
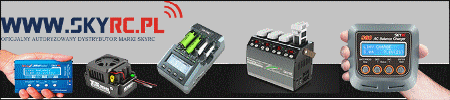
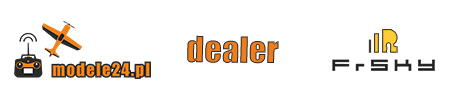
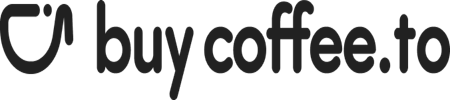
-
Postów
1 808 -
Rejestracja
-
Ostatnia wizyta
-
Wygrane w rankingu
24
Treść opublikowana przez Czaro
-
Spróbuj wygrzać gotowy kadłub, chociażby na kaloryferze. Po moich doświadczeniach stwierdzam, że jest za dużo zmiennych, żeby od razu znaleźć rozwiązanie :/ W międzyczasie składzik ze skrzydłami nam się trochę rozrósł
-
Drugą? Pffff! Od tamtego czasu powstały kolejne cztery kadłuby Przede wszystkim szczelniej zamykamy formę i dajemy mniejsze ciśnienie. To troszkę pomaga, ale niewiele. Najwyraźniej przy nacisku 2-3bar nie da się utrzymać tego legendarnego stopnia zbrojenia. Zresztą, jak się okazuje nie jest to potrzebne. Dotarłem do wyników badań przeprowadzonych kiedyś na MEiLu, które pokazały, że objętościowy stopień zbrojenia 50% (masowy 60%) jest optymalny przy kompozycie laminowanym bez docisku. Podczas laminowania z dociskiem im mniej żywicy tym większa wytrzymałość, a stopień zbrojenia w badanych próbkach dochodził do 75% udziału masowego. W naszych kadłubach jest 68 ... 70%, więc przestałem się tym przejmować. Szczególnie, że po zrezygnowaniu z tkaniny kierunkowej 30g/m2 kadłuby przestały trzeszczeć pod palcami i wszelkie próby statyczne znoszą bardzo dzielnie. Pomiędzy delaminaż, a ręcznik papierowy trzeba było dać folię z dziurkami. Rozwarstwianie się kompozytu niekoniecznie musi być efektem słabego przesycenia. Widzałem kompozyt, który miał właściwy stopień zbrojenia, a można go było rękami porozdzielać na poszczególne warstwy tkaniny. Przyczyną była niedotwardzona żywica. Kompozyt na Lh160 dopiero po trzech dniach w temp. pokojowej przestał się rozdzierać, natomiast próbka na Epolamie (nie pamiętam którym) dopiero po wygrzaniu w podwyższonej temperaturze osiągnęła dobrą wytrzymałość.
-
Mylar jest lepszy, daje ładniejszą powierzchnię i nie trzeba go pastować, ale ciężko dostać w małych ilościach. Grubość folii w okolicach 0,3mm Na natarciu lotki nie musisz mieć folii, docisk ze styroduru Ci wszystko załatwi. Potem tylko równo dociąć i oszlifować. Są minusy i to spore. Trudno będzie okleić równo cały rdzeń. 3M77 to klej kontaktowy i po przyklejeniu nie masz szans na poprawki. Potem jeszcze problem z syceniem tkaniny. Łatwiej to robić, jak masz ją rozłożoną na mylarze. Całą lotkę możesz laminować w jednym procesie. Poszukaj opisów o laminowaniu skrzydeł szybowców metodą VB, w dziale o DLG, albo na rcgroups.
-
Zaproponuję modyfikację propozycji Rafała: Skoro już wycinasz rdzeń styrodurowy, wytnij go o większej cięciwie. Następnie nożem dotnij do właściwej cięciwy, a ścinek który został użyj do dociśniecia natarcia lotki, zamiast listwy sosnowej. Reszta jak pisał Rafał. Dlaczego używasz dziurfolii zamiast sztywnego mylaru / pcv? Im cieńsza mata odsysająca, tym masz większą kontrolę co pod spodem i mniejsze fałdki. Używasz ręcznika papierowego, czy grubych sączków, dedykowanych do vacum?
-
Znalazłem wreszcie moje notatki i mogę dorzucić trzy grosze do dyskusji Przez długi czas w modelu stosowałem akumulator LiPo 2s 350mAh zasilający całe wyposażenie przez BEC z HK. W pewnym momencie zachciało mi się zmodyfikować układ tak, aby odbiornik RC był zasilany bezpośrednio z 2s, abym mógł kontrolować napięcie akumulatora przez telemetrię wbudowaną w odbiornik. Odbiornik JR RG631 zgodnie ze specyfikacją można zasilać takim napięciem, dwa serwa Dymond D47 w kadłubie również, natomiast serw Hyperon D09 w skrzydle już nie i dlatego użyłem regulatora ld 5V pomiędzy nimi, a odbiornikiem. Po wykonaniu przeróbek okazało się, że akumulator wyładowywał się podczas latania o wiele szybciej niż poprzednio. Sprawdzałem pobór prądu przy obu konfiguracjach zasilania: Zasilanie 2s: odbiornik + dwa serwa D47: pobór prądu w spoczynku 170mA, serwa w ruchu 450mA Zasilanie 2s: odbiornik + dwa serwa D47 + dwa serwa D09 za stabilizatorem liniowym: pobór prądu w spoczynku 180mA, serwa w ruchu 600mA Zasilanie 2s + BEC: odbiornik + dwa serwa D47: pobór prądu w spoczynku 120mA, serwa w ruchu 250mA Zasilanie 2s + BEC: odbiornik + dwa serwa D47 + dwa serwa D09 pobór prądu w spoczynku 130mA, serwa w ruchu 450mA Niby Dymondy można zasilać bezpośrednio z 2s, ale biorą sporo więcej prądu Pamiętacie dyskusję z wątku o zasilaniu szybowca F3F, o różnicy w sprawnościach układów obniżających napięcie? Bliżej mi do stanowiska, że mając na pokładzie 1700, czy nawet 2200mAh nie ma się czym przejmować. Jednak w przypadku tak małych pojemności akumulatorów zasilających modele DLG niższa sprawność stabilizatorów liniowych wzgl. układów BEC może mieć już znaczenie.
- 68 odpowiedzi
-
- dlg zasilanie
- 2s
-
(i 1 więcej)
Oznaczone tagami:
-
Dzięki! Dwunasty wygląda jeszcze lepiej Niebawem powstanie pewnie i czternasty, ponieważ trzynastka z wiadomych względów zostanie pominięta w numeracji. Tymczasem trwają testy już trzech nowych kadłubów: Dziś było -15, ale kto by się tam temperaturą przejmował, skoro było słońce i termika
-
Ile kilogramów i których żywic przerobiłeś, że sobie wyrobiłeś taką opinię?
-
Kadłuby 10 i 11 już za nami... Po jedenastej iteracji chyba wreszcie zbliżyliśmy się do optimum - węgiel 93 skośnie na wierzchu - kierunkowy węgiel HM 100 w środku - szkło 50 skośnie wewnątrz - dodatkowa warstwa węgla 93 pod skrzydłem - przód z 3w. kevlaru 60 i 1w szkła 50. Całość waży 38g i jest tak samo sztywna jak kadłub nr 10 z węgla kierunkowego 125 i podwójnej warstwy węgla 93 w centralnej części, który waży 41g. Belka ogonowa na całej długości jest bardzo sztywna i nie wgniata się pod naciskiem palców. Jest dobrze, tak jak to miało być Przymierzyłem wreszcie pakiet lipo Dualsky 520. Pasuje bardzo dobrze, wchodzi do noska nawet głębiej jak Rhino 360.
-
Nowa oficjalna strona Komisji Modelarskiej AP
Czaro odpowiedział(a) na Paweł Prauss temat w Ogłoszenia Aeroklubu Polskiego
No właśnie. Przejrzałem regulaminy i też mi się wydaje, że wystarczy być członkiem stowarzyszonym w jakimś AR, niekoniecznie członkiem zwyczajnym w sekcji. To zdecydowanie obniża koszty, bo np. w AZM jest to tylko 60zł/rok, w AW do tej pory było za darmo. -
Dzięki Paweł za wyszukanie cytatu @Pilatus: Rurka jest mosiężna, na końcu tępo zakończona kawałkiem plastiku, żeby nie przebijała balonu. Otworki do powietrza są dwa, jeden kilka cm od tępego końca, drugi kilka cm przed miejscem, w którym naciągnięty balon się kończy i doszczelniany jest do rurki. Poczyniliśmy w pracach kilka postępów: - Znajomy (dzięki Marku!) podesłał mi rzeczywiste wymiary pakietu Dualsky 520 2s: wym zew 17,8 x 14,2mm, przekątna: 19,4mm. Zrobiłem nowy klocek styrodurowy o tych wymiarach i wchodzi do noska kadłuba bez problemu. Zamówiłem takie dwa pakiety, za kilka dni przekonam się czy rzeczywiście będą pasować. - Zrobiliśmy kolejny kadłub - iteracja nr 9 :/ Tym razem odstopniowaliśmy tkaniny jednokierunkowe na końcu belki ogonowej zyskując trochę masy, którą wykorzystaliśmy na dołożenie w centralnej części pod skrzydłem kolejnej warstwy skośnej 93-ki. Efektem jest wzrost sztywności na zginanie całej belki, dzięki temu, że grubsza ścianka w centralnej części kadłuba jest o wiele stabilniejsza, oraz przesunięcie SC samego kadłuba o ok 20mm do przodu, co zredukuje masę balastu na nosie nawet o 2g Mamy chyba też sposób na zatrzymanie żywicy w tkaninie i uzyskanie bezpieczniejszego stopnia przesycenia, ale nie chcę więcej mówić, póki nie zrobię choć jeszcze jednej próby dla pewności.
-
Używam w konstrukcji swoich kadłubów strukturę o podobnej gramaturze sumarycznie. Przy czym daję więcej tkaniny kierunkowej, a mniej diagonalnej. Jak z wytrzymałością Twoich kadłubów? Belka ogonowa nie ugina się za bardzo?
-
Na RCgroups określane jest to jako "launch preset". Względem klasycznej fazy do rzutu: klapy delikatnie w dół, ster wysokości delikatnie do góry. Ustawia się to w nadajniku, żeby włączało się pstryczkiem ze sprężynką. W trakcie wypuszczania modelu trzymasz palcem tę fazę włączoną, dzięki czemu nawet po płaskim rzucie model szybko przechodzi do prawie pionowego wznoszenia, wtedy puszczasz przełącznik i model wchodzi w standardową fazę rzutu, dla najmniejszego oporu. Zalety: rzucając płasko, nie do góry, możesz rzucić mocniej i jest mniejsze prawdopodobieństwo zahaczenia końcówką skrzydła o ziemię. Nie ma większego znaczenia pod jakim kątem rzucisz. W razie potrzeby przytrzymujesz pstryczek dłużej lub krócej, a i tak model potem idzie prawie pionowo, co jest najbardziej optymalnym torem lotu. Wady: większa pstryczkologia w radiu, część zysku z mocniejszego rzutu tracisz na zwiększonych oporach, kiedy model przechodzi z lotu płaskiego do pionowego. Kiedy model wznosi się prawie pionowo nad głową pilota, trudniej ocenić właściwy moment do przejścia w lot poziomy. Adam, bez wykresów z logera się nie liczy!
-
Z mojego doświadczenia wynika, że wystarczy zostawić taki kadłub z kawałkiem balonika na kilka dni w cieple. Balonik sam się odkleja i odpada. Kadłub nr 8 wyciągnięty. Cała teoria poszła w las. Nadmiar żywicy, który zostawiliśmy w tkaninach też wypłynął na podział i kadłub waży tyle samo ile poprzedni. Co w takim razie zrobić z podręcznikową teorią 60/40? Czy kosztem tych 3g większego ciężaru znaleźć sposób na zatrzymanie żywicy w środku? Może szczelniej składać formę, nie pozwalając żywicy na wpłynięcie między podziały, albo odwrotnie niż Adam używać szybkiego utwardzacza, żeby zżelowana żywica miała mniejszą chęć ucieczki? Jeszcze nie wiem, ale na razie cieszę się z satysfakcjonującej powtarzalności procesu. Trzaski przy zgniataniu palcami ścianek kadłubów muszą się w takim razie brać z innej przyczyny. Stawiam na węgiel kierunkowy 30-tkę. Strasznie licha jest ta tkanina, a wszystkie podejrzane dźwięki wydają tylko ostatnie trzy kadłuby, w których właśnie dołożyliśmy tę tkaninę.
-
Po krótkiej przerwie, korzystając z tego, że jest weekend wróciliśmy na modelarni do tematu kadłubów (to już chyba taka nasza obsesja, albo hobby w hobby, bo tylko spójrzcie: W zasadzie co tu płakać nad nieudanym "kadłubem nr 6"? Trzeba nam było trochę rozrywki, najlepiej nad kubkiem żywicy Efekt rozrywek jest taki, że dziś wyjęliśmy z formy kadłub nr 7 (i wcisnęliśmy kadłub nr 8) Struktura: przód: 5 x szkło 50 ( na przemian skośnie i prosto) reszta: węgiel UD 125 prosto, węgiel UD 30 prosto, węgiel klasyczny 93 skośnie. Wagowo mega super: 35g, wizualnie super, prócz małej skuchy pod skrzydłem i resztki balonika z przodu. Jeden zasadniczy feler, w zasadzie dyskwalifikujący: kadłub trzeszczy pod palcami Coś już mnie tknęło przy poprzednim kadłubie i zacząłem podejrzewać, że w naszej technologii jest poważny błąd. Podczas laminowania poważyłem formatki węgla przed i po kolejnych etapach i wyszło mi, że ostatecznie na wyrobie uzyskaliśmy 68% masowego udziału tkaniny w kompozycie. Trochę dużo, zważywszy na to, że optymalnie powinno być 60%. Podejrzewam, że stąd właśnie to trzeszczenie. Następny kadłub wylaminowaliśmy z tą samą ilością tkanin, ale daliśmy więcej żywicy. Według wagi 55% węgla w kompozycie po ułożeniu w formie, czyli o 3g żywicy ponad optimum. Daliśmy też mniejsze ciśnienie, bo tylko 3atm. Czy balon wyciśnie tylko tyle nadmiaru żywicy, czy więcej? Przekonamy się jutro... Zrobiłem również przymiarkę pakietu Dualsky 520 2s do noska kadłuba. Ponieważ takiego pakiecika pod ręką nie mam, wyciąłem ze styroduru klocek o wymiarach 19x18x50, efekt: Porównanie do Rhino 360 2s Niestety 520 może okazać się za duża. Sytuację może jeszcze uratować mniejszy wymiar rzeczywisty, niż ten podany w katalogu, albo chociaż zaokrąglone krawędzie. Czy ktoś, kto posiada taki pakiet mógłby go dokładnie pomierzyć w przekroju i sprawdzić, jakie ma promienie zaokrąglenia?
-
@list, my zawsze robiliśmy to na dwa ruchy. To znaczy w pierwszym laminowaliśmy zewnętrzne tkaniny i przekładkę, a na następny dzień w drugim ruchu siateczkę i tkaninę zamykającą przekładki. Dzięki temu zamkniecie przekładek robi się bardzo łatwo, pianka przekładki jest już przyklejona i nie pływa. Minus taki, że trwa dwa dni. Można to skrócić i laminować wszystko na raz, ale wtedy nitki siateczki trzeba przykleić na 3M77 do tkaniny zamykającej. @rapier, używamy baloników do modelowania Qualatex. A kadłubik nam nie wyszedł Tzn wyszedł z formy, bardzo ładny, bez żadnych pęcherzy, nawet lekki bo 35g, ale miękki - wgniata się ściskany palcami. Za mało tkanin po obwodzie. Niestety patent z układaniem dwóch tkanin jednokierunkowych 30-tek na przemian po skosie raz -45o raz +45o to za mało. Trzeba będzie używać klasycznej 93ki... czyli wracamy do struktury pierwszego kadłuba. Zatoczyliśmy koło po zrobieniu pięciu iteracji.
-
Wiem o czym mówisz, robiłem tą metodą zakładki przy laminowaniu kadłubów bez docisku. Kopertowanie węgla kierunkowego to podstawowa zasada, o której nigdy nie zapominam. Czasem daję włókna w poprzek, czasem na 45st, ale zawsze taka warstwa tkaniny jest. Inaczej będzie pękać wzdłuż kierunkówki.
-
Najbardziej zastanawia mnie sposób bazowania w formie gwintów pod mocowania statecznika poziomego. Jednym z oczywistych rozwiązań jest dla mnie otwór na przestrzał przez formę. Od zewmątrz formy wkręcam śrubę, której gwint wystaje w formie i na nim bazuję nakrętkę, czy zalewam żelkot podczas laminowania kadłuba. Przed wyjęciem kadłuba, wykręcam śruby z zewnątrz formy. Ale otwór na przestrzał 6cm zbrojenia formy z tkanin i piasku budzi moją wątpliwość. Może jest jakiś łatwiejszy sposób?
-
Wczoraj udało nam się znaleźć czas na zrobienie kolejnego kadłuba. Znowu z inną strukturą, może już ostateczną? Tym razem zmotywowałem się, żeby w trakcie pracy zrobić kilka zdjęć do relacji. Nie jest łatwo jedną ręką trzymać aparat, a drugą laminować, ale mimo to udało się zamknąć formę i napompować balon Cały proces, łącznie z przygotowaniem tkanin trwa ok 3h: Najpierw przygotówka: forma przygotowana, zapastowana, pociągnięta PVA i lakierem bezbarwnym balonik naciągnięty na sztycę (biedak nie załapał się na zdjęcie) główne formatki węgla: kanapka posklejana na 3M77 z (od zewnątrz kadłuba) węgiel UD 125 na 0o, 3 warstwy węgiel UD 30 kolejno na +45o, -45o i 0o formatki szkła na nosek: 5 warstw 50-tki, ułożone na przemian z 0/90o, +/-45o łatki klasycznego węgla 93, na półkę pod skrzydło, pyloniki i cięte na +/-45o depronowe wypełnienie pylonika statecznika poziomego rowing węglowy tex1600 na kańciki sklejki pod gwinty śrub skrzydła Laminowanie zaczynamy od położenia żelkotu z aerosilu w ostre kanciki formy i ułożeniu rowingów Następnie łatka na kopułce noska Oraz pylonik statecznika poziomego: W miedzyczasie sycimy na folii główne formatki węgla Następnie wkładamy je w worek próżniowy dla lepszego odsączenia nadmiaru żywicy Kiedy wszystkie rowingi i łatki w formie są ułożone, wyjmujemy z worka odsączone, główne formatki węgla i układamy w formie Na boku sycimy formatki szkła na nosek, składając kanapkę ze wszystkich 5ciu warstw i układamy w formie Na górnej połówce układamy sklejki pod gwinty śrub i łatkę z węgla Teraz do pracy zatrudniamy zagięte, chirurgiczne nożyczki i docinamy formatki. Górną część docinamy do krawędzi podziału Na dolnej zostawiamy ok 5mm zakładki, a formę układamy w grzebyku do nawijania nitki W środku układamy sztycę z balonem i zaczynamy zawijać nitki przytrzymujące zakładki w pozycji do wewnątrz. Dzięki temu nic się nie podwinie przy składaniu form. Kawałeczek plastelinki na przejściu formy w kanał prowadzący balonik. Ma to zabezpieczyć balonik przed przerwaniem w miejscu gdzie z wąskiego kanału rozszerza się w przestrzeń formy. Teraz już będzie z górki: nakładamy drugą część formy Rozcinamy nitki i powoli wyciągamy Zakładamy obejmy, mocno skręcamy i pompujemy Najpierw powolutku do 1,5bar, żeby napełnić wstępnie balon. Po kilku minutach podkręcamy do 2,5bar, a po kolejnych kilku minutach jeszcze więcej. Kiedy zegar wskazuje 4,5bar, czas wracać do domu. Ciekawe czy nas dzisiaj wpuszczą, czy czeka nas nocleg na wycieraczce? Dziś wieczorem wielkie otwarcie...
-
Fajna instrukcja, kawał dobrej roboty. Bardzo mi się podobają, oprócz całego modelu oczywiście, owiewki dźwigni lotek, super sprawa! Dla mnie niedościgniony wzór.
-
Dzisiaj też udało mi się polatać. Przymocowałem na zewnątrz kadłuba vario Pitlaba i nagrałem trochę lotów Rzucało mi się lepiej jak wczoraj, choć wiem że to jeszcze nie jest to na co mnie stać. Ewidentnie trzy miesiące spędzone na modelarni nie wpływają dobrze na koordynację ruchową. Oto kilka rzutów podczas dynamicznej sesji dla rozgrzewki: Prędkości opadania niestety nie udało mi się zmierzyć. Była termika i trochę turbulencji zza drzew więc pomiary są oszukane.
-
Nowy kadłub oblatany Kamień z serca. Wrażenia? Bardzo pozytywne, szczególnie że większośc problemów jakich się spodziewałem, nie pojawiło się. - Kąty zaklinowania prawidłowe, model dla tego wyważenia wymaga tylko nieznacznego trymowania. - Środek cięzkości wyliczony prawidłowy, choć raczej z tych tylnych (liczony na 8% zapasu stateczności), ale bezpieczny - Stateczność i sterowność bardzo dobra. Dzięki trochę krótszemu kadłubowi względem poprzednich egzemplarzy, zwiększyła się sterowność i tym samym łatwość wykonywania ciasnych zakrętów. - Kadłub wytrzymał kilkadziesiąt rzutów. Fakt, że nie jestem w szczytowej formie, ale nie ma żadnych niepokojących objawów, które mogłyby wskazywać na problemy w newralgicznych miejscach. - Wysokość rzutów dobra, mimo nienajwiększej siły z jaką rzucałem. Spróbuję zmieścić gdzieś jakiś logger przy okazji kolejnych lotów. - Czasy lotów zadziwiająco dobre. Było już grubo po 15-tej, od kilku godzin pełne przykrycie chmurami, wiatru prawie zero, a model zrobił 2:18, 2:24, 2:21, 2:23, 2:19. Loty po kwadracie o boku ponad 200m, wokół całej łąki. Na pewno spróbuję powtórzyć tę próbę z loggerem, przy jeszcze bardziej obiektywnej pogodzie, zapisy mogą być ciekawe! Nie było łatwo pamiętać jeszcze o nagraniu, ale udało mi się w końcu postawić aparat w kilku miejscach, tak żeby było coś tam widać: http://youtu.be/E5VxXw5umpk Każda wolną chwilę będziemy teraz przeznaczać na loty, z maksymalną ilością silnych rzutów, żeby jak najszybciej wyszły problemy z wytrzymałością zmęczeniową, choć po cichu liczę, że ich nie będzie. Muszę też powtórzyć loty w spokojnych warunkach, dla potwierdzenia prędkości opadania, oraz założyć logger. Na termiczną pogodę nie wiem czy mogę liczyć w najbliższym czasie, przydałoby się sprawdzić i dostroić regulacje w termice. Masa tego egzemplarza niestety mocno rozczarowuje. Po wyważeniu jest 291g, w tym: 8,6g nosek 164g skrzydło do lotu 118,6g kadłub do lotu, w tym: 11,3g stateczniki 41g skorupa kadłuba 10g ołowiu Z czego można urwać w przyszłych modelach: - skrzydło, tutaj w wersji d-box czyli cięższe o jakieś 5g od szklanego, w dodatku to było kilka razy klejone i miało przerabiane mocowanie. Nowe skrzydła w szklanej wersji wychodzą nam na 63 - 65g połówka. - kadłub - całe pole do popisu. 41g kadłuba i ponad 8g noska daje 50g za komplet, w czasie gdy konkurencja mieści się w 35-45g ze wszystkim. W dodatku im lżejsza struktura kadłuba, tym łatwiej go wyważyć. Poniżej zestawiłem masy, środki ciężkości i obliczeniową masę balastu, aby SC całości wypadał tam, gdzie powinien: (Xsc liczony wzgl. krawędzi natarcia skrzydła) Widać, jak trudno wyważyć ten kadłub, który ulotniłem. Oczywiście wartości masy balastu ulegają zmianie, kiedy dochodzi masa skrzydła, stateczników i wyposażenia, ale tendencja pozostaje. Musimy solidnie przyłożyć się do redukcji masy struktury i odpuścić trochę ze sztywności...
-
Wczoraj nie zdążyłem wyważyć Dopiero dziś to zrobię, właśnie jadę po model i na łąkę oblatać. Pogoda świetna. Bez balastu model waży 280g. To trochę ciężko niestety, ale na oko nie będzie potrzebował dużo ołowiu z przodu. Zrobię dochodzenie dlaczego taki ciężki i wszystko potem wyjaśnię. @krzysiek w, tak, sprężyna na żywicę bezpośrednio wklejona w rdzeń.
-
Akryl 2k jeszcze mnie nigdy nie zawiódł. Z poliuretanem dwuskładnikowym też miałem dużo dobrych doświadczeń. Ale w wersji ekonomicznej, niektóre Motipy w sprayu też się sprawdzają.
-
Niektóre tasmy papierowe lubią zostawiać ślady. Najlepiej spisuje się nam zwykła taśma biurowa Scotch'a
-
Jak narazie BlueWax. Ale np. z Axson Cire 287 też mam bardzo dobre doświadczenia. Tylko trudno się poleruje :/ Pakietom z Nastika muszę się przyjrzeć. Może się zmieszczą, a 200mAh więcej się przyda. Z HS45 wciąż niestety nie zrobiłem przymiarki w kadłubie. Nie mam w tym momencie pod ręką takiego serwa luzem. Wszystkie w modelach. Tymczasem powalczyłem trochę na modelarni i przygotowałem pierwszy z nowych kadłubów do oblotu A było to mniej więcej tak: Na początek nowy komplecik świeżutkich stateczników: Żeby dokładnie wiedzieć w którym miejscu naciąć zawias, oraz zrobić znaczki pomocne przy wklejaniu statecznika w kadłub robię szybki planik. Tutaj zdjęcia statecznika pionowego: Ważne, żeby wszystkie linie wystawały poza obrys, wiem wtedy dokładnie jak przyłożyć linijkę... ...od której nożykiem robię delikatne nacięcie. Następnie już bez linijki pogłębiam nacięcie kolejnymi przejazdami noża. Kiedy już wyczuję pod nożem, że dotarłem do kompozytu po drugiej stronie rdzenia, robię nacięcia poprzeczne, w kierunku spływu i delikatnie załamuję sterek Następnie biorę iglaczek w kształcie klina i szlifuję rowek pozwalający sterkowi na wychylanie się w stronę przeciwną do zawiasu Szczelinka powinna pozwalać sterkowi na wychył o ok 10mm mierząc w najszerszej cięciwie Następnie przygotowuję dźwigienki z płytki kompozytowej 0,8mm i sprężynki skrętne z drutu 0,5mm Szybka przygoda z żywicą 5min i już wszystko gotowe: Napływ pod statecznik pionowy już przygotowany, wyszlifowany kształ zewnętrzny, a wewnętrzna powierzchnia zmatowiona Pylonik statecznika poziomego również zmatowiony do klejenia. W nacięciu za pylonikiem będzie chowała się dźwignia steru Klejenie stateczników na żywicę z microbalonem Na następny dzień wszystko jest gotowe Skrzydło, którego użyję do tego modelu to już weteran, przeżyło dwa kadłuby starego typu, więc nie wygląda zbyt atrakcyjnie :/ Tuleja tylnej śruby mocującej akurat pasuje i do nowego kadłuba, więc nie trzeba nic modyfikować. Musiałem wykonać wzmocnienie w okolicach przedniej śruby. Wcześniej skrzydło było mocowane na tylnej śrubie i dwóch kołkach wklejonych w krawędź natarcia. Kołki zostały ucięte, a przestrzeń pod przednią śrubą rozborowana, zalana mieszanką microbalonu z żywicą i przykryta łątką tkaniny węglowej. Następnie zrobiłem znaczki środków skrzydła i kadłuba i złożyłem komplet na grubą taśmę dwutronną Otwór pod przednią śrubę nawierciłem wietrłem fi3. Przez tylną tuleję wiertłem fi4 zaznaczyłem na kadłubie centrum otworu. Po zdjęciu skrzydła wykonałem w kadłubie gwintowane otwory M4. Kadłub w tych miejscach miał wcześniej wlaminowane kawałki sklejki 5mm. W skrzydle rozwierciłem przedni otwór na pożądaną średnicę, wkleiłem krótką tulejkę i wyfrezowałem stożek pod łeb śruby. Komplet po zmontowaniu: Montaż wyposażenia poszedł tak szybko, że nie zdązyłem zrobić pośrednich zdjęć :/ Następnym razem zatrudnię do tego kamerę do zdjęć poklatkowych Przed: Po: Zamontowałem zgodnie z planem: Rhino lipo 350 2s HK uBEC 3A odbiornik JR RG 631 2x Dymond D47 Antenki postanowiłem dać w środku, prowadzone w rurce termokurczliwej. Jedna jest przymocowana wzdłuż kadłuba po dnie noska, pod odbiornikiem, druga pionowo pomiędzy odbiornikiem a serwami. Ogonek i wyprowadzenie linek kevlarowych W kadłub wkleiłem 1cm odcinek rurki z bowdena, dzięki czemu linka nie strzępi się o krawędzie węgla. Owijka z nitki widoczna pomiędzy statecznikami to niestety konsekwencja próbnej struktury tego kadłuba. W tym miejscu brakuje włókien kopetrujących tkaninę jednokierunkową biegnącą wzdłuż kadłuba i ścianki miały tendencję do zapadania się. W kolejnych kadłubach już nie robimy takich eksperymentów. Nosek już doszlifowany