
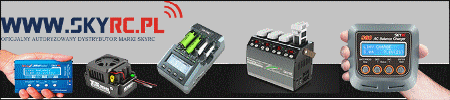
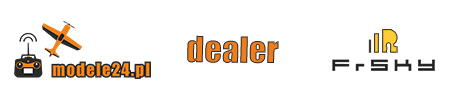
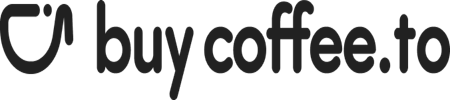
-
Postów
3 456 -
Rejestracja
-
Ostatnia wizyta
-
Wygrane w rankingu
90
Treść opublikowana przez Patryk Sokol
-
Oringi z Castoramy brzmią sensownie. Mam nadzieję tylko, że nie sparcieją od CA tak szybko jak sparciały oryginalne gumki (bo ratując się z otworami, które stawały się dziurami, próbowałem gumki umocować na CA). Tymczasem - udało mi się wytargać współlokatora żeby jakiś filmik nagrał. Niestety stwierdziłem, że "poprawię" ustawienia w ZYXie i ogon stał się nieco gumowy (co widać gdy próbuję walczyć z tic-tocami, wtedy ładnie ogon lata). Wydaje mi się, że na poprzednich ustawieniach osiągnąłem już maxa. Żeby ogon działał lepiej musiałoby być szybsze serwo. Przy sensownym ustawieniu już jest naprawdę ok, sporo lepiej niż na filmie. No i około 2:20 robię pierwszą przymiarkę do overspeeda. Wydaje mi się, że udało mi się go zrobić, bo po dodaniu gazu słychać, że silnik kręci sobie na luzie, a sprzęgło nie załączyło (czyli obroty wirnika zbyt duże dla obrotów silnika, governor przytrzymał) A jak ocenię swoje umiejętności po tym filmie? W skrócie - dużo przede mną Tzn. jak ktoś nie wie co ogląda, to może nawet wyglądać to cool. A ja tutaj widzę przede wszystkim brak precyzji w prowadzeniu. Grunt, że nie zaliczyłem gruntu Tzn. czuję się z tym na tyle komfortowo, że myślę, że dalsze szlifowanie umiejętności to po prostu latanie, latanie i latanie No i trzeba zacząć pirozawis ćwiczyć na końcówce pakietów. Zdaje się to być podstawą, żeby pewnie się czuć w każdym kierunku lotu. Poza tym chyba pakieciki zaczynają dostawać po tyłku. Tj. w Idle2 i max mocy czuć, że silnik zaczyna trochę przydychać. Ale - 150cykli każdy, już im wolno A na deser zamówiłem sobie XK K120. Zobaczymy, czy nie pożałuje, że nie zdecydowałem się na bardziej plasticzanego V977 (wydaje mi się, że K120 może być bardziej delikatna przy kontaktach z glebą)
-
Ok, skoro wszystko działa to ugryźmy inny problem. Obecnie moja kabinka wygląda tak: Czyli. Wielkie otwory, brak gumek itp. I Chciałbym coś z tym zrobić. Na pewno trzeba zamknąć te otwory. Być może użyje sklejki, będzie odporniejsza na takie rozjeżdżanie się od środka (bo mniej krucha ogólnie jest). Ale co zrobić z kwestią gumek? Nie umiem nigdzie znaleźć gumek do kabiny, trzeba będzie jakoś zastąpić. Jakieś pomysły?
-
Za spróbowanie nie karzą, a jak się nie spodoba to można przestać Zdecydowanie próbuj
-
Czyli własne strugi zaśmigłowe. Ok, nic nie poradzę Już eksperymentowałem z tym trochę i jedyne co pomaga to właśnie zejście w locie postępowym i wyższe obroty. A z innych rzeczy. Dokopałem się do instrukcji swojego regla. Okazało się, że jest to stockowy regler Aligna do 450 V2. Oczywiście nie łaska to napisać na nim, więc znalezienie co to jest i instrukcji było tragedią. Ale jako, ze temat wyśledziłem, to z radością ustawiłem soft start (OMG, FTW <3, <3). Nawet nie wiecie jaką radość sprawia mi po prostu odblokowanie przepustnicy zamiast ręcznego otwierania przepustnicy. No i mając dostęp do regla to zacząłem bawić się z governorem. Pierwsze co się okazało - normal idzie przez okno. Nie idzie tego zgrać z govem, heli dostaję trzęsiawki w dolnych zakresach skoku. Nie będę tęsknił i tak go nie używałem. Idle1 ustawiłem na 70% przepustnicy (cała płaska krzywa), Idle2 ustawiłem na 90% (też płasko). Idea była taka, żeby Idle1 był na jak najniższych obrotach. Okazało się, że minimum to 65%. Mniej powoduje, że dzieją się dziwne rzeczy, z przegrzewaniem się regla i pulsowaniem ogona na czele. Na 70% za to lata się cichutko, mięciutko i naprawdę przyjemnie. Pętla, czy beczka wychodzi bardzo fajnie. Względem wcześniejszego ustawienia, gdzie krzywa na zerze miała właśnie 70% i szła do 100% na +/-11st, sporo poprawiła się reakcja na skok. Jest sporo żywsza i nie słychać momentu, kiedy skok już się podnosi, a silnik jeszcze się nie rozkręcił. No i ogon już całkiem przestał uciekać po gwałtownym dodaniu skoku. W Idle2 lata się trochę jak w symulatorze. Szybkie zwrotne itp. Jeszcze nie ustaliłem którego Idle'a wolę, myślę,że to zależy od nastroju. Idle1 zdaje się być na pewno faworytem do szerokiego latania po niebie Myślę, że w tym momencie mogę już śmiało powiedzieć, że zakończyłem ustawianie tego śmigłowca. Lepiej już raczej nie będzie Teraz pozostaje pytanie - co zrobić z trzecią fazą lotu? Autorotację mam na innym pstryku, więc to na pewno odpada. Oczywiście zawsze mogę olać trzecią fazę, ale jak pstryk jest to warto by go użyć No i kolejna kwestia - jak zacząć ćwiczenia autorotacji? Mając soft start (a z governorem nie da się nie mieć soft startu) wyłączając silnik już nie mam odwrotu (bo nie rozkręci się od razu). Stąd pytanie do Was: Jak robić to bezpiecznie? Duża wysokość przerzucić w tryb autorotacji i mieć nadzieję, że się nie pogubię?
-
Wygląda jakbyś miał zbyt tylny środek ciężkości. Z przednim prawie żadnego trzymania nie trzeba.
-
Deltę MJ! http://majankowski.republika.pl/delta_mj.html Prościej i łatwiej do latania się nie da
-
Dziś mogłem pobawić się heli bez ryzyka, ze mi ręce odpadną (tylko -4stC!). Stwierdziłem, ze zamiast latać w kółko to powalczę z regulacją FBLa. O ile wcześniej było fajnie, tak po regulacji konkretnych wartości PID jest tylko rewelacyjnie. A ustawienie funkcji które automatycznie dodaje skoku na ogonie, wraz z operowaniem skokiem głównych łopat sprawiła,ze spędziłem cały lot robiąc pogo No, ale tu pojawia się pytanie do Was. Kiedy schodzę heli pionowo w dół, to sterowanie robi się mniej precyzyjne, nieco roztelepane, a wyrwanie z opadania wymaga więcej gazu niż to co będzie potrzebne w zawisie. Czy mam jakiś błąd w regulacji, czy po prostu helik wpada we własny syf zaśmigłowy? Wydaje mi się, ze druga opcja, bo gubienie wysokości w locie postępowym jest sporo przyjemniejsze.
-
A eksperymentowałeś z obrotami wirnika? Prawda to, że DFC nie lubi się z niskimi obrotami?
-
No i Rexia oblatałem po naprawie. Acz z przygodami. Tzn. po starcie niby wszystko ok, ale na małych obrotach ogon ma nieco trzęsawkę. W pierwszym odruchu zmniejszyłem gaina, powisiałem chwilę na boisku i poszedłem do domu. Później dopiero mnie tknęło, żeby wymienić główny wał. Po wymianie gain wrócił gdzie był i wszyscy happy. Ogólnie to mam wrażenie, że co by się nie działo, to wał do wymiany zawsze jest. IMO za cienkie te wały, tak ze 2mm więcej by nikomu nie zaszkodziło Albo są za długie w sumie... Myślę, że jak mi się zapas wałów skończy, to chyba będzie to znak,żeby przesiąść na typową głowicę FBL, bo każda powinna mieć krótszy wał. Jak już rozmawialiśmy o religii, przekonaniach i orientacji modelarskiej, to teraz pomówmy o typie głowicy. Jak myślicie - DFC, czy klasyczny FBL? Ja się skłaniam do klasycznego FBL, zdaje się być mniej morderczy dla serw.
-
To może będę pierwszy. Jak mi się wszystko finansowo poukłada to sobie w nagrodę kupię jakiegoś większego heli. XLPower jest dosyć wysoko na liście
-
MH32 to bardzo zacny profil. Jeden z niewielu łatwo dostępnych które godnie rywalizują z AG w takich modelach. I żeby było ciekawiej - w mniejszych modelach na tym profilu to mniejsze wydłużenie bardzo pasuje. Wynika to z tego, że to szybki profil, który dobrze pracuje na małych współczynnikach siły nośnej. A bagnet - polecam jednak stalowy. Dużo ciężej nie będzie, a chociaż wymiar trzyma jak należy.
-
Bah - żebyś widział co się w branży rowerowej dzieje Tam jest jeszcze ciekawiej, bo producent odpowiada tylko za ramę (która, szczególnie w hardtailach, jest jedynie wieszakiem na sprzęt), cały osprzęt to wszędzie to samo, albo Shimano, albo SRAM. A mimo to są olbrzymie dyskusje o tym jak to w Specach lepiej chodzi napęd niż w Giantach Dlatego właśnie pytam o konkrety, bo samemu idzie mi jakoś słabo szukanie. A konkrety to właśnie często powtarzające się usterki, bądź konkretne problemy w danym modelu (jak np luz na ogonie w moim Rexie, aż do bólu typowy). A i żeby było ciekawiej. Znalazłem jeszcze takie modele: http://www.xlpower-rc.com/prolist.asp?id=125 I to już nie są klony
-
To już chodziło raczej o kwestie niezużywające się. Szczególnie gwinty kulek były nędzne. No i nowa tarcza Aligna z tych czasów też była luzowata (inny kolega miał taką jeszcze nierozpakowaną z worka). Aczkolwiek nie zrozum mnie źle - Jakbym kupował 700tkę, to w życiu bym nie oszczędził 1000zł na modelu. To nie jest dobry interes
-
A nowy Align jest lepszy niż starszy? Bo mój Rexiu stopniowo staje się Tarotem I szczerze mówiać, to części Tarotowe są lepszej jakości niż to co z Rexia zdejmuje (np tarcza Aligna była wręcz żałosna)
-
No troszkę by się przydało Bo ze dwie części Gartta były w heli kolegi (które naprawiałem po kraksie) i wyglądały jak Tarot. Tzn - nie bronię tego jak dobre dealu, po prostu chce poznać szczegóły
-
Dotarło serwo na wymianę do Rexia i już jest jak nowy Może zaraz go oblatam (jeśli aku naładowane), a może jutro rano Niemniej mam pytanie do Was. Czy mówią Wam coś klony T-Rexa produkcji Gartt? Bo wpadło mi to w oko na Aliexpress i o ile to jest dosyć tanie: https://pl.aliexpress.com/item/Freeshipping-GARTT-GT550-PRO-TT-2-4GHz-3D-Torque-Tube-Helicopter-100-compat-Align-Trex-550/662598566.html?spm=a2g17.search0104.3.44.43026616cJKB9J&ws_ab_test=searchweb0_0,searchweb201602_5_10152_10151_10065_10344_10068_10342_10343_10340_10341_10084_10083_10618_10304_10307_10301_5711211_10313_10059_10534_100031_10103_10627_10626_10624_10623_10622_10621_5722412_10620_5711311,searchweb201603_1,ppcSwitch_5&algo_expid=a4aa2a40-cae0-483e-b3ea-b6e99bf6afd2-7&algo_pvid=a4aa2a40-cae0-483e-b3ea-b6e99bf6afd2&priceBeautifyAB=0 Tak ten misiu: https://pl.aliexpress.com/item/GARTT-GT700-DFC-TT-RC-Helicopter-Torque-Tube-Version-With-Fire-Super-Combo/32490614791.html?spm=2114.12010108.1000013.1.37eb60aejKkOWD&traffic_analysisId=recommend_2088_1_90158_iswistore&scm=1007.13339.90158.0&pvid=15aec267-ff56-4db7-84a4-46d70fb25ffe&tpp=1 Ma cenę oscylującą w okolicach żartu Jest jakiś haczyk, czy są to lotne modele?
-
Sensacje w radiu dot. dronów i programu "Żwirko i Wigura"
Patryk Sokol odpowiedział(a) na AMC temat w Hyde Park
Ćwierć miliona? Komuś zer nie pogubiło? Bo jeśli nie, to zróbmy może zrzutkę forumową, możemy kupić dla forum rynek dronów. -
Nie to nie to. I nie mogę więcej ujawnić niestety.
-
Ale poważnie, opowiedz nam dlaczego. Bo skoro wiesz, to możesz nam powiedzieć Wystarczył by jeden argument i byłoby po "śmieceniu", tak to klepie kolejne posty żebyś użyczył nam niesamowitej wiedzy latacza spalinami i wyjaśnił w czym tkwi problem.
-
To wiesz jak się lata, czy nie jesteś autorytetem? Jedno z dwóch, dwa na raz nie wejdą. Jak już zarzuciłeś mi gadanie bzdur, to teraz czekam na argumenty, bo jak na razie udało Ci się mnie obrazić ,a niczym tezy nie poparłeś. Skoro wiesz jak się lata, to też na pewno będziesz wiedział czemu to nie działa.
-
To nie tego kwestia. Podstawą jest kwestia dobrania frezu. Do tak cienkiego materiału potrzebny jest malutki frez down-cut. Wtedy taką sklejkę mocujesz na taśmę dwustronną do miękkiej podkładki (np. podkładu pod panele) i frezujesz jednym przejściem na wylot. Pełne podparcie pozbawia nas wibracji, a frez down-cut gwarantuje brak tendencji do podrywania materiału. Frezy down-cut masz np. tu: http://allegro.pl/frez-1mm-down-cut-z-weglika-spiralny-lewoskretny-i4903078681.html Ze sklejką potrafi być inny problem. Niestety potrafi to być materiał dosyć niejednorodny (może nie ta lotnicza z modelarskiego, ale inne potrafią być problematyczne). Trzeba więc trzymać dosyć wysokie obroty, bo inaczej w jakiejś twardszej części potrafi się frez złamać. Niemniej - z metodą na pełne podparcie to jest to bardzo wdzięczny materiał.
-
Ech... Naprawdę? To jest tak słaby argument (w sumie to nie jest argument, to taki błąd logiczny: https://rationalwiki.org/wiki/Argument_from_authority . Bo zamiast mi odpowiedzieć, to siebie stawiasz jako autorytet, co powoduje,ze uznajesz za udowodnione), że aż przykro mi robi, że się czyś takim zasłaniasz. Już nawet stwierdzenie, że opóźnienie w reakcji na przepustnicę stanowi problem jest znacząco lepszym argumentem, bo porusza faktyczną kwestię. Poza tym - 6m BSL z dwoma benzynami, to już dosyć, czy jeszcze za mało (i nie fotek nie będzie, jak zwykle NDA)? Ale dobra, uznajmy,ze nie brałem udziału w takich projektach. Więc masz takie rzeczy: http://www.rcuniverse.com/forum/twin-multi-engine-rc-aircraft-192/10768230-differential-thrust-steering-glow-engines.html Gdzie piszą o możliwości użycia tego, ktoś wspomina o użyciu różnicowego ciągu do kołowania. Dobrze, że nie wiedzieli, że w spalinie się nie da. A idąc dalej: http://www.bigplanes.nl/contents/en-uk/p1024_WIKE_RC_TwinSync_Engine_Synchronizer.html To urządzonko śluży do synchronizowania ciągu w naprawdę dużych modelach. I wiecie co jest zabawne? Że ma wbudowaną funkcję do miksowania silników do steru kierunku. Idąc dalej - pełnowymiarowe łodzie latające potrafiły używać różnicowego ciągu do sterowania na wodzie (ale ok, słaby argument, bo to nie w powietrzu). I tak - sterowanie ciągiem w większych modelach nie pozwoli na pętle na żyletce jak Twisntarem, nie to obciążenie mocy. Ale - Ugly Twin jest jedynie 25cm mniejszy od Twinstara, a mocy na pewno będzie miał więcej. Więc - zapraszam do konkretnego argumentu na temat: Dlaczego zróżnicowanie ciągu silników, ma nie spowodować powstania reakcji w płaszczyźnie działania steru kierunku? Pamiętajcie tylko, że taki miks jest niewielki (10-20% przepustnicy do maks steru kierunku) i pamiętajcie, że jest możliwość jedynie dodawania ciągu na jednym silniku, nie trzeba odejmować.
-
Początkowo chciałem zrobić jak w oryginale, czyli jedynie pasek sklejki 3mm (tzn. dwa paski na goleń, bo goleń się rozgałęzia). Jednak tyle mnie to martwiło, ze jeszcze od środka jest listwa sosnowa 6x6mm tak, że z paskiem sklejki tworzy teownik.
-
Pardon? Przecież ja tak latam na co dzień. Jest to jedyna metoda sterowania moim Twisntarem na ziemi (trójkołowe podwozie, bez skrętnego przedniego kółka) i faktycznie pozwala na akrobacje. Oczywiście sam miks jest na wyłączniku i można go wyłączyć w każdej chwili. Możesz podać jeden sensowny powód dla którego to miałoby być niemożliwe?
-
Guma sylikonowa jest zdecydowanie najlepszym rozwiązaniem. Zamienia dużą siłę na początku (kóra próbuje połamać skrzydła), na mniejsza siłę, ale trwającą aż do samej góry startu Zdecydowanie bardziej przyjazne dla modelu, prostsze dla pilota i pozwalające zrobić więcej wysokości (a jak ktoś ma potrzebę łamania skrzydeł, to może pohalsować, albo zrobić ładnego zooma na górze )