
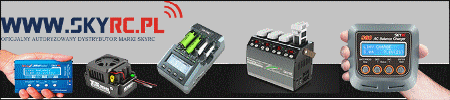
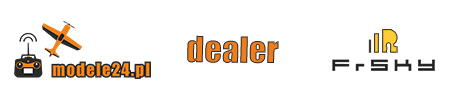
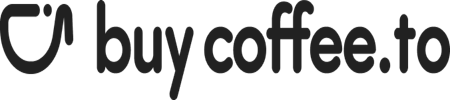
-
Postów
3 456 -
Rejestracja
-
Ostatnia wizyta
-
Wygrane w rankingu
90
Treść opublikowana przez Patryk Sokol
-
I czego to nam dowodzi na temat większej łatwości w wykonaniu Wicherka? Otóż ten argument nie dowodzi nam absolutnie niczego, dlatego że nie ustosunkowuje się do tego co napisałem na temat mniejszej łatwości wykonania Wicherka niż depronu. Idąc tą drogą - jak ktoś ma mniej zdolności wykonawczych, to z racji łatwiejszego wykonania depronu ma mniejsze szanse na popsucie go niż Wicherka.
-
jak na pierwszy model? Oczywiście, że jest. Wiadomo, że sporo prostszy niż budowa choćby Piperka z balsy, ale nie próbuj mi wmówić, że początkujący nie ma co tam popsuć, bo takich rzeczy jest od groma. Szczerze nie widzę opcji porównywania tego do czegokolwiek depronowego
-
Już się o tym rozpisywałem: http://pfmrc.eu/index.php/topic/70358-pierwszy-model-wicherek-25/page-8?do=findComment&comment=687481 W dużym skrócie - rób ClarkY, pamiętając o zmianie kąta zaklinowania (bo Clark Y nie może sobie na płasko leżeć). A jeśli szukasz modelu na pierwszy model RC to w ogóle nie rób Wicherka, lepiej zrób ToTo-0, RWD-5 by Skazoo czy innego Zefirka z depronu. Bądź nawet Deltę MJ, albo Zagi ze styropianu oklejonego taśmą. Jedyny powód żeby robić Wicherka to chęć posiadania oldschoolowego modelu. Obecnie to ciężki i trudny w budowie model.
-
Frez to taki wynalazek: http://allegro.pl/frez-1mm-down-cut-z-weglika-spiralny-lewoskretny-i4903078681.html Posuw 1500mm/min i 12 000obr/min wrzeciona. Podstawa to umocowanie balsy, bo siły przy skrawaniu balsy potrafią być zadziwiająco duże. No i dźwięk jest niezbyt miły, warto coś na uszy założyć
-
To kompensacja do wyrzutu. Na kierunek krążenia wpływ ma tak mały,że za słabo latam żeby go poczuć
-
Nie ma takiej opcji kiedy generujesz trajektorię wprost z krzywych. Żeby to chciało działać musiałbym robić model 3D każdego frezowanego elementu, a to zdecydowanie więcej zbędnej roboty. Głównym problemem w automatyzacji tego jest to, że problem nie ogarnia czy krzywą odsuwać do wewnątrz, czy na zewnątrz. Niemniej - wyrżnąłem większość rzeczy dziś Efekt prezentuje się tak: Jestem w 100% zadowolony z wyniku, wyszło to wielokrotnie lepiej niż przy ostatnim moim podejściu ( http://pfmrc.eu/index.php/topic/70963-avro-avian-ju%C5%BC-nie-taki-maly-dwuplacik/ ) i trzykrotnie szybciej. Na frezie jednopiórowym bywały problemy z zaciąganiem w poprzek włókien i szarpaniem krawędzi (od spodu, bo frez typu down-cut), tutaj wszystko perfekcyjnie wygląda. Dodatkowo, w ramach eksperymentu, próbowałem wyciąć listwy na poszycie kadłuba: To co wyszło idealnie trzyma kąty (znaczy ściany są do siebie ładnie prostopadłe), a wymiar jest w rozsądnej to0lerancji (listwy miały być 5x3, a wahają się w przedziale 5x2,8 do 5x3,1), Na pewno są lepsze niż listwy które kupiłem na dźwigary w Avro Niestety - nie mogę ruszyć ze składaniem, bo nie udało mi się kupić sklejki w interesującym mnie formacie, więc będę musiał aż poczta dostarczy sklejkę. Znając moje szczęście - pewnie na wtorek najwcześniej Z ciekawostek - wycięte elementy z odpadem, listwy sosnowe na główną ramę kadłuba i dźwigary, listwy na poszycie i deski balsy które w całości pójdą na kesony i krycie kadłuba to już 900g wagi Ten model będzie szedł na pewnie z 1,5kg wagi pustego. Przejąłbym się, ale jestem na to za stary
-
Ok mamy pewne postępy Niestety (?) przy projektowaniu wycinanek do tego modelu nie udało mi się rozchorować, więc nie mogłem na to poświęcić tyle czasu ile bym chciał. Dorzućcie do tego fatalną dokładność posiadanych przeze mnie planów (nieprostopadłe osie wręg, sporo elementów skoszonych w jedną stronę, różne długości połówek skrzydeł, nie pasujące od siebie elementy na różnych rzutach etc.) i było to bardziej pracochłonne niż się spodziewałem. No i oczywiście sporo pracy polegającej na odmóżdżającym offsetowaniu wszystkich elementów o pół średnicy freza i wycinanie z tych krzywych mostków trzymających materiał w kupie. Ale efekt jest jakoś taki : W sumie nic niezwykłego - ot elementy porozrzucane po deskach balsy, Jedynym patentem wprowadzonym po cięciu Avro jest upchnięcie sporej części elementów z balsy 1,5mm na deskach które pójdą na kesony skrzydła. Zmniejszyło to zapotrzebowanie na deski do wycinania o 3. Oczywiście pozmieniałem też nieco grubości elementów, głównie po to żeby nie musieć kupować zbyt dużo balsy (co się opłaciło, zakupy ograniczają się jedynie do deski balsy 3mm i deski 6mm). Niestety - pójdzie calutki arkusz sklejki modelarskiej. A ta niestety tania nie jest. Jak jutro wystarczy mi czasu to nawet coś tam na swojej ZOśce wyrżnę. Udało mi się zdobyć nawet pięciopiórowy, jednomilimetrowy frez down-cut. Próbne frezowanie pokazało, że jakość obróbki jest nieporównywalnie lepsza niż na poprzednio stosowanym frezie jednopiórowym.(aczkolwiek - to raczej tylko kwestia zbyt niskich obrotów wrzeciona dla stosowanych przeze mnie prędkości posuwu) Jakby ktoś był zainteresowany to mogę to wycinanki udostępnić w formacie DXF
-
A ok, ma sens W sumie to prosta metoda rozwiązania problemu przejścia pełnego poszycia kadłuba w krycie folią. Do rozważenia w moim projekcie Gee Bee
-
Na plecach to już nieco latałem, nawet ósemkę zrobiłem Na zawis z kolei się nie odważyłem, bo przy tym już samolotowe odruchy tak nie pomogą. Troszkę nie zrozumieliście mojego problemu. On polega nie na tym, że narzekam na swoje umiejętności; Te się rozwijały bardzo satysfakcjonująco dla mnie i się nie cofnęły. Po prostu w pewnym momencie coś kliknęło i latanie heli stało się absurdalnie stresujące Innymi słowy - jak teraz się zmuszę do zrobienia pętli, to po pętli mam już ochotę lądować (bo wiecie, tętno wyższe niż mam w trakcie biegania) Ogólnie - zjawisko nie jest jakieś wyjątkowe, jest dosyć powszechnie opisywane przez teoretyków nauczania, tyle że z reguły wiąże się z jakimś ciężkim przejściem w trakcie nauki. U mnie tego nie było, więc jest to taka dosyć ciekawa zagadka kognitywno-fizjologiczna. Trochę grzebiąc w teorii tego zjawiska dogrzebałem się do tego, że mogę istnieć niekoniecznie uświadomione skojarzenia z jakimś innym mocnym przeżyciem z przeszłości, a tu bym paru kandydatów miał. Niemniej - robi się pod tym względem lepiej, wręcz z każdym lotem. Dzisiejsze latanie było z grubsza bezstresowe.
-
Jak działa to pokrycie garba kadłuba balsą? Nie ma tam stopnia? I dobrze widzę, że pokrycie będzie się opierać jedynie na podłużnicach?
-
Wrzuć go w jakimś formacie wektorowym (a już najlepiej w .dat) to go przedmucham Pochwal się jeszcze jaką metodą robiłeś profil
-
Lepiej napisz na http://www.ossm.pl , będziesz miał większe szanse
-
Jest jeden bardzo konkretny powód dla którego te nowoczesne profile mogą nie wyjść tak dobrze. One wszystkie były projektowane do szybowców, więc mogą charakteryzować się sporo niższym maksymalnym współczynnikiem siły nośnej, bardziej agresywną charakterystyką przeciągnięcia i większymi wymaganiami co do jakości powierzchnia/odwzorowania. Paradoksalnie te wszystkie stare profile, pokroju Clarka Y, Aquilli i innych rzeczy które jak widzę w szybowcach, to mi się już nawet pisać nie chce, to tu mogą wyjść bardzo dobrze. Nadmiar siły nośnej w szybowcach często jest niepożądany (bo opór indukowany), tak w samolotach, gdzie i tak silnik gubi nam małą doskonałość, to ma on same zalety. Zasadniczo mógłbym się zająć kwestią profilu do tego RWDziaka, ale to tak na koniec tygodnia
-
Bez przesady... 145 to kawał cięciwy jak na tak mały model. Daleko nie szukać to nawet współczesne zawodnicze DLG potrafią mieć koło 160mm przy kadłubie. Oczywiście końcówka jest węższa, ale tam już wir indukowany zmniejsza ryzyko jakiejś strasznej separacji. Dorzuć do tego, że skrzydło jest opływane dosyć turbulentnym strumieniem zasmigłowym, a model musi być dosyć szybki - to będzie to latać ok. Proponuje też olać ten słynny wykresik z podkrytycznymi i nadkrytycznymi liczbami Reynoldsa. Cala rzecz polega na tym, że nie można wyznaczyć jednego zakresu dla wszystkich profili, bo ten jest zmienny zależnie od profilu i kąta natarcia Np. tutaj widać fajny wzrost siły nośnej dla ClarkaY, ale typowy nowoczesny profil już się tak zachowuje dopiero przy naprawdę niskich liczbach Re. Podsumowując - spokojnie będzie latać, bo zakres wejścia w obszar nadkrytyczny śmiało można ściąć o połowę (wpływ wibracji i strumienia zaśmigłowego), a nawet jesli to 5m/s to naprawdę bardzo mało jak na tak mały model (bo paradoskalnie małe latają szybko).
-
Podobno lepiej nie kupować, na RCGroups psioczą Instrukcji wytropić mi się nie udało, odezwę się na PM. Cóż, widać nie dosyć doświadczony jestem A tak poważnie - to problemem jest raczej złożoność. Jednak bryła jest dosyć obła, ma trochę oprofilowań, więc trzeba będzie się pobrudzić żywicą. Choć i tak pewnie zrobię styrodurowe formy na frezarce nie będę tego ręcznie rzeźbił Tak czy inaczej - czasu się trochę zejdzie Dlatego już jestem prawie pewny, że mój Gee Bee będzie miał rozwiązanie ułatwiające proste założenie komicznie wielkich kółek, do startu z trawy i mniejszych, w pełni oprofilowanych na okazje asfaltowe/do cieszenia oka na półce. A Twój Gee Bee wyglądał bardzo zacnie Naprawdę zwiększa motywację do pracy nad własnym
-
No i pinion w końcu przetestowany. Efekt w 100% jest pozytywny. Zauważyłem, też że mimo sporo cichszego zawisu i niższego poboru prądu, to odejście w pion po gwałtownym dodaniu skoku jest duże lepsze. Wniosek jest taki, że na poprzednim przełożeniu silnikowi zwyczajnie brakowało momentu i zdychał po dodaniu gazu. Teraz jeszcze bym chciał przetestować piniona 9t, ale to już na spokojnie jak mnie wiatr zawieje w okolice ArtHobby. Obecnie mam podobne przełożenie jak było oryginalnie (czyli okolice 12,1:1, gdzie oryginalnie było 12,5:1), a stosując 9t zejdę do 13,4:1. Nie wiem czy to krok w dobrą stronę, ale koszt eksperymentu to tylko 15zł Żal nie sprawdzić No, ale ok teraz pomówmy o czymś innym. Minęły dwa miesiące od założenia wątku, przyjrzyjmy się postępom. Prezentuje się to... Nędznie? Pierwszy miesiąc szedł pięknie, w końcu jeszcze w poprzednim roku pisałem o robieniu ranwersów, pętli czy beczek. Ba nawet zdarzyło mi się zrobić loty pionowo ogonem w dół. Więc teraz powinno być sporo lepiej, nie? Efekt jest tymczasem odwrotny. Wynika to z tego, że latanie heli stało się dla mnie bardzo stresujące. Kiedy miesiąc temu robiłem pętle to była to po prostu pętla, teraz to naprawdę stresujące przeżycie. Ciężko określić z czego to wynika, być może to skutek to skutek dwóch kraks które zaliczyłem? Efekt niemniej jest taki, że wróciłem do latania w kółko i powolnych ósemek. Grunt, że nie uwsteczniłem się umiejętnościami, sprawa jest jedynie związana z utratą komfortu w trakcie latania ps. Na latanie w sobotę szans nie ma, mam do wykonania zbyt dużo elementów z kompozytu, które wyglądają jak rolka na papier toaletowy. Nawet nie mogę się dowiedzieć po co, klient twierdzi, że to ściśle tajne
-
Czołgiem Panowie Robiąc przegląd swojego hangaru uświadomiłem sobie jedną rzecz - Wszystkie modele są naprawdę przyjemne i poprawne w pilotażu. Z ogonem, bez ogona, nawet bez silnika - ale niezmiennie wszystkie są miłe w prowadzeniu. Czas więc to zmienić! Postanowiłem wykonać jednego z dwóch legendarnych nielotów (znaczy latających, ale niesłynących z przyjemnego pilotażu). Wahałem się miedzy tym miśkiem (i kiedyś go zrobię ): https://en.wikipedia.org/wiki/Vought_V-173 A tym mordercą pilotów: https://pl.wikipedia.org/wiki/Granville_R-1_%E2%80%9EGee_Bee%E2%80%9D Koniec końców - Vought okazał się po policzeniu dosyć zbliżony do latającego skrzydła, powierzchni dużo i raczej latałoby to (z odpowiednio dobranym profilem) dosyć lekko i przyjemnie, więc odpuściłem. Gee Bee za to - łoj, olbrzymi kadłub, malutkie skrzydła, jakoś statecznika pionowego brakuje, będzie bardzo ciężkie, więc w sam raz, tego szukam Poszukując planów znalazłem ten plan: https://outerzone.co.uk/plan_details.asp?ID=7330 Na pierwszy rzut oka mi się spodobał. Później nawet znalazłem relację z budowy w oparciu o ten plan*: https://www.rcgroups.com/forums/showthread.php?927412-Build-Log-1-5-scale-Page-Aviation-Gee-Bee-R2 *Znaczy - nie do końca to ten, widać że tam sporo laserowej wycinanki, tam gdzie plany mają listwy sosnowe. Ale widać, że coś te modele mają ze sobą wspólnego. Plan był dla mnie typowy ostatnimi czasy - tj. zwektoryzować wszystko, podzielić na deski i wyciąć na swojej frezarce większość elementów. Przy wektoryzacji okazało się, że statecznik pionowy jest narysowany ok, skrzydła są narysowane krzywo (tzn. połówki są mocno asymetryczne, czyli trzeba to przeprojektować praktycznie od podstaw), a kadłub to istna tragedia. Tzn. konia z rzędem temu kto ogarnie jak zrobiona jest część podskrzydłowa i część ogonowa z samego rysunku. I o ile ogarnąłem temat części podskrzydłowej z pomocą zdjęć, to budowa ogona jest dla mnie wciąż tajemnicą Tu prośba o pomoc do Was: Może poratujecie innym planem w tej skali? A jeśli nie, to może kojarzycie jakieś fotki tego? Jeśli nic nie wymyślę, to po prostu zrobię tam profilowaną płytkę balsową (tam gdzie ciągną się dalej listwy za ostatnią wręgę). Tutaj chyba budowniczy tak właśnie postąpił: http://www.rcuniverse.com/forum/attachment.php?attachmentid=829660&d=1375393949 Niemniej wolałbym wiedzieć co autor planów chciał przekazać, bo może ma lepszy pomysł na to niż ja. I jaki plan na ten model? Zwektoryzować to do końca tygodnia, wyciąć w przyszłym tygodniu, a później lepić to powolutku. Co by nie było konstrukcja wredna, więc plan żeby poleciało w wakacje No i dobór napędu to będzie przygoda. Wygląda, że tu będę musiał wyjść już ponad moje komfortowe 3s
-
A jak Ci ze sztywnością górnego płata wyszło? Na oko to jakoś tak cienko się te pręty prezentują. U mnie mam pręt stalowy 3mm i do spokojnego latanai jest ok.
-
W sumie to jakiś ciężki ten Goblin Fireball. Mniejszy jak mój Trex, a waży tyle samo Z moich obecnych doświadczeń to lepiej podchodzą mi wolniejsze obroty, jakoś tak bardziej samolotowo pętla wychodzi A tymczasem to udało mi się kupić 10 zębów piniona (tego od Gaui). Geometrię ma identyczną jak poprzednik Tarota, wszystko się ładnie zgrywa. Teraz tylko poczekać aż będzie pogoda i spróbuje wykręcić znowu uczciwe 10 min lotu
-
E... słaby wybieg. Doświadczenie doświadczeniem, ale nie warto tego używać w kontekście odrzucania nowych konceptów. A karty technologiczne czytać TRZEBA, tak mnie nauczyło moje 15 lat doświadczenia Kolejną kwestią jest to ,że wikol jest dobrym klejem. Bo wikol jest dobrym klejem, po prostu zrobiliśmy już lepsze.
-
, Ja widzę jednak pewien problem z dłuższym ogonem, bo i tak wożę już balast w owiewce Jak rozbiję będę myślał. Ale powiedz mi - czemu preferujesz lekkie modele i powoli kręcące się wirniki? Co się inaczej prowadzi, co się wtedy zmienia? Pytam poważnie, bo sam nie mam odniesienia, a temat mnie bardzo ciekawi, bo o wpływu wagi na latanie szybowcem to mógłbym powieść napisać
-
Nie podoba mi się, jakiś ten ogon taki długi A tak poważnie: Dobrze widzę, że to od 450 rózni się tylko dłuższym ogonem i dłuższymi łopatami? Jest jakiś powód, żebym nie przerobił swojej 450 na 470tkę, po kraksie w której polegnie belka ogonowa i łopaty?
-
Tak na oko to są tylko w Chinach. Nie, że drogo, ale tyle czekania to aż się odechciewa. Chociaż znalazłem coś takiego: http://www.arthobby.pl/index.php?page=8&prod_id=1892 Teoretycznie do Gaui, ale może się zgrają ze sobą?
-
To inna sprawa - pinion musiałby mieć 10 zębów dla takiego samego efektu
-
Zmiana piniona mi się podoba. Pytanie brzmi czy widziales gdzieś pioniina o 11zębach na ośkę 3,17mm?