednym serwem, tak jak zaplanowałem. Zmodyfikowałem prostokątne osłony podwozia głównego, bo oryginalnie otwierały się za szeroko i daleko od koła co przy trawiastym lotnisku dla modelu nie jest najlepsze. W moim rozwiązaniu są przytwierdzone na stałe do goleni. Widok bez kształtek kadłuba. Działa też całkiem dobrze Zostało teraz wprojektowanie układu w model. video-64f8b70f705d0e9e513d6c731444fa01-V.mp4 video-700c37d4dafa126d72d8e2d27c9cd55e-V.mp4 -
Płatowiec PZL-130 ORLIK TC-II
Stearman odpowiedział(a) na Stearman temat w Modele średniej wielkości
Tak wyszły pierwsze testy. Całkiem dobrze, kilka poprawek i będzie OK. Przednie podwozie skończone, teraz czas na główne. Tak się otwiera: video-9eceb7fa33739e6e5a9d06a67a900c8b-V.mp4 A tak skręca: video-80e62c4d7cf89bb36e4d37379335ff18-V.mp4 Teraz pora na zaprojektowanie podwozia głównego... ? Potem już z górki. Stanowisko testowe ? -
Płatowiec PZL-130 ORLIK TC-II
Stearman odpowiedział(a) na Stearman temat w Modele średniej wielkości
Poszedłem na łatwiznę i do testów wydrukowałem osłony na drukarce 3D. Wyszło obiecująco. Muszę dopracować jeszcze dźwignię otwierania i zamykania. Tak to ma wyglądać w teorii: Tak wychodzi otwarte: Tak zamknięte: A tak złożone, ale z otwartymi osłonami: Muszę dopracować parę szczegółów, ale już prawie jest. -
Płatowiec PZL-130 ORLIK TC-II
Stearman odpowiedział(a) na Stearman temat w Modele średniej wielkości
Będę musiał porobić kilka doświadczeń..... jak mi coś wyjdzie to się podzielę spostrzeżeniami -
Płatowiec PZL-130 ORLIK TC-II
Stearman odpowiedział(a) na Stearman temat w Modele średniej wielkości
Raczej chodziło mi o to, by po wyschnięciu balsa zachowała swój kształt po zdjęciu z "kopyta". Myślałem, że może jak po zamocowaniu balsy na kopycie dodatkowo "pomaluję" czy przesączę ją rozcieńczonym wikolem to dostanę twarda balsowa skorupę? -
Płatowiec PZL-130 ORLIK TC-II
Stearman odpowiedział(a) na Stearman temat w Modele średniej wielkości
Mam pytanie z działu techniki wykonania.... Oczywiście pracuję teraz nad podwoziem Orlika, jestem na etapie projektowania osłon przedniego koła. Chciałbym je wykonać z balsy bo mają kształt walca. Zastanawiałem się jaką techniką to zrobić, czy namoczyć balsę w wodzie aż będzie elastyczna i na kawałku rurki ułożyć ją do wyschnięcia? A może nim wyschnie to pomalować ją wikolem czy co? Chciałbym by po wyschnięciu była trwała skorupa, lekka, ale odwzorowująca kształt walca. Myślałem o sklejce 1mm grubości, a średnica na której chcę ją owinąć to 50mm. Ktoś może ma swój sposób na takie formowanie balsy? -
Ile filamentu średnio trzeba zużyć na model o wadze 1000g?
-
Piękne samoloty pięknie latają... oto dowód. ? Świetna robota ? Gratuluję! Czekamy na krajowy oblot i kolejny twój projekt ??
-
Płatowiec PZL-130 ORLIK TC-II
Stearman odpowiedział(a) na Stearman temat w Modele średniej wielkości
Dzięki Andrzej ? im prościej tym lepiej, podoba mi się to rozwiązanie. Po prawej zmodyfikowane skrzydło, chyba wygląda lepiej Wszystko jasne.... w temacie skrzydła, a jak się spisze w modelu, mam nadzieję kiedyś napisać. WIELKIE DZIĘKI PANOWIE ?? -
Płatowiec PZL-130 ORLIK TC-II
Stearman odpowiedział(a) na Stearman temat w Modele średniej wielkości
Może taki kompromis.....???? Lotki i klapy na całej długości skrzydła. Przekrój dla lotek z zaokrąglonymi krawędziami i osią obrotu w środku: Warto je zaokrąglać czy lepiej zostawić na prosto???????????????????? Przekrój dla klap: -
Płatowiec PZL-130 ORLIK TC-II
Stearman odpowiedział(a) na Stearman temat w Modele średniej wielkości
No i sobie porumakowałem ?, ale bardziej chodziło mi o klapy nie lotki. W sumie masz rację, prototyp powinien być prosty w budowie. Więc klapy cos takiego: A lotki postaram się zaokrąglić cos jak to, chyba, że nie ma sensu????? Tak właśnie było, proporcje wzięte z oryginału, ale słusznie, ten stały element skrzydła tylko utrudni konstrukcję.... odcinamy -
Płatowiec PZL-130 ORLIK TC-II
Stearman odpowiedział(a) na Stearman temat w Modele średniej wielkości
A tak wygląda skrzydło po uwzględnieniu zmian jakie zaproponowałeś Całkiem przyzwoicie. Zastanawiam się czy nie powiększyć lotek kosztem klap, czy lotki nie są za małe jak na model rc? -
Płatowiec PZL-130 ORLIK TC-II
Stearman odpowiedział(a) na Stearman temat w Modele średniej wielkości
Andrzeju, wielkie dzięki za pomoc przy aerodynamice płata, ma to sens i zastosuje je na pewno. Jako prototyp zrobię prosty model 1300mm bez fajerwerków, bez podwozia, albo ze stałym... zobaczymy jak mnie poniesie i co się zmieści Jeszcze tylko muszę wybrać rodzaj klap dla tego skrzydła bo Orlik ma skomplikowany mechanizm wysuwu klap, a ja potrzebuję zwykłe zawiasowe... tylko szczelinowe chyba typy slotted flaps? Czy są jakieś wytyczne dla wymiarów dla takiego typu klap? Czy one będą dobre dla takiego profilu skrzydła? -
Płatowiec PZL-130 ORLIK TC-II
Stearman odpowiedział(a) na Stearman temat w Modele średniej wielkości
Dzięki Wiekie, teraz sporo modelowania przede mną :), ale wiem od czego zacząć ? Powiesz dlaczego 1500mm rozpiętości? Pasowałby do twojej kolekcji? ? Nie mam tak mocnego napędu, musiałby mieć masę do startu poniżej 3kg.... ale może się uda.... -
Płatowiec PZL-130 ORLIK TC-II
Stearman odpowiedział(a) na Stearman temat w Modele średniej wielkości
Andrzej.... no teraz to mi zaimponowałeś dzięki za obliczenia i proste wytyczne językiem .... dla opornych To co napisałeś jest dość bliskie projektowi skrzydła jakie planowałem zrobić bazując na wcześniejszych wypowiedziach, ale twoje cenne uwagi zastosuję tylko musze uściślić parę detali. Najlepiej wyglądało dla mnie skrzydło jak na rysunku powyżej, dwutrapezowe + winglet o takiej konstrukcji: Jeden profil NACA 2415 dla wszystkich sekcji Sekcja pierwsza 275x161x419 zwichrzenie -2 stopnie nos profilu w dół (obrót wg końca profilu - krawędź spływu) Sekcja druga 161x136x186 zwichrzenie -1 stopień nos profilu w dół (obrót wg końca profilu - krawędź spływu) Stały wznios skrzydła +6 stopni Kąt zaklinowania skrzydła 0 stopni Kąt zaklinowania statecznika poziomego 0 stopni. ?????????????????????????????????? Czy dobrze rozumiem, jeśli chciałbym wprowadzić twoje sugestie to wtedy skrzydło powinno mieć konstrukcję: Profil sekcji pierwszej: nasada - NACA 2415 (275) końcówka NACA 2415 (161), zwichrzenie - 2 stopnie w dół. Profil sekcji drugiej: NACA 2415 (161) końcówka NACA 3412 (136), zwichrzenie - 1 stopień w dół. Stały wznios skrzydła +6 stopni Kąt zaklinowania skrzydła +2 stopnie Kąt zaklinowania statecznika poziomego 0 stopni. ????????????????????????????? Projekt jest otwarty.... Jaka twoim zdaniem rozpiętość byłaby odpowiednia? ? -
Płatowiec PZL-130 ORLIK TC-II
Stearman odpowiedział(a) na Stearman temat w Modele średniej wielkości
Jurku - z moim małym doświadczeniem w 100% się z Tobą zgadzam.... Liczę jednak, że nie rozpętasz wojny (bo nie rozważamy tu wysublimowanych konstrukcji szybowców o idealnej konstrukcji i profilach, a modele codziennego użytku) a szybko dojdziemy do konkluzji... w postaci kilku rad, na czym się skupić projektując własny model samolotu. Co liczyć a co nie? Tak z twojego doświadczenia? : -
Tak trzymaj ? i do przodu! Czekam z niecierpliwością kiedy zobaczę go na rodzimym lotnisku ? i radochę jaką będziesz miał z oblotu ???
-
Już zaczynałem się martwić co tak zamilkłeś , ale cisza czasami mocniejsza jest niż tysiąc słów, a mi teraz cisną się na usta tylko dwa.. ŚWIETNA ROBOTA!!!!!!! ????? Z niecierpliwością czekam na dalszy rozwój projektu, bo znam Ciebie.. i po prostu wiem, że to nie koniec ??