
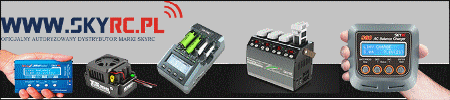
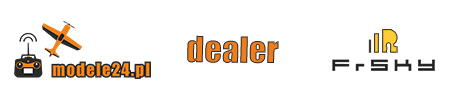
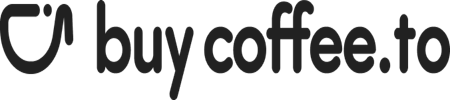
-
Postów
4 363 -
Rejestracja
-
Ostatnia wizyta
-
Wygrane w rankingu
48
Treść opublikowana przez RomanJ4
-
A nie masz drogi Marku czegoś tam do naprawy, co dało by się wytoczyć, przetoczyć? Jeśli nie, to może potrenuj sobie nacinanie gwintów na jakim kawałku kolorowego czy nawet drewnianego wałka, ostatnio opisałem co i jak krok po kroku więc powinno być łatwiej.... P.S. Pasowanie pod łożyska bez mikrometru to loteria, +3μm nad nominalny dla małego łożyska to już za ciasno, a -1μm pod to już lata... Chyba, że nasz Kolega mikrometr posiada...
-
Na pewno koledzy zauważyli, że gwint nacinany tylko na części wałka o jednolitej średnicy (rys.1c) ma wyjście z materiału dla ostrza noża w postaci podcięcia o średnicy równej lub mniejszej od śr. d3 gwintu. Podobne wyjście stosujemy przy nacinaniu gwintu na stopniu wałka o mniejszej średnicy (rys.2b), oraz nacinając gwint lewozwojny, dla ustawienia głębokości skrawania i wprowadzenia ostrza w materiał. Dlatego, że manualnie nie jesteśmy w stanie nawet stosując najniższe obroty, w kolejnych przejściach noża zawsze idealnie w tym samym punkcie wyprowadzić ostrze z materiału.. Bez tego podcięcia, zwłaszcza nacinając gwint o dużym (głębokim) skoku, przy ostatnich przejściach moglibyśmy nieopatrznie wjechać ostrzem w cały niegwintowany materiał, co przeważnie skutkuje złamaniem noża. Także wewnętrzne gwinty nieprzelotowe oraz lewozwojne nacinane nożem muszą mieć wybieg. Podcięcia nie robimy dla nacięcia gwintu na części wałka o większej średnicy (rys.1b), oraz przy gwintowaniu narzynką (rys.1a, 2a). Możemy tez zaryzykować przy nacinaniu niezbyt grubych gwintów w materiałach o małej wytrzymałości - miękkich, Sam proces nacinania i kolejne czynności operatora prześledzimy na przykładzie nacinania gwintu zewnętrznego prawego, pomocny w tym będzie poprzedni rysunek Po wybraniu i zainstalowaniu odpowiednich dla danego skoku kół gitary, ewentualnym nastawieniu przełożenia skrzynki prędkości, właściwego kierunku obrotów śruby pociągowej (nawrotnicą), i ustawieniu osi noża do powierzchni materiału ustawiamy sobie jeszcze wskaźnik skali sanek narzędziowych na "0", (raczej ich przestawianie przy nacinaniu nie będzie nam potrzebne, ale nigdy nic nie wiadomo), i sprawdzamy czy nóż ma dość miejsca na bezpieczne wyjście z gwintu, czy nie wjedzie nam w materiał bądź uchwyt, bo pamiętać musimy że wrzeciono (i napęd) też mają pewną bezwładność, i najczęściej w miejscu nam nie stanie. (gwinty które muszą dochodzić do ścianki stopnia należy robić narzynką lub wykończyć nią dociągając gwint do końca) Potem włączamy obroty, podjeżdżamy nożem pod materiał dostawiając go wierzchołkiem, i w tym położeniu ustawiamy skalę pokrętła sań poprzecznych na "0", i staramy się tego nastawienia bębenka skali na pokrętle potem nie zmieniać(ważne!). Będzie to nasza baza do kontroli przybierania głębokości nacinania za każdym przejściem noża, oraz pokazywania sumarycznej głębokości zarysu nacinanego gwintu h3 (lub H). Musimy oczywiście przy tym pamiętać czy skala na pokrętle sań poprzecznych naszej tokarki pokazuje nam wielkość przyrostu po promieniu r, czy po średnicy D jak na zdjęciu poniżej (jeśli średnicy, to do ustalenia aktualnej głębokości h3 naszego gwintu wskazania trzeba oczywiście mnożyć razy dwa) wycofujemy nóż przed początek materiału, nastawiamy głębokość pierwszego przejścia na nasze "0" + 0,1-0,15mm, by tylko zarysować powierzchnię materiału, włączamy obroty wrzeciona, dźwignią załączamy na suporcie zamek śruby pociągowej, i nacinamy gwint aż do momentu wyjścia noża z materiału. W momencie wyjścia ostrza z gwintu w przestrzeń wybiegu na końcu nacinanej powierzchni, musimy jednocześnie wykonać dwie czynności: - jedną ręką kręcąc korbką sań poprzecznych odsunąć nóż od materiału, - a druga przełączyć obroty wrzeciona na lewe (przełącznikiem kierunku obrotów silnika) by nóż nam nie wpadł w materiał czy szczęki. Albo tylko chwilowo zatrzymać. Wymaga to pewnej wprawy, dla której nabrania polecałbym kolegom dopiero uczącym się nacinać gwinty zastosować jak najniższe obroty wrzeciona, dając tym samym wystarczająco dużo czasu na reakcję, raz potrenować sobie na przygotowanym wałku z dość szerokim wybiegiem na początek, np z aluminium (albo nawet z twardego drewna, byle nie za długim). Niezbędnych odruchów szybko się nabiera, więc nie powinno to sprawić trudności zwłaszcza modelarzom nawykłym do zsynchronizowanej obsługi drążków aparatur. Na lewych obrotach wycofujemy nóż aż na początek naszego gwintu, zatrzymujemy obroty, i nastawiamy nową głębokość nacinania w drugim przejściu (np "0" + 0,3mm) Zanim rozpoczniemy drugie przejście koniecznie sprawdźmy czy nasze ustawienia tokarki były prawidłowe ! Najlepiej grzebieniem do gwintów, albo jeśli takowego nie mamy to dla większej dokładności można zmierzyć suwmiarką długość np 10 zwojów zarysowanego gwintu, i podzielić wymiar na 10, Następne przejścia wykonujemy analogicznie, aż do nacięcia pełnego zarysu. Po wykonaniu ostatniego nacinającego już pełną głębokość można wykonać jeszcze jedno dodatkowe przejście wygładzające, tym samym wymiarem. Przy nacinaniu smarujemy olejem lnianym lub preparatami do gwintowania/wiercenia, ostatecznie nawet emulsją chłodzącą lub jakimkolwiek olejem. Proces nacinania możemy poobserwować na filmie, (choć takie zatrzymanie noża w materiale jak to widać w 0:58; 1:11; 1:20 minucie grozi wyszczerbieniem lub złamaniem ostrza, dlatego starajmy się zatrzymywać/przełączać obroty wrzeciona już po wyjściu noża z materiału). A jeśli już nam się podobnie zatrzyma przed wyjściem z materiału, to przy nacinaniu małych gwintów powinniśmy ostrożnie dociąć obracając wrzeciono ręcznie podobnie jak na filmie. Przy grubych gwintach możemy nie dać rady ręcznie dociąć, więc musimy (też ręcznie) cofnąć nieco obroty, obracając wrzeciono w przeciwna stronę by odsunąć od ostrza nawarstwiony na nim wiór, i dopiero wtedy odsunąć nóż od materiału cofając do siebie (oczywiście nie rozłączamy w tym czasie zamka śruby), cofnąć go na lewych obrotach na początek gwintu, i przejechać jeszcze raz z tym samym wymiarem. Widać też dlaczego naukę należy zaczynać na bardzo małych obrotach - bo mało jest miejsca na wyjście noża. a na tym filmie (jednego z kolegów z forum http://www.cnc.info.pl) mogą koledzy zobaczyć jakiego refleksu trzeba przy nacinaniu na szybkich obrotach wrzeciona, nawet przy szerokim wybiegu z gwintu (przy okazji różnica w nacinaniu na sucho i z olejem). Dlatego zalecam zaczynać naukę na bardzo wolnych... http://www.youtube.com/watch?v=cJM8s8SP5HY cdn...
-
Faktycznie cool chłopaki, często te siadające na dzwoneczki pozwalały się brać na dłoń. Ale szkoda, że nie widzieliście mojego ojca jak mu jeden taki zawodnik latem wpadł pod koszulę kiedy motorem z pracy wracał... Schwarzenegger przy nim wyglądałby jak cienias... Niemniej ciekawe zajęcie, pożyteczne, i sąsiedzi chwalą... a i przyjemnie posłuchać jak w nagrzanym słońcem ogrodzie coś buczy...
-
Macie koledzy na myśli pszczółki? Bardzo pożyteczne, ale i odpowiedzialne zajęcie.. A własnej marki "przepalanka" jaka dobra... cymes! (mój ś.p. teść był pszczelarzem na 46 uli, to się co nieco tego botoxu zażyło..)
-
A jak to wygląda w tokarkach ze skrzynkami posuwów między przekładnią gitary a śrubą pociągową. Weźmy tu na tapetę popularne u nas chińskiej produkcji tokarki sprzedawane przez różnych dystrybutorów pod różnymi nazwami (Bernardo, Holzmann, Hafen, itd), w takich tokarkach oprócz skompletowania zgodnych z tabela kół gitary należy jeszcze nastawić właściwe pokrętło skrzynki posuwów na wartość wskazaną przez tabelę podobnie w bardzo popularnych w USA tokarkach ze skrzynką Nortona zamiast klasycznej skrzynki posuwów, gdzie napęd od gitary przekazywany jest przez koło pośrednie znajdujące się w przesuwnej dźwigni na zespól położonych rzędem obok siebie stopniowanych kół zębatych, i dalej na śrubę pociągową. tu mamy tabelę ustawiania posuwów i skoków gwintów tokarki Grizzly ze skrzynką Nortona (bez odboczki) Niektóre skrzynki Nortona posiadaja zintegrowaną z nimi odboczkę (ABCDE) redukująco/multiplikującą (1:2/1:1/2:1) obroty wałka pośredniego (atakującego) przekładni, lub nawrotnicę (z osobnymi dźwigniami) Mam nadzieję, że nie jest to już dla kolegów taka czarna magia jak mogło by się komu wydawać. I proszę pamiętajcie koledzy o dobrej praktyce by zawsze sprawdzić poprawność ustawienia skoku, zarysowując tylko powierzchnię materiału w pierwszym przejściu noża. Najlepiej użyć do tego grzebienia do gwintów. Bo znając prawo Murphy'ego pomyłki się zdarzają, i zaoszczędzimy sobie nieraz wiele pracy z dorabianiem detalu na nowo a po nacięciu sprawdzamy głębokość jeśli trzeba. Głębokość h3 nacinanego gwintu metrycznego(60°) dla danego skoku jaką mamy naciąć nożem, możemy obliczyć według danych z dostępnych tablic gwintów, odejmując od średnicy zewnętrznej d średnicę dna gwintu d3 i dzieląc przez dwa https://www.google.pl/url?sa=t&rct=j&q=&esrc=s&source=web&cd=12&cad=rja&uact=8&ved=0ahUKEwjohsLdwc3LAhUsKpoKHbL6A54QFghXMAs&url=http%3A%2F%2Fwww.pg.gda.pl%2F~wlitwin%2Fpkm%2F3_gwinty%2520metryczne.pdf&usg=AFQjCNHrYNlfqlBiREoBmavopcEQ5S0X4A&bvm=bv.117218890,d.bGs h3 = (d - d3):2 lub prościej ze skoku gwintu P h3 = (P:2)•1,24 lub wprost h3 = 0,6134P H = 0,8660P - pełny zarys gwintu a sugerowaną liczbę przejść noża dla nacięcia pełnego gwintu metodą promieniową (prostopadle do osi toczenia) podaje poniższa tabela, Dla wygody kolegów zamieszczam podręczne tabele wymiarów, głębokości nacinania gwintów o różnych zarysach, oraz otworów pod typowe zarysy gwintów (w mm) które można stosować też do nacinania nożem.(powiększenia rysunków pod linkiem) http://www.e-darmet.pl/typowe-zarysy-i-parametry-gwintu-srednice-otworow-pod-gwintowanie-cid-40.html W praktyce nacinanie jest wykonywane różnymi metodami, zależnie od zarysu i skoku gwintu, materiału, narzędzia, i mocy maszyny. W naszych zastosowaniach gdzie będziemy nacinać raczej gwinty o niewielkim skoku (i głębokości nacięcia) które nie generują dużych oporów skrawania, zastosujemy głownie najprostszą do wykonania dla operatora promieniową metodę a, ewentualnie z dosuwem b z rysunku poniżej, która wymaga już więcej matematyki i zachodu. Pozostałe metody cząstkowego nacinania zarysu stosuje się do nacinania gwintów o dużych skokach, szerokich zarysach (trapezowe, prostokątne, itd) lub twardych materiałach, gdzie metoda promieniowa (a) toczenia w każdym przejściu pełnego zarysu generowała by zbyt duże obciążenia dla narzędzia których mógłby nie wytrzymać. Metoda a jest najłatwiejszą dla operatora, ponieważ poza pilnowaniem ustawienia wg skali pokrętła sań poprzecznych głębokości ap dla kolejnego przejścia, oraz pilnowaniem by suma tych głębokości nie przekroczyła wysokości zarysu gwintu, potrzebna jest tylko pewna manualna zręczność dostatecznie szybkiego wycofania noża i zatrzymania czy przerzucenia obrotów by nie "wjechać" nim w inna niż gwintowana część materiału. Aby naciąć gwint o prawidłowym zarysie nóż ustawiamy osią zarysu ostrza prostopadle do nacinanej powierzchni. Pomocnymi tu będą zarówno do prawidłowego wykonania kąta wierzchołkowego (60° lub 55°), jak i naostrzenia ostrza noża, któremu powierzchni przyłożenia (od strony w którą porusza się nóż posuwem fn) trzeba nadać trochę większą wartość kąta α by nie tarła ona o pochyłą linia nacięcia bruzdy gwintu, a także do ustawienia ostrza do nacięcia gwintu zewnętrznego czy wewnętrznego, będą tokarskie wzorce zarysu gwintu, Ruch noża przy poszczególnych przejściach nacinania gwintu zewnętrznego (czopa) będzie wyglądać jak na poniższym rysunku
-
Witam kolegów, i chciałbym zapewnić, że się nigdy na nikogo nie obrażałem ni żywiłem urazę, i dalej nie zamierzam, a tym bardziej do kolegi Kacpra któremu życzę dużo Słońca i pogody ducha. Fakt, środkowa Anglia do najsłonieczniejszych nie należy, ale i u mnie w środkowej Polsce w odróżnieniu od krakowskiej wiosny kolegi Marka, do wczoraj szaro, buro, i z porannym szronem było. Na szczęście dzisiaj kochane Słoneczko pełną gębą świeci, i choć białe dachy były rano, to zaraz cieplej na duszy się robi. A i bociany pono już przylatują, pewnie się zwiedziały i na 500+ pierwsze chcą się załapać. Głowa do góry drogi Kacprze, i do Ciebie się w końcu w tej Anglii uśmiechnie ! I ponawiam swoją szczerą prośbę byś poprowadził temat obróbki CNC, czy też w swoim autorskim, czy jako współautor w wydzielonym właśnie przez kolegę Kubę temacie o obróbce skrawaniem. Bo przecież jedno drugiemu na drodze nie stoi, wręcz przeciwnie - mogą się wspaniale uzupełniać, a na pewno wszyscy na tym skorzystamy... Wszystkich zresztą kolegów mających do czynienia z obrabiarkami i obróbką, większe czy mniejsze, pozytywne czy mniej doświadczenie do udziału zapraszam, bo suma wiedzy nas wszystkich jest nie do przecenienia, a mniemam, że jeszcze długo w środowisku będzie aktualna (no chyba, że nasz kolega wynajdzie drukarkę 3D na metal )
-
Rozważając dalej - mamy do nacięcia gwint o danym skoku(na jeden pełny obrót materiału), a śruba pociągowa przesuwająca narzędzie ma przecież swój gwint o własnym, na dodatek stałym skoku na jeden obrót, zazwyczaj innym niż ten który mamy naciąć. I właśnie do tego by 1 obrót wrzeciona przełożyć na odpowiednią wartość obrotu śruby, aby ta w tym czasie przesunęła narzędzie o żądaną długość h (P), służy przekładnia zębata gitary z wymiennymi kołami. I tu pomoże nam arytmetyka. Przykładowo chcemy naciąć skok P = 2mm, a śruba pociągowa ma skok 4mm, nawet bez liczenia widać, że aby to osiągnąć trzeba dwa razy obrócić wrzecionem (i materiałem) na jeden obrót śruby, czyli przełożenie ogólne między śrubą a wrzecionem powinno wynosić: 4/2 = 2 razy a przy żądanym skoku P = 0,5mm przełożenie wyniesie 4/0,5 = 8, które łatwo osiągnąć nawet dwoma kołami, Ale już przy nacinanym skoku P = 0,75mm przełożenie wyniesie 4/0,75 = 5.333333333; a dla P = 2,25mm przełożenie wyniesie 4/2,25 = 1.7777777777777777; i tu już nie jest tak łatwo, trzeba zastosować przekładnię wielostopniową, najczęściej w małych tokarkach składającą się z 4-6 kół (+ stałe na wrzecionie), której poszczególne koła można obliczyć np za pomocą wzoru; (a/b)*(c/d) = Sn/Sp gdzie a,b,c,d - (z1, z2, z3, z4) koła gitary Sp - skok śruby pociągowej Sn - skok gwintu nacinanego dla calowych a można użyc także gotowych tablic tokarskich (Poradnik Tokarza) lub np takiego kalkulatora ( http://www.dobreprogramy.pl/Gitara,Program,Windows,11751.html ) (gdzie L- to skok śruby pociągowej, M - skok nacinanego gwintu (lub ilość zębów nacinanego koła zęb.) który oblicza najbardziej prawdopodobne kombinacje kół (z dokładnością do wielu miejsc po przecinku) które dopasowujemy do zestawu kół posiadanych przez nas, lub kalkulator w którym podajemy jakie koła posiadamy. tu kalkulatory kół gitary dla posiadaczy tokareczek Mini-Lathe (i klonów) ze śrubą pociągową o skoku 1,5mm, dla skoków metrycznych i TPI (ang. Thread Per Inch- zwojów na cal) http://www.cgtk.co.uk/metalwork/reference/changegears http://www.littlemachineshop.com/Reference/change_gears.php http://www.gizmology.net/changegears.htm...(calowe) http://mynewlathe.blogspot.co.uk//2015/01/threading-gears-calculator.html...(na Android) Ale na szczęście zazwyczaj nie musimy łamać sobie głowy żmudnym liczeniem, bo do ustawienia skoku gwintu korzysta się z tabliczek dla wygody operatora umieszczonych przez producenta na obrabiarce i/lub zapisanych w DTR-ce maszyny, w których podano skład kół dla danego skoku obliczony dla tej konkretnej obrabiarki, wraz ze schematyczną ich konfiguracją które z którym się zazębia, a które są ze sobą sprzężone na jednej osi, Tak, że już nie musimy znać skoku śruby ani dokonywać samodzielnie czasochłonnych obliczeń. Tabliczki wszystkich tokarek mają często odmienny kształt i kolejność rozmieszczenia tabel dla poszczególnych rodzajów gwintów i posuwów, ale zawsze zawierają 3 głównie nas interesujące: — tabela ustawień posuwów, mm/O, (w dużych maszynach posuw napędza wałek pociągowy a nie śruba, oznaczany często symbolem żmijki WW) — tabela ustawień dla gwintów metrycznych, mm/O (dla wszystkich rodzajów gwintów suport napędza śruba co oznacza się przeważnie symbolem lub rozciągniętą żmijką ) — tabela ustawień dla gwintów calowych (TPI), n/1" (zwojów na 1 cal), a także mniej dla nas istotne — tabela ustawień dla gwintów modułowych πmm/O — tabela gwintów Diametral Pith (DP) https://www.google.pl/search?q=tabliczki+gwint%C3%B3w+tokarek&tbm=isch&imgil=IErq6t4629DOSM%253A%253BlfSIrbfqVSz-nM%253Bhttp%25253A%25252F%25252Fwww.cnc.info.pl%25252Ftopics56%25252Ftablica-gwintow-tokarka-tub-32-vt45485.htm&source=iu&pf=m&fir=IErq6t4629DOSM%253A%252ClfSIrbfqVSz-nM%252C_&usg=__T38RuUIWJFqpNEltvV_dfXU3-vM%3D&biw=1214&bih=750&ved=0ahUKEwj7mf22lcvLAhUzS5oKHTOVAKEQyjcIJQ&ei=f3HsVrvePLOW6QSzqoKICg#imgrc=_ http://www.cnc.info.pl/topics56/tokarka-tbs-20-vt51290.htm Dlaczego posuwy do toczenia są w tabelach na tabliczkach umieszczane osobno od gwintów? Bo posuwy muszą mieć dużo mniejszą niż do nacinania gwintów wartość skoku na obrót, przecież inaczej wyszedł by nam gwint a nie gładka powierzchnia po przetoczeniu. Poza tym posuwy w bardziej od prostych hobbystycznych maszyn rozbudowanych tokarkach napędzane są najczęściej wałkami pociągowymi przesuwającymi suport, a nie śrubami pociągowymi. Instrukcję jak ustawić w tokarce pożądany przez nas skok gwintu pokażemy może na przykładzie popularnej wśród modelarzy tokarki Mini Lathe (i jej klonów) o bezpośrednim sprzężeniu śruby z gitarą, której DTR-kę mamy w linku http://users.tpg.com.au/users/p8king/files/c3lathe.pdf Musimy przy tej tokarce na początek zwrócić uwagę na jeden szczegół budowy. A mianowicie na umieszczony między wrzecionem a kołami gitary zespół kół nawrotnicy, którego koła wejściowe Spindle Gear 45t, i zdawcze Driver Gear 45t mają tę samą ilość zębów(z=45), a razem z dwoma pośrednimi kołami nawrotnicy F/N/R Idler Gears o jednakowej ilości zębów jego sumaryczne przełożenie równa się 1:1, i nie wnosi do ogólnego przełożenia wrzeciono-śruba żadnej zmiany obrotów. Tabela doboru kół zmianowych dla gwintów metrycznych dla tej tokarki ma postać a tabliczka na maszynie wygląda podobnie na (klon Sieg C2) Dla gwintów calowych (ilość zwojów na 1 cal) wygląda ona podobnie, i podobny jest sposób kompletowania kół wymiennych dla danego skoku, ale potrzebna jest do tego zmiana sruby pociagowej na calową o skoku 16TPI (16 zwojów na cal, lub metrycznym skoku 0.0625in= 1.5875mm) Jak widać w zależności od ustawianego skoku do gitary zakładamy jednym razem komplet 3 kół, a innym razem komplet 4 kół. Osie kół pośrednich w gitarze są przesuwne i mocowane na tzw lirze, która może być obracana wokół osi koła zdawczego (na śrubę pociągową), a to w celu dopasowania do siebie różnych średnic kół wymiennych gitary. Podobne liry maja wszystkie mechaniczne tokarki Ustawianie posuwu. Tokarka Mini Lathe jest tak prostą konstrukcją, że mechaniczny posuw do toczenia ma stałą wartość przy kombinacji 4 kół: 2 x z=20 i 2 x z=80, co przy obrotach 800obr/min daje szybkość skrawania vc=75mm/min, a posuw wyniesie fn= 75mm/800obr = 0.09375mm/obr ≈ 0,1mm/obr, czyli średnio.. W popularnych konstrukcjach powstałych na bazie tokarki Nutool proces ustawiania skoku gwintu(0,25-3mm) wygląda bardzo podobnie, choć mimo braku skrzynki posuwów ma ona w porównaniu z Mini Lathe możliwość ustawienia gitarą większej ilości zakresów posuwów do toczenia fn (0,04-0,20mm/obr) co znacznie podnosi jej walory użytkowe. Niektóre tylko odmiany http://img8.nokaut.pl/p-cc-d8-ccd83da2141308ed2fbc359ece747c49500x500/tokarka-uniwersalna-precyzyjna-do-metalu-maktek-tytan-700x330-ewimax.jpg mają miedzy gitarą a śrubą zamontowaną nawrotnicę, podobnie jak to jest w tokarkach AT http://pfmrc.eu/uploads/monthly_02_2016/post-3384-0-65091700-1454580306_thumb.jpg, BL-480PS, itp, Tabela kół zmianowych gitary do gwintów ma wartości cdn...
-
Serdecznie dziękuję Koledze Moderatorowi za wydzielenie tego tematu, co mam nadzieje pozwoli szybciej dotrzeć poszukującym do potrzebnych im informacji. Jednocześnie gorąco zapraszam wszystkich kolegów mających jakiekolwiek doświadczenie i wiedzę o obrabiarkach, obróbce metali i nie tylko, do współredagowania tego tematu, a zainteresowanych do przedstawiania swoich problemów, pytań, na które postaram się w miarę mojej wiedzy odpowiedzieć a sadzę, że i doświadczeni koledzy nie poskąpią swojej pomocy. Roman P.S. do Kolegi Moderatora. Z tego co się zdążyłem zorientować to w tym temacie brakuje wpisów ze starego tematu http://pfmrc.eu/index.php?/topic/58564-jaka-ma%C5%82a-frezarka-do-metalu/page-7 z dni między 2 marca a dziś(17.03) (data + nagłówek, pierwsze zdanie): Napisano 06 March 2016 - 20:18 Wytaczaki. Napisano 11 March 2016 - 13:25 Wykonanie potrzebnych otworów o bardzo małych średnicach Napisano 14 March 2016 - 02:05 Rowek (przelotowy!) na klin w kole pasowym, zębatym i innym Napisano 15 March 2016 - 14:26 Gwintowanie. Jeśli by można to wstawić to bardzo prosiłbym (mam nadzieję, że sam tu czegoś nie pokiełbasiłem, a jeśli, to bardzo przepraszam..)
-
Jak tam Kolego Marku mają się postępy w wiórotwórstwie i poznawaniu tajników Twojej maszyny, obrabiałeś może coś poza kajzerowskimi bombami? Omówiliśmy już sobie prostszą dla amatora metodę wykonywania gwintów narzynkami i gwintownikami, teraz przejdziemy do nacinania ich nożem. Pewnie niektórzy koledzy mają mgliste dość pojęcie jak to w tokarce funkcjonuje i co od czego zależy, zatem znów zacznijmy od odrobiny teorii, przy czym interesuje nas tylko podstawowa geometria gwintu (bez zagłębiania się w jego zagadnienia wytrzymałościowo-kinematyczne) bez której zrozumienie pewnych zależności miedzy gwintem a mechanizmami tokarki byłoby trudniejsze. Jak zapewne wszyscy wiedzą teoretyczny gwint jest to linia śrubowa powstała z nałożenia na obracający się walec o średnicy d trójkąta prostokątnego o wysokości h, i długości podstawy A-A równej obwodowi walca πd, (a fizycznie przybiera postać śrubowego nacięcia na powierzchni walcowej lub stożkowej, zewnętrznej lub wewnętrznej) Wysokość h jest tożsama ze skokiem P naszego gwintu. Krótko mówiąc jest to liniowe przesuniecie narzędzia wzdłuż powierzchni materiału o stałą wartość podczas każdego jego obrotu. Ale jak to zgrać by taką synchronizację obrotów wrzeciona z zamocowanym materiałem, i liniowego posuwu suportu z narzędziem uzyskać? Sposoby praktycznie dostępne amatorom są dwa: - mechaniczny, poprzez sprzęgnięcie przekładnią zębatą zwaną gitarą wrzeciona ze śrubą pociągową napędzającą przesuw suportu po łożu. Sprężenie to będzie miało stałą wartość przełożenia, niezależnie od wielkości i kierunku obrotów jakie ustawimy dla wrzeciona, - elekromechaniczny (CNC), gdzie rolę gitary spełnia programowalne zsynchronizowanie obrotów autonomicznych napędów wrzeciona i suportu w kilku osiach przez komputer, ale o tym więcej z pewnością mógłby nam powiedzieć kolega Kacper jako bardziej rzeczy świadom. My zajmiemy się układem mechanicznym - gitarą, jako prostszym, i chyba jak dotąd bardziej rozpowszechnionym wśród amatorów. I tu musimy wrócić do schematycznej budowy tokarki, jej mechanizmów. Poniżej mamy prostą animację ukazująca w schematyczny sposób jak działają najważniejsze funkcje w tokarce. nas pod kątem nacinania gwintów interesują w zasadzie trzy: - działanie nawrotnicy (od 0:40) zmieniającej kierunek obrotów śruby pociągowej - działanie gitary (od 0:51) zmiana przełożenia (kół przekładni) - załączanie śruby pociągowej zamkiem (od 2:43) do przesuwu suportu (jak działa zamek - poniżej..) W praktyce konstrukcji obrabiarek hobbystycznych mamy dwa rodzaje sprzężeń wrzeciona ze śrubą pociągową: - w konstrukcjach prostszych typu Mini-Lathe, AT, Nutool, i innych, nie posiadających osobnej skrzynki posuwów, gdzie śruba pociągowa sprzęgnięta jest bezpośrednio z przekładnią gitarową (czasem tylko pośrednia nawrotnica zmieniająca kierunek obr. śr. jak np w AT), - konstrukcje posiadające wygodne w użyciu podczas toczenia, pozwalające szybko zmieniać prędkość posuwu fn narzędzia mniej lub bardziej rozbudowane skrzynki, które zmieniają lokalnie obroty śruby (przełożenie) niezależnie od głównego przełożenia gitary, ale których ustawienia są włączone w ogólne przełożenie wrzeciono - śruba podczas ustawiania skoku gwintu do nacięcia albo w ustawieniu ich przełożenia 1:1, albo innym w/g tabliczki (pola A, B, C - część biała tabliczki; część niebieska odnosi się do kół gitary)
-
Dobrej. Odpowiedź może się wydać infantylna, ale myślę, że nawet zatwardziałego fana jednego gatunku jest w stanie poruszyć dzieło wybitne z zupełnie innego.. Wszystko zależy od okoliczności.
-
Przykro mi, że odniosłeś kolego wrażenie, że zawłaszczam sobie temat, bo ani nie miałem takiego zamiaru, ani tym bardziej do głowy mi nie przyszło kogoś z niego wyrzucać. A już w żadnym wypadku nie uważam się za właściciela wiedzy którą tu przedstawiałem. Forum jest jest przecież otwarte dla wszystkich, i wszyscy mogą się w nim swobodnie wypowiadać w każdej kwestii, zwłaszcza "po linii" tematu. Co najwyżej możemy się pospierać o meritum, bez żadnych osobistych wycieczek. W cytowanej odpowiedzi określiłem tylko do kogo i dlaczego kierował będę głownie swoją wiedzę, czyli zaczynających przygodę z obrabiarkami i obróbką metali, a mających prawie lub żadne w tym doświadczenie, bo nadal uważam (może mylnie), że sztuki latania nie zaczyna się od sterowania akrobatów. Jak słusznie zauważył kolega Leszek, są to podstawy podstaw, ale mnie osobiście przeraża wykształcony inżynier nie znający tabliczki mnożenia, nie mówiąc o absolwentach podstawówki czy technikum (szok prawda? niestety znam takiego) Do dyskusji włączyłem się kiedy kolega Marek poprosił szerokie gremium o radę i uwagi odnośnie tokarko-frezarki którą zamierzał nabyć, a jako że sam stwierdził brak doświadczenia odnośnie sztuki skrawania, dlatego staram się Jemu i innym tym zainteresowanym pomóc na ile tylko potrafię, I tylko tyle. A jeśli kolega ma chęć podzielić się swoimi doświadczeniami i wiedzą o maszynach i obróbce CNC, to ja mogę tylko takiemu pomysłowi przyklasnąć i szczerze do niego namawiać, choć nie jestem gospodarzem wątku. A i sam chętnie z wiedzy kolegi skorzystam i z pewnością wiele się nauczę, bo w tym temacie nie mam doświadczenia. Ma kolega po części rację, że trochę wykraczam poza temat, choć po omówieniu podstaw toczenia chciałem przybliżyć kolegom również zagadnienia dotyczące frezowania. i może dobrze by było wydzielić i przenieść owe moje i innych wiadomości do nowego tematu "Warsztatu", np "Obróbka i obrabiarki" czy jakoś podobnie, który byłby adekwatniejszy do zawartości, a i dla poszukujących łatwiejszy do znalezienia, O co kolegę Moderatora, jeśli jest to możliwe do wykonania, gorąco proszę. A kolegę, i innych kolegów serdecznie do współpracy i podzielenia się swoja wiedzą w tym temacie namawiam. I jeszcze raz Cię kolego Kacprze szczerze przepraszam, Mea Culpa, jednocześnie gorąco Cię namawiam do włączenia się w temat, bo tu przecież nie o to co my sami wiemy chodzi, tylko ile możemy pomóc innym. Tak przynajmniej zawsze do tego podchodziłem... Roman.
-
Gwintowanie. Teraz zajmiemy się dość częstą i ważną z punktu widzenia każdego tokarza-majsterkowicza, także modelarza, umiejętnością jaką jest gwintowanie maszynowe. Zarówno zewnętrzne jak i wewnętrzne. Można je wykonać na tokarce na dwa sposoby: - narzynką lub gwintownikiem, zalecane wszędzie tam gdzie stosowane są typowe rodzaje gwintu(metryczne, calowe), z typowymi wartościami skoków gwintów (w tym drobnozwojne), oraz do małych i najmniejszych średnic, których wykonanie za pomocą naszej tokarki nie stanowi trudności (moc napędu) Ten sposób jest najprostszym i najpopularniejszym do wykonania gwintu na tokarce, nie wymaga jakichś większych zdolności manualnych od operatora, można wykonać go tymi samymi co do ręcznego gwintowania narzędziami, choć do jego poprawnego wykonania trzeba znać kilka tokarskich tricków, o czym dalej. - nacinany nożem, stosowany tam gdzie z racji nietypowego zarysu (prostokątny, trapezowy, niesymetryczny, czy okrągły), nietypowej średnicy, skoku (np M38x1,5; M25x3), ciężko byłoby znaleźć nam takową narzynkę czy gwintownik, lub byłoby to ekonomicznie nieopłacalne. A duża średnica gwintu czy "gruby" skok powodowałby przy gwintowaniu nimi takie zapotrzebowanie na moment obrotowy Mo (duże opory skrawania Fc), którym nie podołałby napęd naszej maszyny, zwłaszcza na potrzebnych do tej operacji bardzo małych obrotach. Nacinanie nożem jest dużo mniej "momentożerne" i w zasadzie nie różni się parametrami od typowego toczenia, Poza tym można je wykonać miejscach dla narzynek niedostępnych, np między kołnierzami (+dzielona nakrętka), czy na materiałach niezbyt z powodu ich wytrzymałości na rozciąganie do gwintowania narzynka/gwintownikiem się nadających. Zaczniemy jak zawsze od odrobiny od teorii co do samego gwintu. Ile jest rodzajów i odmian gwintów służących do konkretnych zastosowań możemy zobaczyć tu https://pl.wikipedia.org/wiki/Gwint http://slideplayer.pl/slide/812972/ których najpopularniejszych przedstawicieli mamy tu http://www.rems.de/kataloge/pol/sections/Gewindetabellen.pdf Kąty zarysu wierzchołkowego wybranych typów gwintów mamy tu Jak widać większość gwintów zwłaszcza o zarysie trójkątnym ma kąt 60° lub 55°, w tym: 60°- wszystkie metryczne, lub dla calowych : 55° "angielskie" Withwortha, i 60° "amerykańskie" Briggsa, (zwłaszcza drobnozwojne). . Ale więcej informacji znajdą koledzy w necie, lepiej zajmijmy się praktyką. Zarówno w ręcznym jak i w typowo maszynowym gwintowaniu potrzebne do wykonania będą nam wymiary wyjściowe dla danego gwintu - średnica d sworznia (czopu) śruby, - lub średnica D otworu nakrętki, Zazwyczaj posługujemy się tu gotowymi tabelami których w internecie jest multum (ale ostrzegam, niektóre zawierają błędy). My posłużymy się tu sprawdzonymi http://www.pkm.edu.pl/index.php/polocenia-obl/50-01010001 Kto potrzebuje dokładniejszych danych, zwłaszcza dla nietypowych gwintów metrycznych, może sobie zaimplementować bardzo dobry i przydatny kalkulator gwintów, podający wymiary nawet w zależności od wybranych właściwości, tolerancji gwintu (typowa - 6e) ze strony http://www.obliczenia.icad.pl/gwinty/ screeny Najczęściej wykonywanym amatorsko gwintem jest gwint metryczny-trójkątny, prawozwojny, o kącie zarysu wierzchołka 60°, który charakteryzuje się podstawowymi cechami Opis: P - skok gwintu, D – średnica nominalna gwintu nakrętki, d – średnica nominalna gwintu śruby, (jak widzimy duże litery dla wymiarów gwintów wewnętrznych - nakrętek, a małe litery dla wymiarów gwintów zewnętrznych - śrub. Czasem jednak spotyka się oznaczenia odwrotne) D1 – średnica wewnętrzna gwintu nakrętki, d1 – średnica wewnętrzna gwintu śruby, D2 – średnia średnica gwintu nakrętki, d2 – średnia średnica gwintu śruby, d3 – średnica rdzenia śruby, Kąt zarysu gwintu 60º. Oznaczenie gwintu metrycznego trójkątnego: M W przypadku gwintu o skoku zwykłym, oznaczenie odpowiada średnicy nominalnej gwintu bez podawania skoku: np dla gwintu o średnicy d =20mm i skoku P = 2,5mm oznaczenie to: M20 (w tabelach, rysunkach narzędziach) Dla gwintu drobnozwojnego lub nietypowego obok oznaczenia średnicy podajemy również skok(skok P = 1,5mm): M20x1,5 Gwinty lewozwojne (lewe) wszystkich rodzajów i skoków oznacza się w symbolu (także na narzędziach) wyróżnikiem (LH) na końcu, przykładowo M12LH; M20x1,5LH; 1¼" LH , lub z wyróżnikiem z przodu, np LHM16; LH1¼" (zależy od zastosowanej normy, czasem na rysunkach w symbolu także zamiast wyróżnika LH stosuje się napis "lewy") Dla innych kształtów gwintów będą inne niż M oznaczenia, np trapezowy średnicy 20 i skoku 4mm będzie miał oznaczenie: Tr20x4; Tr20x4LH, LHTr20x4; itd. Jeśli nie mamy pod ręką tablic, to interesującą nas średnicę D1 otworu (nakrętki) pod gwintownik dla znormalizowanych gwintów metrycznych można samemu obliczyć dla danego skoku P i średnicy nominalnej śruby d ze wzoru : D1=d1= d - 1,082531755P d2= d - 0,649519053P d3= d - 1,226869322P (średnica d3 natomiast będzie nam potrzebna kiedy będziemy nacinać gwint zewnętrzny nożem.(do ewentualnego obliczenia wysokości zarysu h3, czyli głębokości nacięcia gwintu, która nie jest tożsama ze średnią otworu D1 (nakrętki). A dlaczego to wyjaśnimy za chwilę.) Sprawdźmy dla gwintu M20x1,5: D1= 20 - (1,082531755 • 1,5) = 20- 1,62376-976325 = 18,37620023675 ≈ 18,376 i z tabelą http://www.pkm.edu.pl/index.php/polocenia-obl/52-01010003 Teoria się zgadza. No tak , ale porównując to z dostępnymi w internecie tabelami średnic wiercenia otworów pod dany gwint, stwierdzimy różnicę, w poniższym przypadku o +0,124mm... (?) http://koledzypofachu.pl/index.php/jak-dobrac-wiertla-pod-gwinty-metryczne/...(warto sobie to wydrukować i powiesić koło maszyny, wiertarki,) Skąd się to bierze... Jak pamiętamy z wątku o igle przebijającej szybę, narzędzia skrawają relatywnie twardy przecież metal poprzez skumulowanie na swej krawędzi skrawającej ogromnej siły, zdolnej pokonać jego granicę plastyczności, (a przedtem sprężystości). I to właśnie plastyczność warstwy metalu będącej w bezpośredniej bliskości ostrza, która nie jest oddzielana nie w postaci wióra (pozostaje), powoduje minimalne "rośnięcie" wysokości gwintu pod naciskiem narzędzia, którego wartość jest zależna od jego wytrzymałości( twardości). dlatego też dla różnych materiałów wartość tej korekty jest różna. Stąd bierze się także "wypływka" powstająca wokół krawędzi otworów wierconych w miękkich metalach. Także nacinając gwint zewnętrzny praktycznie zmniejsza się wymiar sworznia o ok 0,2 mm, by narzynka nam nie zrywała pęczniejącej nitki, a po nożu nie został za ciasny. Biorąc pod uwagę owo "rośnięcie" wysokości gwintu pod ostrzem, możemy się zdziwić dlaczego w takim razie podawane w innych praktycznych tabelach średnice otworów wierconych właśnie w miękkich materiałach mają być mniejsze niż w twardych, skoro przecież właśnie bardziej "rosną", czyli logicznie średnice powinny być jeszcze większe? Da się to logicznie wytłumaczyć. Otóż ta właśnie większa plastyczność przy mniejszej sprężystości powodująca, że np aluminium bardziej "puchnie" pod gwintownikiem, powodując też, że ten więcej tego "naddatku" ścina bardziej zmniejszając w ten sposób naprężenia. A przez to aluminium nie wywiera takiego jak np twarda stal, odwrotnego nacisku na posiadające przecież także swoją (co prawda rząd wielkości mniejszą, ale jednak,) określoną sprężystość narzędzie. Potocznie mówi się, że w aluminium gwintownik czy narzynka bardziej "zacinają" gwint, dlatego wiercąc otwór jak dla stali może okazać się, że gwint wyszedł nam za luźny, a za to zbyt mały otwór dla stali spowoduje taki wzrost oporów, że urwiemy gwintownik (dlatego też stosuje się 2 lub 3 częściowe stopniowe wykonanie gwintu - kompletów gwintowników) (obecnie produkuje się komplety w których gwintownik bez pasków jest wykańczakiem, czyli "dwójką" bądź "trójką") Narzynki wykonuje się jako jednoprzejściowe - wykonują gwint od razu na gotowo.. Obrazowo mówiąc aluminium zachowuje się trochę jak glina, która gdy będziemy ją naciskać wypłynie między palcami, ale już nie wróci do dawnego kształtu zachowując ten naszych dłoni (gwintownika czy narzynki), a stal jest bardziej jak guma - pod naciskiem ustąpi, coś zetniemy, ale wróci częściowo do dawnego wymiaru (zmniejszając otwór) bo jest bardziej sprężysta a mniej plastyczna. (dlatego gumę dość trudno się skrawa, bo odkształca sie pod nożem , który powinien wywierać na nią jak najmniejszy nacisk - czyli być bardzo ostry - w praktyce najlepiej z HSS, któremu możemy nadać większy bezpieczny niż w VHM kąt natarcia). Na pierwszy rzut oka trochę to kuriozalnie wygląda, ale wypracowane zostało praktyką pokoleń, i możemy stosować zbliżone proporcje do naszych potrzeb, Ale trzeba tez wspomnieć, że są "wredne' gatunki nieżelaznych, zwłaszcza niektóre aluminium, które z racji ich własności fizyko-strukturalnych, tendencji do miejscowego utwardzania struktury pod naciskiem, skłonności do tworzenia narostów, w ogóle ciężko się obrabia i owe zasady zdają się im troszkę wymykać. Na szczęście z innymi jest na ogół trochę lżej. Reasumując dla stali możemy śmiało przyjmować praktyczne wartości tabelaryczne, lub teoretyczne pomniejszone o ok. 0,2mm, i powinno być Ok. Chyba, że chcemy wykonać super dokładny gwint, wtedy trzeba brać pod uwagę własności danego gatunku stali. A jak na tokarce wykonać gwint np narzynką? Można metoda prostszą - podpierając zwłaszcza przy początku gwintu typową ręczna oprawkę narzynki tuleją konika. Gwintowany sworzeń(czop) powinien mieć na swej powierzchni czołowej (najlepiej dość dużą) fazę pomagającą centrycznie wprowadzić w materiał przypieraną do niego tuleją konika (z czuciem by jej nie połamać) narzynkę. W miarę zagłębiania się narzynki w czop dosuwamy z lekkim dociskiem do niej tuleję, co zapobiegnie zwichrowaniu jej płaszczyzny do osi (czyli krzywemu nacięciu gwintu). Co kilka obrotów cofamy o jeden czy pół obrotu by zerwać zbyt długie wióry. Jeśli chcemy by gwint dochodził do samego końca zatoczonego stopnia, to najlepiej proces docinania dokończyć pokręcając narzynkęręcznie, by przez przypadek nie "wjechać" na obrotach w materiał, co grozi zerwaniem gwintu lub połamaniem narzynki. Do gwintowania narzynką służy też tzw, "lufka", która bardzo ułatwia i "automatyzuje" proces gwintowania jak to widać też na powyższym filmie, składa się z części stałej (prowadnicy) mocowanej w koniku, i przesuwanej po niej części ruchomej(suwaka) z oprawką narzynki. Zazwyczaj ma wymienne oprawki do mocowania różnych średnic narzynek, i niekiedy chwyty do mocowania gwintowników. Oczywiście zawsze nacinając gwint, niezależnie czy to narzynką, gwintownikiem, głowicą do gwintów, czy nożem, należy stosować smarowanie np olejem (najlepiej lnianym) lub specjalnym preparatem do gwintów (np Terebor, Starex, itp), bo to polepsza warunki skrawania, chłodzi, a zmniejszając opory pozwala uzyskać lepszą powierzchnię gwintu. Obroty jakie należy przy gwintowaniu stosować, podobnie jak to widać na filmie, powinny być bardzo małe, lub nawet ręczne jeśli z racji średnicy gwintu silnik małej tokarki nie daje rady. Za wysokie obroty są przeważnie przyczyną zrywania zwojów, zapychania kanałów wiórowych, nadmiernego grzania się narzędzia wskutek wiekszych oporów, a często i jego pękania. Wykonując w materiale otwór do gwintowania gwintownikiem należy przed wywierceniem wiertłem wykonać najpierw nakiełek, a jeśli średnica pozwala, to po wierceniu roztoczyć nożem do potrzebnego wymiaru, by zneutralizować ewentualne bicie otworu. Gwintownik mocujemy np w uchwycie wiertarskim mocowanym w tulei konika, lub specjalnej oprawce. Po "załapaniu" kilku pierwszych zwojów przez gwintownik odpuszczamy zacisk konika na łożu i powalamy by konik był swobodnie "wciągany" przez gwintownik, który w ten sposób samoczynnie centruje się do otworu. A jeśli mamy obawy, że drobny gwint przy małej średnicy gwintownika mógłby się zerwać nie dając rady uciągnąć dużej masy konika, to popychamy konik po łożu ręcznie, dopychając cały czas go do materiału. podobnie wyciągamy go przy wycofywaniu gwintownika z otworu. Musimy też zwrócić uwagę na możliwość zapychania się rowków wiórowych gwintownika wiórami, zwłaszcza przy małych średnicach gwintów, dlatego należy gwintownik stosownie często wycofywać przerzucając obroty wrzeciona na lewe, oczyszczać, i ponownie wprowadzać. Gwintownik uchwycony w oprawkę do ręcznego gwintowania można też podeprzeć kłem konika za nakiełek w chwycie bądź oprawce, Zresztą podobnie można podpierać gwintownik by wprowadzać go centrycznie w wywiercony na wiertarce czy frezarce otwór... Przy okazji - do ręcznego gwintowania dokładnie prostopadle do powierzchni materiału służą takie i podobne przyrządy (które możemy wykonać nawet sami) http://www.micro-machine-shop.com/tapped_threads_reference_tables.htm cdn..
-
To też silniki modelarskie, tyle, że rakietowe (z wymiennymi ładunkami) z lat 50-tych, produkowane ówcześnie do napędu modeli, na fali zafascynowania nowinką techniczną jaką był wtedy silnik odrzutowy... http://archivesite.jetex.org/motors/motors-imitators.html http://archivesite.jetex.org/archive/article-tailored_history-rs-ss-13.html http://archivesite.jetex.org/archive/archive.html Nawiasem, innym wówczas hitem był... atom, któremu wieszczono szerokie praktyczne zastosowane. Planowano nawet produkcję samochodów z "kieszonkowymi" reaktorami atomowymi.. Ford Nucleon
-
Ciekawe jaki dzisiaj byłby odsetek "specjalistów" od robienia z kosy korkociągu ... A pewnie jeszcze mniej umiało by to.. A propo's, Przypomniał mi się reportaż w TV bodaj z początku lat 90-tych, kiedy to dziennikarze zanabyli informację, że w jakiejś wsi gdzieś na "ścianie wschodniej", stary dziadek klepie swoją kosę na improwizowanej "babce" z... pocisku artyleryjskiego! Po dotarciu na miejsce, okazało się to szczerą prawdą! Bardzo wylewny sędziwy właściciel owego przyrządu chciał im nawet pokazać jak to się dobrze klepie... na bodaj 85mm pocisku od działa, na dobitkę wkopanym zapalnikiem do góry , co wywołało niezłą panikę i rejteradę ekipy z podwórka. Oczywiście zaraz przybyli zaalarmowani przez nich saperzy z milicją, ale właściciel zdecydowanie opierał się zaborowi, twierdząc, że "on na tej babce już tak klepie od wojny i jakości nic, a lepszej nie znajdziesz. Ważne tylko by się metal za bardzo nie rozgrzał !..." http://www.garnek.pl/michalb/3603534/dziadek-klepie-kose-na-babce http://cygnus.ne.3lab.info/post/96073,kosba-przyspieszenie-czwartek
-
Rowek (przelotowy!) na klin w kole pasowym, zębatym i innym, możemy także wydłutować za pomocą kwadratowej (najmniejsza ma 4x4) lub prostokątnej stalki zamocowanej lekko skośnie w imaku nożowym, swoją osią symetrii na wysokości osi koła. Stalka ma zaszlifowaną powierzchnię czoła na kilkanaście stopni (powierzchnia natarcia γ), z krawędzią skrawającą "na ostro", oraz lekko stożkowo boki na długości trochę większej niż wykonywanego rowka, by nie przycierały o jego boki (pomocnicze powierzchnie przyłożenia) Przybieramy na 1 suw w stali (ap) nie więcej niż po 0,2-0,3mm, powtarzając kilka razy przejścia z jedną nastawą (tzw. "wybieganie" się narzędzia do momentu braku ścinania wióra), ze względu na pewną sprężystość naszego dłuta, bo bez tego wytnie się nam skośna głębokość rowka, mogąca w rezultacie dokładania za każdym przejściem głębokości skrawania ap doprowadzić do pęknięcia narzędzia. W trakcie obficie smarujemy olejem, np lnianym lub innym do gwintowania, co redukuje tarcie i opory skrawania. Podobnie jeżeli zauważymy zaokrąglenie rogów krawędzi ostrza lub jego stępienie, to należy je przeostrzyć, bo opory szybko będą rosły odginając nam nóż z wiadomym skutkiem. można tez użyć a do wykonania w otworach rowków nieprzelotowych należy wykonać podcięcie, by dłuto mogło wyrzucić wiór lub jeśli nie chcemy osłabiać detalu - wykonać nawiercenie w miejscu zakładanego wyjścia rowka klina
-
Wykonanie potrzebnych otworów o bardzo małych średnicach (poniżej Ø6mm) które nie jest możliwe do wykonania nawet składanymi typowymi wytaczakami na wymienne płytki, jest natomiast możliwe do zrobienia za pomocą specjalnych narzędzi. Oprócz wykonanych we własnym zakresie ze stali szybkotnących można do roztaczania, gwintowania, rowkowania otworów zastosować też gotowe mikronarzędzia - wytaczaki wykonane najczęściej jako całowęglikowe lub jako węglikowe wkładki do oprawek mocowanych w imakach narzędziowych maszyn. Mają one specjalny kształt chwytu do mocowania w oprawce w konkretnym niezmiennym położeniu( https://www.youtube.com/watch?v=jzXMm_t0X-E&feature=youtu.be ) Ale ich stosowanie wymaga dość sztywnych, pozbawionych nadmiernych luzów maszyn, z racji dużej kruchości węglika. W dobrze wyregulowanej amatorskiej tokareczce też się da, ale te narzędzia nie są niestety zbyt tanie, choć zdarzają się okazje http://archiwumallegro.com.pl/mikrowytaczak_z_w%C4%99glika_r006_0815_15_picco_ic228-2_3942117293.html. http://www.byteboss.com/958286.xls Minimalne średnice wykonywane tymi narzędziami to typowo Ø3mm, a specjalnymi nawet Ø0,42mm (http://www.genswiss.com/microbore.pdf) http://www.fanar.pl/wp-content/uploads/oferta/18_mikronarzedzia.pdf http://www.whizcut.com/internal_turning/boring_bars.html http://www.whizcut.com/internal_turning/turning.html http://www.genswiss.com/microbore.htm http://www.genswiss.com/boringbars.htm http://www.youtube.com/watch?v=oFsReVPJ6KM A amatorsko można pokusić sie o wykonanie takiego mikrowytaczaka nawet na domowej szlifierce stołowej, ze stalki HSS np 4x4mm lub okrągłej, do czego będzie nam potrzebne również dobre oświetlenie i szkło powiększające, oraz dobrze obciągnięta ściernica. Najprostszy to okrągła stalka jak poniżej z zaszlifowaną tylko powierzchnią natarcia, ale przy ich użyciu trzeba mieć na uwadze b. częste wycofywanie celem usuwania wióra. Także ułamane wiertło HSS lub gwintownik z zaostrzoną jak wytaczak resztką kanału wiórowego nadaje się do wytaczania. A co z głębokimi otworami o małej średnicy, którego poprawne wytoczenie nożem jest mało prawdopodobne? To można zrobić na dwa sposoby: a) 1 - nawiercamy w materiale prowadzenie wiertła nawiertakiem, który z racji swojej sztywności zmniejsza potencjalną możliwość bicia nawiercanego otworu. https://www.youtube.com/watch?v=YPZKMs5ocp4 2 - wiercimy wiertłem o średnicy mniejszej od żądanej o 0,2mm. Wiertła można dostać w handlu o gradacji co 0,1mm już od średnicy 0,3mm), 3 - rozwiercamy rozwiertakiem do zakładanej średnicy z dokładnością zazwyczaj H7 ( http://www.pkm.edu.pl/index.php/tolerancje-i-pasowania ) Smarujemy olejem. Rozwiertaki w handlu są dostępne zazwyczaj od średnicy ø2,00mm z gradacja zazwyczaj co 1mm, czasem 0,5mm. rozwiertak powinien być prowadzony możliwie luźno, bez zaciskania konika na łożu i tulei konika w jego korpusie, by nie rozbijał otworu z razie niewspółosiowego jego ustawienia. Do tego tez służy tzw. "pływająca" lub "wahliwa" oprawka rozwiertaka http://www.cnc.info.pl/topics66/rozwiertak-rozbija-o-003-vt69777,20.htm A co zrobić jeśli nie mamy rozwiertaków, lub potrzebna nam nietypowa średnica otworu, na która nie mamy rozwiertaka? Można to zrobić stosując zamiast rozwiertaka wiertło o potrzebnej nam średnicy. Powtarzamy kroki 1 i 2 jak powyżej, z tym że wiertło do wstępnego wiercenia (2 kroku) ma mieć średnice 1/2-2/3 finalnego wymiaru. 3 - wiercimy (powiercamy) wymiar na gotowo wiertłem o żądanej średnicy, gdzie wykonany wcześniej otwór nie pozwala drugiemu wiertłu rozbijać otworu z powodu np niesymetrycznego naostrzenia (wierci wtedy tylko końcówkami jak rozwiertak na swoją średnicę nominalną) Rozwiertak małej średnicy do metali kolorowych, na przykład mosiądzu, można zrobić nawet w ten sposób inne przydatne filmy https://www.youtube.com/watch?v=0H7B1AHlOrY , tu to co omawialiśmy w temacie noży https://www.youtube.com/watch?v=2R0l6I1yrrk . -II- https://www.youtube.com/watch?v=FFWSaffwZOo . . jak i czym wydłutować rowek na klin https://www.youtube.com/watch?v=e4apNy_2AB8 . jak zrobić koło pasowe, chociaż za takie użycie suwmiarki oberwałbym operatorowi uszy.. https://www.youtube.com/watch?v=NqF_ETWvBCA czym skutkują luzy na pokrętłach i śrubach https://www.youtube.com/watch?v=9IvWuXjCVbg . proces nacinania gwintu nożem
-
Obawiam się, że "grafen' to tylko chwyt reklamowy...
-
Na to też znajdzie sę sposób.... https://www.youtube.com/watch?v=jityxjT4Tk0
-
Wytaczaki. Jak już wiemy wytaczak także pracuje w dość szczególnych warunkach. Z jednej strony wymagana jest od nich duża sztywność dla zachowania warunków skrawania - wysokości do osi, rzutującej na kąt natarcia, co z kolei wpływa na opory skrawania, a z drugiej - duża smukłość z racji głębokości otworów jakie mają wytaczać. Dlatego mają inną od krępych noży zewnętrznych noży konstrukcję, gdzie część robocza jest połączona z mocowanym w imaku trzonkiem długą częścią walcową. Potrzebny jest tu kompromis. Wytaczak nie może być zbyt smukły - jak do głębokich małych średnic - bo się złamie lub zbytnio ugnie i odegnie, zmieniając wymiar otworu i psując jego powierzchnię, Ale i zbyt krępy, nadmiernie wypełniając swoim przekrojem na przykład nieprzelotowy otwór, utrudni lub wręcz uniemożliwi usuwanie wiórów z przestrzeni roboczej, i będzie je mielił aż do awarii. http://www.cnc.info.pl/topics89/noze-skladaki-do-nutool-vt11377,50.htm W dodatku długi smukły nóż jest bardzo podatny na generowanie drgań, dlatego jedna z głównych zasad mocowania wytaczaków brzmi: jak najkrócej się tylko da dla wykonania zadania. Nawet za część walcową, jeśli jest sposobność. Oczywiście istnieje wiele modyfikacji kształtu i funkcji, gdzie trzonek jest okrągły, okragło-spłaszczony, lub wytaczak ma aż do części roboczej przekrój kwadratowy, noże hakowe do wewnętrznych rowków i do nacinania wewnętrznych gwintów (też rodzaj wytaczaka), ale podstawowy typ którym głównie będziemy się zajmować jest jak na fotografii. Tu akurat z kątem przystawienia Kr=95°, a są jeszcze Kr=75° I tu podobnie jak w innych rodzajach, z nożami składanymi nie mamy w zasadzie nic do roboty, ale już noże HSS i lutowane mają swoje tajniki które powinniśmy znać by móc sobie taki zmodyfikować(z płytką VHM) lub wytworzyć od podstaw (z HSS) do naszej konkretnej potrzeby.. Jak już wspomniałem z racji swej budowy mają one tendencję do generacji drgań, która zależy od kilku czynników. O długości wystawienia już wspomniałem, zależnej także od materiału z jakiego jest wykonany, nas w zasadzie interesuje pierwszy z góry Inne zależności można przedstawić w takim prostym zestawieniu Jak widzimy amplituda (skłonność do drgań) wzrasta wraz z: - zmniejszaniem kąta przystawienia ostrza Kr, bo wypadkowa sił skrawania zmienia kierunek z poosiowego który nie odgina noża, na bardziej promieniowy, ...................... - powiększaniem promienia wierzchołka ostrza, bo to też przy nie za dużej głębokości skrawania ap w makroskali daje wypadkowy kąt przystawienia Kr ....................... - zmniejszaniem dodatniego kąta natarcia γ, który jak pamiętamy zależy również od wysokości zamocowania przecinaka do osi i średnicy(krzywizny ścianki) otworu, jak łatwo na tym rysunku zauważyć * - w przypadku a duże opory skrawania przy ujemnym kącie natarcia γ zaburzają dobry spływ wióra, skutkujący dużą chropowatością i większymi oporami zwłaszcza tarcia. Te siły oporu odpychają jednocześnie ostrze od materiału, paradoksalnie zmniejszając głębokość skrawania i wytaczaną średnicę. * - w przypadku b wartość kąta γ jest zerowa przy której spływ wióra powinien być regularny, co da dobrą chropowatość, ale wiotkość noża pod wpływem sił oporu skrawania powoduje z jednej strony odpychanie noża po promieniu w kierunku osi obrotu pomniejszając wytaczaną średnicę, a z drugiej działając w dół będą lekko wciągać w materiał w wyniku czego będą się w dużym stopniu znosić. * - w przypadku c w małej średnicy otworze nóż (który powinien być z powodu wiotkości jak najgrubszy), może trzeć o materiał usiłując wypchnąć go z materiału. Z drugiej strony mała sztywność długiego trzonka powoduje, że składowa siły F przy dodatnim kącie natarcia γ będzie (do granicy sprężystości trzonka) próbować wciągać go w materiał, powodując wzrost głębokości skrawania i powiększanie się wytaczanej średnicy. Wypadkowa obu zależy od wysokości do osi, przekroju i długości trzonka oraz rodzaju materiału. Oczywiście jest to bardzo bardzo uproszczony opis zjawiska, bo działa na nie także wiele innych tu nie uwzględnionych czynników. Ale pokrótce można by powiedzieć: lepiej w małych otworach dać nóż nawet lekko powyżej osi, bo może stracimy na gładkości ale nie powiększymy wymiaru, niż za nisko, bo nie dość że powiększy nam otwór to jeszcze trąć spaprze nam powierzchnię. Znaczący wpływ w obu przypadkach ma tu sztywność trzonka. W dużych otworach natomiast, ze względu na duży promień ich krzywizny można dać lekko poniżej, uzyskując bardziej pożądany kąt natarcia γ. I lepszą powierzchnię, gdyż pomimo pewnego ugięcia, ani trzonek ani powierzchnia przyłożenia ostrza nie będzie nam trzeć o materiał.. Oczywiście zdrowy rozsądek jest jak najbardziej pożądany, bo te zależności najbardziej sprawdzają się w metalach, które mają dużo mniejszą sprężystość i "płyniecie" pod nożem niż tworzywa i inne materiały jakie może nam przyjść obrabiać. - kształtu mikroprzekroju i zużycia ostrza (kąt pochylenia krawędzi skrawającej λ - lepszy bliżej zera) stępione lub wyszczerbione ostrze wzmaga opory i drgania - minimalnej długości zamocowania, którą zaleca się na co najmniej 4 przekroje, Co prawda wytaczaki kute ze stali szybkotnącej SWW i z lutowanymi płytkami występują już pd przekroju trzonka 6x6 (widziałem gdzieś takie) a typowo od 8x8, to jeśli musimy zrobić sobie samemu potrzebny wytaczak np ze stalki HSS o kwadratowym przekroju, jak sie do tego zabrać? Trzeba przede wszystkim odsunąć od wytaczanej wierzchołkiem wytaczaka krzywizny otworu przednią ściankę trzonka (dm) między częścią roboczą a mocowaną w imaku, bo nie możemy stalki HSS wygiąć jak nóż kuty ze stali SWW (bo pęknie) Oczywiście podszlifowanie robimy tylko niezbędnej długości, czołem ściernicy, nie dopuszczając do przegrzania. spód trzonka fazujemy zostawiając płaską część w razie potrzeby krótszego mocowania, a spód części roboczej kształtujemy tak by umieszczona w osi pomocnicza płaszczyzna przyłożenia nie tarła o ścianę krzywizny wytaczanego otworu (to samo dotyczy przeostrzanych wytaczaków z płytką lutowaną, które są zazwyczaj topornie zrobione) Niekiedy lekko stożkowo szlifujemy również spód do wytaczania bardzo małych otworów Na koniec robimy odpowiedni kąt głównej powierzchni przyłożenia, oraz obniżamy pod odpowiednim kątem (+γ) powierzchnie natarcia. Można też, jeśli wymiary masywnego trzonka do wytaczania dużych otworów pozwolą, zrobić rowek wiórowy Inne dość nietypowe szlify tu przerobiony z fabrycznego SW7M (zmniejszony przez zeszlifowanie) Jeśli ktoś nie ma (jeszcze) takich manualnych zdolności, to dobrym substytutem jest zastosowanie pasującego wielkością (np 12mm średnicy chwytu) noża od wytaczadła, po lekkiej modyfikacji (zazwyczaj zmniejszeniu, obniżeniu, i zrobieniu kątów) przeważnie dość dużej płytki węglikowej. (ale są też takie i HSS, SW7) Niestety u nas występują zazwyczaj w zestawach jak na zdjęciu, ale na szczęście nie są drogie, za to różnych wielkości, więc do małej tokareczki powinny zaspokoić gro potrzeb. http://archiwum.allegro.pl/oferta/noze-do-wytaczadla-12mm-gwzn50-wytaczak-9-szt-noz-i4178574704.html http://expancnc.com/zestaw-nozy-do-wytaczadla-glowicy-wytaczarskiej-12mm,118,2008.html http://www.e-darmet.pl/glowice-wytaczarskie-cat-92.html http://allegro.pl/noze-noz-do-wytaczadlo-wytaczadel-glowicy-12mm-i5364838074.html do których dorabiamy z aluminiowego/mosiężnego kwadratowego pręta 16x16, 14x14 (dostępne np w OBI) oprawkę do mocowania w imaku tokarki (przez zaciśnięcie). Otwór wiercimy w tokarce podkładając pod szczęki podkładki, lub w wiertarce stołowej, przesuwając w razie potrzeby jego oś względem centrum co umożliwi nam lepsze ustawienie podkładkami wytaczaka do osi toczenia w imaku. Jak już wspomniałem fabryczne wytaczaki z lutowaną płytką są dość toporne, a kąty ich płytki przedstawiają wiele do życzenia, I w takiej surowej formie po lekkim tylko przeostrzeniu powierzchni przyłożenia, z racji nieosłabionego poprawkami przekroju nadają się w zasadzie do zdzierania większych średnic otworów w niezbyt czystej stali, np z rdzą, zapiaszczonych odlewów, odkuwek, porowatego żeliwa, albo części napawanych, chropowatych, czy nieokrągłych. Co można w takiej surówce poprawić? Przede wszystkim można obniżyć wysokość zazwyczaj dość wysokiej płytki węglikowej, by można było ustawić ostrze jak najbliżej osi obrotu, zwłaszcza w małych otworach, poprawiając w ten sposób ogólny kąt natarcia γ jak najbliższy dodatniemu, zapewniając lepsze parametry skrawania niż w oryginale. Można to zrobić albo poprzez płaskie zeszlifowanie płytki z lekko dodatnim kątem płaszczyzny natarcia γ ostrza, albo poprzez zrobienie równoległego do krawędzi skrawającej niezbyt głębokiego rowka wiórowego. podcinamy także pomocniczą płaszczyznę przyłożenia płytki i poniżej płytki, spód części roboczej, oraz ukosujemy powierzchnię przeciwległą pomocniczej. Oczywiście radykalnego "odchudzenia" wytaczaka dokonujemy tylko w razie zaistnienia takiej potrzeby bo wytaczanie dużych otworów lepiej oczywiście wykonywać sztywniejszym nożem. Wtedy poprawiamy tylko kąty samego ostrza. Praktycznie podobne poprawki fabrycznego wytaczaka pozwalające na wytaczanie mniejszych niż oryginalnemu nożowi otworów widać na zdjęciach poniżej.(tu bez obniżenia płytki- nie było takiej potrzeby) Jako że wytaczak jest dość wygięty, a wytaczany otwór nie był głęboki, to mocowano go w imaku trzonkiem było nieco skośnie, by odchylenie od ścianki otworu nie było zbyt duże (by kąt przystawienia ostrza Kr był jak najbliższy 90°, a wypadkowy wektor oporów skrawania był jak najbardziej równoległy do osi) Przedstawione powyżej wytaczaki, również wytaczaki składane, mogą wytaczać otwory do średnic około Ø8mm, a specjalnie wykonane do minimalnie Ø5-6mm, Mniejsze średnice wykonuje się przeważnie w inny sposób, który przedstawimy sobie następnym razem. Wytaczanie otworów stosuje się również jako przygotówka przed operacją rozwiercania rozwiertakami, a ma to na celu usunięcie ewentualnego bicia otworu po wierceniu, i zostawienie tylko niezbędnej wielkości naddatku pod rozwiertak (tylko 0,15-0,2mm). Trzeba wiec taki zabieg przed rozwiercaniem uwzględnić, jeśli chcemy otrzymać centryczny otwór o dokładnej średnicy. Jak koledzy widzą przygotowanie wytaczaka i samo wytaczanie nie jest to jakieś skomplikowane zadanie, a jego kształt nie jest jakiś krytyczny, trzeba tylko trzymać się zasady, że z toczonym materiałem w wytaczaku (podobnie jak i innych nożach) styka się tylko główna krawędź skrawająca, a wielkość trzonka w otworze pozwala na dobry wyrzut wiórów. Polecam kolegom pobuszowanie po poniższych stronach, jest tam wiele ciekawych ilustracji i materiałów odnośnie narzędzi (w tym pomiarowych), obrabiarek, i różnych metod obróbki, wykorzystywanych w amatorskim zastosowaniu. http://www.micro-machine-shop.com/quick_change_tool_post_tool_bits.htm (http://www.micro-machine-shop.com/) I przypominam o świętej zasadzie tokarzy: Toczony przedmiot tak długo będzie idealnie współosiowy, dopóki go nie odmocujemy ! Co to oznacza: jeśli na przykład przetoczymy wałek, wyjmiemy go z uchwytu, zamocujemy ponownie, wytoczymy w nim otwór, zatoczymy część jego zewnętrznej powierzchni na nowo (np czop), lub zatoczymy drugą stronę po jego odwróceniu chwytając za zatoczoną uprzednio część, to nowo wykonane powierzchnie nie będą już idealnie współosiowe z tą wykonaną uprzednio (przed odmocowaniem). Czyli mniej lub więcej będą biły, ponieważ nawet w najlepszym uchwycie istnieją luzy potrzebne do jego prawidłowego działania (prowadnic szczęk, spirali w korpusie i we współpracy ze szczękami), zwłaszcza przy mocowaniu w twardych szczękach. Oczywiście staramy się by to bicie było jak najmniejsze, dlatego jeśli zależy nam na współosiowości to do zataczania drugiej strony stosujemy na przykład miękkie szczęki, z zatoczoną na nowo po ich założeniu powierzchnią mocującą detal, http://www.mechanicalphilosopher.com/3jawtru5.jpg http://homews.co.uk/LrgSoftJawsU02.jpg Co prawda zawsze jakiś uchyb wprowadzą, ale dla większości tolerancji zbyt mały (mikrony lub mniej) by był istotny. Lub przewidując np obracanie detalu do kolejnych zabiegów tokarskich, pomiarów, mocujemy materiał do toczenia w kłach (od strony wrzeciennika może być zatoczony w uchwycie), po uprzednim wykonaniu nakiełków. Da nam to pewność współosiowości skrawanych powierzchni niezależnie ile razy byśmy odmocowywali (mają tak np ostrzone narzędzia jak rozwiertaki, frezy, itp) http://www.northernsteam.com/assets/images/25NC/fronttruck/FT%20(22).jpg http://www.projectsinmetal.com/wp-content/uploads/2009/10/100_0238.jpg ................................................................................................................................................................ No to w zasadzie mamy już omówione z grubsza wszystkie niezbędne tokarzowi noże i ich tajniki, i myślę, że przedstawione tu materiały pozwolą kolegom na samodzielne wykonanie/naostrzenie i pomyślne zastosowanie poprawnie skrawającego noża, Ale jeśli któryś z kolegów ma pytania czy uwagi odnośnie tego co tu sobie przedstawiliśmy, to służę pomocą. W innych kwestiach również... cdn...
-
http://johnsmachines.com/2015/07/07/model-engineering-exhibition-at-bendigo-victoria-australia/ Silnik musi fajnie burczeć... szkoda, ze nie ma filmu.. Edit. Są.. (i inne na stronie) https://www.google.pl/search?q=Gerard+Dean&ie=utf-8&oe=utf-8&gws_rd=cr&ei=gcfWVvO1MoaUsAHgl4XAAw#q=gerard+dean+tiger+tank&tbm=vid
-
A przyjrzyjmy się teraz procesowi przecinania na tym filmie. Co możemy powiedzieć o błędach popełnionych przez operatora i wadach maszyny, które doprowadziły do takiego skutku? 1 - za dalekie wysuniecie materiału z uchwytu, zbyt krótkie i słabe jego mocowanie w szczękach. Na moje oko materiał wystawał jakieś 3-4 średnice, a zamocowany był za 1,5 - góra 2-ie. Przez co narastające coraz bardziej opory skrawania nie miały żadnej trudności by wyrwać go ze szczęk. Zawsze starajmy się przecinać jak najbliżej szczęk, jak najwięcej łapać w szczęki i mocno zaciskać, możliwie krótko wystawiać nóż (jeśli to listwa tnąca), a jeśli już musimy z jakiegoś powodu przecinać daleko od szczęk, to jeśli nie ma otworu na kieł zróbmy w wałku nakiełek, otworek, i podeprzyjmy go nim, przynajmniej do momentu docinania. (od 3:40, zwróćcie uwagę na wielkość obrotów, i jednostajny, niezbyt szybki, ale i niezbyt powolny, skutkujący ciągłym wiórem posuw) Jeśli mamy do przecięcia daleko od szczęk długi cienki wałek, pręt, którego nie ma jak podeprzeć kłem, lub pod jego naciskiem i naciskiem noża może się on wyboczyć, to możemy go podeprzeć w ten sposób, w dopasowanej średnicą, nasmarowanej wewnątrz tulejce zamocowanej np w uchwycie wiertarskim w koniku Innym sposobem na wyboczenie i podrywanie wałka jest podparcie go podtrzymką ruchomą (jak do toczenia gwintów). 2 - za wysokie obroty, na moje oko około ~700-900/min, przez co duże tarcie materiału o chłodzony z przerwami nóż ze stali szybkotnącej szybko rozhartowało i stępiło jego ostrze, doprowadzając do narastania oporów skrawania. Objawiało się to coraz głośniejszym wyższym w tonacji piskiem (od 6:11min), (nawiasem jak usłyszycie coś takiego, to przerwijcie cięcie, przeostrzcie nóż, i zastanówcie się nad obrotami i zamocowaniem materiału). Tu obroty powinny być na poziomie od 250 do max. 400/min, zależy czy to był zwykły HSS czy HSS-Co (kobaltowy) i dobre chłodzenie. Jak nie wiemy jak będzie się zachowywał materiał i nóż, to lepiej zacząć od niższych obrotów, i w razie czego podnieść. 3 - zbyt mało zdecydowany, za wolny, dodatkowo przerywany posuw, co prowadzi do powstawania rwanego, częściowo igiełkowego wióra, kiedy to nóż zamiast skrawać skrobie materiał, który generował słyszane od początku przecinania niższe niż późniejszy pisk tarcia drgania, Takie drgania to zjawisko bardzo niepożądane, odpowiedzialne w efekcie za większość połamań noży i luzowanie się wszystkiego co za słabo dokręcone, również za samoczynne przestawianie się niezaciśniętych dostatecznie mocno elementów obrabiarki (tzw."pływanie"). Paradoksalnie to jednym ze sposobów stłumienia powstających drgań jest zwiększenie posuwu noża by poprzez zwiększenie nacisku na materiał skasować możliwość jego drgania. Oczywiście jeśli maszyna nie ma nadmiernych luzów wrzeciona, bo wtedy to i tak nie pomoże. Nieraz ,zwłaszcza przy cięciu na małych hobbystycznych maszynach zdarza się, że pomimo właściwych parametrów obrotów, stanu luzów i łożyskowania, krótkiego wystawienia materiału i sztywnego, dobrze naostrzonego noża, drgania i tak się wzbudzają. Tu przyczyną może być zbyt mała masa maszyny, zwłaszcza suportu. Zastanawiało Was może kiedyś dlaczego obrabiarki są, wydaje się ponad miarę, tak ciężkie i masywne, choć konstrukcyjnie mogły by być bardziej finezyjne? To stuknijcie młotkiem w pudło z cienkiej 1mm blachy a zrobione na przykład z 15-ki. W którym wzbudzicie większe drgania? Jasne że w tym z cienkiej, bo do wzbudzenia drgań dużej masy potrzebna jest dużo większa energia. Poza tym ich częstotliwość rezonansowa jest o rzędy wielkości mniejsza niż cienkich membran, a harmoniczne szybciej gasną. Dlatego w praktyce naszych małych tokareczek ,gdzie zwłaszcza masa suportu jest znikomo mała, a przecież tylko swoim ciężarem leży na pryzmach łoża, na generujące się zwłaszcza w procesie przecinania (ale nie tylko) wibracje cudownym lekarstwem okazuje się często położenia na sankach poprzecznych relatywnie ciężkiego pucka stali (lub czegoś podobnego, hantla, itp,..), oczywiście tak by można je było dalej przesuwać i nie przeszkadzał w toczeniu. Spróbujcie kiedyś. 4 - maszyna prawdopodobnie ma duże luzy lub zużycie łożysk wrzeciona, co skutkuje podnoszeniem się i nabieganiem wałka na nóż. To powodowało chwilowe ustawienie ostrza poniżej osi toczenia, a przy jego zerowym kącie natarcia, chwilowo zmieniał się on na kąt ujemny, co jeszcze bardziej pogarszało warunki skrawania. Widać to dobitnie zwłaszcza w zwolnionej części filmu: 3:48, 5:13, 5:46, zresztą jak się uważnie przyjrzymy, to każde zwiększenie nacisku przez nóż, nawet małe, powoduje "bujanie" się wałka. Co prawda część winy za to ponosi także plastyczność metalu w którym pod naciskiem siły szczęki wygniatają swoje ślady, zmniejszając siłę zacisku (prawie zawsze szczęki uchwytu, zwłaszcza o małych, "ostrych" powierzchniach dociskowych zostawiają swoje ślady, nawet na twardej stali), ale gro winy ponoszą luzy, bo jego średnica raczej nie pozwala na wyboczenie pod naciskiem noża, jak to często się zdarza z cieńszymi daleko wystawionymi wałkami.. Na moje oko gdyby pewniej zamocował wałek, podparł go, zmniejszył obroty, i zwiększył oraz nie przerywał posuwu, to nawet miałby szansę ten wałek przeciąć. A jaka ta geometria przecinaka ma być? Obecnie, w dobie coraz większego udziału w obróbce noży składanych, w których geometria ostrza wymiennej płytki jest w zależności od przeznaczenia ustalana na gotowo w fazie jej produkcji, docelowych geometrii ostrza, zwłaszcza kształtu powierzchni natarcia może być baaardzo wiele. I choć kształt jednych jest technologicznie zasadny, a innych "najnowszych rodzajów" to czysty pic na wodę jak coraz to nowe "formuły" proszków do prania (a naprawdę różniących się tylko kolorem "kuleczek"), to i tak nie mamy przy nich nic do roboty. https://www.google.pl/search?q=parting+carbide+insert+geometry&biw=1188&bih=742&source=lnms&tbm=isch&sa=X&ved=0ahUKEwjA88r3t6XLAhWlIpoKHXlcCz4Q_AUIBygB Ale dla noży ze stali szybkotnących (HSS, HSSCo, SWW, itd) w tym większości listew tnących, oraz noży z lutowaną płytką, które nas najbardziej interesują, geometria jest w zasadzie jedna - podstawowa. A ma ona na celu tak ukształtować ostrze narzędzia, by stykało się ono ze skrawanym materiałem tylko jedną częścią - główną krawędzią skrawającą. Pozostałe nie powinny dotykać materiału(trzeć) A wygląda ona tak Jak widzimy wszystkie krawędzie i powierzchnie oprócz głównej skrawającej i natarcia są tak ukształtowane by nie stykać się z przecinanym materiałem. Jest to nieodzowne z tytułu nie za dużej w porównaniu z innymi nożami wytrzymałości tak długiej i wąskiej konstrukcji, która miałaby problemy z wytrzymaniem zbyt dużych naprężeń. Jedynie niektóre listwy tnące z gotową geometrią mają równoległe pomocnicze krawędzie skrawające(boki) stykające się ze ścianami wycinanego w materiale rowka. W teorii wystarczy że kąty α'1, α'2, K'r1, K'r2 będą miały wartość 1-2°, ale w praktyce amatorskiego ręcznego szlifowania zazwyczaj mają więcej, 2-3°, nawet do 5°. Oczywiście im większy on jest tym słabszy jest przekrój w tym miejscu. Kąt głównej powierzchni przyłożenia α może mieć więcej, w zależności od szczególnych potrzeb nawet do 30°, ale podobnie jak wyżej - im będzie on większy, tym mniejszy będzie przekrój i wytrzymałość na złamanie ostrza w newralgicznym miejscu. Jednym z kryteriów jakie musimy wziąć pod uwagę przecinając konkretna średnicę i materiał by opory skrawania były możliwie minimalne, jest szerokość jaką wycina w materiale ostrze (nie długość głównej krawędzi skrawającej bo ta może być nierównoległa do osi toczenia Kr≠90°) Generalna zasada jest taka: im mniejsza średnica - tym wąższe ostrze, Ale przy użyciu wąższych niż 2 mm, np do przecinania średnic poniżej Ø10mm, trzeba już zachować szczególną ostrożność. Najczęściej jednak w amatorskiej robocie używa się o szerokości 2÷4mm, a najlepiej mieć kilka z różnymi szerokościami do różnych zastosowań. Typowe wartości są przedstawione w tabeli Powierzchnia natarcia może mieć kąt natarcia γ = 0°, ale lepiej sprawują się takie z najlepiej szerokim kroplowym rowkiem wiórowym i dodatnią wartością γ około 15°, lepiej po nich spływa wiór zwijając się często grzecznie w rolkę (jak to widać na filmie) Przecinak możemy wyszlifować sobie z kwadratowej lub lepiej prostokątnej stalki, szlifując boki zgrubnie najpierw czołem ściernicy(obwodem), a potem wyprowadzając właściwe kąty poprzez dostawianie szlifowanego ostrza lekko pod kątem do jej płaszczyzny, i wykonując zwrotne ruchy wzdłuż jej promienia. jak wykonać kanałek wiórowy było wcześniej. (temu nożowi praktycznie brak skosów, widać na przeciętej powierzchni ze tarł bokami, trzeba by skorygować) z listwy tnącej HSS o prostokątnym przekroju podszlifowujac boki, rowek, i czoło (do której mocowania potrzebna jest oprawka mocowana w imaku) z praktycznie gotowej, o geometrycznie trapezowym przekroju listwy, ewentualnie ostrząc ją tylko i wykonując rowek wiórowy, http://chronos.ltd.uk/acatalog/New--Clamp-Type-Parting-Tool-s-with-Chipbreaker-Blade--5--cobalt-.html https://www.youtube.com/watch?v=w0N6K9y2i2M Również dla noży z lutowanymi płytkami trzeba stosować te same zasady geometrii, bo dostępne w handlu egzemplarze to zazwyczaj surówki bez wyprowadzonych kątów i rowka wiórowego, Pamiętając oczywiście o stosowaniu właściwych ściernic, i nie przegrzewając płytki (o czym już mówiliśmy). Jedynie w celu ochrony naroży głównej krawędzi skrawającej przed wykruszaniem dobrze jest zrobić na nich małe 0,2-0,4mm pionowe fazki jak w profilu graniastym lub małe promienie naroży r , a ostrą krawędź skrawającą lekko zatępiamy osełką. tu mamy niezbyt wypracowaną geometrię, bardzo szeroki, z prostą krawędzią skrawającą nóż, nieznane parametry obrotów i posuwu, igiełkowe wióry świadczące o drganiach i skrobaniu, i niestety efekt... Bardzo dobrze przecina się listwami tnącymi z wymiennymi płytkami o szerokości roboczej zaczynającej się typowo od 2mm. Są one niestety drogie, ale za to bardzo odporne na uszkodzenia, co najwyżej wymienia się uszkodzona płytkę, a z mojego doświadczenia (mam dwie, na płytki 2 i 3mm) wybaczają wiele błędów i są mało wrażliwe na drgania. niektóre płytki mogą też skrawać bocznymi krawędziami Podobne i innego kształtu płytki są mocowane także w oprawkach typu trzonkowego do bezpośredniego mocowania w imaku jak zwykłe noże Niektórzy koledzy amatorzy wpadli na pomysł by zamiast kupować drogie listwy i płytki, wykorzystać niepotrzebne, uszkodzone, np pęknięte.. piły tarczowe z węglikowymi płytkami o pasującej do cięcia geometrii. jak to zrobić widać na filmie. Niekiedy nawet nietanie oprawki do listew można zastąpić tańszymi lub własnej roboty zamiennikami.. http://bbs.homeshopmachinist.net/threads/66132-Parting-tool-holder-for-0-1-quot-x-0-46-quot-x-4-25-quot-blade-on-9x20-lathe-turret-post?s=9da5d7a67ce0d7ba53a297c1d5646aa7 A domowym sposobem ominięcia drogich oprawek do listew tnących z wymiennymi płytkami jest dorobienie im trzonka do bezpośredniego mocowania w imaku, przykręconego do niej na odpowiedniej wysokości by utrzymać wysokość ostrza do osi. Otwory pod śruby w hartowanej listwie wiercimy widiowym wiertłem do betonu zaszlifowanym na ostro (pow. przyłożenia) jak zwykłe wiertła do stali, chłodzić naftą. (sam wiele razy tak robiłem) lub typowym z węglika spiekanego (ostatecznie ścierniczką) Gdy nie mamy palnika plazmowego do wycinania można z powodzeniem użyć szlifierki kątowej ("bosza") z tarczą do przecinania stali (okulary!) Jak więc koledzy widzą, demonizowane często przez niepowodzenia pierwszych prób przecinanie wcale nie jest takie straszne, jak zna się zasady. 10 przykazań: 1 - właściwie wyprowadzona geometria noża, 2 - dobrana do średnicy szerokość ostrza, 3 - nóż ustawiony na wysokości osi toczenia i prostopadle do niej 4 - możliwie krótko, lub podparty daleko wystawiony materiał, 5 - materiały o bardzo małej średnicy a dużej długości podparte podtrzymką by zapobiec ich wyboczeniu, 6 - właściwie dobrane obroty, (zawsze lepiej mniejsze), 7 - nie za powolny, zdecydowany i równomierny posuw, redukowany przy końcu cięcia, 8 - smarowanie/chłodzenie w celu zmniejszenia tarcia i powstawania narostów, 9 - wykasowane luzy łożyskowania wrzeciona, luzy jaskółek, 10 - ewentualne dociążenie masy suportu (w małych maszynkach) ... i 11-te, najważniejsze... SPOKÓJ... Myślę, że te podstawowe już teraz będą znane, a w razie pytań czy wątpliwości - służę pomocą. Kolegom próbującym pierwszy raz zalecałbym zacząć od przecinania najpierw drewna, aluminium, mosiądzu, by "otrzaskać się" z tym procesem, a potem miękkiej stali. Dla kolegów nie posiadających frezarki wskażę prosty pomysł, wymagający niewiele inwencji i nakładów, a pozwalający na nawet dość zaawansowane frezowanie w tokarce z wykorzystaniem obrotnicy tokarki http://www.cnc.info.pl/topics56/jak-zamocowac-vt49816.htm http://www.cnc.info.pl/topics56/po-co-kupowac-frezarke-gdy-mamy-tokarke-vt15740.htm https://www.google.pl/search?q=frezowanie+w+tokarce&tbm=isch&tbo=u&source=univ&sa=X&ved=0ahUKEwiGpe21oqXLAhXHjSwKHTUuCd0QsAQILA&biw=1188&bih=742#tbm=isch&q=milling+a+lathe .
-
Możliwe, ale znalazłem je na stronie motocyklowych wariatów więc wszystko jest możliwe... https://www.pinterest.com/pin/28780885096265010/ https://www.google.pl/search?q=Double-duty+%23motorcycle+with+twin+%23sidecars.+%28say+what%3F%29&source=lnms&tbm=isch&sa=X&ved=0ahUKEwj2ksDtyZzLAhViM5oKHZplDjQQ_AUIBygB&biw=1188&bih=750
-
Nie sądzę, spójrz na mocowania obu przyczep do motocykla, musiałyby być idealnie lustrzane obrazy.
-
No i super wyszło! To kiedy nalot na Paryż?
-
A teraz o ściernicach, szlifierkach, i ostrzeniu. Zazwyczaj ściernice oznaczone są według podobnego schematu, przy czym różnią się one nieco w zależności od firmy gdzie - Typ ściernicy oznacza jej znormalizowany kształt, jest ich duża różnorodność, ale my do ostrzenia za pomocą szlifierki stołowej zasadniczo używać będziemy Typu 1, oraz docelowo w/g potrzeb Typu 6, 11, 12.. (w/g katalogu Andre http://www.andre.com.pl/katalog-produktow/narzdzia-cierne-ze-spoiwem-ceramicznym ) Ściernice te mają różne gatunki nasypu, z których wyróżniamy 3 grupy podstawowych materiałów ściernych używanych do ostrzenia noży tokarskich i innych narzędzi: - a) - Elektrokorundy (korundy syntetyczne) - αAl2O3 Elektrokorund w różnych odmianach jest najczęściej stosowanym ścierniwem. Wytapiany jest w piecach elektrycznych w temp. powyżej 2000° C z boksytu, względnie tlenku glinu. - 95A - Elektrokorund zwykły (brązowy) Otrzymywany jest z boksytu. Zawiera 95% Al2O3, ~ 3% tlenku tytanu (TiO2) oraz ~1-2% innych domieszek. Jest najbardziej wytrzymałym elektrokorundem charakteryzującym się wysoką ciągliwością. Stosowany do przecinania i zgrubnego szlifowania niskostopowych stali, stali nierdzewnych, żeliwa, szczególnie przy dużych naddatkach zbieranego materiału. - 97A - Elektrokorund półszlachetny (szary) Otrzymywany jest z kalcynowanego boksytu oraz dodatku w postaci tlenku glinu. Zawiera 97% Al2O3. Charakteryzuje się średnią twardością i wytrzymałością. Stosowany jest do szlifowania precyzyjnego i do szlifowania narzędzi. - 99A - Elektrokorund szlachetny (biały) Otrzymywany jest z czystego tlenku glinu. Jest najczystszym elektrokorundem zawierającym powyżej 99% Al2O3. Charakteryzuje się dużą twardością i kruchością. Stosowany do szlifowania precyzyjnego, np.: szlifowanie płaszczyzn, szlifowanie cylindryczne, ostrzenie narzędzi skrawających. - CrA - Elektrokorund chromowy (różowy) Otrzymywany jest z tlenku glinu z dodatkiem tlenku chromu w ilości do kilku procent. Charakteryzuje się dużą twardością i wytrzymałością, większą od elektrokorundu szlachetnego. Stosowany do precyzyjnego szlifowania stali wysokostopowych, do ostrzenia narzędzi skrawających. - M - Monokorund (szary) Otrzymywany z boksytu metodą redukcyjną. Zawiera ponad 99% Al2O3. Charakteryzuje się wysoką mikrotwardością i wytrzymałością mechaniczną. Posiada wyjątkową zdolność do samoostrzenia. Stosowany do szlifowania wysokostopowych stali szybkotnących i do ostrzenia narzędzi. Szczególnie nadaje się do szlifowania profili złożonych. - ZrA - Elektrokorund cyrkonowy Otrzymywany jest z tlenku glinu lub boksytu z dodatkiem tlenku cyrkonu. Charakteryzuje się najwyższą wśród elektrokorundów ciągliwością i wytrzymałością mechaniczną. Stosowany do wysokowydajnego szlifowania żeliwa, do szlifowania półfabrykatów stalowych z dużymi naciskami. - b - Węgliki krzemu (nazywane też karborundem) - SiC Otrzymywany w piecach oporowych w procesie syntezy wysokiej czystości piasku kwarcowego oraz koksu naftowego. Drugi, po diamencie pod względem twardości. - 99C - Węglik krzemu zielony Wysokiej czystości węglik krzemu jest barwy zielonej i zawiera min. 99% SiC. Stosowany do szlifowania węglików spiekanych, ceramiki, kamieni, do ostrzenia narzędzi skrawających z ostrzami z węglików spiekanych. - 98C- Węglik krzemu czarny Zawiera 98% SiC i więcej domieszek. Stosowany podobnie jak 99C do szlifowania węglików spiekanych, materiałów ceramicznych, betonu, kamienia, do zgrubnego szlifowania odlewów z twardego i kruchego żeliwa białego oraz do przecinania betonu, kamienia, żeliwa białego. - c) Diamentowe - © Zarówno z diamentów naturalnych, jak i bardziej powszechnych i tańszych diamentów syntetycznych. Najtwardszy ogólniedostępny materiał ścierny. (są jeszcze borazony, ale bardzo drogie) Przy czym do szlifowania trzonków noży lutowanych najlepiej najdają się 95A, 97A, do noży ze stali szybkotnącej (w tym HSS) nadają się najlepiej 99A, CrA, M, do węglików spiekanych 99C, 98C, diamentowe. Nas w zasadzie najbardziej interesować będą z uwagi na kompromis cena/przydatność cztery z nich: 95A - korundowa do szlifowania miękkiego trzonka, 99A - korund szlachetny do wyszlifowania i ostrzenia noży ze stali szybkotnącej (HSS) (opcjonalnie) 99C - węglik krzemu do ostrzenia płytki z węglika spiekanego diamentowa T6, 11 lub lepiej T12 - do dopieszczania ostrza z węglika (opcjonalnie) Oczywiście zamiast podanych można stosować i pozostałe z danej grupy zastosowań, ale te stanowią niezbędną podstawę do ostrzenia danego rodzaju noża. Można także HSS ostrzyć ściernicami do węglika, ale ze względu na mniej odpowiednią dla HSS twardość ich spoiwa szybciej się będą one zużywały(sypały). ale nie polecam szlifować ściernicą diamentową czy 99C miękkiej stali trzonka, bo szybko się one zalepią i będą wymagać obciągnięcia (diamentowania) aby móc nadal wydajnie szlifować. Jak wygląda zalepiona ściernica korundowa możecie zobaczyć poniżej Praktycznie na szlifierkę stołową poza podstawowym układem ściernica 95A z jednej strony a 99C z drugiej, można zamontować nawet 3 ściernice na raz uzyskując super zestaw szlifierski, np ściernica 95A do trzonków z lewej, 99C + diamentowa do spieków z prawej, o ile długość części wałka do ich mocowania na to pozwoli. Można to zrealizować w ten sposób: inne http://www.robohippy.net/featured-article/ Trzeba tylko dorobić lepsze, większe stoliki. W ogóle fabryczne stoliki(podstawki) w typowych marketowych szlifierkach stołowych z punktu widzenia ostrzenia noży tokarskich są bezużyteczne z kilku powodów. Przede wszystkim są niestabilne, zrobione ze zbyt cienkiej, wygiętej tylko kątowo blaszki, której zamocowanie (prowadnica) jest bardzo wiotka, przykręcona do równie mało sztywnej osłony ściernicy, co przy szlifowaniu większej powierzchni np trzonka prowadzi do powstawania drgań (sprężynuje). Ich mała szerokość także nie stanowi pewnego oparcia dla dużego dość trzonka, ani nie pozwala na swobodne i pewne ustawienie pod dowolnym kątem do czoła ściernicy, nie mówiąc już o przystawieniu go do jej bocznej powierzchni, bo jej nie obejmuje (jak to widać na moim rysunku powyżej). Konstrukcja tych podstawek nie pozwala także na dokładne ustawienie pochylenia w stosunku do czoła ściernicy (kąt przyłożenia α, czy pomocniczy kąt przyłożenia α') Sugerowałbym kolegom wykonanie w sumie prostych ale bardzo użytecznych nawet dla doświadczonych szlifierzy, uniwersalnych, nie tylko do ostrzenia noży podstawek z grubszej np ≠5-7mm blachy, aluminium, a nawet sztywnej grubszej sklejki, których różnorakie konstrukcje można zobaczyć poniżej. I wybrać sobie wzór możliwy do wykonania we własnym zakresie. http://www.cnc.info.pl/topics80/tarcza-do-ostrzenia-widi-vt62985,10.htm poczynając od najprostszej, po mniej lub bardziej złożone konstrukcje, choć tez nie jakiś technologiczny kosmos http://www.cnc.info.pl/topics85/ostrzalka-lub-szlifierka-stolowa-vt49960.htm https://www.youtube.com/watch?v=Xbggxj2kgyc https://www.google.pl/search?q=Homemade+Grinder+Tool+Rest&source=lnms&tbm=isch&sa=X&ved=0ahUKEwin99Wjy5jLAhXlJZoKHQ1JAugQ_AUIBygB&biw=1214&bih=750#imgrc=_ Gorąco namawiam kolegów, bo takie proste usprawnienie wielce ułatwi poprawne wykonanie dobrej geometrii noża nawet mało doświadczonym, a na pewno będzie dużo bezpieczniejsze. A zastosowanie w podstawce prostej poprzecznej prowadnicy (nawet ze złożonych i skręconych śrubami płytek) dla suwaka z ustawianym kątem podpórki dla noża, pozwala na wykonanie precyzyjnych prostoliniowych szlifów pod właściwym pożądanym kątem. http://www.steves-workshop.co.uk/tools/grindingrest/grindingrest.htm ************************************************** Naukę ostrzenia dla ułatwienia zaczniemy od wykonania ze stalki noża prostego bocznego, o prostej do wykonania geometrii, bardzo dobrego do aluminium, miedzi, mosiądzu, ale także i miękkiej stali możemy wzorem noży lutowanych przyjąć kąt przystawienia głównej powierzchni przyłożenia Kr=70°, a kąt pomocniczej płaszczyzny przyłożenia K'r=20°, kąt naroża εr wyniesie wtedy 90° (180°- {70°+20°}) zaczniemy od wykonania głównej płaszczyzny przyłożenia 1 z kątem przystawienia Kr Właściwy kąt głównej powierzchni przyłożenia (α=10-12°) uzyskujemy przez odpowiednie pochylenie stolik w stosunku do czoła ściernicy, z uwzględnieniem krzywizny obrysu samej ściernicy zależnym od jej średnicy D (przez co wyszlifowana powierzchnia będzie lekko wklęsła ale to nie przeszkadza) Następnie także czołem ściernicy szlifujemy pomocniczą powierzchnię przyłożenia 2 z kątem K'r , kąt pomocniczej powierzchni przyłożenia (α') może pozostać taki sam jak głównej, lub dla wzmocnienia zmniejszony do 8°. następnie dla wzmocnienia wierzchołka noża załamujemy go robiąc nieduży promień (r) (może też być w formie płaskiej 0,5-1mm fazy) można to zrobić także ręcznie na osełce Ostatnią operacją ostrzenia 3, jednocześnie dość trudną a bardzo ważną, będzie zaszlifowanie powierzchni natarcia z odpowiednim kątem (γ), z zachowaniem zarazem właściwego kąta pochylenia głównej krawędzi skrawającej (λs). Jako że do tej operacji kładziemy nóż nie na podstawie, a na prawym boku, właściwy kąt natarcia γ=12°-18° zapewni nam odpowiednie pochylenie stolika (podobnie jak wcześniej do uzyskania odp. kata przyłożenia), a właściwy (dodatni) kąt pochylenia głównej krawędzi skrawającej λs do 30° dla aluminium, i 8°do15° dla stali, zapewni skośne ustawienie na stoliku osi trzonka noża do czoła tarczy ściernicy. Przy pewnym doświadczeniu można to wykonać także "pod palec", ale ja pokazuję ten film by mieli koledzy lepszy pogląd na zagadnienie (są tam też inne filmy o ostrzeniu) https://www.youtube.com/watch?v=hrDr4rYLiAk https://www.youtube.com/watch?v=dRyqIm5JR5s https://www.youtube.com/watch?v=HTQ46NMMc88 https://www.youtube.com/watch?v=HTQ46NMMc88 Przykładowe kąty poszczególnych powierzchni zalecane dla wybranych rodzajów skrawanego metalu podano w tabelce poniżej. Ale nie są one bezwzględnie krytyczne i wystarczy wykonując ostrzenie zachować przybliżone wartości Można także zamiast klasycznego szlifowania całej powierzchni natarcia pod kątem γ wyszlifować krawędzią ściernicy, koniecznie wzdłuż głównej krawędzi skrawającej (z zerowym lub ujemnym kątem pochylenia λs) rowek/kanałek wiórowy, opierając na stoliku nóż na wierzchołku ostrza, i dosuwając powierzchnię natarcia do krawędzi ściernicy, z główną krawędzią skrawającą ustawioną pionowo (prostopadle do powierzchni stolika). Osobiście uważam to za opcję lepszą, bo sam rowek wiórowy zapewnia nam już dodatni kąt powierzchni natarcia, a jednocześnie pełni funkcję łamacza/zwijacza wióra. Rowek wiórowy może mieć zarys wycinka okręgu - okrągły, z większym ale mniej wytrzymałym mechanicznie dodatnim kątem γ powierzchni natarcia, zależnym od wartości promienia r krawędzi ściernicy, nadającym się do skrawania miękkich materiałów i metali jak aluminium, miedź, brązy, wyżarzany mosiądz, tworzywa sztuczne, twarda guma, itp.. lub kroplowy (jak odwrócony profil płaskowypukły), z mniejszym katem powierzchni natarcia γ, ale za to dużo wytrzymalszy, bardziej nadający się do skrawania stali, gdzie wartość kąta natarcia γ jest różnicą kąta 90° a kąta przystawienia trzonka noża do czoła ściernicy x γ = 90°- x° różne przykłady rowków wiórowych Kto chce sobie nieco pogłębić temat może poczytać w linkach https://books.google.pl/books?id=WCYDAAAAMBAJ&pg=PA150&lpg=PA150&dq=how+to+grind+a+lathe+bit+chip+breaker&source=bl&ots=uOUoU0ThEz&sig=-g04FiB_OcsnNpIVynzimdmHV6k&hl=en&sa=X&ei=7xAIUe2uDsOO2wWuyYGABQ#v=onepage&q=how%20to%20grind%20a%20lathe%20bit%20chip%20breaker&f=false http://lotek.info/proj/dead_center/ Jak koledzy widzą naostrzenie noża do wzdłużnego toczenia nie jest wcale czarną magią, wymaga tylko troszkę wiedzy, podstawowego sprzętu, i nieco manualnych zdolności na których, jak śmiem sądzić, modelarzom nie zbywa. Analogiczne zasady stosujemy do innych rodzajów noży poza przecinakami i wytaczakami, o czym bedzie dalej. Od biedy rowek wiórowy można wykonać i w taki sposób, ale wymaga to pewnej ręki, i tego nie polecałbym. http://www.practicalmachinist.com/vb/south-bend-lathes/easy-hss-chip-breaker-219269/ Kąty przyłożenia i rowki wiórowe w nożach odsadzonych bocznych których będziemy używać do toczenia najczęściej wykonujemy podobnie A noże VHM z płytkami z węglików spiekanych? Ogólnie zasady ostrzenia są prawie identyczne, należy tylko odpowiednie części noża szlifować na właściwych ściernicach, i nie stosować za dużych katów natarcia z racji większej kruchości spieku. Główną powierzchnię przyłożenia w nożach z lutowana płytką szlifujemy w dwóch fazach: - najpierw pod większym kątem αn2= 10°-12° sam miękki trzonek na ściernicy 95A, bez szlifowania płytki VHM, - potem pod mniejszym kątem αn1 = 5°-7° powierzchnię przyłożenia płytki ze spieku VHM na ściernicy 99C Jeśli mamy do dyspozycji również ściernicę diamentową to kąt αn1 płytki szlifujemy na 2 razy: - w pierwszym zabiegu na ściernicy 99C pod katem αn1= 7°-10° (kąt ten stosuje się również do mocno szczerbatych płytek), - w drugim zabiegu na ściernicy diamentowej pod katem αn1= 5°-7° już na gotowo. Orientacyjne wymiary rowka(kanałka) wiórowego w zależności od głębokości skrawania (ap) i prędkości posuwu (fn) mamy w tabelce poniżej. Oczywiście do amatorskich zastosowań na słabonapędowej obrabiarce wystarczy przyjąć średnią lub największą wartość z pierwszego rzędu (dla ap =1mm), i lekko dodatnią lub nawet zerową wartość kąta natarcia ( widać to na zdj. poniżej), co wzmocni krawędź skrawającą. Którą po naostrzeniu należy dodatkowo lekko stępić diamentową (lub z węglika krzemu) osełką by nie dopuścić do wykruszania się zbyt cienkiej krawędzi ostrza. Uniwersalnym, najczęściej w robotach tokarskich używanym, będzie profil odsadzonego noża bocznego NNBe z dobrze skrawającym stal kroplowym rowkiem wiórowym wzdłuż głównej krawędzi skrawającej, o niedużym kącie natarcia, ale za to zapewniającym ostrzu dużą wytrzymałość, jaki widać na zdjęciu poniżej. Wykonanie podobnej geometrii noża NNBe naprawdę nie jest takie trudne, nawet dla początkującego tokarza, jeśli się zna kolejne kroki (j/w), a z każdym przeostrzeniem będzie coraz doskonalsze. Troszkę inaczej wygląda proces ostrzenia dwu innych rodzajów noży; przecinaków i wytaczaków, a to ze wzgledu na ich szczególne warunki pracy i odmienną ogólną geometrię, chociaż główne zasady dotyczące samych ostrzy skrawających są identyczne. Zacznijmy od przecinaków. Przecinaki mają dość niekorzystną budowę pod względem wytrzymałościowym, ich część robocza jest bardzo wydłużona i wąska, przez co podatna na wyginanie na boki pod wpływem niezrównoważonych oporów skrawania. A przy ograniczonej (ze względu na wymiar h do osi) wysokości mają niewielki w porównaniu z trzonkiem dużo mniej wytrzymały na przeciążenia w porównaniu do innych noży przekrój poprzeczny. W dodatku pracuje w wąskiej zazwyczaj głębokiej szczelinie przecinanego materiału gdzie spływ i usuwanie powstającego wióra jest utrudnione. Wszystko to razem wzięte sprawia że przecinaki są dość delikatnymi, narażonymi na uszkodzenia narzędziami. W dodatku na proces cięcia mają wpływ także inne czynniki, takie jak sztywność i wielkość luzów maszyny, zwłaszcza luzy łożyskowania wrzeciona, jaskółek sań, wysunięcie, średnica, rodzaj i twardość przecinanego materiału, same parametry cięcia, a nawet masa maszyny(o czym wspomnimy dalej). jak sprawdzić luzy jaskółek przedstawia zdjęcie poniżej (analogicznie podważając dźwignią imak - tu akurat tylny) Jeśli mamy możliwość zaciskania śrubą lub dźwignią docisku suportu do łoża w celu jego unieruchomienia, to warto to przy przecinaniu uczynić - im sztywniejsza maszyna tym lepiej dla procesu przecinania. Podobnie z zaciskiem na listwie jaskółki sanek narzędziowych (przy poprzecznych kasujemy tylko nadmierny luz). http://www.model-engineer.co.uk/sites/7/images/member_albums/86530/571926.jpg Z tego powodu proces przecinania jest swoistym testem sztywności i poprawności regulacji luzów nowej, a zużycia i ogólnej kondycji (zwłaszcza łożyskowania wrzeciona) używanych tokarek. Im szerszym przecinakiem możemy bezproblemowo, bez wzbudzania szkodliwych drgań, przecinać stal - tym ocena kondycji wyższa. Niestety nasze hobbystyczne obrabiarki nie mogą pochwalić się najlepszymi rezultatami w tym zakresie. Dlatego wykonaniu prawidłowej geometrii przecinaka podczas szlifowania, która zapewnia nam jak najmniejsze opory skrawania powinniśmy poświecić nieco więcej uwagi i staranności. A potem właściwemu przebiegowi samego procesu cięcia. Poniżej prezentuję film jak właściwie dobrane parametry i narzędzie w zasadzie bezproblemowo(nie licząc samej końcówki) pozwalają na przecięcie dość dużej średnicy wałka z wywierconym współśrodkowym otworem (co też ma znaczenie, o którym powiemy dalej). Jak widać pomimo dużej średnicy do przecięcia bardzo wydłużoną częścią roboczą noża (tu akurat listwy tnącej, ale to bez znaczenia) proces cięcia idzie sprawnie i bez komplikacji, o czym może świadczyć ładnie spływający wstęgowy wiór, brak odgłosów wzbudzania się niepożądanych drgań, oraz prosta i gładka płaszczyzna po cięciu. Materiał wystawiony możliwie krótko, obroty nie za duże, dobrze dostosowane do dużej średnicy w myśl dobrej dla ręcznego cięcia zasady: im większa średnica - tym mniejsze obroty, ręczny posuw narzędzia odpowiedni,nie za szybki, ale i nie wolny(o tym dalej), oraz zastosowane chłodzenie które prócz obniżania temperatury również smaruje powierzchnię natarcia noża, polepszając spływ po niej studzonego wióra, i równocześnie wydatnie zmniejszając tendencję do powstawania niepożądanego narostu na krawędzi skrawającej. Wiec skoro tak dobrze szło, to czemu w końcowej fazie docinania nóż nie wytrzymał ? Na to niekorzystne zjawisko złożyło się kilka przyczyn. Aby je właściwie zanalizować musimy cofnąć się nieco do teorii. Otóż jak już poznaliśmy ze wzoru, prędkość skrawania vc zależy od obrotów n, i średnicy Dm skrawanego materiału. Tu obroty n są stałe, więc przekształcając wzór prędkość skrawania vc zależy od średnicy skrawania Dm . Ale średnica ΔDm zmniejsza się wraz wcinaniem się noża w materiał, co analogicznie skutkuje zmniejszającą się w sposób proporcjonalny prędkością skrawania vc2. Malejąca prędkość skrawania pogarsza spływ wióra z powierzchni natarcia, bo prędkość nabiegania materiału na nóż maleje, a utrzymany stały posuw fn przy malejącej średnicy skutkuje proporcjonalnym wzrostem pozornej głębokości skrawana ap, co w sumie prowadzi do narastania siły oporów skrawania Fc działających na nóż, W dodatku spiętrzanie się wióra na coraz większej powierzchni ostrza zmienia kierunek jej wypadkowego wektora ΔFc na bardziej pionowy niż na początku(Fc), przez co działa ona na mniejszy przekrój L2 części roboczej, wynikający z pochylenia płaszczyzny przyłożenia o kąt α. Do tego dochodzi jeszcze zjawisko występujące w samej końcówce procesu docinania materiału z współśrodkowym otworem, polegające na plastycznym odkształcaniu się pierścienia coraz cieńszej, pozostałej do przecięcia warstwy materiału. W praktyce naciskające na plastycznie niestabilną warstwę ostrze zamiast skrawać bardziej trze o nią, wybrzuszając ją w światło otworu, aż do momentu przekroczenia granicy jej wytrzymałości na rozciąganie. Następuje wtedy nagłe przebicie tej warstwy, a uwolniona gwałtownie siła nacisku powoduje nagły skok ostrza Δfn w światło otworu, zazwyczaj o wartość luzów śruby sanek poprzecznych suportu, łożysk wrzeciona, i ew. ugięcia samego noża i materiału pod nożem (w zależności od ich wiotkości). Może to być czasem milimetr i więcej, zależy od powyższych. A jako, że przecinany materiał obraca się nadal, to pozostała część niedociętego jeszcze pierścienia materiału nabiegając na powierzchnię natarcia łamie się i spiętrza, powodując duży skokowy wzrost siły oporu skrawania ΔFc. Jeśli wzrost tej siły będzie dostatecznie duży, to może przekroczyć wytrzymałość na ścinanie przekroju ostrza w punkcie jej przyłożenia, co skutkuje pęknięciem i wyłamaniem "czubka" ostrza. Lub dokładając do tego wzmacniający moment długości dźwigni między miejscem przyłożenia siły Fc(na ostrzu) a punktem zamocowania (podparcia) noża w imaku, może przekroczyć wytrzymałość na zginanie nawet pełnego przekroju części roboczej (który w tym miejscu jest mniejszy niż przy wierzchołku z racji geometrii ostrza), wyłamując ją w całości. Jak to było w przypadku tej listwy tnącej na filmie. Podobnie ma się sprawa przy przecinaniu pełnego materiału, tam jednak sprawcą destrukcji jest najczęściej urywanie się odcinanego detalu pod wpływem własnego ciężaru i siły odśrodkowej, przed całkowitym docięciem do osi, przez co pozostaje niedocięty czop, często przy okazji wyłamujący część ostrza. Tu również może nastąpić niepożądany "skok" noża do przodu jeszcze pogarszającysytuację, jednak w porównaniu do odcinania detalu (pierścienia) z centralnym otworem jak wyżej, zagrożenie jest dużo mniejsze. "Skok" w przypadku jest tym bardziej prawdopodobny, im większa jest odchyłka ustawienia wierzchołka ostrza pod osia toczenia, gdyż materiał czopu wykorzystując brak dostatecznej sztywności maszyny oraz pewną sprężystość ostrza noża i materiału, uwalniając nagle naprężenia nabiega na powierzchnię natarcia ostrza, prowadząc w skrajnych przypadkach do jego wyłamania. Dlatego starajmy się zawsze ustawiać wierzchołek ostrza dokładnie w osi toczenia. Jak można takim niepożądanym zjawiskom zapobiec, by docinając nie uszkodzić przecinaka? Według teorii - nie dopuszczając do zmniejszania się szybkości skrawania vc, poprzez zwiększanie aż do maksymalnych, obrotów n. Ale w mechanicznych obrabiarkach, z niesterowalnym w czasie rzeczywistym napędem jest to niemożliwe do zrealizowania, poza tym mogło by być niebezpieczne z powodu gabarytów, kształtu, czy niecentryczności zamocowanych mas (wibracje). Ewentualnie można zastosować mniejsze obroty na początku przecinania centrycznego detalu o dużej średnicy, a potem gdy ta znacznie się zmniejszy, do docinania zwiększyć je. Do bezpiecznego jednak poziomu. Nie zawsze jest to jednak możliwe. Cóż innego więc można zrobić? Można stopniowo (z wyczuciem) zmniejszać posuw narzędzia, a w końcowej już fazie docinania, kiedy czujemy że materiał zaczyna plastycznie ustępować i wybrzuszać się w światło otworu pod naciskiem ostrza, robić małe "przystanki" w posuwie, pozwalając tym samym na "wybieganie się" wióra, i stopniowe z każdym obrotem detalu automatyczne redukowanie się nacisku ostrza na pozostałą do przecięcia część("pierścionek"). Postępowanie takie, zmniejszające presję ostrza na materiał i redukując powstałe naprężenia, najczęściej zapobiega gwałtownemu jego "skokowi" w światło otworu podczas przebicia ścianki pierścienia, pozwalając na bezpieczne oddzielenie odciętej części od reszty. Tego właśnie zmniejszenia posuwu (i nacisku) przy docinaniu, zapobiegającego owemu "skokowi" nie zrobił operator na powyższym filmie, z widocznym dla wszystkich skutkiem. W redukcji zagrożenia "skokiem" pomaga także lekko skośna w stosunku do osi toczenia materiału głowna krawędź skrawająca, będąca wynikiem skośnego zaszlifowania głównej płaszczyzny przyłożenia (czoła przecinaka). czyli kąt przystawienia Kr różny od 90°. Zazwyczaj skos wykonywany jest w ten sposób, że wierzchołek ostrza jest od strony odcinanego detalu, by odcięta płaszczyzna nie miała niedociętych pozostałości czopa czy "pierścionka". http://www.model-engineer.co.uk/sites/7/images/member_albums/69121/458626.jpg Może też być odwrotny. Taka skośna linia głównej krawędzi skrawającej powoduje, że docinany "pierścionek" lub czop ma niejednakowej grubości stożkowaty kształt, o różnej w przekroju wytrzymałości na rozciąganie, zapobiegający jego wybrzuszaniu przez ostrze do światła otworu. Wówczas zamiast całą szerokością, przez "pierścionek" przebija się najpierw sam wierzchołek ostrza, odcinając tym samym detal od całości, a stopniowo wraz z posuwem noża ukośnie skrawana reszta stożka zapobiega tak niepożądanemu "skokowi" przecinaka. Wartość kąta przystawienia ostrza Kr nie może być jednak za bardzo różna od 90°, bo podczas cięcia będzie spychać ostrze w kierunku wierzchołka powodując cięcie materiału po łuku, https://john5293.files.wordpress.com/2014/03/2019-parting.jpg?w=300&h=225.jpg co może się skończyć pęknięciem twardego ale kruchego ostrza. Główna krawędź skrawająca przecinaka może też mieć inny, bezpieczniejszy dla naroży kształt (a, b ), oraz rzadziej spotykany, odcinający "pierścionek" czy czop jednocześnie od obu ścianek materiału - kształt c (niektóre listwy tnące z półokrągłą powierzchnią natarcia), a. półokrągły, b. graniasty(boczne fazy) c. wklęsły cdn..