
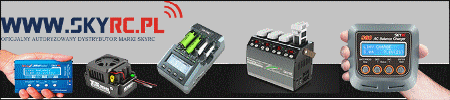
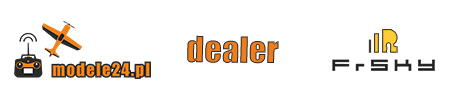
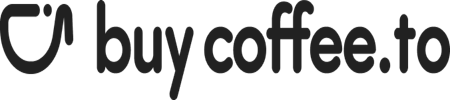
-
Postów
3 456 -
Rejestracja
-
Ostatnia wizyta
-
Wygrane w rankingu
90
Treść opublikowana przez Patryk Sokol
-
Zgoda - pomyliły mi się relacje (bo naoglądałem się dmuchania kadłubów na dziesiątki). Niemniej - w dalszym ciągu twierdzę, że lateks się od makaronu sprawdza gorzej. PCW ma przewagę jeszcze w paru kwestiach: -Nie wymaga naciągania, luźno leży w formie -Pozwala się zgrzewać, jak ktoś potrzebuje mniejszego -Nigdy nie robi problemów z odłażeniem od wnętrza kadłuba (bo zwyczajnie mocne to jest - nie jest to łatwo rozerwać) -Nie trzeba się przejmować różnego rodzaju ostrymi rzeczami w formie (jak np wklejanymi w trakcie laminowania nakrętkami, kantami etc.) -Jest całkowicie wielorazowe (rekord - na jednym makaronie 8 kadłubów) -Nawet jak jest dziurawe, to nie trzeba od razu wymienić (acz powietrze wiadomo - ucieka, kompresor się włączy co jakiś czas) A jak dodać do tego,że zwyczajnie pęknąć nie może, bo się nie rozciąga w formie to powodu do stosowania balonów nie widzę. Z początku się bałem, że na kantach może nie dociskać, ale okazuje się, że pod tym względem jest identycznie jak z balonem, kanty wychodzą bardzo zgrabnie.
-
Ułoży się bez problemu, najwyżej będzie trzeba go luźno ułożyć.
-
Mi Qualatexy tyle napękały, że boje się używać wyrobów lateksowych :| A gwarantuje Ci, że szukając rozwiązania problemu skopiowaliśmy każde jedno rozwiązanie jakie pokazaliście na forum. Ostatnią rzeczą która może powodować, że Ci balony nie pękają to to, że czubek balonu macie z tyłu rury, tam gdzie balon rozprężać się nie musi. U nas nie do sprawdzania, bo nie mamy odejmowanego noska, tylko klasyczną kabinkę.
-
Drobna uwaga - jeśli strzelił bagnet, to zdecydowanie nie był to korkociąg tylko spirala. Podczas korkociągu siły gnące na skrzydle są malutkie, bo skrzyło jest przeciągnięte. Popróbuj wchodzenie w korkociąg przez, najpierw, spowolnienie, a później wrzucenie kierunku. Jeśli wrzuci się na raz oba stery, to model potrafi wejść w pionową spiralę, bez przeciągnięcia i w efekcie rozbujać się do prędkości godnych dynamic soaringu. Co do klapolotek - same nie pomogą, ani lekko w górę, ani w dół. To co za to potrafi pomagać, to klapy na max w dół (jeśli lotki są osobno, to lotki do góry do tego, czyli butterfly). Taka konfiguracja tworzy solidny opór, co pozwala śmiało nurkować modelem, bez obawy, że przekroczymy prędkość podczas której zaczyna się flatter.
-
Byłem, widziałem, rozwiązałem http://pfmrc.eu/index.php?/topic/59704-nowy-spinacz-dlg/page-2&do=findComment&comment=639590
-
Hike FPV, czyli pooglądajmy termikę od środka :)
Patryk Sokol odpowiedział(a) na Patryk Sokol temat w Motoszybowce
Cóż, z małymi perturbacjami, ale mamy już komplet wzorców na Hike'a. Temat mocno się przeciągnął, ze względu na awarię naszej frezarki. Szczęśliwie - z pomocą przysżła nam firma BXC sp. z o.o. z Oławy. Dzięki ich pomocy, nieszlifowane wzorce prezentują się tak: Teraz tylko przygotować to do zdejmowania form (choć szczerze - wyfrezowane jest to tak, że więcej na tym woskowania niż szlifowania ) i być może pod koniec tygodnia będziemy już zdejmować formy -
Tutaj znajdziesz: http://charlesriverrc.org/articles/supra/all%20PDFs/supra_wing.pdf A jak chcesz mieć profil czyściej narysowany, z jedną pozycją klap itp,to mogę to zrobić, ale do komputera z softem siądę pewnie pojutrze dopiero
-
Ale w dużym skrócie - dla małej zbieżności nie warto, szkoda Twojej roboty. A w mniejszym skrócie - polecam jednak zostawić w spokoju RG-15. To bardzo sympatyczny profil, ale jednak model nieco przymaławy i separacja laminarna zaczyna zbierać żniwo.: To takie śmieszne wcięcie w okolicach 0,2Cz to właśnie efekt separacji. Dla porównana masz AG40d, sporo lepszy profil do tego zastosowania, lepszy dla każdego stanu lotu i całkiem zjadający RG-15 dla wolnego lotu (choć tego nie widać na tym wykresie, po prostu im niższe Re, tym przewagę ma większą).
-
NanoWing - Pierwsze skrzydło i pierwsze FPV
Patryk Sokol odpowiedział(a) na czarobest temat w Platforma - nasze konstrukcje
Nie muszą Planki muszą mieć (czyli takie bez skosu). Ogólnie im większy skos do tyłu i większe skręcenie końcówki, tym profil musi być mniej samostateczny. -
Hike FPV, czyli pooglądajmy termikę od środka :)
Patryk Sokol odpowiedział(a) na Patryk Sokol temat w Motoszybowce
Ok, lecimy z tematem dalej Najpierw - jak robimy prowadzenie kołków ustalających skrzydło. Cały problem polega na tym, że frezarkę mamy trzosiową, a trzeba jakoś poprowadzić otwór równoległy do powierzchni rozdziału formy. Rozwiązanie jest nieco pośrednie. Otóż, na powierzchni rozdziału formy robimy taki kanalik: Dlatego, że jest to wykonalne na frezarce o trzech osiach. Następnie, w całość montujemy rurkę mosiężną: Ten kawałek taśmy robi po prostu za zabezpieczenie przed rozlaniem się żelkotu No i na koniec dnia zalewamy żelkotem: Tak po prawdzie - może być jakakolwiek żywica, myślę, że nawet Poxipol byłby ok. Żelkot po prostu kolorystycznie się zgadza No i dnia następnego - używamy rurki jako prowadzenia wiertła podczas wiercenia: W efekcie mamy ładne prowadzenie kawałka metalu, który zrobi nam później otwór na kołek ustalający I w sumie to tyle z formami. Tak naprawdę - moglibyśmy już robić próbne skrzydła. Problemem jest jednak to, że wciąż testujemy jak zachowuje się Freekote Loctite'a przy lakierowaniu w formie. Wyniki są tak obrzydliwie niejasne, że jestem bliski podjęcia decyzji o olaniu tematu i użyciu Spacewaxa. Podobnież też - zaczynamy frezowanie ogonów. Wzorce mają się prezentować tak: Jak widzicie - statecznik z belką ogonową ma stanowić całość. Konstrukcja i wykonanie ma być hybrydowe. Tj. część statecznikowa ma być laminowana jako element z pełnym rdzeniem, a rura ogonowa ma być dmuchana. Rozwiązanie ma same zalety i jedną główną wadę - forma na to jest zwyczajnie duża. Może nie kubaturą, ale wymiary liniowe ma już konkretne. Efekt taki, że całość nie mieści się na frezarce, stąd wzorce będą dzielone do frezowania i klejone do obróbki. Całość frezujemy z płyty na której były frezowane skrzydła. To już nawet nie kwestia oszczędności, ale to spory, ciężki kawał płyty modelowej, którego nie bardzo mam gdzie trzymać. Żeby mieć pewność, że nie braknie grubości materiału to całość podkleiliśmy na OSB: Tutaj jak widzicie - ex skrzydło i kawałek na belkę ogonową. No i jak już się z tym babrałem: Kawałki na kadłub też są już przygotowane. Wszystkie te płyty są tak oszlifowane od góry z dosyć interesującego powodu - woleliśmy nie ryzykować, że gdziekolwiek znajdzie się choć odrobina piasku z żywicą. Jeśli do tego by doszło - frez ginie od razu -
Panowie wszystko ok, LiPol może się zapalić etc (ba, kilka wysadziłem sam), ale... Od nadmiernego rozladowania pakiet zapalić się nie może. Spuchnie, zniszczy się, ale zapalić się nie może, bo zwyczajnie nie ma do tego zmagazynowanej energii. To tak jak z balonem, jak nie ma w nim powietrza, to można go kłuć do woli i tak nie pęknie.
-
Ja bym się nie nabrał.
-
A ja jestem prostym człowiekiem, we wszystkich swoich modelach używam taśmy do zabezpieczenia przed rozsunięciem (włącznie z kompozyciakami). Ma same zalet - lekka, aerodynamiczna, łatwo demontowalna, dobrej jakości w ogóle nie brudzi, puszcza przy uderzeniu - szczerze polecam
-
RESPECT przed lataniem czyli początki F3F na poważnie
Patryk Sokol odpowiedział(a) na Shock temat w Szybowce
Zdecydowanie nieprawda, nie mów takich rzeczy głośno. Praktycznie każdy wypełniacz do żywicy zwiększa jej udarność, co ciekawe najbardziej Aerosil. Łysa żywica jest obrzydliwie krucha, pęka od popatrzenia na nią. To co z kolei pokazujesz jako żywicę, to w rzeczywistości klej na bazie żywicy epoksydowej, jest sporo gęstszy i do laminowania się zupełnie nie nadaje A to co różni go od żywicy, to jest właśnie obecność jakiegoś wypełniacza, choćby po to, żeby proporcje mieszania byłe 50:50 objętościowo. Kleje epoksydowe potrafią być o tyle niebezpieczne, że często mają problemy z równą dyspersją wypełniacza w bazie epoksydowej i w efekcie lubią się czasem niedotwardzić, mimo prawidłowego wymieszania przez użytkownika. Żeby nie być gołosłownym - dokładnie takie opakowanie epoksydu jak masz zdarzyło mi się wywalić, bo zostawała lepka po kilku dniach. -
Idzie wiosna, w końcu będzie można porzucać w uczciwych ciuchach, to zmontowałem sobie nowego Spinacza Mój pierwszy egzemplarz w nowym malowaniu
-
Hike FPV, czyli pooglądajmy termikę od środka :)
Patryk Sokol odpowiedział(a) na Patryk Sokol temat w Motoszybowce
Czasem warto popracować nad projektem od nieco innej strony, czyli od strony sprzętu do FPV. Wciąż jestem na etapie kompletowania "sprzętu idealnego", więc jest dużo różnych opcji do ogarnięcia. A dodajmy do tego chroniczny brak czasu i okropną zimę, to do testowania mi się przez ostatnie miesiące nazbierało. Stąd, kiedy okazał się, że muszę odwiedzić rodzinne miasto, a prognoza pogody wyglądała jak wyciągnięta z późnego marca - nie wahałem się ani chwili W czwartek zameldowałem się na lotnisku i ze zdziwieniem stwierdziłem,że kurtka była zbędna Nie pozostało nic innego, jak uzbroić sprzęt: Poskładać stację naziemną stację naziemną: I można było lecieć: I jak było? Fajnie, ale krótko, bo stało się coś takiego: Czyli Twinek stał się samolotem jednosilnikowym :| Niestety, jest to choroba tych silników: https://www.ef3m.pl/pl/p/Silnik-rc-bezszczotkowy-EMAX-CF-2822-KV1200/171 Są naprawdę fajne i sensownie wykonane, tylko łoże lubi im się odkręcać. Problem zauważyłem w poprzednim sezonie już i nawet łoże skleiłem, jednak cyjanoakryl się poddał i zgubiłem silnik (swoją drogą - powrót nad lotnisku na jednym silniku to ciekawe doświadczenie). No dobra, ale co było testowane? Po kolei: 1 - Monitor LCD z matrycą TN (bo jasna) 2 - Konwerter AV -> D-Sub 3 - Bosscam 5,8GHz (nuda) 4 - monitorek z gogli, gdyby nowy sprzęt nawalił 5 - zasilanie ze starych Li-Poli 6 - Przetwornica 12->220V (nie załapała się na zdjęcie) Innymi słowy - cała zabawa polega na wyeliminowaniu gogli i zastąpieniu ich uczciwej wielkości ekranem. Wszystko wzięło się stąd, że gogle mi zwyczajnie nie podeszły (główny powód? Są aspołeczne. Poza tym nie są dla mnie szczególnie wygodne, męczą szyję i przerzucenie parametrów z OSD na zewnętrze ekranu męczy oczy), a dostępne w sklepach dedykowane wyświetlacze są małe i drogie. To co widzicie powyżej, to wciąż etap przejściowy, testowałem samą koncepcję monitora komputerowego w praktyce. Efekt mi się bardzo podoba, jakość obrazu jest zdecydowanie lepsza niż w goglach (lepiej widać szczegóły, nie ma problemu z ostrością obrzeży wyświetlacza, który powoduje soczewka Fresnela), jasności jest aż nadto (ten pokrowiec na skrzydła, który leży na monitorze, okazał się całkowicie niepotrzebny), a możliwość popatrzenia na obraz została doceniona przez kolegów na lotnisku Kolejnym etapem będzie próba zintegrowania tego w uczciwą całość. Chciałbym zlikwidować przetwornicę 12/220V, przez wywalenie zasilacza z monitora (jeśli w tych co mam się da, oczywiście), pozbawić konwerter AV/D-Sub zasilacza, a całość zintegrować w jedną walizkę, z jednym tylko przyłączem zasilania do akumulatora 12V. Pozostałe wnioski? Idzie wiosna, trzeba zrobić sobie nowe DLG. -
Hike FPV, czyli pooglądajmy termikę od środka :)
Patryk Sokol odpowiedział(a) na Patryk Sokol temat w Motoszybowce
No, akurat gładkość powierzchni nie pomoże kiedy się będzie miało przylepić Choćby gładkie było tak, że odbijałoby jak lustro od teleskopu, to wciąż bez rozdzielacza, zlepi się na amen. A jaki będzie kolejny etap? To zależy, waham się jeszcze. Albo frezowanie ogonów i zdejmowanie ich form. albo może jakieś skrzydełka próbne wyklepiemy. Jedno wymaga ode mnie frezowania (nie chce mi się), a drugie wycięcia kilkudziesięciu kawałków stali na ściski (też mi się nie chce). No ale do rzeczy. Czas pochwalić się foremkami: Tak to wygląda w całości. Jak widzicie całość jest dopolerowana w części roboczej, jeszcze nadmiar szkła od spodu formy jest do docięcia. Samo doprowadzenie form do takiej postaci to nie jest wielkie wyzwanie, raczej tylko pracochłonne. Cała rzecz rozbija się tak naprawdę o porządne pasty polerskie. Całość zaczynamy oczywiście od czyszczenia powierzchni form z wosku - najszybciej idzie rozpuszczalnikiem nitro. Później idzie na to papier ścierny na mokro, gradacje kolejno 800, 1500 i 2500. Jeśli całość równiutko doczyściliśmy papierem ściernym, to sama polerka idzie szybko. Przy czym - zdecydowanie polecam użycie dedykowanych past polerskich do żelkotów, takich jak z mojego poprzedniego postu. Efekt jest taki, że to co zrobiłoby się w 6h pracy pastą pokroju Farecla G3, tutaj robi się w 30min. Teraz jeszcze kwestia pokrycia form rozdzielaczem. Na razie testujemy rozdzielacz polimerowy (produkcji Loctite), jak wyniki będą tak dobre jak nam się wydaje (jutro laminujemy DLG z jego użyciem) to te formy wosku nigdy nie ujrzą. Następnym razem pokaże jak wykonujemy zamknięcia form i prowadzenia bagnetów, bo jak na razie: Wciąż są do obróbki. -
Hike FPV, czyli pooglądajmy termikę od środka :)
Patryk Sokol odpowiedział(a) na Patryk Sokol temat w Motoszybowce
Epopeja robienia form na skrzydła dobiegła końca. Foremki są gotowe, wypolerowane, wyczyszczone etc. Niestety - bateria w aparacie mi padła, więc póki co tylko jedna fotka na zachętę: W dużym skrócie - wyszło to bardzo ładnie. Szerszy opis jak do tego formy doprowadziliśmy i więcej fotek pewnie w poniedziałek (bo jutro to ja wolę polatać niż w warsztacie siedzieć ) -
Dynamic Soaring - teoria i praktyka
Patryk Sokol odpowiedział(a) na Patryk Sokol temat w Aerodynamika
Panowie... Dokładnie o tym podlinkowałem pracę naukową (sam koniec pierwszego posta) -
Hike FPV, czyli pooglądajmy termikę od środka :)
Patryk Sokol odpowiedział(a) na Patryk Sokol temat w Motoszybowce
Powiem tak - testowaliśmy, nie opłacało się Głównym problemem jest jednak podłoże. Wszelkiego rodzaju MDF, OSB, czy MFP dają radę, tak długo jak nie robimy skrzydeł. Wtedy utrata 0,1-0,2mm potrafi zaboleć (a to się zdarza choćby przez wilgoć w powietrzu). Dobra rzecz gdy robimy jakieś duże i mało dokładne rzeczy. Ale wtedy to nawet zdarza nam się użyć styroduru jako podkładu. Tak naprawdę główną wadą tej metody jest odwzorowanie różnych pionowych ścianek, ostrych krawędzi etc. No i jak wspomniałem - czy frezujemy u kogoś, czy u siebie - koszt frezowania musi być mniejszy niż różnica kosztów wynikająca z tańszego materiału. Pamiętajcie, że płyty modelowe jednak są dosyć tanie, jak na rozmiar jaki prezentują, a żelkot do nałożenia też nie jest za darmo. I to zobaczysz właśnie u nas. Pracując w płycie modelowej w ogóle nie walczymy o połysk, walczymy tylko o kształt i gładkość powierzchni. Stąd odejście od jakichkolwiek metod z lakierowaniem płyt. Obecnie, co widać a zdjęciach, pracę z płytami kończymy na pozbawieniu ich porowatości. Płyty zostają w takim "półmacie", gładkie, ale makijażu w nich poprawić się nie da. Badamy temat - różne próbki do nas już jadą. Bo choć wosk nie daję złych wyników, naprawdę dobrze radzimy sobie z lakierowaniem na woskowanych podłożach, to jednak nakładanie rozdzielacza raz na 50 cykli pracy, jest bardzo pociągające, wiele pracy powinno to oszczędzić. Jednakże - tak wysokie temperatury nas nie interesują - lakiery lubią od nich żółknąć. Z reguły ograniczamy się do 50st. A dziękuje, dobrze wiedzieć, że ktoś te posty techniczne czyta No dobra, ale do rzeczy. kontynuujmy naszą relację Całą robotę zawsze należy zacząć od przeglądu wzorców (czy nic im się nie przydarzyło, czy są czyste, etc.), czy mamy komplet materiałów i czy wszystkie narzędzia są przygotowane. Powód jest dosyć prosty - jak żelkot dotknie wzorców, to już nie ma odwrotu!. Pierwszym etapem jest przetarcie wzorców delikatnie wilgotną szmatką. Fotek brak - to nic skomplikowanego Następnie na wszystkie kanty formy nakładamy żelkot cienkim, twardym pędzlem (i tu mała uwaga - włochate pędzle warto skleić u podstawy cyjanoakrylem. Włos znaleziony na licu formy psuje mocno nastrój). Żelkot którego używamy to Axson GC1 080. Dobrze się poleruje i formy są na nim wystarczająco trwałe. Być może są lepsze, ale jednak nie spotkałem się z takim. Korzystanie wciąż z tego samego żelkotu ma tę zaletę, że zwyczajnie się go uczymy i lepiej czuje się pracę z nim. Samo nakładanie żelkotu na kanty jest nieco kontrowersyjne. Ja tak robię, ale nie znam nikogo innego kto tak robi. Tok myślowy za tym jest dosyć prosty - dzięki temu trudniej zamknąć bąbel powietrza np. na krawędzie natarcia. Później już tylko nakładanie żelkotu. Tutaj można powiedzieć parę słów o tym jak pracować z żelkotem. To co widzicie na zdjęciach - nie nakładam żelkotu na całą powierzchnie formy od razu, nakładam najpierw na powierzchnie skrzydła, a na powierzchnie rozdziału idą już resztki z kubeczka. Powód jest taki, że żelkot świeży nakłada się znacznie lepiej , niż żelkot po 5-10minutach od zmieszania. Stąd - póki nakłada się to dobrze, to żelkot idzie na powierzchnię roboczą, gdy gęstnieje - maluję nim powierzchnie rozdziału. Do nakładania żelkotu dobrze użyć naprawdę twardego pędzla. Gdy nie mamy nic innego - pędzel do malowania obcięty na krótko i sklejony cyjanoakrylem, u podstawy włosia, daje całkiem nieźle radę. Ostatnio, jednak odkryliśmy coś takiego: https://www.castorama.pl/produkty/narzedzia-i-artykuly/auto-i-garaz/szpachle-samochodowe/pedzel-do-kdm-autofit-szer-25-mm.html Twardy pędzel bardzo pomaga pozbyć się powietrza. Gdy nakładamy miękkim pędzlem, to żelkot bardziej odkształca pędzel, gdy pędzel ma twarde włosie, to rozbija ono żelkot na równiejszą warstwę i pomaga wydobyć bąbelki na zewnątrz. O ślady po pędzlu nie ma się co martwić. Chwilę po nałożeniu żelkot, dzięki dodatkom modyfikującym napięcie powierzchniowe, sam je zaleczy i rozpłynie się równiutką warstwą. Ze względu na krótki czas pracy (który jest konieczny,żeby można było nakładać kolejne warstwy w rozsądnym czasie) szczerze polecam rozrabiać po 100g żelkotu. Rozrabianie więcej bardzo lubi poskutkować zagrzaniem całości i zżelowaniem w kilka minut. Warto też pamiętać, że większość żelkotów posiada obrzydliwie silne barwniki. Na szczęście - izopropanol zmywa żelkot wspaniale (podobnie jak i nieutwardzoną żywicę epoksydową). Po położeniu żelkotu na wszystko: Można wyskoczyć z warsztatu na herbatę. Żelkot potrzebuje teraz trochę czasu dla siebie, z nakładaniem kolejnej warstwy należy poczekać do momentu aż żelkot zżleuje. Etap ten można poznać po tym, że już niespecjalnie jest płyny, ale jeszcze nie jest twardy. Tak naprawdę od momentu, kiedy nie rozłazi się już pod naciskiem to można nakładać kolejną warstwę. Po przekroczeniu tego momentu jedyne co jeszcze robi to staje się coraz mniej lepki. Moment kiedy całkowicie przestaje być lepki wyznacza z grubsza chwilę kiedy warto by już skończyć nakładać drugą warstwę. Wszystko później (a więc położone na już utwardzony żelkot) może mieć tendencję do łuszczenia się. Kiedy czas już nadejdzie - nakładamy kolejną warstwę żelkotu: Drugą warstwę należy nakładać poruszając pędzlem prostopadle, jak było poruszane podczas poprzedniej warstwy. Służy to wyrównaniu śladów pędzla po poprzedniej warstwie. W przypadku tego żelkotu, nie jest to szczególnie istotne, jest na tyle łatwo rozpływający się, że po 5min sam wyrównuje wszystkie ślady. Niemniej - warto wyrabiać sobie prawidłowe nawyki. Możecie też zauważyć na zdjęciach, że dopiero podczas drugiej warstwy maluję żelkotem pionowe ścianki ograniczające obszar formy. Powód jest bardzo prosty - na ścinkach nie potrzeba dwóch warstw żelkotu (ba... nie potrzeba nawet jednej, po prostu ładniej to wygląda), a pierwsza warstwa lepiej trzyma ściankę na miejscu. Otwartym pytaniem jest, czy druga warstwa jest konieczna. Moim zdaniem konieczna nie jest, ale jest naprawdę pożądana. Dzięki niej dużo łatwiej o nieprzeoczenie żadnej dziurki w żelkocie, bo wbrew pozorom to się zdarza. Kiedy na formę wydaje się masę środków i czasu, to na drugiej warstwie żelkotu IMO nie warto oszczędzać Po nałożeniu drugiej warstwy - znów można iść na herbatę Kiedy herbatę skończymy, a żelko zsiecuje, czas na położenie "białego żelkotu". Biały żelkot to tylko nasza wewnętrzna terminologia. Jest on niczym innym jak żywicą, którą użyjemy do laminowania tkanin zbrojących formę, zagęszczoną za pomocą aerosilu i mikrobalonu do konsystencji gęstej śmietany. Ról tej warstwy jest kilka. Zaczynając od najbardziej prozaicznej - poprawienia wiązania tkaniny zbrojącej z żelkotem, przez ułatwienie układania tkainy na żelkocie, a kończąc jako warstwa buforowa, zmniejszająca aprężenia termiczne między tkaniną szklaną, a żelkotem, co zapobiega wyłażeniu faktury tkaniny na powierzchnie formy. No i po "białym żelkocie" znów mamy przerwę, tym razem dłuższą (bo LH160 ma większy czas pracy od żelkotu). Różnica jest taka, że białemu żelkotowi nie pozwalamy zsieciować do końca przed nakładaniem tkaniny. Zamiast tego pozwalamy żywicy zgęstnięć do fazy takiego mocno lepkiego, płynnego gluta. Kiedy pozwolimy żywicy zsieciować na tyle,że już nie będzie plastyczna, to sporo utrudnimy sobie pracę - nie będzie się ona chciała rozpływać pod tkaniną. Kiedy przerwa się skończy, przychodzi czas na pierwszą warstwę zbrojenia: Jak widzicie, pierwszą warstwą zbrojenia jest mata szklana przeznaczona do pracy z epoksydem. Jest nakładana jako pierwsza, z dwóch powodów. Pierwszym jest brak faktury, która mogłaby wyleźć na powierzchni formy, a drugą jest jest to, że jest dziurawa. Dzięki temu bardzo łatwo odpowietrzyć pierwszą warstwę i nie ma ryzyka, że zajdzie się tam bąbel powietrza który spuchnie w trakcie wygrzewania kompozytu. Dalej nakładamy już to co ma stanowić o brutalnej sile formy: Czyli grubą tkaninę szklaną. Jest to tkanina pochodzenia nieznanego - otrzymaliśmy ją od kolegi, u którego zalegała w piwnicy. Okazało się, że jest naprawdę gruba (około 800g/m^2), fantastycznie gęsto tkana, świetnie się przesyca itp. Aż szkoda, że jest w tej gramaturze, bo inaczej z radością byśmy ją zużyli na wyroby, a nie na formy (no, może poza tymi fragmentami, gdzie jest lekko brązowa. Ale na formie to nie przeszkadza). Jednakże - tkanina może i gruba, ale 10 warstw na każdą formę poszło. Nikt jeszcze nie stworzył czegoś takiego jak zbyt sztywna forma Na szczęście - po tkaninie nie ma co czekać, trzeba sypać wypełnienie w formy Tutaj będzie mało zaskoczenie - nie użyliśmy Poraveru, zamiast tego użyliśmy piasku Pomysł wziął się, jakiś czas temu, z potrzeby zrobienia naprawdę wytrzymałych na ściskanie form (zupełnie niemodelarskich). Wtedy użyliśmy piasku po raz pierwszy i efekt jest tak świetny,że już tak zostało. Piasek, wymieszany z żywicą, ma zadziwiająco wysokie parametry wytrzymałościowe. Okazało się, że potężny jest nie tylko na ściskanie (no, bo jakby inaczej... To przecież Poraver bez porów), ale również na zginanie i ścinanie. To co jest interesujące, to sposób pękania takiego kompozytu. Otóż o nie pęka przez rozerwanie ziarenek od siebie, pęknięcia rozrywa również ziarenka. Zasadniczo - piasek ma same zalety, poza jednym mankamentem - jest obrzydliwie ciężki. Na tyle ciężki, że jedna część formy na skrzydła, będzie ważyć pewnie koło 20kg. Ale z drugiej strony - dbam o swoje miejsce pracy, przenoszenie tych form to jedyna rzecz, w której Angelika nie może mnie zastąpić Samego piasku nakładamy dwa rodzaje. Najpierw leci drobniutki piaseczek formierski, kupiony w sklepie z żywicami. Ma on same zalety, poza jedną - bierze bardzo dużo żywicy i przez drobne ziarno wychodzi jeszcze ciężej. Stąd jego jest tylko warstwa buforowa, tak na 2-3cm gruba. A później - piasek z Castoramy (chyba do piaskownic). Na ostatnich fotkach widzicie patent na ładną górną powierzchnię piasku. Czyli wystarczy go przewałkować, za pomocą zwykłego wałka, ale zostawionego w folii Z samym piaskiem pracuje się naprawdę przyjemnie. Żeby zmieszać go z żywicą, to wystarczy wsypać go do wiadra, wlać żywice i pomieszać kilka minut mieszadłem mechanicznym Nie mam pojęcia ile procentowo mamy w tym żywicy (waga waży nam tylko do 5kg), ale dobór jej ilości jest stosunkowo prosty. Jeśli piasek cały ściemniał, a po zgnieceniu go w kulkę trzyma mniej-więcej swój kształt - to więcej żywicy nie potrzeba. I to na tyle na ten etap. Po tym formy należy zostawić w spokoju, aż żywica się utwardzi, a następnie zalaminować im plecki. Mam taką teorię, że najlepiej laminowałoby się to gdy piasek był już związany i lepki, ale ten etap utwardzania wypada już w nocy, a my też czasem odpoczywamy. Niemniej - dzień później (czyli dziś) powstały plecki. Plecki to nic innego, jak zalaminowanie otwartych piaskowych powierzchni tkaniną. Zacząć należy od pozbycia się piasku, z miejsc gdzie być go nie powinno. Najprościej - zeskrobać go śrubokrętem (który stanie się okrągły, nie warto robić tego nowym i dobrym narzędziem) A później - już tylko przemalowanie całości zagęszczoną żywicą, ułożenie na tym tkaniny i przesycenie całości. Warstw - znów 10, ale idzie naprawdę szybko. No i na razie tyle, przynajmniej na jakiś czas. Musimy ten cykl przelecieć jeszcze ze 3 razy, więc nie będzie co raportować (no bo całość będzie wyglądać dokładnie tak samo). Z racji tego, że formom do rozpakowania nigdy się nie śpieszy, to rozformujemy cokolwiek najpewniej w przyszłym tygodniu. Wtedy wrócimy do relacji i opiszemy co z tym robi się później, gdy trzeba je przygotować do laminowania. -
Hike FPV, czyli pooglądajmy termikę od środka :)
Patryk Sokol odpowiedział(a) na Patryk Sokol temat w Motoszybowce
Masz na myśli Topkast? Ogólnie - patent z frezowaniem czegoś, nałożonego na coś jest niezbyt dobry. Frezowanie dwa razy jest zwyczajnie drogie. -
Hike FPV, czyli pooglądajmy termikę od środka :)
Patryk Sokol odpowiedział(a) na Patryk Sokol temat w Motoszybowce
No dobra, wzorce są przygotowane do robienia form: Widać, że od woskowania doszły kołki w otworach. Kołki są wykonane z takich śmieciowych rurek aluminiowych z Castoramy- miękkie i badziewne, ale tak na szybko nic innego nie mieliśmy. Docelowo w otwory wklejone będą rurki mosiężne, mają robić za tuleje prowadzące docelowe, stalowe kołki Wyjątkiem jest prowadzenie śrub mocujących skrzydło. Tutaj wstawiona jest rurka o średnicy otworu (bo akurat rurki mieliśmy o pasującej średnicy), które jest nawoskowana. Na nią nałożona jest rurka która jest o 1mm większa. Ta rurka z kolei jest zmatowiona i odtłuszczona. Założenie jest takie, że rurkę wewnętrzną wyciągamy, a zewnętrzna zostaje już w formie i robi za tuleje. Same ścianki są z kolei wykonane w najprostszy możliwy sposób - jest to brystol pocięty na paski i przyklejony do wzorców klejem na gorąco. Przed sklejeniem się z formą brystol jest zabezpieczony taśmą pakową (oklejamy cały arkusz, a później tniemy na paski). Żeby ścianki trzymały pion - używamy po prostu trójkącików z depronu. Aczkolwiek - to nie jest najlepsza metoda jaką znam. Najfajniejsze były ścianki wykonane z blachy 0,15mm ocynkowanej. Miałem kiedyś szpulkę takiej taśmy o szerokości 8cm, fantastycznie się to formowało, trzymało pion i łatwo się rozformowywąło. Niestety szpula się skończyła, a ja nie wiem gdzie taką kupić. Znajduje jedynie blachę w arkuszach, a ciąć mi się tego nie chce po prostu. Plan na jutro - zalewamy formy. Ale atpię, że jutro będzie mi się jeszcze chciało cały proces opisywać, czekajcie na niedzielę -
Jest, poszła na PW
-
Ostatnimi czasy dostałem już kilka pytań, jak w zasadzie wygląda nasz zestaw. Z racji tego, że od poprzednich zdjęć konstrukcja poszła nieco do przodu, to wrzucamy nowy zdjęcie, korę pokazuje co jest w pudełku Mamy tutaj kolejno: -Kadłub z gotowym mocowaniem śrub skrzydła i aramidowym noskiem - 2,4GHz friendly -Skrzydła z obrobionymi lotkami i zamkniętą ich szczeliną -Stateczniki z orbrobionymi zawiasami, zamkniętymi szczelinami, w zasadzie gotowe do wklejenia w kadłub -Kołek typu T -Worek z częściami potrzebnymi do zmontowania napędu sterów i lotek (popychacze węglowe, komplet dźwigienek, linki, sprężynki, tuleje sprężynek i snapy) -Worek potrzebny do wykończenia skrzydła (taśma szklana na łączenie, tuleje śrub mocujących skrzydło i śruby mocujące skrzydło) -Obrazkowa instrukcja złożenia
-
Hike FPV, czyli pooglądajmy termikę od środka :)
Patryk Sokol odpowiedział(a) na Patryk Sokol temat w Motoszybowce
No to pytanie jest trudne Sama charakterystyka lotu F5J jest wybitnie nieprzelotowa, to raczej tak coby każde pierdnięcie komara wyłapywać. Kiedy lecimy na przelot interesuje nas łapanie mocniejszych noszeń, więc cały model policzony jest bardziej na mocniejszą penetrację, niż krążenie w słabych noszeniach. Stąd model przesunięty jest w nieco szybszą stronę - myślę, że F3B jest tu znacznie lepszą analogią. Ale... W dalszym ciągu mamy tu naprawdę dobre profile i skuteczny obrys skrzydła, więc jakby zejść z masą do 1,8kg, to modele tego typu http://www.hyperflight.co.uk/products.asp?code=GRAPHITE-2E&name=graphite-2e Nie powinny być nawet konkurencją w lotach termicznych. Nie to, że można się śmiało ścigać, powinno się je zjadać bez problemu w termice (bo jednak tam jest tylko MH32, a Hike ma cały komplet profili, które operują na bardzo szerokich kątach klap). Z masą startową jest dosyć ciekawie. Sensowne latanie powinno zaczynać się od 1,5kg masy startowej, do powolnego bujania się w termice. Z dodawaniem masy, model będzie robił się coraz bardziej przelotowy, więc optimum wykorzystania termiki przesunie się na silniejsze noszenia i większą prędkość przelotu między nimi (co nie jest szczególnie dziwne - szybowce na przelot się w końcu balastuje). Tak niespecjalnie chce mi się teraz chce dorabiać wykresy, bo to jest jednak nieco pracy (a mi i tak snu brakuje w tym tygodniu), ale tak na szybko wrzucę porównanie które robiłem już: Wykres przedstawia zależność doskonałości aerodynamicznej od prędkości lotu MH32 analog to coś o rozpiętości, wydłużeniu i profilu linkowanego Graphite'a (czyli tak naprawdę nie mogą się wiele różnić). Porównanie jest zrobione dla tego samego obciążenia powierzchni nośnej (czyli Hike cięższy o 200g, czyli dajmy na to, że jest to waga bardziej ambitnego sprzętu do FPV). To co widać, to to, że Hike wypada lepiej w zasadzie dla każdego zakresu prędkości. Dodaj do tego większy efektywny zakres pracy klap wypornościowych i otrzymasz motoszybowiec ze znacznie większymi możliwościami w termice, niż nawet stosunkowo drogi motoszybowiec (czyli to właśnie Twoja średnia klasa). Zmierzam do tego, że może i nie jest to konstrukcja aż tak specjalizowana jak najlepsze zawodnicze szybowce F3J i F5J, to jednak, nowoczesne i wykonane bezpośrednio do skrzydła, profile aerodynamiczne robią swoje i konstrukcja będzie lepsza od wielu typowych szybowców termicznych, mimo dorzucenia jej dodatkowej masy wyposażenia (i to jest ta specjalizacja w aerodynamice pod FPV o której mówiłem). Wiadomo, że w zawodach z F3J, ani F5J nie wygra, ale one z kolei nie będą w stanie ani zrobić tak dobrych wyników w przelocie, ani bezpiecznie się pchać w obszar zawietrznej dużego zbocza (mój plan - zrobienie dużego dynamic soaringu na zboczu góry Keprnik w Czechach).