
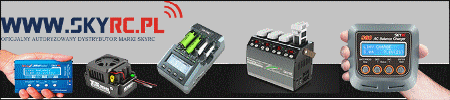
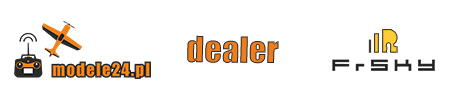
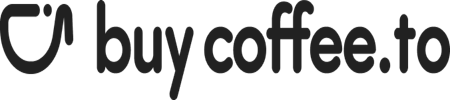
-
Postów
370 -
Rejestracja
-
Ostatnia wizyta
-
Wygrane w rankingu
2
Treść opublikowana przez TKC
-
wspomniana przeze mnie Technoline BC700 ma taką możliwość - od 1 do 4 paluszków (AA lub AAA) standardowo prąd ładowania 200mA ale można więcej, poza tym możesz wybrane ogniwa ładować inne rozładowywać itp. rzuć okiem na opis w sieci. Pozdrawiam Tomasz
-
Miałem ten sam problem, finalnie zainwestowałem w dwie ładowarki Technoline BC700 i wreszcie problem się rozwiązał . Pozdrawiam Tomasz
-
<usunięte przez autora -> przez wydzielenie wątków rozbita została logika/ciągłość wypowiedzi.>
-
<usunięte przez autora - przez wydzielenie wątków rozbita została logika/ciągłość wypowiedzi>.
-
garść fotek po zmianie kolorystyki, montażu serw i otwarciu drogi powietrzu chłodzącemu kadłub: - góra modelu -dół modelu -wylot powietrza chłodzącego wnętrze kadłuba (drugi jest umieszczony symetrycznie po lewej stronie) - "kroplowa" osłona serwa wysokości + przeniesienie napędu - serwa lotek + popychacze cdn... pozdrawiam Tomasz
-
Patryk, zerknij tutaj może to coś to pomoże, co prawda więcej roboty ale balon robiony na wymiar...
-
Miło, że mój wybór się komuś podoba - model jest tak pokraczny i nietypowy, że aż przypadł mi do gustu - grunt to mieć odpowiedni gust . A skoro już się odzywam , to pozwolę sobie również dorzucić fotki z moich wczorajszych zmagań z nosem modelu . Pozdrawiam Tomasz
-
Ostatni tydzień nie był zbyt udany - musiałem ogłosić w mieszkaniu kwarantannę. Jakieś <piiiiii...> zaatakowało cała rodzinkę... temperatura od 38 do 39.5C u wszystkich domowników ... do dziś nie bardzo mam siłę się ruszać... Z tego też powodu, w temacie Radiusa nic się nie działo... Jednak dziś, w ramach rozruchu i dalszego siedzenia w mieszkaniu, postanowiłem troche podłubać, choć muszę przyznać bardzo ciężko szło - ledwo wkleiłem i obrobiłem krawędzie spływu z balsy, wykonałem z "bachy alu" stateczniki pionowe i okleiłem ster wysokości. W zeszły weekend, zanim mnie rozłożyło, udało mi się jeszcze zalaminować pierwszy stopień KFM (szkło 25/m2) i wzmocnić natarcie paskiem 50-tki. 25-tka poszła zarówno od góry jak i dołu skrzydła. Na dole wywinąłem ją na całą wysokość kadłuba. Mam zamiar jeszcze zalaminować całą skrzynkę kadłuba jedną warstwą 50-tki, aby po pierwszych lądowaniach nie trzeba było remontować kadłuba - wszak latam na łące gdzie czasem trafiają się jakieś kretowiska, górki dołki itp. Poniżej dwie fotki z postępu prac: Pozdrawiam Tomasz
-
lukasto jeśli to jest sterownik z postu SRB: To według opisu na stronie niestety nie będzie działał: "... NOTE: - This driver board is controlled by USB port, can only use with the CNC software special designed for this board. It can't be used with MACH3, KCAM4 or other CNC softwares. ..." Jesteś chyba skazany na software dostarczony ze sterwonikiem - jak dla mnie to duża wada. Pozdrawiam Tomasz
-
Cześć! Zrobiłeś już drugą próbę? Jaki rezultat? Jaka metoda ? Dużo pytań jednak bardzo mnie ciekawi czy i jak udało Ci się zatrzymać odpowiednią ilość żywicy w tkaninie. Miałem podobny problem zarówno przy "desce" węglowej jak i szkle (podwozie). Przesadziłem z odebraniem laminatowi żywicy - wstępnie odsączyłem (odcisąłem wałkiem stalowym przez papier toaletowy) kompozyt, dałem delaminaż na to dwie warstwy ręczników papierowych następnie wrzuciłem kanapkę do worka, oddessałem na max powietrze (pompą z agregatu) na koniec podgrzałem wszystko suszarką i finalnie okazało się że laminat wyszedł zbyt suchy - w przypadku szkła wyglądało to tak jakby warstwy tkanin kiepsko się trzymały siebie - przy przełamanym elemencie można było odrywać warstę tkaniny za warstwą - obierać prawie jak cebulę. W węglu wyglądało to tak jakby w środku kompozyt był niedostatecznie przesączony (choć tutaj nie jestem na 100% pewien czy go poprawnie przesączyłem, ale raczej tak- poszczególne warstwy ~120'ki jednokierunkowej przesączałem z 2 stron i jeszcze porządnie każdą warstwę przewałkowałem). Pozdrawiam Tomasz
-
Tak, wiem , tylko że chcę się pobawić w wychylenia różnicowe a może i coś więcej pokombinować . Pozdrawiam Tomasz
-
Witam Jako, że od ponad miesiąca nie mam serca do babrania się w żywicy i tkaninach, stwierdziłem, iż w ramach przerywnika w projekcie mojego COS-2 trzeba coś zbudować "na szybko", bez większego zastanawiania się co i jak. Z tego też powodu włóczyłem się po czeluściach modelaskiego internetu w poszukiwaniu natchnienia i ponownie trafiłem na niemiecką stronkę modell-aviator.de . Już raz zbudowałem model - Nieuport IV wykorzystując plany zamieszczone na tym portalu i pomyślałem że coś powinno się tam dla mnie znaleźć. I nie zawiodłem się - znalazłem plany modelu Radius - plany znajdują się na stronie opisu modelu - z prawej strony ekranu (wersja mini - rozpiętość 400mm oraz większa wersja - rozpiętość ~550mm ) a tutaj filmy z lotów (projektanta modelu): -> wersją mini http://youtu.be/hZoTLoyWAeg -> i większą wersją http://youtu.be/dCFUruqCpIM Zainspirowany przedstawionymi na filmach możliwościami modelu postanowiłem, że budowa większej wersji będzie moim przerywnikiem w pracach nad innymi projektami. Co chcę włożyć do środka? - Praktycznie kopia wyposażenia, które już się sprawdziło w moim pylonie s(f)lipso400 , zastosuję tylko inny regulator. czyli: Silnik: Turnigy 2830-3500 Śmigło: APC 4.7x4.7 Pakiet: 2s Ray 1600mAh, 25C Regulator Foxy 35A Serwa: Hitec HS55 - 2 - lotki + 1 - ster wysokości. Odbiornik: Jedi Rex 5MPD Ze względu na fakt, iż w/w silnik jest silnikiem przeznacznonym do śmigłowców nie ma on w prosty sposób możliwości montażu przed wręgą - z tego też powodu musiałem zmodyfikować oryginalny projekt i "dostrugać" odpowiedni domek. Dodałem również dźwigar z listewki 5x5mm oraz zamierzam zastosować 3 serwa zamiast 2. Poniżej kilka zdjęć z aktualnego stanu prac. - > z góry (lotki i ster wysokości zostały przyklejone tyczmczasowo taśmą) -> z dołu -> zbliżenie na domek i mocowanie silnika -> jeszcze surowe stateczniki pionowe CDN Pozdrawiam Tomasz
-
SRB to nie wina sprzęgła, pisk silnika i jego zatrzymanie to oznaka, że pogubił kroki. Na forum CNC info, polecają zwykle sprzęgła kłowe - te z wkładką polimerową. Napięcie znamionowe silników równe lub większe od napięcia podawanego ze sterownika - > kiepska dynamika Ja na przykład mam silniki Un=1.76V In=2A a zasilam je ze sterownika, który jest zasilany z 24V (oczywiście prąd w sterowniku jest ograniczony do wartości poniżej 2A, chyba 1.75A). Oczywiście można by było silniki zasilać z niższego napięcia jednak w w/w konfiguracji krzywa narastania prądu (dI/dt) w silniku jest bardziej stroma niż przy zasilaniu niższym napięciem - silnik szybciej osiąga swój maksymalny moment i szybciej się obróci o zadany krok - czyli można go szybciej "taktować". Za regulację prądu (i jego maksymalnej wartości ) jest opowiedzialny sterownik i w trakcie normalnej pracy nie dopuści on do przepływu zbyt dużego prądu = przegrzania i spalenia uzwojeń silnika. Myślę więc, że i tutaj jest pies pogrzebany - uzyskane wolne przebiegi i gubienie kroków przy szybszym taktowaniu. Pozdrawiam Tomasz edit: taka uwaga, zauważyłem, że sterownik z w/w linków ma w opisie 15kHz - cokolwiek autor miał na myśli . Np. Mach 3 pozwala w wersji testowej pracować z częstotliwością jądra 25kHz. Aby się nie okazało w przyszłości, że to też wąskie gardło np. przy pracy z mikrokokiem - kika obliczeń dla mikrokroku 1/16: -> 200 kroków silnika na obrót * 16 (max mikrokrok) =3200 impulsów na obrót silnika. -> biorąc za dobrą monetę 15kHz jako max częstotliwość taktowania jednego silnika -> max prędkość obrotowa: 15000/3200=4.6875 obrotu na sekundę. 4.6875 *60 s = 281.25 obrotu na minutę. Zakładając skok śruby 1.25mm (dla zwykłego gwintu M8) daje nam to ~351 mm/minutę. Przeskalowując dla innych ustawień mikrokroku uzyskamy inne maksymalne prędkości posuwu wynikające z częstotliwości pracy samego sterownika. ufff... mam nadzieję że nigdzie się nie machnąłem się w rachunkach.
-
Piszczenie silnika to gubienie przez niego kroków - spróbuj zmniejszyć prędkość posuwu i/lub spróbuj jak będzie pracował z wyłączonym mikrokrokiem (u mnie silniki z wyłączonym mikrokrokiem pracowały jak traktory ) Gdy uda Ci się otrzymać stabilną pracę przy komendzie G0, spróbuj włączyć mikrokrok i po kolei go zwiększać od 1:2 w górę (aż ustawienie cię zadowoli) sprawdzając po każdej zmianie czy silnik nie gubi kroków przy G0. Jeśli silnik gubi kroki , to trzeba albo wrócić do niższego podziału, albo zmniejszyć prędkość posuwu. Pamiętaj aby po każdej zmianie ustawienia mikrokroku modyfikować ustawienia dla maksymalnej prędkość posuwu - aby prędkość była stała należy uwzględnić ziększoną liczbę kroków wprowadzaną przez ustawienie mikrokroku. Przy okazji sprawdź jak masz ustawione "ładowanie" - decay mode dla sterownika ja bym zaczął od ustawienia go na normal. Stosowanie śruby metrycznej (pręta gwinowanego) to "zło", z którym można (przez pewien czas) żyć zakładając okazyjne prace na maszynie i godząc się na ograniczenia (znając je) takiego rozwiązania. Pozdrawiam Tomasz
-
jak luzów nie ma to przychodzą mi do głowy jeszcze następujące elementy: - niedokładność wykonania śruby - software (z tego co pamiętam używasz jakiegoś dodawanego do sterownika) - silnik(edit) gubi kroki (raczej byś to słyszał). Skalibruj oś na najdłuszym możliwym odcinku a potem sprawdź w kilku przejazdach czy pozycjonowanie na "0" i max jest powtarzalne. Pozdrawiam Tomasz
-
klasa F5D czy ktoś lata?
TKC odpowiedział(a) na jaciomp temat w Imprezy szybowcowe - miejsca do latania
Będziesz latał na Pałacowej , czy może masz na oku jakąś inną, roleglejszą i mniej uczęszczną (bezpieczniejszą dla otoczenia) miejscówkę? Pytam, ponieważ latanie pylonem na Pałacowej zawsze mnie nadmiernie stresuje - także mój Slipso raczej zbiera kurz niż lata. Pozdrawiam Tomasz -
Dzięki za wyjaśnienie. Nigdy nie brałem pod uwagę "rozcięcia" zwykłej podkładki sprężystej jako elementu haczącego się o nakrętkę i materiał... widocznie podkładki, które najczęściej posiadałem były dość podłej jakości i nie zwróciłem na to uwagi. Gdy była potrzeba lepszej odporności na rozkręcanie (biorąc pod uwagę drgania) to stosowałem inne rozwiązania lub dublowałem zabezpieczenia (np podkładki+klej). Wiem, że podkładka sprężysta opierając się, nie o element, tylko o zwykłą podkładkę będzie próbowała ją "ruszyć". Jednak zawsze zakładałem, że tracie między elementem skręcanym a zwykłą podkładką (która dość często jest przeze mnie stosowana w wersji powiększonej aby rozłożyć siłę docisku na większą powierzchnię ) jest wystarczające by temu zapobiec, a wtedy podkładka sprężysta wykona poprawnie swoją robotę. - Pamiętajmy, iż większość połączeń skręcanych w naszym amatorskim światku nie jest liczone i z tego powodu jest zwykle znacznie przewymiarowane. Ok, ale co w wypadku materiałów takich jak stopy alumnium, które mają tendencję do płynięcia... Mówię tutaj o przypadku gdy musimy rozłożyć nacisk aby nie odkształcić plastycznie (uszkodzić) elementów skręcanych a dodatkowo musimy zabezpieczyć się przed poluzowaniem złącza, spowodowanego w/w zjawiskiem. Tutaj sam klej nie załatwi sprawy, to samo dotyczy kontrnakrętki czy nakrętki samkontrującej się. Możesz dla takiego przypadku zaproponować jakieś rozwiązanie? Ja w tym przypadku stosuję - odpowiednio powiększoną podkładkę zwykłą -> rozłożenie nacisku na większą powierzchnię; - podkładkę sprężystą -> eliminacja "luzów " na łączeniu, spowodowanych płynięciem materiału; - klej do gwintów między śubę i nakrętkę - zabezpieczenie przed poluzowaniem się nakrętki na śrubie (można też dać kropelkę miedzy element a podkładkę zwykłą - będzie pancerne ); Może to rozwiązanie nie jest do końca zgodne ze sztuką, albo jest zbyt nadmiarowe/przekombinowane, jednak jak do tej pory mnie nie zwiodło . Jeśli znacie jakieś inne rozwiązania to chętnie je rozważę i koniec OT bo naprawdę mnie pogonią Pozdrawiam Tomasz
-
lukasto, nie pisałem mojego posta z sugestią, abyś coś zmieniał , tylko ciekawy jestem powodów odmienności zdania kolegów - może czegoś się nauczę Pozdrawiam
-
Nie chcę się z nikim sprzeczać jednak ja zwykle stosowałem dwie podkładki: zwykłą (ochrona skręcanego elementu, rozłożenie nacisku na większa powierzchnię), na nią sprężystą (przecięty i rozchylony pierścień- DIN 127) i na to nakrętkę - może to rozwiązanie jest nie do końca poprawne ale jak na przykład skręcić mocno dwa elementy drewniane lub z innego miękkiego materiału, tak aby śruba czy nakrętka nie zagłębiła się w materiał i dodatkowo zabezpieczyć połączenie w takim wypadku przed rozkręcaniem się (wiem można zastosować inne rozwiązanie - przecinakrętkę, lub np nakrętkę koronkową)? W/w podkładka sprężysta zabezpiecza przez osiowo działające siły sprężystości - w płaszczyźnie nakrętki. Jeśli stosowałem podkładkę sprężystą, ząbkowana (np DIN 6797) wtedy faktycznie na skręcany element podkładka sprężysta ząbkowana i nakrętka - w tym przypadku podkładka odkształcała się (osiowo działające siły sprężystości) i dodatkowo wbijała się w materiał i nakrętkę dodatkowo uniemożliwiając ruch "odkręcający" nakrętkę- czyli w płaszczyźnie nakrętki). @Bubu & Wapniak - Mogę poprosić o szersze uzasadnienie niż lakoniczne stwierdzenie "nie bo nie" Pozdrawiam Tomasz
-
.... zanim dojdziemy do odprężania konstrukcji stalowej i faktu ze sama konstrukcja stalowa ma za małe przekroje, albo do kosntrukcji z betonu, moze epoxy -betonu czy innych wynalazków, które faktycznie poprawjają sztywność, dokładność itd... zwróćmy uwagę co jest celem projektu. Jak zrozumiałem, jest to prosta, tania maszyna, która jest możliwa do wykonania przy zastosowaniu minimalnego parku maszynowego, bez większych wymagań dotyczących precyzji czy prędkości pracy... Pozdrawiam Tomasz
-
Myślę, że wzieło się z mojego postu : "To rozwiązanie, moim zdaniem, w tym konkretnym przypadku jest lepsze ze względu na mniejsze "odchudzenie" profiu na samym środku jego rozpiętości." - Dwa otwory na śrubokręt to mniejszy ubytek matreiału z profilu niż przy wykonanych slotach pod klucz. Fakt, zastosowane rozwiązanie jest tańsze i zwykle łatwiej dostępne. Jendak dobrej jakości śruby i klucze imbusowe pozwalają w zadowalającym stopniu wykonać wytrzymałe połączenie śrubowe. Jeżeli chcesz "kleić" to sugeruję odpowiedni klej do gwintów (np firmy Loctite) (...chociaż sam, czasem, stosuję lakier nitro. Używam go zwykle w sytuacji gdy trzeba coś na szybko zabezpieczyć, a utrzymanie połączenia, czy raczej możliwość jego demontażu, nie jest krytyczna) I jeśli już zabezpieczać klejem to nie po dokręceniu nakrętki, tylko w trakcie (czyli odtłuszczona śruba i nakrętka, kropelka kleju na gwint i dopiero skręcamy (zwykle są to kleje anaerobowe czyli utwardzające się po odcięciu dopływu powietrza)- technologia klejenia powinna być gdzieś opisana na stronie producenta) Poza tym jak już mówił YaneQopter, śruby po "sklejeniu" i tak mogą się poluzować - aluminium ma tą paskudną cechę, że "lubi" popłynąć pod obciążeniem, a wtedy pojawia się minimalny luz (ponieważ nie będzie niczego co będzie zapewniało docisk a klej tylko utrzyma nakrętkę na miejscu) i już z górki . Natomiast najprostsza i najtańsza podkładka sprężysta powinna zapewnć wymagany docisk i zabezpieczć połączenie. Pozdrawiam Tomasz
-
Dość duże wyszły te otwory dające dostęp do nakrętek ... W projekcie sugerowane były śruby z główkami PH (philipsa) i odpowiednie otwory przez zewnętrzną/boczną ściankę profilu (zrobione tak by dostać się śrubokrętem, ale nie wchodzące na ścieżkę/bieżnię po której mają się poruszać łożyska wózka -uwagi na na rysunku i zdjęcie 29 z albumu). To rozwiązanie, moim zdaniem, w tym konkretnym przypadku jest lepsze ze względu na mniejsze "odchudzenie" profiu na samym środku jego rozpiętości. Można by było ewentualnie zastanowić się nad zamianą śrub PH na imbusowe, ale to w przypadku gdyby była obawa, że śrub z główką PH nie da się wystarczająco mocno przytrzymać śrubokrętem i skręcić. To takie moje małe luźne przemyślenia, ponieważ otwory już są i przecież nie będziesz ich łatał . Co mogę jeszcze zasugerować to stosowanie podkładek sprężystych - po co masz się w przyszłości denerować, że coś, co raz ustawiłeś, rozjeżdża Ci się tylko dlatego, że nakrętki się poluzowały (np. od wibracji albo ze względu na to że "aluminiowy" profil popłynął pod nakrętką). Pozdrawiam Tomasz
-
Troche OT ale może za "dwa słowa" w odpowiedzi na Twoje pytania autor wątku mnie nie przegoni - są 4 niezależne osie: X,(lewa pozioma), Y (lewa pionowa), A (prawa pozioma) i B (prawa pionowa) - jeszcze testuję Mach'a 3, ale przymierzam się do linux cnc - przy wolnych przebiegach faktycznie trochę wszystko gra jednak przy powieszeniu mokrych kawałeczków reczników na końcach drutu do cięcia, nie ma problemu z drganiami i dokładnością (tzn większe są problemy z poprawnym ustawieniem rzazu niż wpływ pojawiających się rezeonansów). .Zresztą jak posłuchasz filmów z cięciem ploterem innych konstruktorów to w większości wypadków też gdzieś maszyna zagra.. ten typ tak ma (wiotkie, lekkie itd...) Jeśli miałbyś ochotę więcej porozmwiać na temat wycinarki to zapraszam do wspomnianego wątku - nie róbmy koledze bałaganu w jego relacji. @lukasto, sorry za OT. Pozdrawiam Tomasz
-
przejrzałem ten temat... - jak autor pisze finalnym krokiem jest przygotowanie planów pod laser... - celem jest otrzymanie tak zwanego tartaku - czyli laser/frezarka (czy water jet jeśli ktoś by chciał to ciąć z metalu za pomocą wody) jest traktowany jak zautomatyzowana piłka włosowa - > wycinanie z desek balsy czy sklejki kształtów 2D i składaniu ich jak puzle 3D w naszym świecie 3D jako bryły. Jeżeli takie są Twoje potrzeby to faktycznie jest dość sporo możliwości zaprojekowania modelu i jego wycięcia. Jeśli jednak chciłbyś sięgnąć dalej i np.: tak jak to jest pokazane w temacie Virgos F3K, w poście otwierającym wątek , gdzie na zdjęciach jest przedstawione frezowanie kopyta skrzydła (bryła 3D) do zdjęcia z niego formy, to wszystko się trochę komplikuje. Zawsze jednak można znaleść jakieś rozwiązanie (BTW jestem właśnie na etapie jego poszukiwania). Wracając do tematu samej frezarki to kibicuję Ci i jestem bardzo ciekawy efektów pierwszych cięć. Pamiętaj, iż zdobytego doświadczenia nic nie zastąpi. Ja, na początku prac koncepcyjnych, chciałem budować frezarkę najpierw na prowadnicach szufladowych, potem na łożyskach, rurkach itd.. jednak po doświadczeniach z moim ploterkiem do pianki oraz lekturze forum cnc.info.pl (tylko nie należy dać się zwariować ), postanowiłem, że jak już będę działał w temacie frezarki to raczej oprę się na wałkach (celuję w podparte 20'tki) , łożyskach liniowych i śrubach trapezowych... i tak dochodzimy od drewniaka na prowadnicach szufladowych do urządzenia trochę bardziej "profi" Pozdrawiam Tomasz